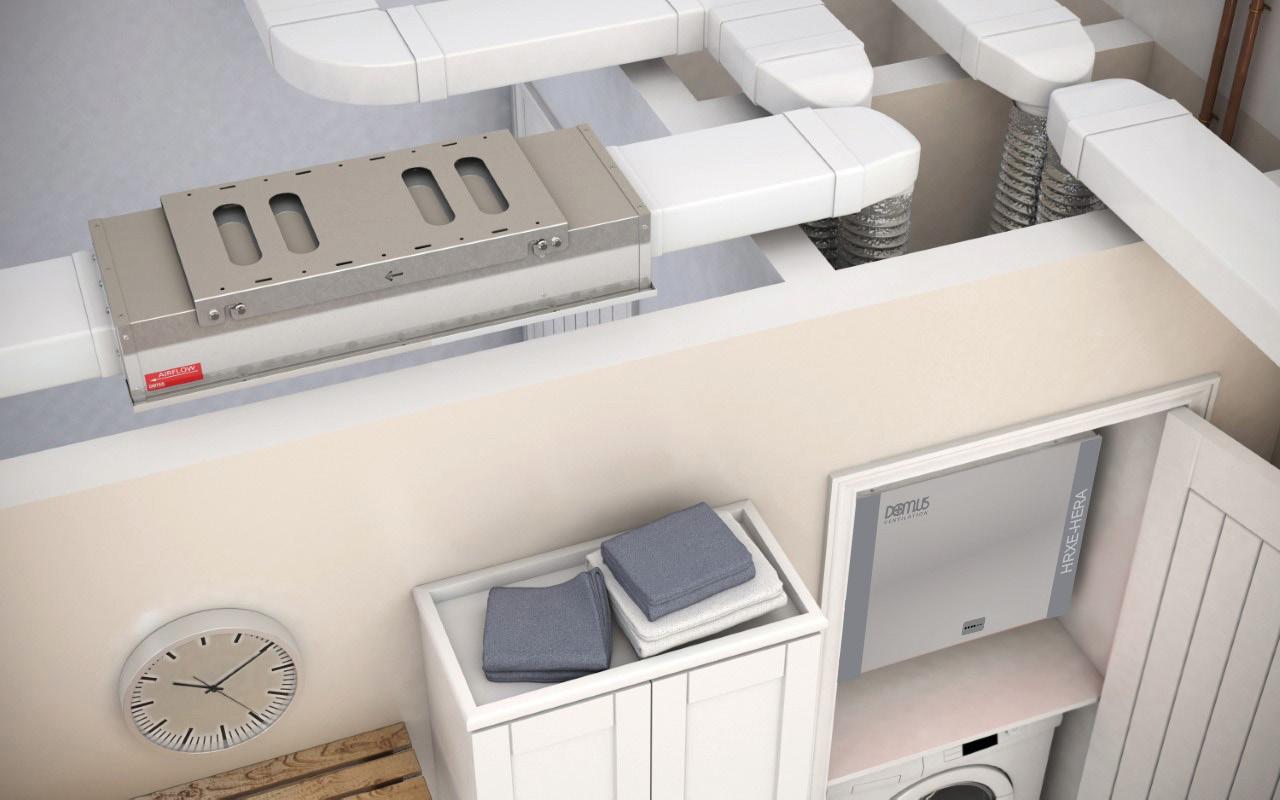
7 minute read
VIEWPOINT
Revised Building Regulations Part F: What You Should Be Doing Differently And Why
By Paul Williams, Domus Ventilation Product Manager
Advertisement
The world is a very different place since 2010, the year that Building Regulations ‘Ventilation: Approved Document F’ was previously revised. In the years that have elapsed we have learnt considerably more about Indoor Air Quality (IAQ), have had to contend with a pandemic, and have the Future Homes Standard to meet in 2025 which requires average new homes to have 80% less carbon emissions.
Building Regulations is the method being used to achieve the Future Homes Standard. Set amongst this context, it is without doubt that Building Regulations Part L (Conservation of fuel and power) and Part F were ripe for an update. These were published in December 2021 with the immediate aim to ensure new homes built from 2022 produce 31% less carbon emissions compared to current standards. A further revision will take place to come into force in 2025. The revisions to Part F are a direct response to this requirement. So, what has changed?
Air Tightness Testing - Under the previous Regulations, smaller developments were exempt from air tightness testing. Now, air tightness testing is mandatory in all new build dwellings.
Mechanical Ventilation Systems - Mechanical ventilation systems in the form of Mechanical Extract Ventilation (MEV) and Mechanical Ventilation with Heat Recovery (MVHR) are recognised in Building Regulations as the most proficient means of ventilating a dwelling. To ensure incoming air reaches all parts of a home – especially the bedrooms - the minimum ventilation rates have been increased as follows:
For larger properties, this increase is substantial and will mean choosing mechanical systems with greater fan power. In a much welcomed move, predicted occupancy rates have been removed from the ventilation calculations, making them far more straightforward.
No. bedrooms
1
2
3
4
5
Previous min. ventilation rate l/s
13
17
21
25
29
New min. ventilation rate l/s
19
25
31
37
43
Background Ventilation - Two key changes have been introduced here. The first is the guidance on sizing background ventilators, including intermittent extract fans, trickle vents in windows and airbricks in the wall. These are to be done on a room-by-room basis rather than the whole property. The second applies to extract only systems, such as MEVs, where the background vents must be increased in size from 2500mm2 to 5000 mm 2 . This may well impact on the property’s façade and window sizes.
Natural Ventilation - Natural ventilation systems, such as background vents, remain an option although only for less airtight homes with a design air permeability of ≥ 5. However, with the background ventilation to be determined on a room by room basis, rather than based on the whole property, this will probably mean much larger grilles are required.
No matter how well designed the grille is, it is likely to compromise the aesthetics of the property from both inside and out. Ultimately, natural ventilation isn’t an efficient means of ventilating a home as heat will be lost and there is no guarantee of moisture or pollutants migrating outside.
Air Pollution Guidance - With air pollution now firmly on the news agenda, and our increasing understanding of its dangers to our health, the revised Part F addresses both internal and external air pollutants more thoroughly. Useful indoor air pollution guidance has been added, covering exposure limits and times for Carbon monoxide (CO), Nitrogen dioxide (NO2), Formaldehyde (CH2O) and TVOC.
In areas with high level of outdoor pollution, advice has been provided on the location of intake grilles, primarily away from the direct impact of the sources of local pollution. Where urban traffic is a source of pollution, the air intakes for dwellings next to busy urban roads should be as high as possible and located on the less polluted side of the building. Ventilation intakes should not be located in courtyards or enclosed urban spaces where air pollutants are discharged.
Reporting - With many homes unable to comply even with the previous Building Regulations Part F requirements, either through confusion and a lack of understanding of the requirements or through deliberate flouting of them, the reporting procedures have been tightened up under the 2021 revisions.
Now a new style commissioning sheet featuring a compliance report and photographic evidence must be provided to Building Control Bodies and the building owner, along with a Home User Guide specifically for householders. So much has changed in the eleven years since Building Regulations ‘Ventilation: Approved Document F’ was last revised. The changes made to Part F are both a reflection on this, but more importantly look to the future and how we as an industry can meet Net Zero and provide housing fit for purpose.
Domus Ventilation is a manufacturer of marketleading ventilation systems that save energy and improve indoor air quality. www.domusventilation.co.uk vent.info@domusventilation.co.uk
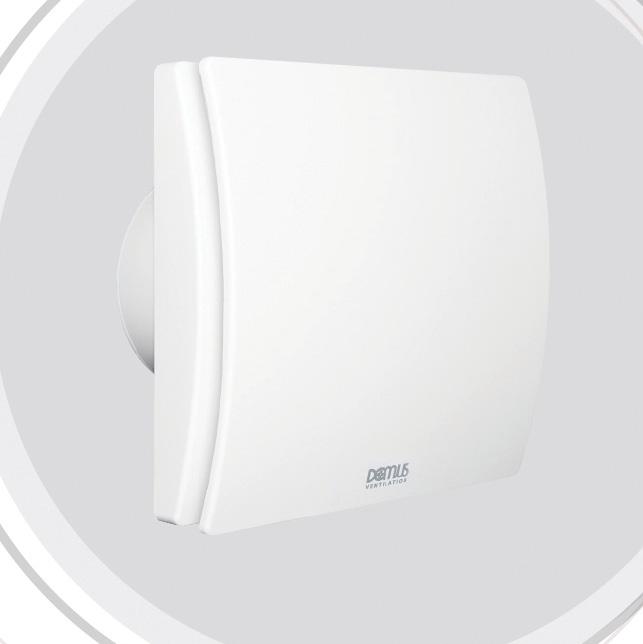
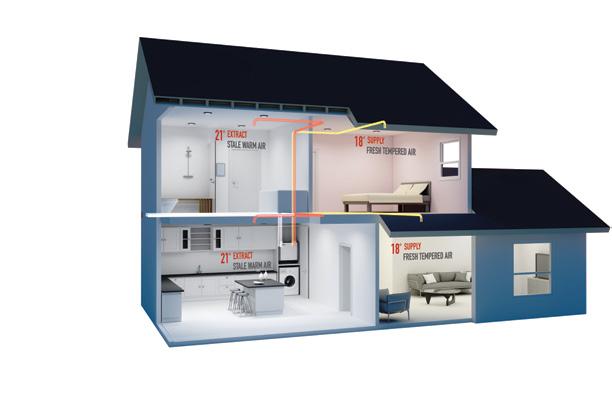
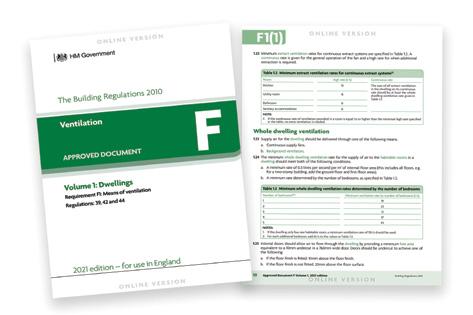
Why Modular Building Systems Are More Valuable Than Ever
At a time of soaring energy costs and global supply chain issues, the value of using prefabricated modular building systems has never been clearer. Alan Green, Managing Director of Neaco Ltd, explains their many advantages. The term modular building is commonly used to describe a self-contained structure or unit - sometimes for temporary use - but another important definition relates to architectural solutions assembled from a range of standardised modular components which are individually manufactured to a finished state at a factory. Finished components are delivered and assembled on site to form an installation, usually connected with a fixing standardised system which uses dry works rather than hot works. Modular construction represents an alternative to traditional methods in which materials are fabricated and finished on site, rather than in a factory.
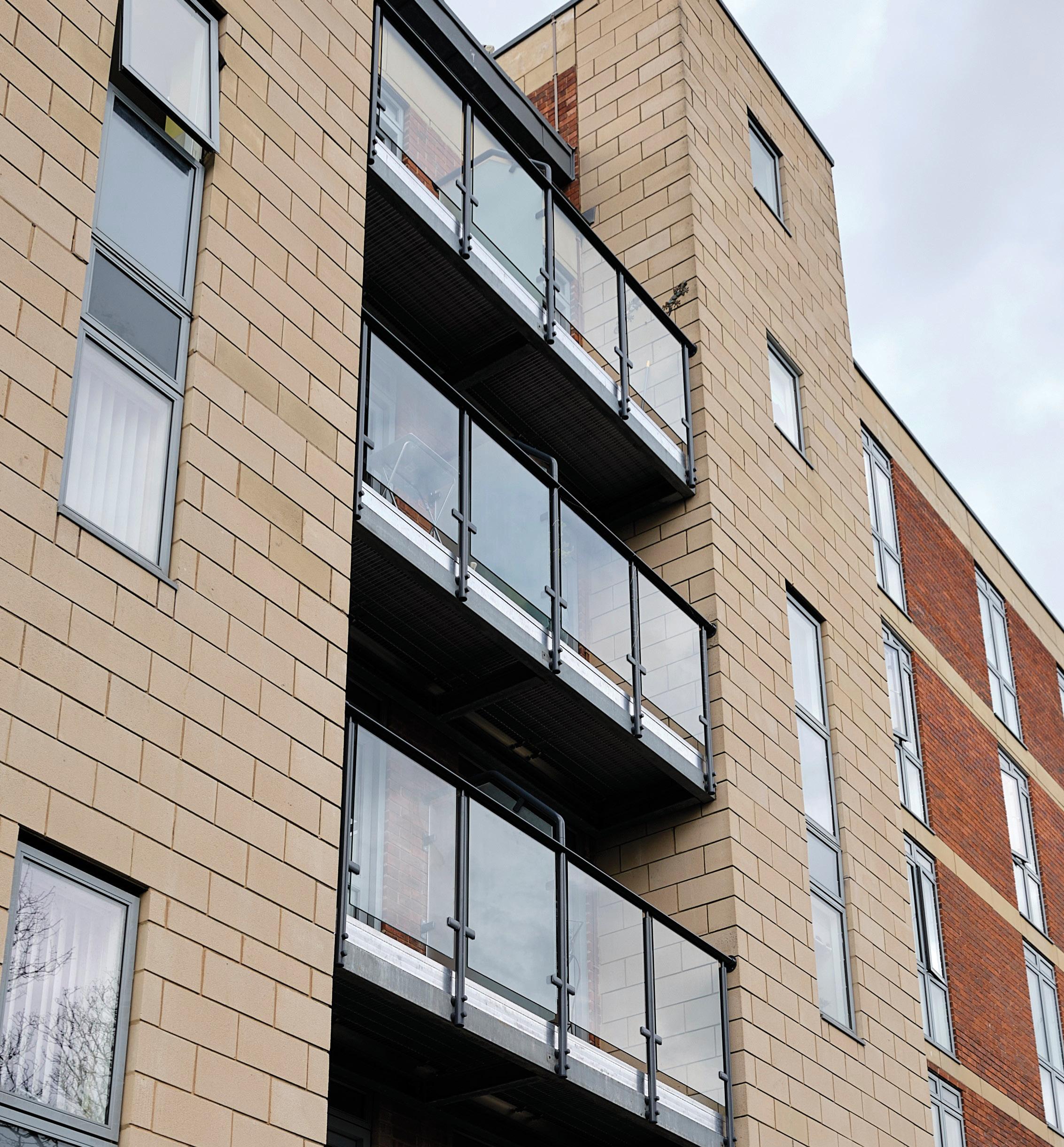
With components already manufactured and finished, modular systems dramatically reduce the time required on site in comparison to using traditional construction methods.
The precise combination of components, angles and dimensions required for a scheme is either a standardised, off-the-shelf design or defined and specified through consultation between the architect/designer and the manufacturer’s technical support. This means that survey, assembly and installation is the only time spent on site.
Carrying out fabrication in factory conditions avoids exposure to delays on-site caused by adverse weather. The shorter construction period allows a quicker return on investment for the client, and reduced overheads. Time efficiency is an especially valuable advantage in where build schedules are subject to time constraints.
In comparison, solutions fabricated on-site involve much more noise, dust, and light pollution. Off-site manufacture of complete modular solutions means that all materials arrive on site in a single delivery in contrast to traditional construction methods, which often require multiple separate deliveries.
For example, a modular balcony is supplied preengineered and pre-assembled in a completed state, ready to be fixed in position on delivery. In contrast, a balcony fabricated on site will often rely on different suppliers for the decking, glass and rails/stanchions. If just one of these suppliers is delayed, the completed installation is pushed back, which could have a knock-on impact on the rest of the construction schedule.
Carrying out construction in safer, more controlled factory conditions enables better risk management. In contrast, solutions fabricated on site increase onsite activity and therefore increase risk, especially if they involve hot works such as welding. Preengineering components in a factory environment enables higher degree of quality control with testing, prototyping and checking for uniform standards.
Solutions fabricated on site are much more variable in quality, largely determined by the individuals involved in carrying out the work. Without the shelter of a factory, exposure to the British climate often presents working conditions which adversely affect quality. Manufacturing in a factory allows far better management of the waste stream. Standardised finished components mean minimal or zero off-cuts and waste materials.
Any waste or off-cuts that occur in a factory can be more easily collected and reused or recycled. Managing waste at factory stages reduces financial and carbon costs of waste disposal on site. Dry works consume less energy and involve far less noise and atmospheric pollution than hot works. Modular construction involves less on-site activity, reducing the environmental impact on the locality and reducing carbon footprint from lighter site traffic.
The importance of energy savings has further increased amid a global energy crisis. Global supply chain problems are impacting a huge range of sectors. Companies relying on products and raw materials from overseas are suffering sharp increases in import costs and lead times. Pre- fabricated modular systems can be held as stock, bypassing supply chain delays and enabling faster lead times.
Neaco source all our raw materials from UK suppliers, which means we can avoid international supply chain obstacles and supply domestic projects with maximum speed and efficiency. Modular systems perform better in every key category, from sustainability, site impact and energy consumption to speed, safety and quality control.
Where possible, the construction industry should opt for modular solutions to improve the quality, efficiency and carbon savings of each project. Neaco manufacture a wide range of modular building systems including architectural grilles, decking, adaptive bathing aids, balustrade and balconies. www.neaco.co.uk