
3 minute read
SUSTAINABLE FUELS
OVERCOMING SUPPLY CHAIN CHALLENGES
Samer Kaissi, Country Manager Dubai and Northern Emirates at DHL Global Forwarding, writes about how diversifying supply chains can steer electrical vehicles in the right direction
Advertisement
Lured by the prospect of tax incentives and deterred by rising oil prices, a growing number of consumers are making the shift to Electric Vehicles (EVs). According to the latest industry figures, Ford recorded EV sales growth rate of 139%, Tesla reported 81% growth and Volkswagen 65%, as of May 2022. Deloitte anticipates that the world is on course to reach annual EV sales of 31.1 million by 2030.
This is encouraging news for EV manufacturers, who are grappling with securing supply chains. Shortages of key materials like lithium batteries, ongoing sanctions against Russia (a key market for raw materials like nickel), impact of COVID-19 lockdowns, amidst other regulatory challenges, could curtail manufacturers’ ability to meet growing demands.
Furthermore, raw materials necessary for EVs are mined only in certain parts of the world, and their lack of availability directly impacts prices. Batteries and electronic parts are largely sourced from Asia. In fact, China is a leader in the lithium battery market, with the country manufacturing 60% of global battery components. But the pandemic-induced lockdowns have badly affected global production and supply chains.
Diversifying supply chains To address such challenges in the future, there is a need to diversify supply chains. Moreover, the public and private sectors must adopt an integrated approach to secure the EV supply chain, right from the design and production of a new
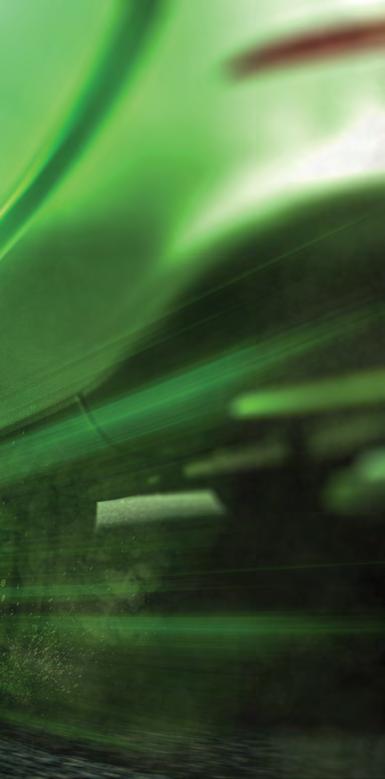
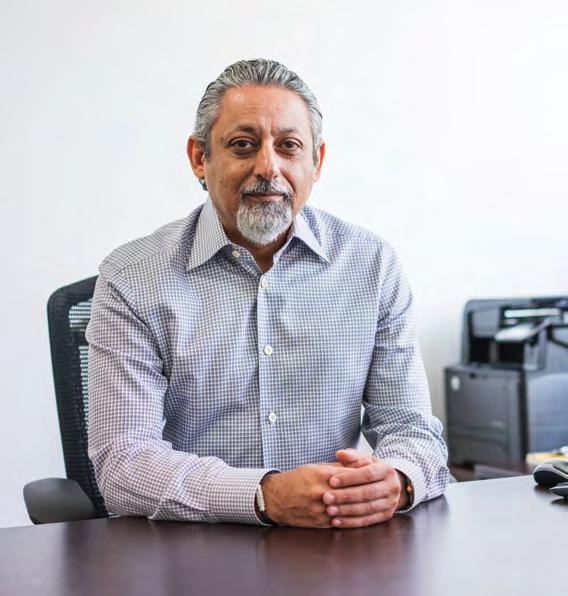
Samer Kaissi, Country Manager Dubai and Northern Emirates at DHL Global Forwarding
vehicle, all the way through reclamation and recycling programs, and beyond. Given that the automotive industry is undergoing drastic evolution, with convergence between engineering and modern technology, logistics companies must also adapt their offerings.
The UAE has set ambitious targets to transition to EVs, with Dubai aiming for government organisations to increase the number of purchased or leased electric and hybrid vehicles to 20% from 2025 to the end of 2029, and 30% from 2030. This is encouraging, but there is a need for compliant and cost-efficient supply chains that support EV development to support this growth.
The batteries powering these EVs will need maintenance, repair, and exchange, which in turn requires a way to transport replacements quickly and safely on a regular basis. Being able to transport them via freight makes this process far faster than ever before. But a conveniently located hub would accelerate the growth of EVs in the region. In anticipation of a booming lithium-ion battery market, DHL launched a 23,478-sq m EV and battery logistics hub in Dubai South earlier this year. It includes a 652-sq m EV battery storage area, which can be expanded to 2,000 sq m, to support future growth. It is the region’s first compliant facility for EV batteries and other dangerous goods. The hub enables the EV circular economy – batteries can be stored, recycled, repaired, and processed at end of life – ensuring long-term sustainability.
Addressing infrastructure bottlenecks There is an urgent need to manage the complexities of storing parts for different EV variants, amidst regulations constraints. Given that there is no standard battery size – lithium-ion batteries come as battery cells, modules, and packs – more logistical planning by automakers is needed as original equipment manufacturers (OEMs) have different sourcing strategies for all three.
PWC anticipates that the lithium-ion battery pack alone can account for up to 50% of the value of EVs. Battery prices, which had fallen in recent years, suddenly went up to an estimated USD160 per kilowatt-hour in the first quarter of 2022 from USD105 last year.
Many of these batteries are made by companies outside the traditional auto supply chain, which has created competition with legacy suppliers. Some EV battery suppliers are also developing expertise in manufacturing electric powertrains, which presents a shrinking potential market for suppliers and narrower margins as EV adoption rises. In short, suppliers that provide components for ICE vehicles will have to diversify to retain a share of the market, or risk falling revenues.
Auto makers, OEMs and aftermarket suppliers must invest in the right logistics framework to manage EV components, despite regulatory constraints. Access to the right infrastructure, including temperature-cooled shipping containers and managed customs-clearance solutions, can minimise the actual burden for business in the long run and help establish a reliable supply chain for EV production.