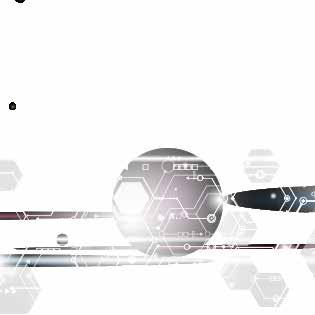
6 minute read
COVER
Strategic ALLIANCE

Advertisement
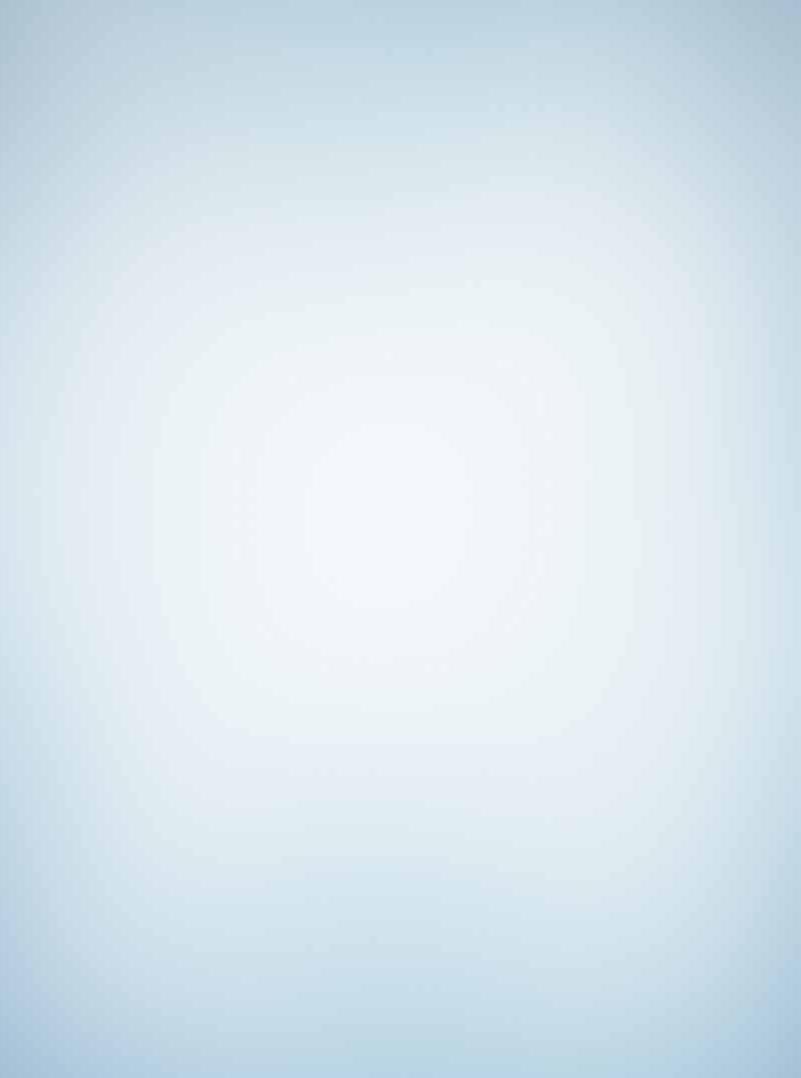
Swisslog and Mai Dubai join forces to install and implement a new fully-automated and retrieval solution for Mai Dubai
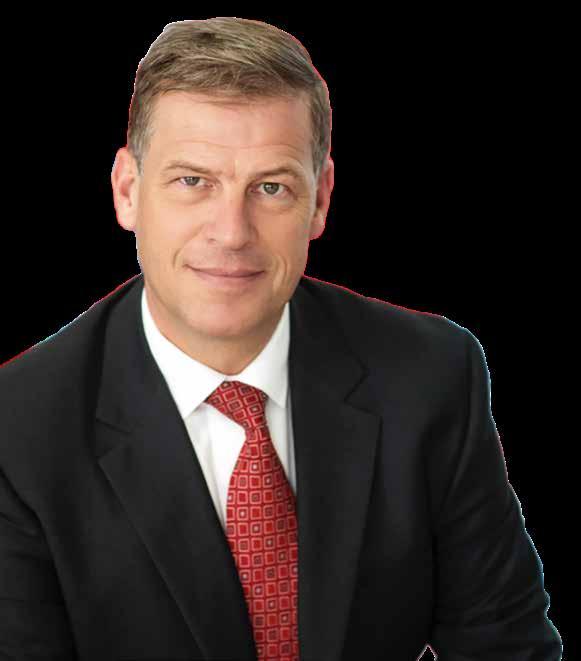
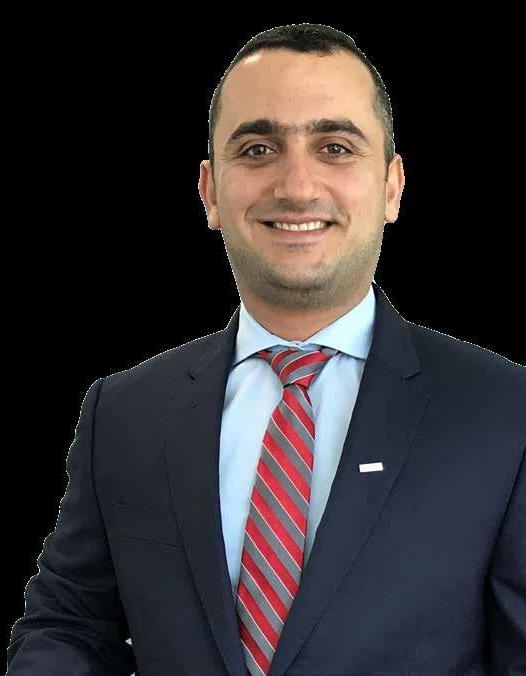
Global logistics automation specialist Swisslog has revealed the successful installation of a new fully automated storage and retrieval solution of Goods for Mai Dubai, a leading Dubai-based bottled drinking water company. The move is part of Mai Dubai’s ongoing expansion initiative and involves implementing a fully automated and data-driven intralogistics system that is future ready.
Swisslog is shaping the future of logistics automation and transforming warehouses and distribution centres to achieve maximum efficiency, flexibility, and agility.
Alain Kaddoum, General Manager, Swisslog Middle East, said, “Warehouse and factory managers constantly need to synchronize their material flow between production and warehouse to optimize the inventory level and reduce the operational costs.”
Alexander van’ t Riet, CEO of Mai Dubai LLC, said: “Swisslog’s many years of experience
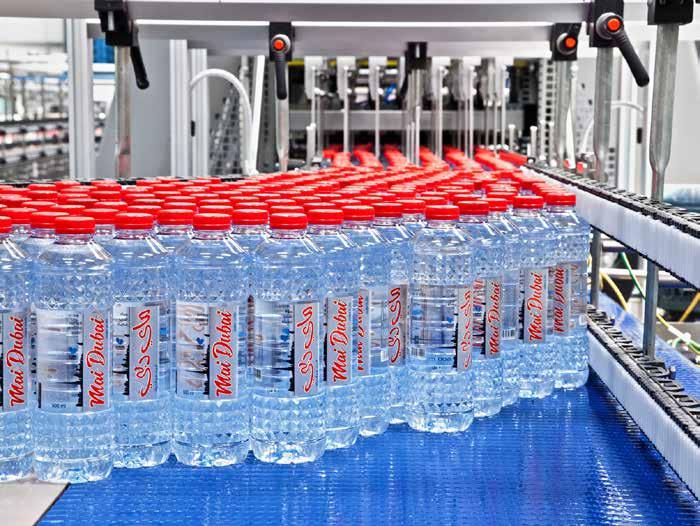
and expertise in logistics automation for the food and beverage industry convinced us to go with Swisslog Middle East as our intralogistics partner for our expansion project.”
The benefits that Mai Dubai will reap out of this are plentiful; a complete solution for end-toend material flow, requisite logistics in place to handle considerable increases in capacity, significant improvement of flow of goods through automation, and having tight control of all logistics components through the usage of software and technology. With this installation, Swisslog offered complete system design, engineering, simulation, implementation, and integration of two high-bay warehouses with associated monorail and conveyor technology.
EXEMPLARY FOOD SAFETY STANDARDS
Since its establishment in December 2012, Mai Dubai LLC has enjoyed exponential growth of the bottled water it produces and is an excellent example of an inspiring success story. The fully owned subsidiary of the Dubai Electricity and Water Authority (DEWA) has been investing in state-of-the-art technologies from the start for its facilities to guarantee the production of high-quality end products. Due to its commitment to excellence, the young company has earned the region’s highest award for food safety year after year.
Mai Dubai currently is the number two brand in the market and also enjoys an excellent reputation beyond the borders of the United Arab Emirates (UAE). Apart from being the official bottled water partner of Emirates Airlines, the company’s distinctive and iconic water bottles with red lettering have also become a fixture in 13 countries across the GCC, Asia, Europe, and Africa.
The use of Swisslog’s fully automated storage and retrieval solution will help drive critical benefits and advantages for Mai Dubai, including a
significant reduction in labour costs, improved production flows and enhanced storage efficiencies. The installation proves to be both timely and strategic, and is expected to sustain Mai Dubai’s continued growth ambitions.
SWIFT AND EFFICIENT PROCESSES IN TWO HIGHBAY WAREHOUSES
To meet the steadily climbing demand, the company decided in 2016 to expand production by 2020. Mai Dubai committed to massive investments in production and intralogistics and elected to rely on the expertise of Swisslog to deliver its needs and requirements.
As part of an order valued over Euro 20 million, Swisslog planned and implemented a fully automated system based on intelligent software in the context of big data. The major expansion project included planning and implementing a six-aisle automated high-bay warehouse for raw material and packaging materials as well as -only a few hundred meters away- a high-bay warehouse with 17,560 pallet locations for finished goods with 10 aisles.
“The introduction of new automation deployments driven by strong warehouse management software (WMS) can maximize return on investment and minimize risks to supply chain operations. Combining Swisslog’s SynQ WMS solution, Mai Dubai was able to modernize their warehousing, distribution, and production operations by optimizing the performance of the various components while maximizing the storage capacity,” said Alain.
Swisslog’s SynQ is a modular, service-oriented software platform for warehouse management and material flow orchestration. SynQ, representing Synchronized Intelligence, gives the organization the precise functionality they need to optimize warehouse operations. It lit
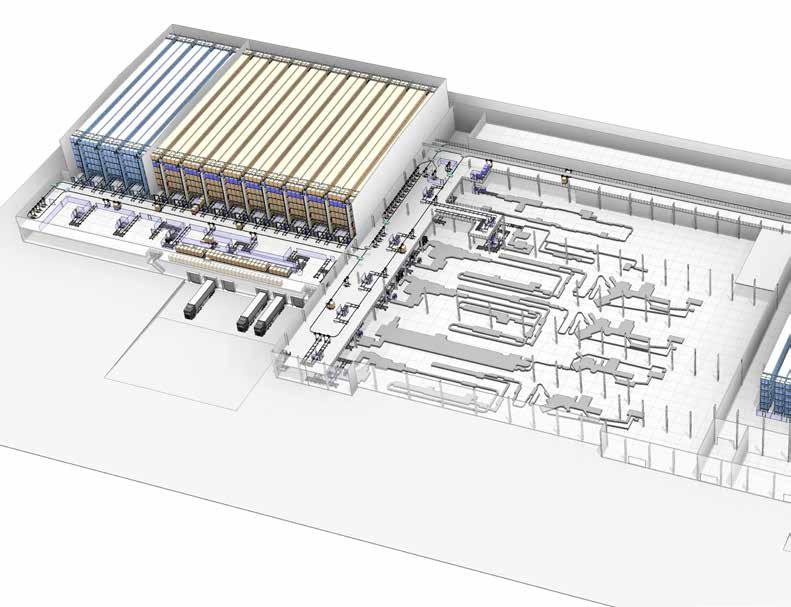
erally embeds intelligence in the operation and synchronizes the performance of their automated and manual warehouse equipment in the best possible way. It encompasses warehouse management (WMS), material flow (MFC/WCS), and automation control systems (ACS) functionality, along with an array of business intelligence tools to boost the warehouse performance. SynQ covers the full spectrum of an organization’s supply chain needs to optimize their warehouse operation in the era of interconnectivity, automation, machine learning, and real-time data and help them stay ahead of the competition.
“Our SynQ software is a future-proof solution offering efficient integration to 3rd party ERP systems, comes with integrated user-friendly interfaces for all the shop floor operations and condition monitoring of the entire site as well as administrative tasks. Our modular platform also
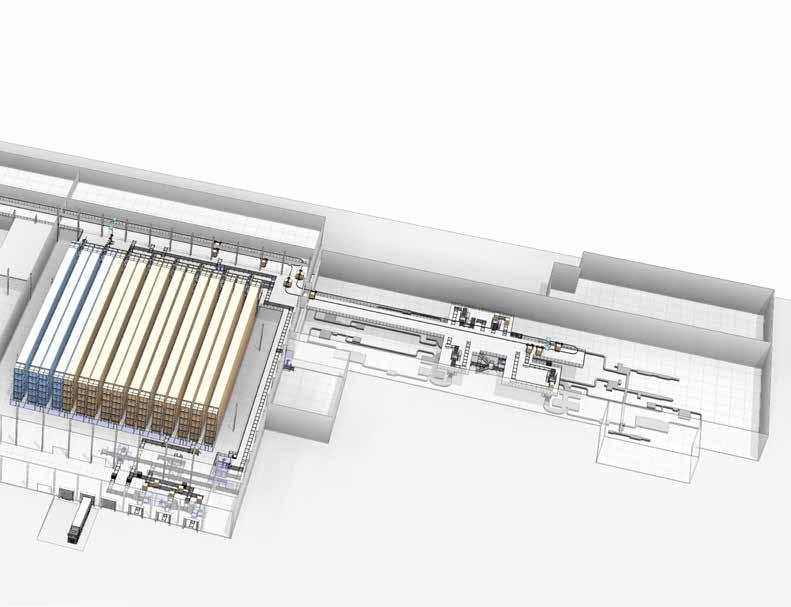
includes the visualization of the entire plant in 3D, VR and AR,” Alain commented.
Swisslog Vectura stacker cranes connected to the transport system will provide swift and efficient storage and retrieval processes in both warehouses. Fundamental to the material and goods flow concept is the over 1,100-meter long monorail system, which guarantees processoptimized transports - from receiving the raw products and packaging materials from warehouse to the production lines, transporting the Finished Goods from production lines to the finished goods warehouse, and to the shipping lanes in the distribution center. Within the configuration, a total of 44 Swisslog trolleys, each capable of carrying two pallets at a time, can travel along with the rail system.
Alexander explained, “Working closely with Swisslog was part of our expansion strategy. The implementation of an automated and digitalized
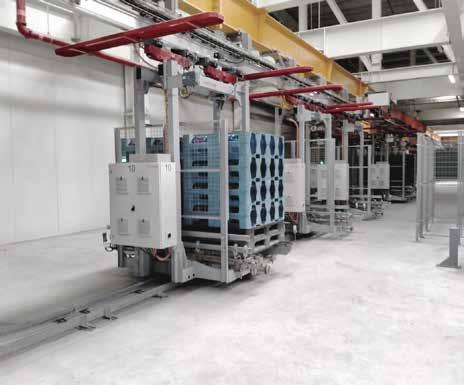
logistics solutions is part of -and contributes toour customer-focused approach. This initiative will help us not only to improve our production control but also allows for greater storage density and increased efficiency.”
HIGH-PERFORMANCE IT INFRASTRUCTURE
In addition to the installation of warehouse technology components, the mega expansion project implemented by Swisslog also includes advanced high-performance information technology (IT) infrastructure and control technology. The ProMove pallet conveyor system ensures the efficient flow of goods and the sequencing of pallets in receiving and shipping. Swisslog Warehouse Management Software is crucial to this process. Algorithms guide the movement of goods across two floors to the right locations at the right time.
FUTURE READY
The modular software platform also offers several big-data business intelligence tools that can be flexibly added over time. With its modular
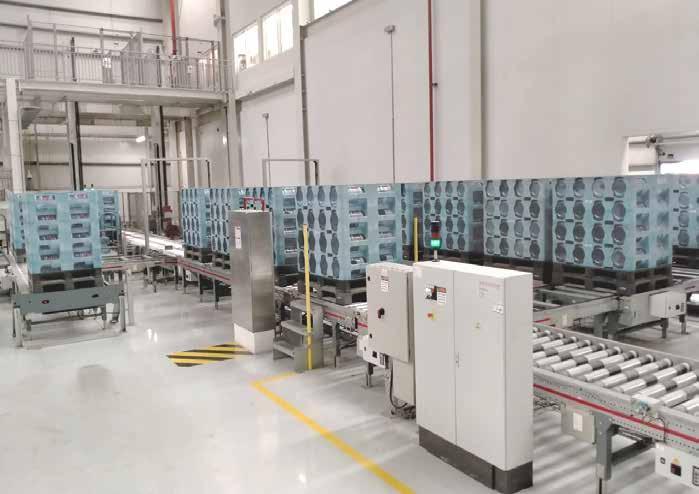
architecture and intelligent, automation-friendly design, the software helps Mai Dubai prepare for the changes that digitalization brings so the company can benefit from its opportunities.
“Implementing automation can help companies with achieving their best supply chain performance, which now acts as an indicator of resiliency and not merely cost management. In
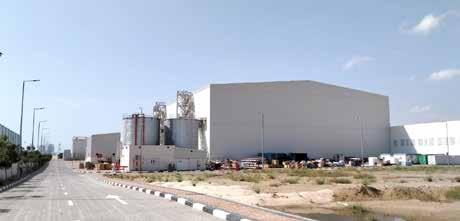
the current competitive and dynamic market, risk of disruption in the supply chain can cause issues with business continuity, losing competitiveness, reduced short-term financial performance. Automation can help companies deal with the complexities, increase the performance of supply chain and make it resilient for any kind of disruptions,” concluded Alain.