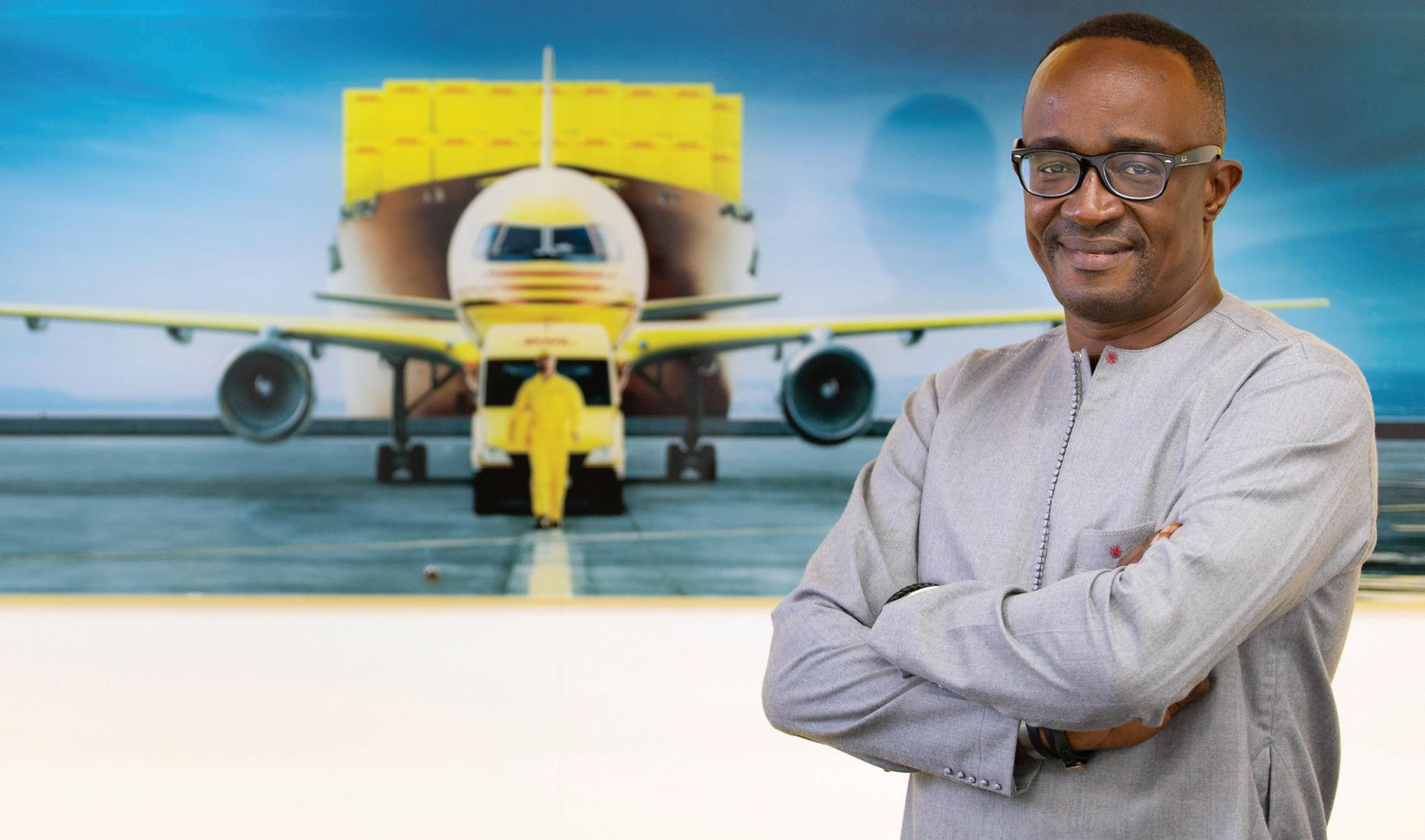
7 minute read
TALKING POINT
LNME
TALKING POINT
Advertisement
THE FUTURE OF LOGISTICS
Amadou Diallo, CEO of DHL Global Forwarding Middle East and Africa, tells us about the five lessons learnt from a global pandemic
ore than a year since
Mthe first COVID-19 case came to light, uncertainty still drives our decisions. Despite widespread vaccinations and control mechanisms put in place across the globe, we continue to fight a prolonged battle. As challenging as the situation may be, it contains within it the seeds of learning and growth. Here are five lessons distilled from the pandemic, critical to the future of our business.
1. PEOPLE OVER PROFITS
Best-in-business companies have always operated with this ethos. But COVID-19 really drove this lesson home. A people-centric approach during challenging times is not just ethically correct, but it also makes sound business sense. If employees are happy and motivated, their productivity is greater than those who feel undervalued or unappreciated. Businesses should remember that it’s their people who work to achieve the profit in the first place, therefore they must always
Amadou Diallo
be priority. People-first companies are not only great places to work, they are also profitable enterprises.
2. CRISIS SITUATIONS HELP TO BENCHMARK RESILIENCE
Uncertainty and volatility are the only certainty today. Logistics providers had to showcase real strength in situations when things are not going according to plan. We expect the unexpected, and plan for it. This builds resilient organizations.
From shipping large quantities of personal protective equipment (PPE) to communities that urgently needed it, to shipping shipping vaccines around the world so they can be used to save lives, logistics providers have been crucial in the fight against the pandemic. We have the monumental responsibility of distributing approximately 10 billion doses of vaccines over the next two years.
Uncertainty also drives flexibility and agility. Businesses and people
THE FUTURE OF LOGISTICS
have demonstrated incredible agility and resilience in adapting to the new situation. New transport solutions and connections have been set up without anyone being able to travel. Digital such as a new Transport Management System enabled supply chains to keep going.
3. REMOTE WORK, WORKS
Technology has enabled us to stay connected with colleagues through the pandemic, and manage businesses across geographies. Though frontline workers in the operations are not able to work from home, the pandemic proved the power of teamwork in logistics. If there is one thing that the pandemic has taught us, it is that together we are stronger. For a successful transition to remote work, trust is one of the most powerful leadership skills. A global company can be managed remotely – but not without trust. You have to trust your people and equally important, tell them that you trust them.
4. DIGITALIZE TO THRIVE
In the UAE, we have witnessed the exponential rise of e-commerce, supply chain innovation and digital transformation, which are contributing factors to the growth of logistics sector. As many parties are involved in getting goods moved around the world, digitalisation has the potential to ease not only the life of shippers but make processes even faster and leaner. The recently launched customer platform myDHLi is one example, while Saloodo!, the digital road freight solution platform, is leading the movement to ‘Uberize’ trucking. It helps carriers manage their fleets better and optimize the capacity of their full truckload (FTL) shipments.
5. WE NEED MORE GLOBALIZATION
A globalized world stands not only for trade, but also for the free flow of information, vital supplies and people. Back in April last year when air freight capacity was severely impacted due to border closures, DHL Global Forwarding had operated dedicated flights carrying PPEs as well as essential supplies from China to Middle East and Africa via Dubai, ensuring a steady supply of these life-saving items especially for frontline healthcare workers.
We are learning to share information, and this is resulting in growing prosperity, not only economically but also socially and socio-culturally. Without a globalized world we wouldn’t be able to fight this pandemic. We hope that the level of globalization will even increase after COVID-19, which will put us in a stronger position to face existing and future challenges.
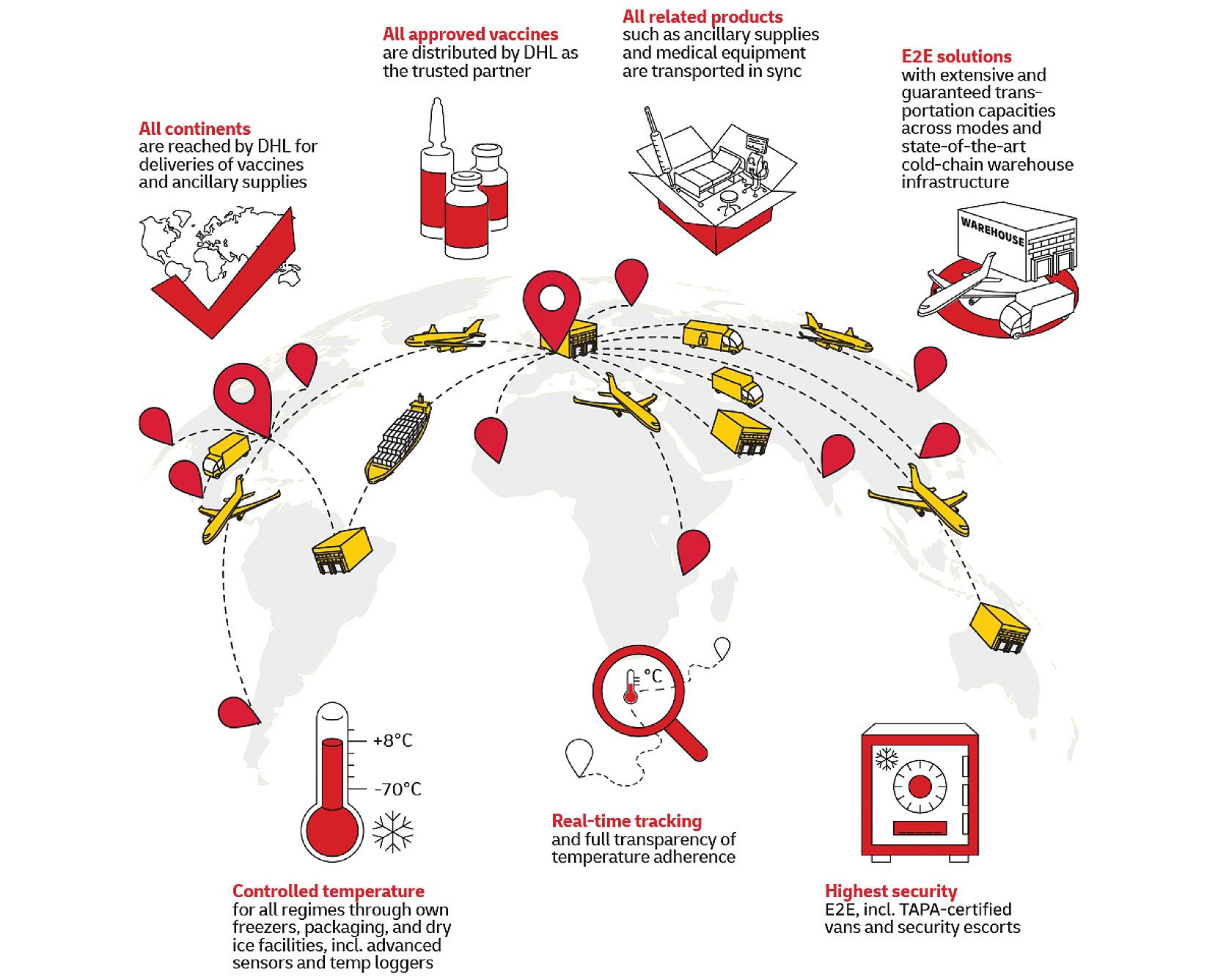

LNME
WAREHOUSE
IS YOUR WAREHOUSE A CANDIDATE FOR AUTOMATION?

BY DAVID DRONFIELD, GENERAL MANAGER, SWISSLOG MIDDLE EAST
obotic material handling
Rsystems, such as pallet shuttles and goods-to-person AS/ RS systems, are proliferating because they are ideally suited to meet the needs of today’s warehouses. Offering exceptional storage density, high throughput, enhanced sustainability and improved accuracy and productivity, these systems are helping warehouse operators and supply chain managers deal with SKU growth, fluctuations in demand and changing customer expectations.
In the Middle East and North Africa (MENA) region, the increase of demand and use of e-commerce and e-retail has forced the logistics sector to work towards increasing productivity and costefficiency. According to a recent report by Statista, the value of e-commerce warehouse usage is expected to reach 500 million USD in the Middle East region by 2024, from 180 million USD in 2018 and the overall warehouse automation market in the region is expected to reach a value of 1.6 billion USD by 2025.
Some operators with older warehouses may feel left behind by this new wave of warehouse technology. They may believe they have no choice but to live with the limitations of their current processes and systems or may even be considering investing in a new build to address the challenges they face. Fortunately, there is a third alternative: adding automation to the existing facility.
RETROFITTING WAREHOUSES WITH ROBOTIC AUTOMATION Unlike older mechanized approaches to warehouse automation, today’s robotic-
IS YOUR WAREHOUSE A CANDIDATE FOR AUTOMATION?
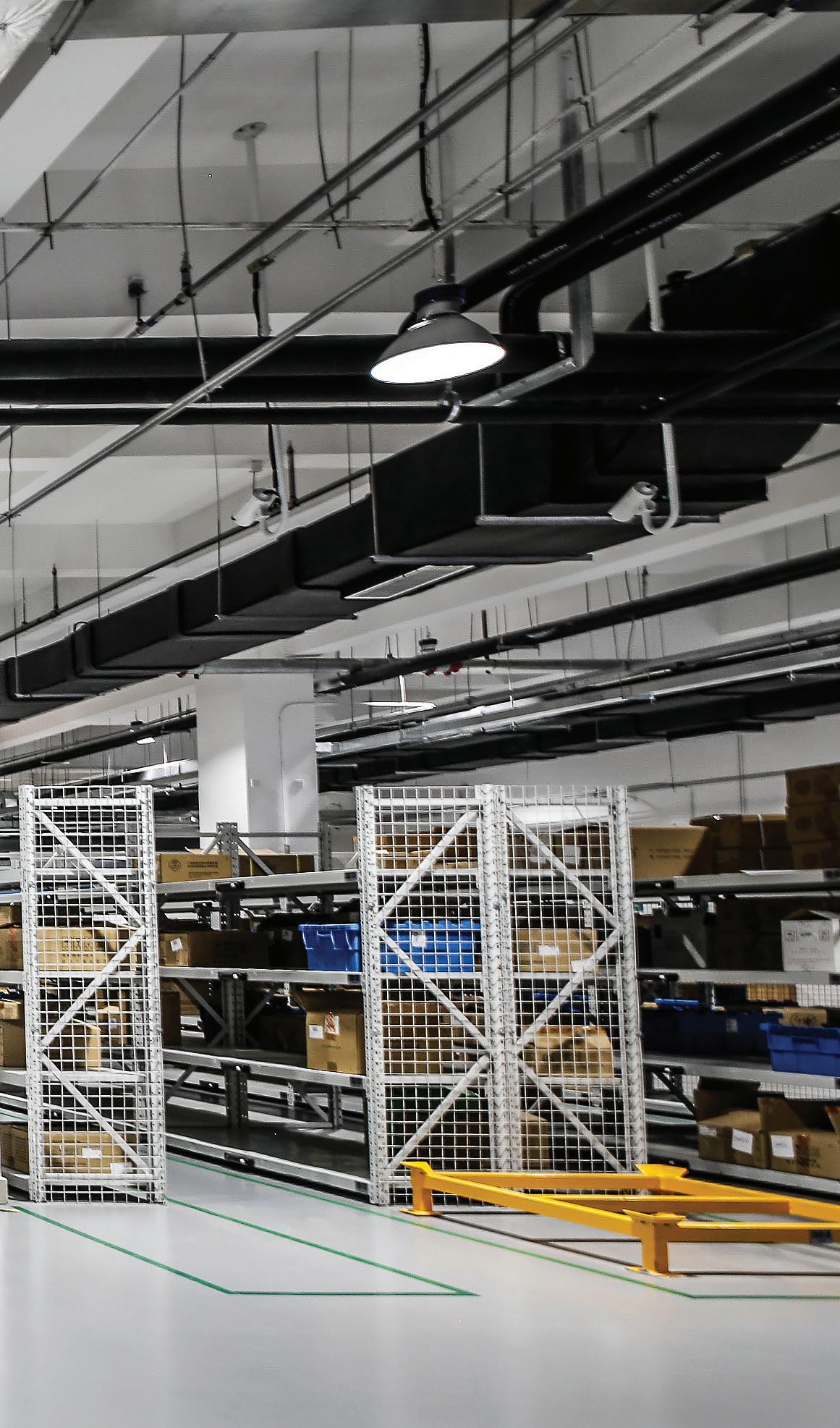
based systems are adaptable to their environment. Their flexible configuration options allow them to work in a variety of building shapes and sizes and even around obstructions such as columns. They also feature a modular design that enables a phased approach to implementation that can allow the warehouse to continue to serve customers while automation is deployed.
There are some challenges that may need to be addressed in older facilities, such as cracked or uneven floors. However, it’s much less expensive to repair or replace a cracked floor than to build a new facility. And lower capital costs are just one of the many benefits you can realize by adding automation to an existing warehouse.
ASRS systems, such as Swisslog’s PowerStore pallet shuttle, can deliver up to 60% more storage capacity than exist“THE SWISSLOG SITE ASSESSMENT PROCESS IS DESIGNED TO HELP YOU DETERMINE THE FEASIBILITY OF YOUR FACILITY TO ACCOMMODATE AUTOMATION AND IDENTIFY ANY LIMITATIONS THAT MUST BE ADDRESSED BEFORE AUTOMATION CAN BE DEPLOYED.”
ing shelfing or pallet storage, expanding warehouse capacity and freeing up space for other processes. In each-picking applications, goods-to-person AS/RS systems, such as AutoStore and CycloneCarrier, deliver productivity improvements of 200% to 300% with picking accuracy of 99% or better.
Automation can also reduce the environmental footprint of the facility by minimizing interplant and intra-plant transportation requirements, and the automation software delivers better visibility into product inventory, enhanced performance reporting and synchronization of manual and automated processes.
In short, you get the full benefits of today’s data-driven, robotic, and flexible automation technologies faster and at lower cost than you would by building a new automated warehouse.
THE SWISSLOG RETROFIT PROCESS The first step in adding automation to an existing building is a site assessment. The Swisslog site assessment process is designed to help you determine the feasibility of your facility to accommodate automation and identify any limitations that must be addressed before automation can be deployed. One of the benefits of working with Swisslog is that we offer a full range of pallet-handling as well as case and each-picking technologies, allowing us to tailor solutions to specific structural requirements as well as density and throughput objectives.
Regardless of the automation system selected, implementation must be carefully managed to minimize disruption on current operations. Our process can often be accomplished while the facility continues to serve customers using established manual processes.
One approach that has been successful is to consolidate inventory in one area of the warehouse to free up space for the initial phase of the automation deployment. The first module of the automation system is then deployed and brought online as a pilot and the warehouse operates in hybrid manual-automated mode while the next module is deployed. Alternately, we’ve worked with customers who have been able to transfer some inventory to secondary locations to free up space for the first phase of implementation. Once the first module is deployed, inventory is transferred back to the facility and the increased storage density provided by the automation system can be leveraged to free up space for additional modules.
GIVING NEW LIFE TO OLDER WAREHOUSES If you’re dealing with SKU proliferation, experiencing deteriorating service levels, struggling to maintain efficiency and productivity goals, or having trouble recruiting and retaining labor, a warehouse automation project can solve your operating problems while extending the life and value of your warehouse.
David Dronfield, General Manager, Swisslog Middle East
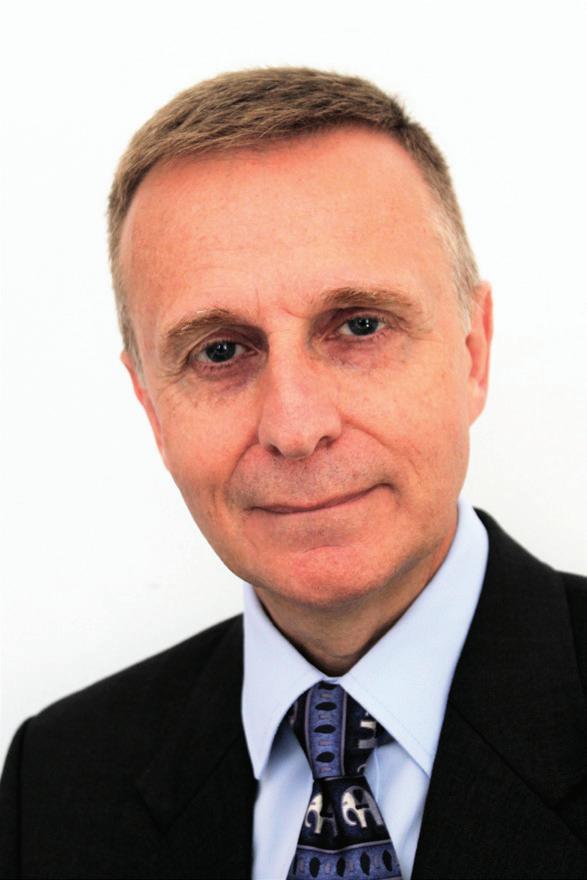