
10 minute read
COLD CHAIN
WHAT’S ON THE HORIZON FOR COLD CHAIN LOGISTICS
Ken West, Reefer Digital Development Manager at Maersk, shares his expert opinion on the future of cold chain logistics
Advertisement
When thinking about the current state of refrigerated logistics, two words come to mind immediately: challenges and innovation. Such different words, but intrinsically connected as one is the main cause for the other to come to life.
If you are shipping any cargo today, particularly if your products are perishable, you are certainly familiar with challenges. A global pandemic, delays, congestions, political instability, shortages, and several other issues are plaguing the world of container logistics and weakening the links of global cold chains. Supply chain challenges are sparking fascinating innovation efforts, among both established players in the market for perishable goods as well as small start-ups, in areas ranging from pure data aggregation to new methods for extending shelf-life.
There are huge opportunities to revolutionise and digitise the container logistics industry that is unfortunately still depending on unique paper copies for certain transport documents. But what is currently at the top of the wish list for cold chain customers?
Levels of visibility Visibility is becoming a buzzword within logistics. Typically, cold chain customers are looking for a level of visibility and control that can answer three simple questions:
When will my container arrive? Customers want to know the exact time their refrigerated container is ready for pick-up from the terminal or when the trailer truck will arrive with their goods at the destination. To meet this need, Maersk is currently seeing an increased use of GPS trackers mounted on containers and GPS signals coming from the truck driver’s smartphone. Machine learning is also being applied to achieve more accurate arrival estimations taking both historic transport times and weather forecasts into account.
Will my cargo arrive in the expected condition?
Given the pandemic, customers are no longer able to travel as easily to destinations to check the quality of their cargo upon arrival. Now they need to rely more heavily on data points collected during the journey, and here temperature is the most important parameter to look at.
More container carriers are investing in infrastructure which enables a remote data flow from the container, and several customers are even applying temperature loggers themselves on a few pallets inside the container. Despite this, we are still in the early days of having a fully connected cold supply chain:
The container temperature does not tell the full story of cargo which might also have travelled through packhouses and cold store facilities on both import and export side.
Transmitting temperature loggers have so far been too costly to apply on every single pallet or box of a shipment. Combining data from different sources into a single overview is a challenge, unless you have one party handling the entire cold chain.
There is ongoing work on quality prediction models which can estimate the remaining shelf-life of certain perishable commodities based on parameters measured during the journey, but these models will in future be heavily dependent on data input from across the entire supply chain. New technology, such as smart- labels and sticker sensors, will soon come to a more realistic cost level and thereby enable reliable shelf-life predictions.
Has my container been opened by any unauthorised parties?
Container contamination, or even theft of cargo, are becoming a growing challenge for cold chain customers. Different compartments of a refrigerated container can be used by criminals to place illegal substances, unknown to the shipper or the receiver of the goods. Therefore, it is necessary for customers to know whether their container has been opened while in transit, especially during inland transportation or storage. Several types of door-opening and light detection sensors are becoming available in the market, and we are seeing an increased interest from customs service and import/export authorities to collaborate with logistics providers on data sharing to achieve more intelligent inspection routines, and therefore reduce unnecessary disruptions to customers’ supply chains.
Enabling mitigating actions Overall, the logistics industry is undergoing transformation in terms of digitization and data offerings, with great momentum around new visibility related solutions and technology. Once the above mentioned three customer needs for visibility have reached a satisfactory level, then comes the next question to the logistics providers: which mitigating actions can I take here and now if things are not going according to plan?
Serving customers with data is crucial, but the real benefits will only be achieved if the information is up-to-date, and everyone can interpret the aggregated data in the same way to take the right strategic decisions based on it.
That will be the next big leap in terms of optimising global supply chains for perishable cargo to ultimately avoid cargo damage, contamination, or loss.
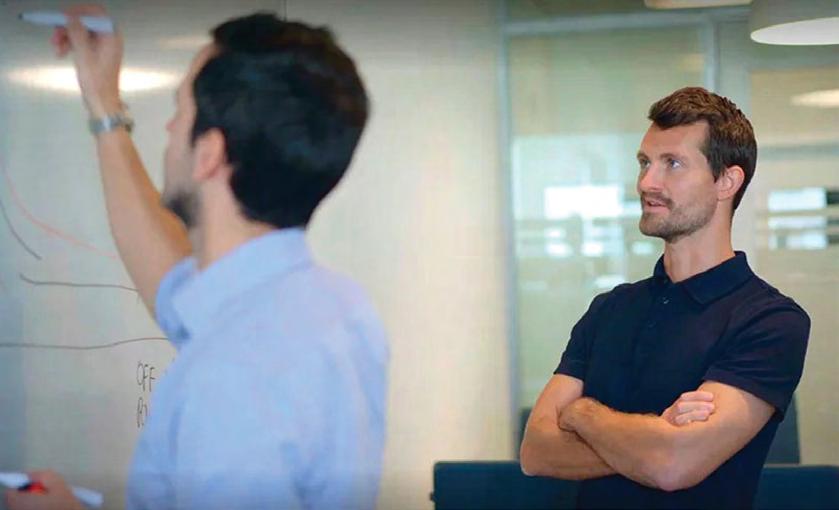
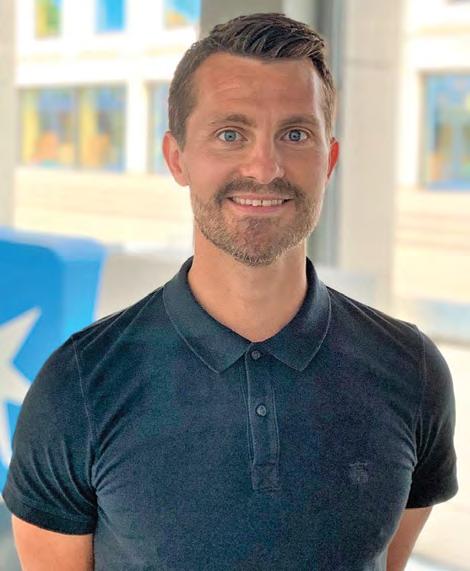
Ken West, Reefer Digital Development Manager at Maersk
TECH FOR CHANGE
Soham Chokshi, CEO and co-Founder of Shipsy, discusses how technology is imperative to enable ESG results and drive sustainable logistics
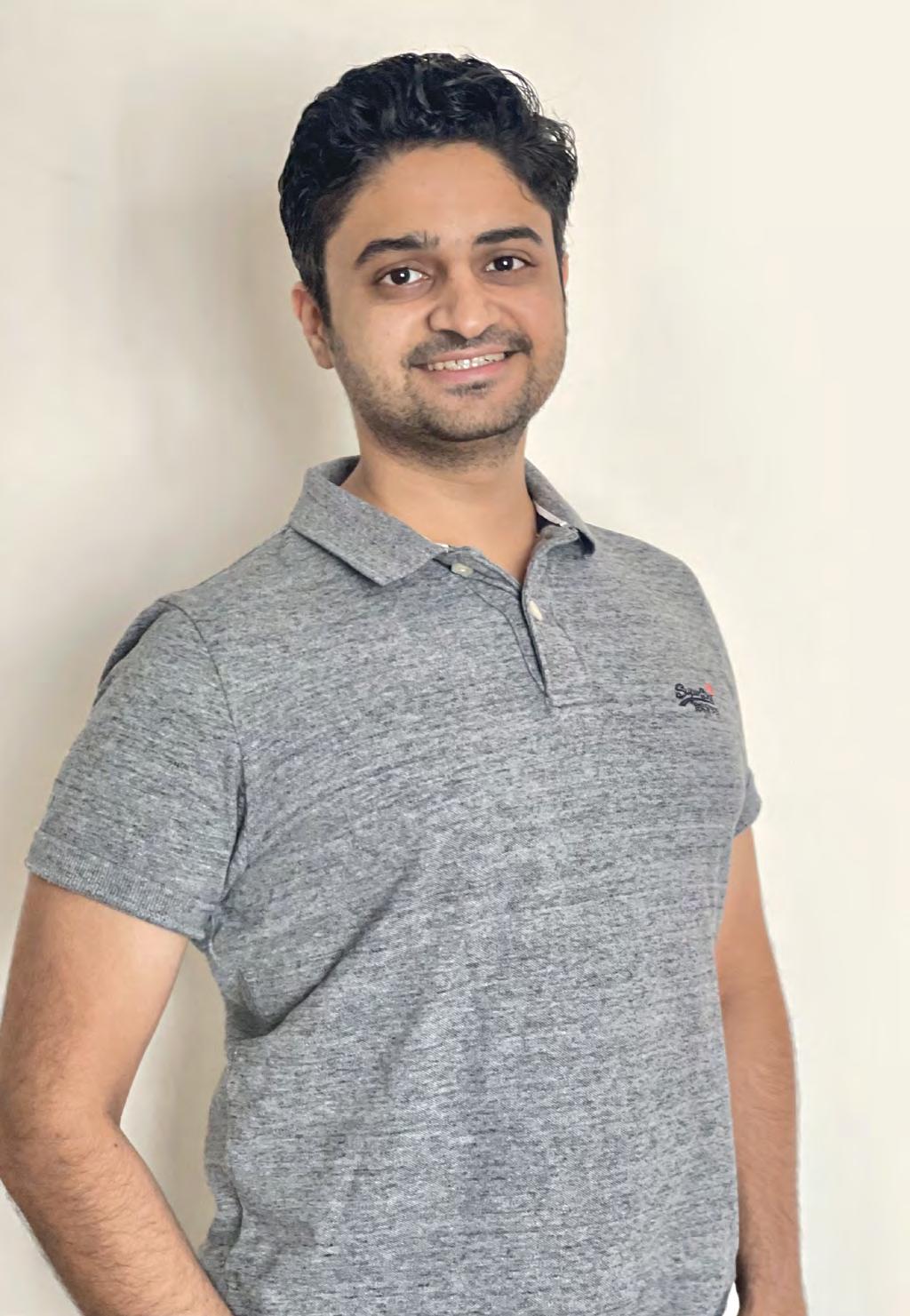
When Soham Chokshi, Dhruv Agrawal, Himanshu Gupta, and Sahil Arora established Shispy back in 2015, their focus was on addressing the challenges that existed in the last-mile ecosystem.
But soon they realised that supply chain and logistics sectors are all connected and that lastmile inefficiencies were only the tip of the iceberg. They saw an alarming need to marry the physical and digital parts of logistics. This in turn resulted in massive expansion of the platform across first, middle, last-mile, cross border logistics and intermodal freight movement.
Today, Shipsy has grown into a sprawling business empowering the biggest retailers, manufacturers, eCommerce providers, on demand delivery brands, and logistics service providers to build resilient, agile, and automated supply chain and logistics processes. Shipsy’s intuitive platform provides complete visibility of first, middle and last-mile operations, unlocks operational efficiency, and leverages real-time analytics to empower businesses to make data driven decisions, better manage costs, boost customer experience, and reduce carbon emission.
Rising environment pollution Carbon emissions pose an enormous threat to the environment, living species, and businesses with some hard facts. Melting glaciers, growing cases of forest fires, and floods, among other natural calamities, are nature’s way of voicing her state of depletion.
The consistent rise in global average temperature is triggering unprecedented floods, especially in Australia, Asia, and South America. Growing carbon emissions are a major contributor to these alarming figures. >>>
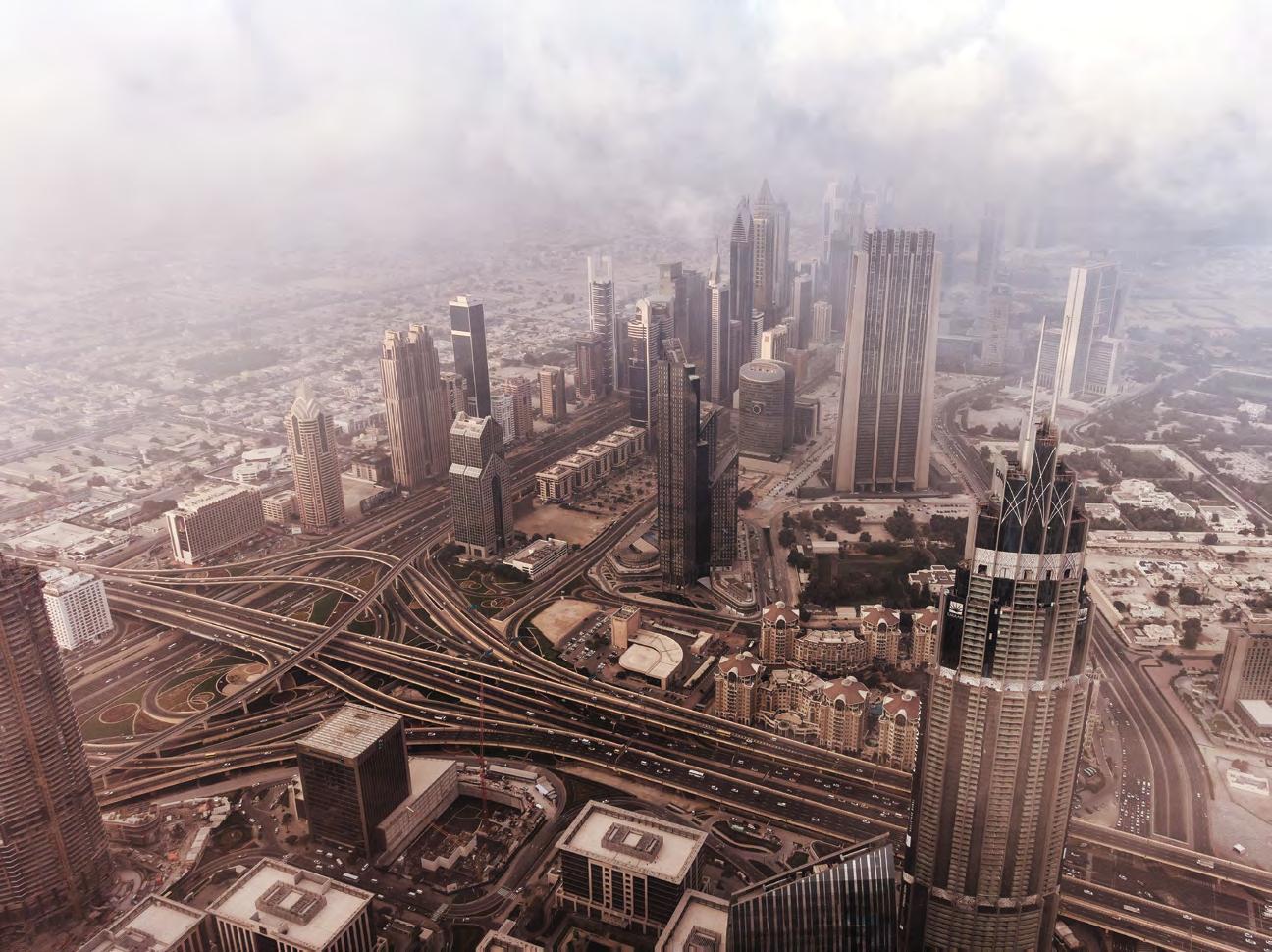
Unfortunately, today 24% of global CO2 emissions can be attributed to the transportation sector, and 30% of this comes from trucks carrying freight. Going by the numbers, CO2 emissions from road freight transportation have grown by 20% since 1995. These figures can be overwhelming.
Taking just the region into consideration, in 2018, the Middle East and North Africa emitted 3.2 billion tonnes of CO2 and produced 8.7% of global greenhouse gas emissions (GHG) despite making up only 6% of the worldwide population, according to reports. Soham says: “As supply chain and logistics stakeholders, we can no longer ignore these figures and should consider it our responsibility to make the movement of goods sustainable. On the brighter side, governments, especially in this part of the world, are taking solid actions to battle growing carbon emissions.”
Countries in the region have chalked out stringent penalties for those flouting environmental norms. Depending on the kind of violation and extent of damage caused to the environment, the Abu Dhabi government can levy fines on responsible parties up to Dhs1 million. “This can significantly impact the bottom lines of businesses that are heavily dependent on logistics operations,” Soham suggests.
Quick yet sustainable shipping With environmentalism going mainstream, modern customers are gradually showing signs of purchasing from brands that are socially responsible and are taking measures to reduce their carbon footprint, especially in the last mile, says Soham. “But if one follows the trend, this is not surprising.”
A Global Customer Insights Survey revealed that 35% of consumers
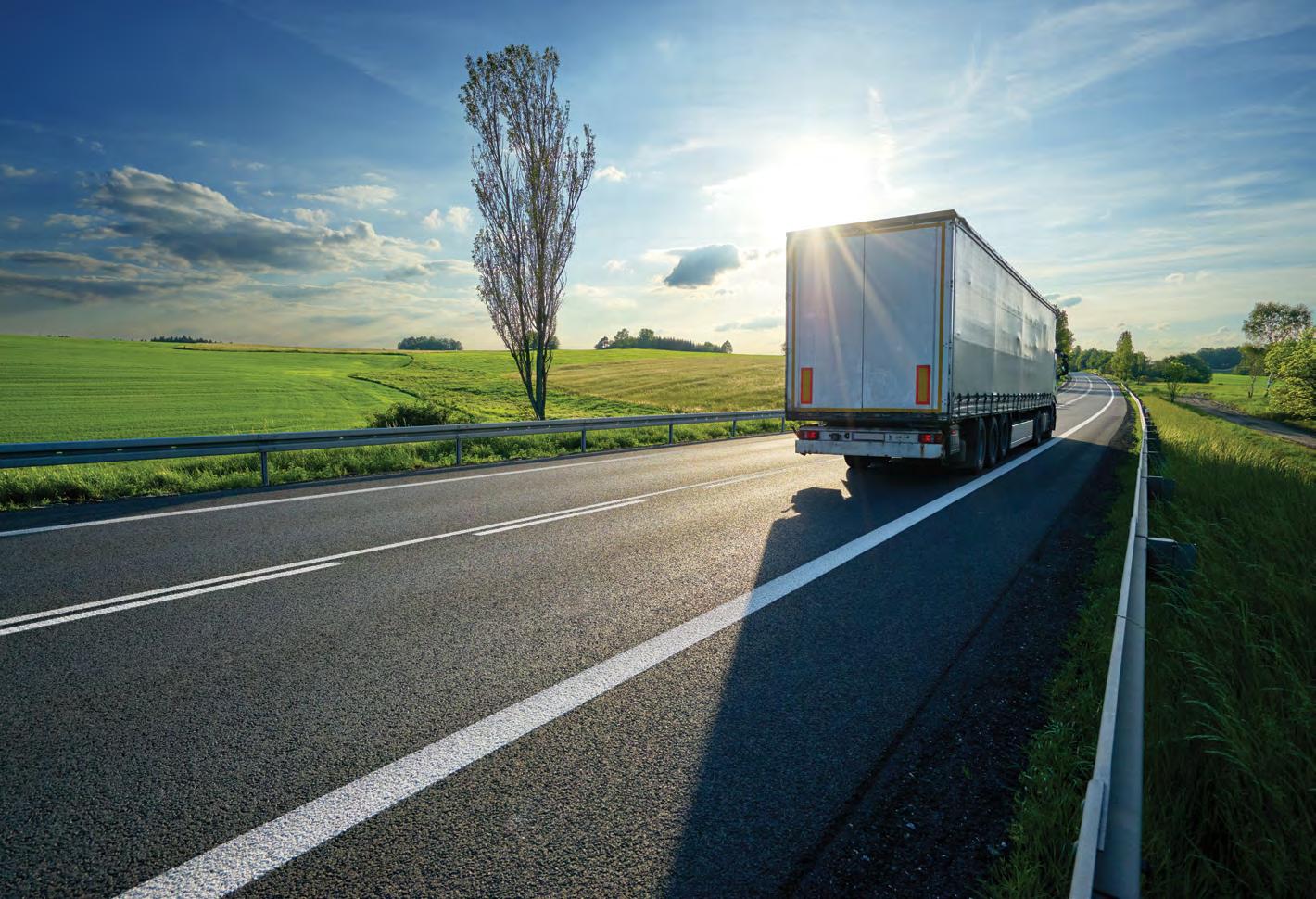
choose sustainable products, and 37% want products that come with environmentally friendly packaging. “Expectations around eco-friendly deliveries can be considered an organic progression. Especially in the Middle East, where customers are more empowered and aware,” he notes.
He adds: “At the same time, customers also love fast deliveries and are willing to pay more for the same. Ensuring deliveries with turnaround times of less than 30 minutes tends to consume more resources, more delivery trips, and more fuel, leaving behind bigger carbon footprints.
“So, how does one balance customer experience and an organisation’s sustainability goals? The answer lies in deploying advanced logistics management solutions like Shipsy. What really inspires me is that a recent survey by Nielson highlighted that 73% of eCommerce customers say they would want to change their purchasing behavior to reduce any negative impact on the environment.”
Driving logistics sustainability Shipsy’s smart logistics management powered by AI helps businesses reduce their carbon footprint by ensuring lesser miles traveled, shrinking trip volumes, improving first-attempt success rates, gaining better visibility of carbon footprint and more.
He explains: “We are making this possible through our technology by improving address accuracy, driving intelligent route planning, optimising vehicle capacity, ensuring dynamic clubbing of orders, improved customer communication, eliminating diversions and idling, leveraging intermodal transportation, and providing sustainability dashboards.”
Inaccurate customer addresses are a massive challenge in the Middle East. “It increases last-mile delivery attempts and subsequently results in greater carbon emissions,” Soham reveals.
According to Statista, last-mile delivery failure rates range from 15% in the UAE to 40% in Saudi Arabia, and this can impact eCommerce revenue worth USD7.42 billion in the Middle East.
“Shipsy’s advanced geocoding capabilities seamlessly convert physical addresses into highly accurate latitude/longitude- >>>
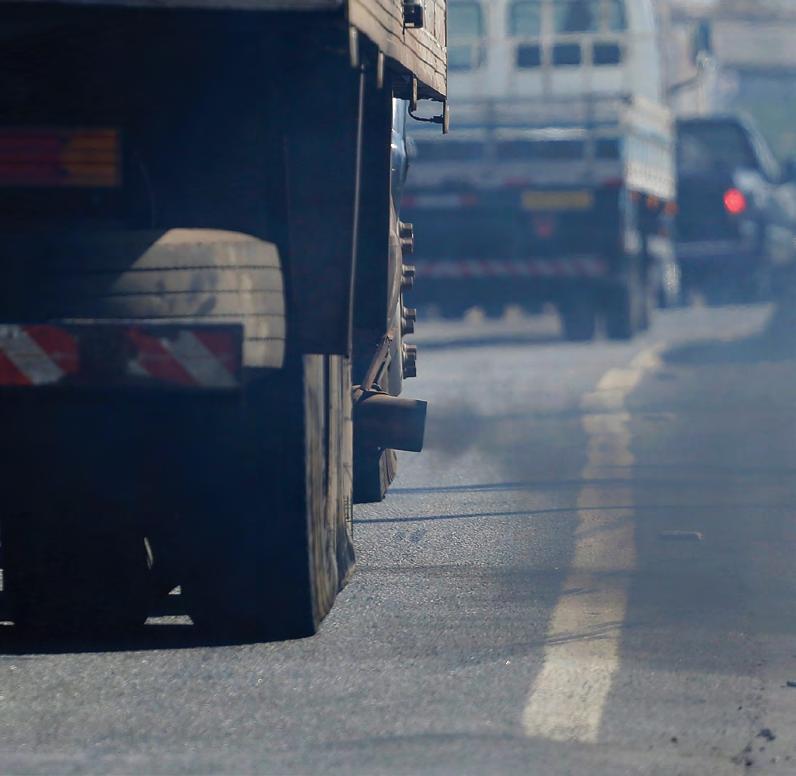

based locations and drastically eliminates delivery failures due to incorrect addresses. This boosts profitability and brings down delivery reattempts,” he shares.
With regards to driving intelligent route planning, Shipsy considers multiple constraints like fuel consumption, turnaround times, proximity, cost, speed and more before finally creating routes to travel from point A to B to C. He adds: “We also enable businesses to eliminate empty miles by ensuring round trips are productive. Research reveals that almost 40% of trucks often run empty, resulting in emissions that could have been avoided.”
Furthermore, Shipsy’s capacity optimisation algorithms consider multiple factors while planning routes. It reflects constraints like delivery location, weight, volume, service type, vehicle make, storage type, and more when allocating delivery tasks. “We empower businesses to optimise capacity by 31% and reduce delivery trips,” Soham notes.
Through dynamic clubbing of orders, Shipsy ensures that in case subsequent orders fall under the same radius on either side of the already planned delivery route, the system clubs them and assigns them to the same driver, significantly bringing down trips needed for pickup and delivery tasks. “Our customers are experiencing a 14% increase in deliveries per driver by using the dynamic order clubbing capability,” he explains.
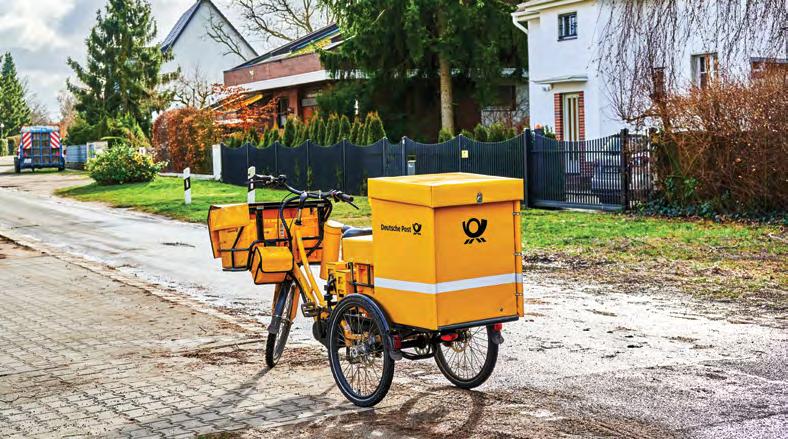
Making logistics sustainable Shipsy’s platform is accompanied by datarich and intuitive sustainability dashboards. These dashboards help delivery stakeholders monitor carbon emissions at a granular level throughout disparate legs of a logistics network. Soham says: “This improves logistics planning and delivers actionable insights on shrinking an organisation’s carbon footprint.”
He adds: “In a nutshell, three critical factors will drive businesses to make logistics sustainable. One, government regulations and compliance. The second is customer expectations, and the third is the need to reduce operational costs. These factors will also trigger the need for enterprises, shippers, retailers, and logistics service providers to embrace advanced logistics management solutions.”
According to inhouse reports, with Shipsy’s end-to-end smart logistics management solution, businesses across the globe are reducing their carbon footprint by curbing distance traveled by 5% and decreasing trip volumes by 6%.
He concludes: “Let’s play our part in restoring the balance that allows nature, wildlife and human lives to thrive in the same ecosystem.”
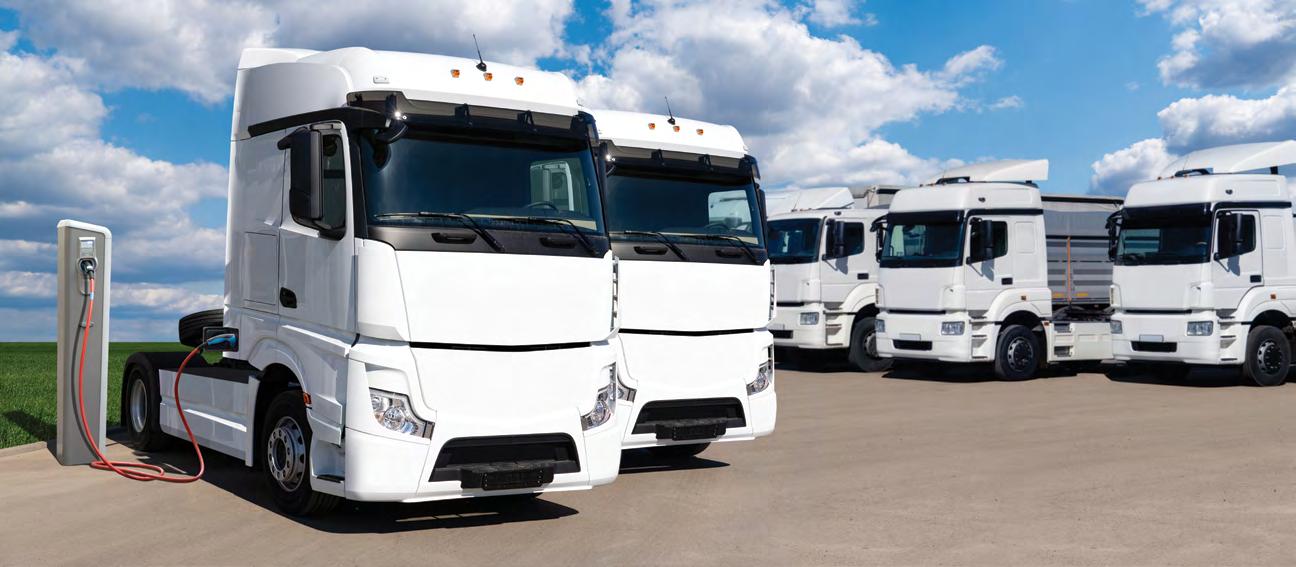