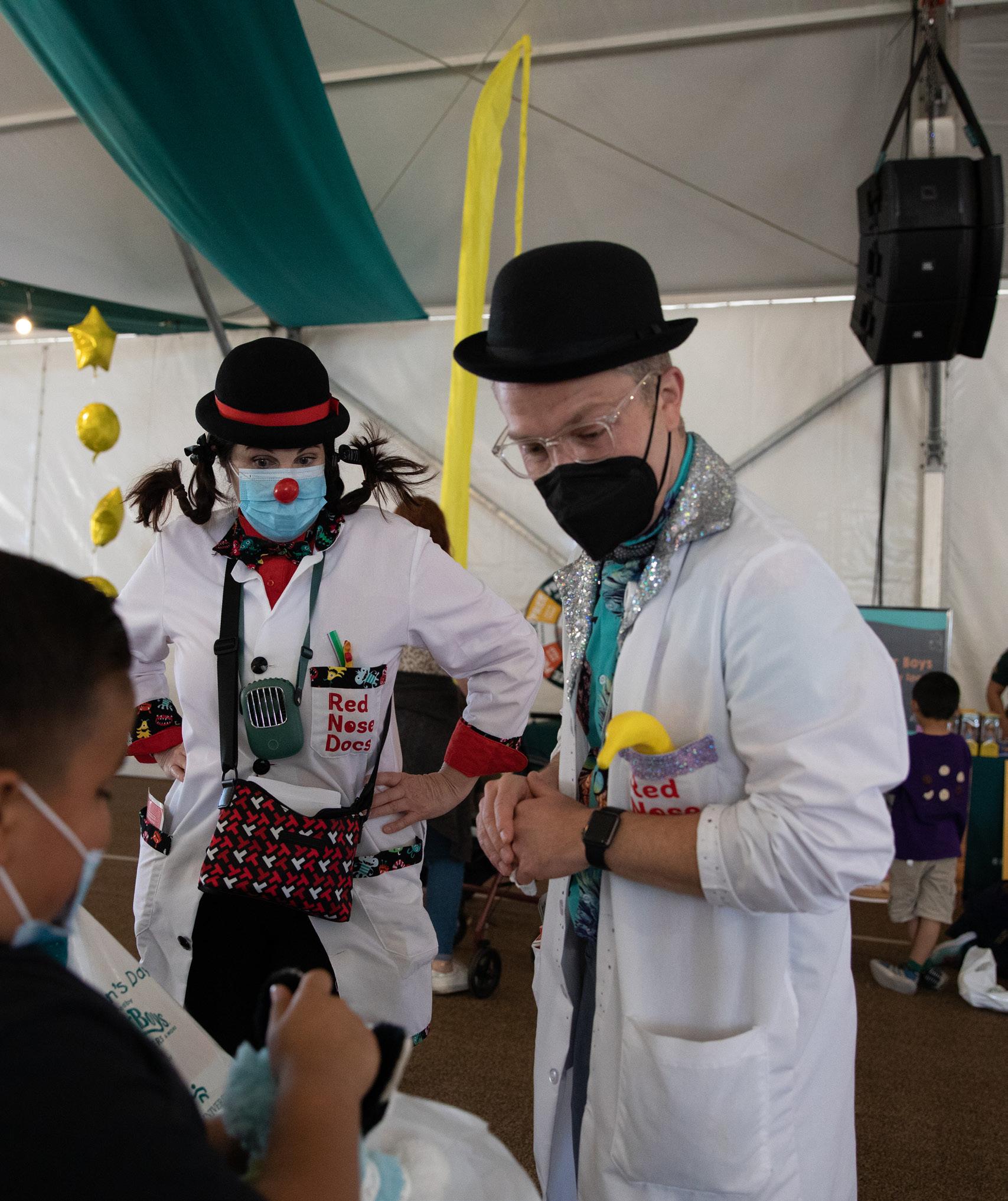
4 minute read
Re-engaging With Our Community
With COVID-19 changing our process, delivering care to our pediatric population underwent an update. Our goal at Loma Linda University Children’s Hospital is to not only provide high-quality care, but to help children better understand common experiences they may encounter in healthcare. In 2022, we were able to start in-person events again, and we were pleased that on Wednesday, March 9, in collaboration with Farmer Boys, we hosted the 37th Annual Children’s Day. We were excited that for the first time in two years we had the opportunity to greet the children of our community and provide them with a fun learning experience.
Six hundred children attended this event, which focused on education for children and families, as well as the opportunity to help children experience clinical settings and procedures without the intimidation factor. Nurses and nursing students, in collaboration with Child Life, participated in the event to support and volunteer for different booths and interact with the visitors. The booths included stitch stations, a teddy bear clinic to role-play common healthcare scenarios, learning about casts, being educated on venomous creatures, and spending time with animals, and our volunteer dog therapists. This year’s Children’s Day was a successful event highlighting our community engagement.
IV Pump Efficiencies
Many times, to address an issue, one must change the process no matter how great the endeavor may be, such was the case with our IV pump process. Electronic error reports (EERs) were written regarding the need for additional equipment, especially during the COVID-19 surge. Since this became a quality of care concern, the Loma Linda University Health Quality Team decided to conduct a performance improvement project. The quality team compiled the number of reports and then mapped out a flow diagram of the process. The flow diagram showed that the rate limiting steps to get equipment in an efficient amount of time was due to the process of sending equipment back and forth between our Central Supply department and the various units. It was proposed to eliminate these steps and to keep the equipment on the floor to be cleaned by our environmental services teams.
To change a process that had been in practice for years, and second nature to some, required the support of multiple stakeholders. This included the departments of quality, environmental services, central service and supply chain, nursing, biomed, and administration. A reasonable change process was discussed where there would be the most benefit and least costly endeavor in the long run, while also putting the patient’s safety and the delivery of medication as a priority. Out of those discussions, a new process was created along with a flow diagram to communicate the change. This change took into account not only cleaning tools, but staff competency. This flow diagram, or algorithm, would be the main tool for the units to reference regarding the changed IV equipment process.
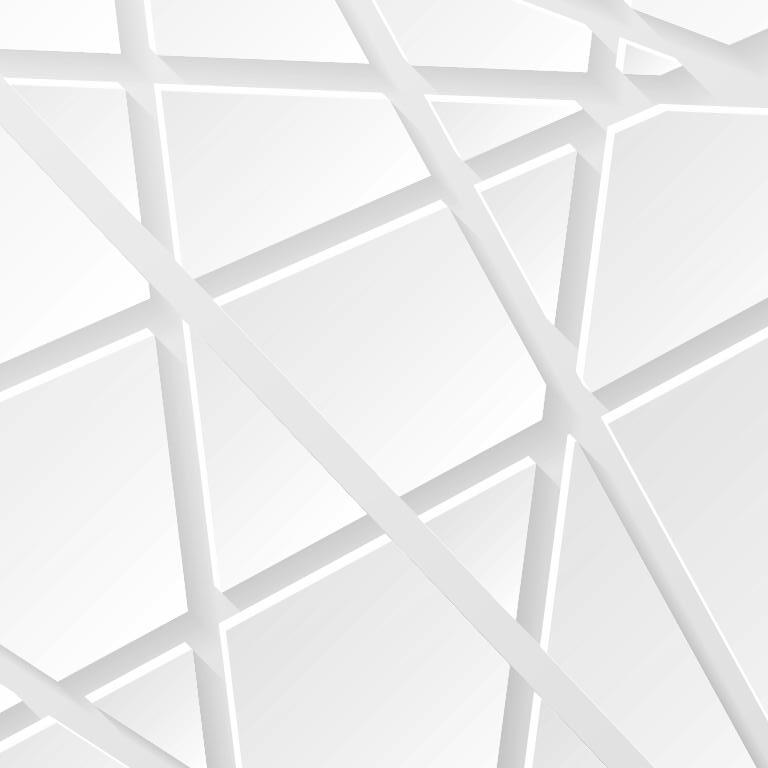

When considering cost savings and safety, although not quantified, there are labor savings for the time saved in transporting equipment back and forth to Central Supply. Since the IV equipment stays on the unit, the staff has the equipment readily available to start the IV treatment ordered without delay. In addition, there should be less equipment damage, as there is less travel of the equipment back and forth. For staff and patient satisfaction, although not measured directly, does impact both as the nurse is able to perform their care without pausing for equipment, and the patient will not be experiencing delays in treatment.
IV Pump Process Scenario Algorithms
Scenario
ED takes pump(s) with patient
ED leaves pump with patient on unit
Staff will bring clean pump back from that room to ED
If the IV fluid is a basic infusion (NS ), and can safely be taken off the pump for transfer, the ED can do so
! !
IV pump kept in room and cleaned by EVS when patient discharged or transferred
Scenario 2

If additional pumps needed beyond unit PAR * or you need to replenish your PAR
Sending unit will transfer the pump with the patient
Sending unit will bring back a clean pump from the receiving unit (to bring unit back up to PAR)
If patient is on 2 pumps, and the receiving unit only has a PAR of 1 pump in that room, the sending unit will take back the 1 clean pump (see scenario 2 for PAR replenishment)
If you take a pump out of an occupied room , please ensure that it is cleaned before use If there is no additional clean equipment on the floor
Staff will need to place an order with CS for additional equipment needed
CS or Dispatch will deliver clean equipment to unit
Further Clarification
If a pump cannot be immediately taken back after transfer , the receiving and sending units need to coordinate with Dispatch to get the clean pump (s) back to the sending unit .
It is recommended that single chargers and combicords should stay in the room when the pump and pole are transferred Space stations should be sent
If a pump is not working/needs service, contact EVS to clean it . Once cleaned, contact Dispatch to send it to CS where Clinical Engineering will pick it up .
Pumps will transfer with the patient
If safe, transfer the IV s to the ICU pumps
If not safe, then transfer the pump into the ICU space station and ICU will give back the number of pumps brought with the patient
Reverse the process for the ICU to floor transfer
Two Options
Option 1:
The OR can send an Anesthesia Team Member up to the ICU to pick up pumps in the clean room that is reserved for that patient
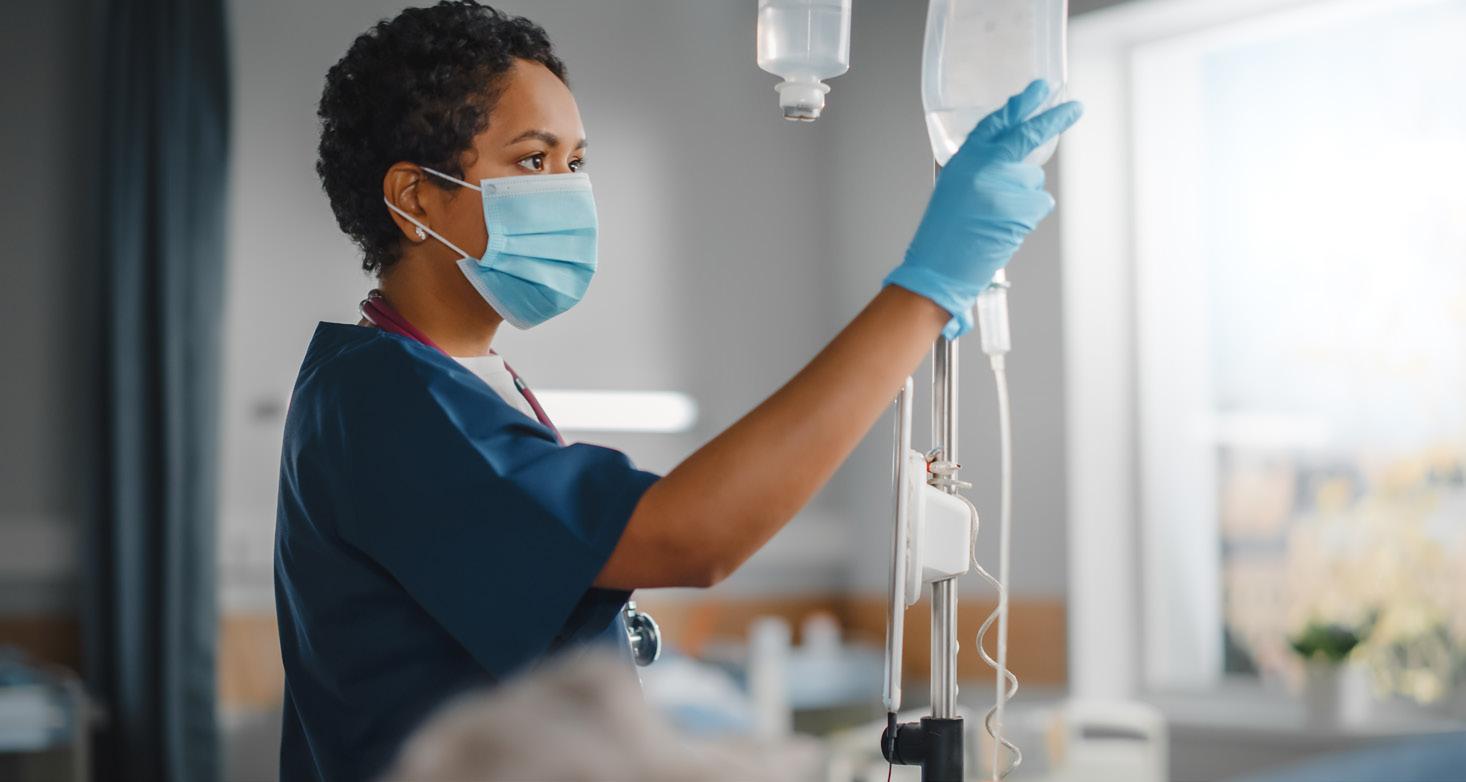
Option 2:

Patient will transfer from the OR to the ICU with the space station and pumps
Anesthesia Team Member will take back the clean pumps/spacestation from the room where surgical patient went.