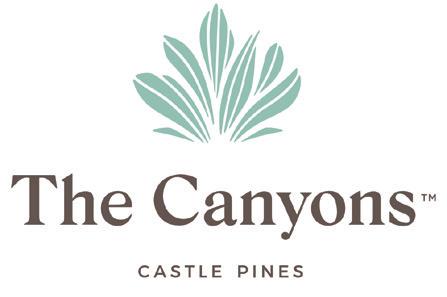
18 minute read
A new way to live in Castle Pines.
The Canyons At A Glance
• 1,270 acres, located east of I-25 in the City of Castle Pines, between the Castle Pines Parkway and Happy Canyon Road interchanges.
Advertisement
• 2,000 single- and multi-family homes by a variety of builders.
• Single-family home options will include ranch, two-story and patio plans; multi-family home options will potentially include duplexes, triplexes, cluster homes and townhomes.
• Community architecture will represent authentic regional building styles, including Modern Colorado, Modern Prairie, Colorado Ranch and Chalet interpretations.
• Located within the well-recognized Douglas County School District, children in The Canyons will attend Timber Trail Elementary School, Rocky Heights Middle School, Rock Canyon High School, as well as nearby private and charter schools.
• 12 acres within Shea Homes’ portion of The Canyons will be dedicated to future public schools.
• An initial monthly homeowner assessment is anticipated to be approximately $168.75/ month per household as of March, 2020. This is a combination of a $138.75 HOA fee and a $30 Metro District fee. The HOA fee covers the ownership, operations and maintenance of The Canyons and Canyon Village amenities, as well as residential trash and recycle services and community engagement. The Metro District fee covers the maintenance of all district amenities including parks, trails, arterial landscaping, fencing and open space areas.
• Property tax is estimated to be about 1.19% of the sales price of the purchased home, which is in addition to the HOA and Metro District Assessments.
• Water/Sewer supplied by the Parker Water and Sanitation District.
• Natural Gas services provided by Black Hills Energy.
• Electric service is provided by Intermountain Rural Electric Association (IREA). The city of Castle Pines is known for its natural beauty, and offers more than 500 acres of open space and over 70 acres of active parks, and provides easy access to downtown Denver and Denver International Airport.
Planned Community Amenities
• We envision the future Canyon House to be equal parts gathering space and wellness place. With community rooms and outdoor decks for small events, movement and fitness studios for a little self care. And a pool for relaxing days in the sun. In other words, the perfect place to spend time on your terms.
• From chef-inspired, seasonal menu items to creative cocktails, craft beers and wine, our food and beverage offerings take drinking and dining local to the next level.
• Resort-style pool
• Pickleball courts with shelter
• Outdoor seating and manicured lawn areas for smaller community gatherings, classes or events
• Playground areas
• Outdoor fire pit
• The Green is The Canyons’ central community park, where families will meet for events and concerts.
• The Exchange Coffee House & Information Center is the first amenity to open at The Canyons. A gathering space where visitors and residents can meet for coffee and conversation, it’s also where prospective homebuyers will start their tour of The Canyons, ask questions, and get information on home collections and the community.
Planned Natural Amenities
• Almost 1/3 of the community is dedicated to parks and open space, with a variety of large grassy areas, playgrounds, community gardens, shade structures, picnic areas and more.
• A network of approximately 15 miles of hard and soft-surface trails will meander throughout the community, accompanied by a variety of trail heads for hikers, bikers and walkers.
• We are committed to respect the land that was here before us, and re-establish what may have been lost during construction. So our landscaping includes the utilization and re-seeding of natural plants and grasses that will grow and transform over time. It will take a little time for this refined and carefully considered landscaping to mature, but it will be well worth the wait.
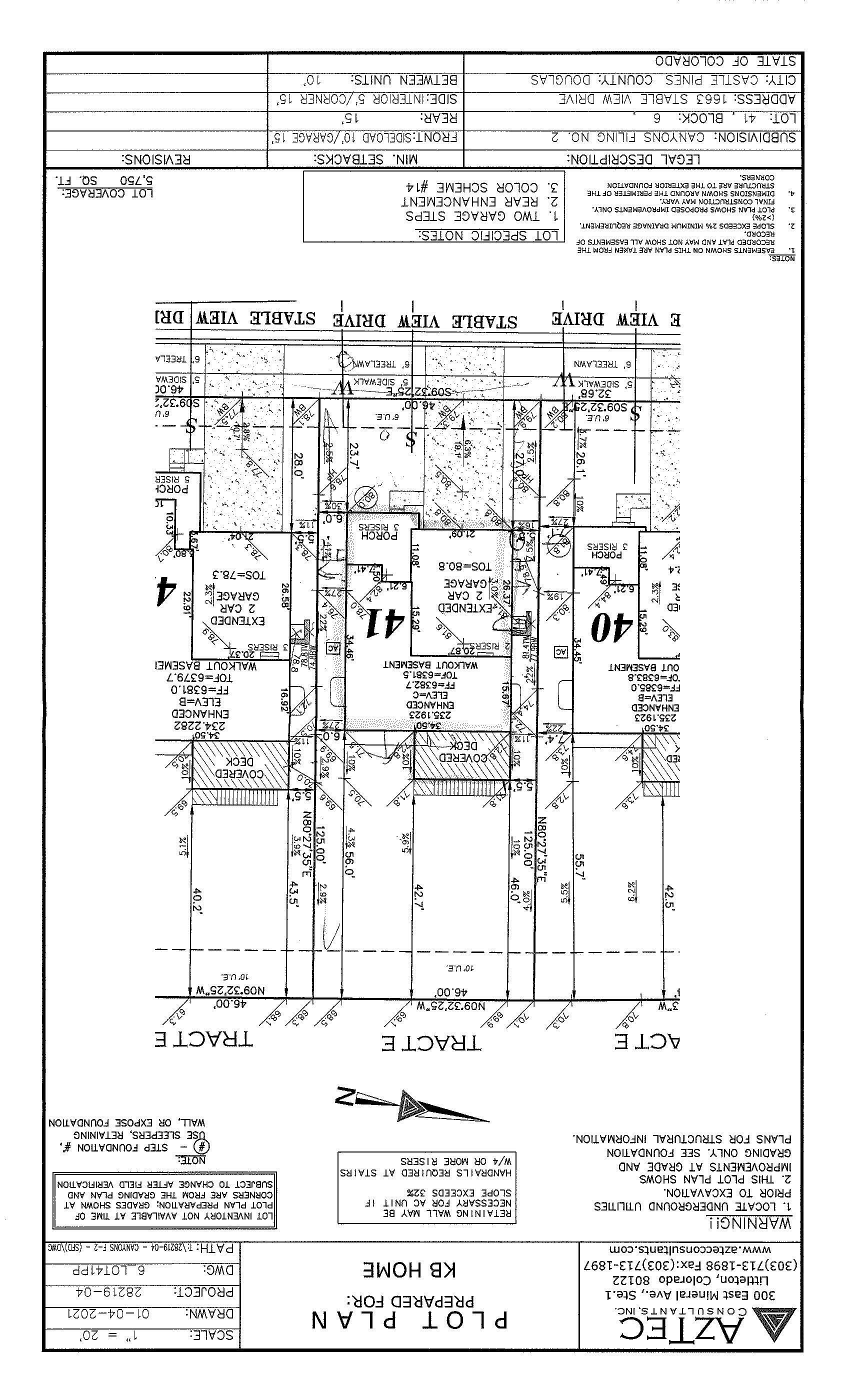

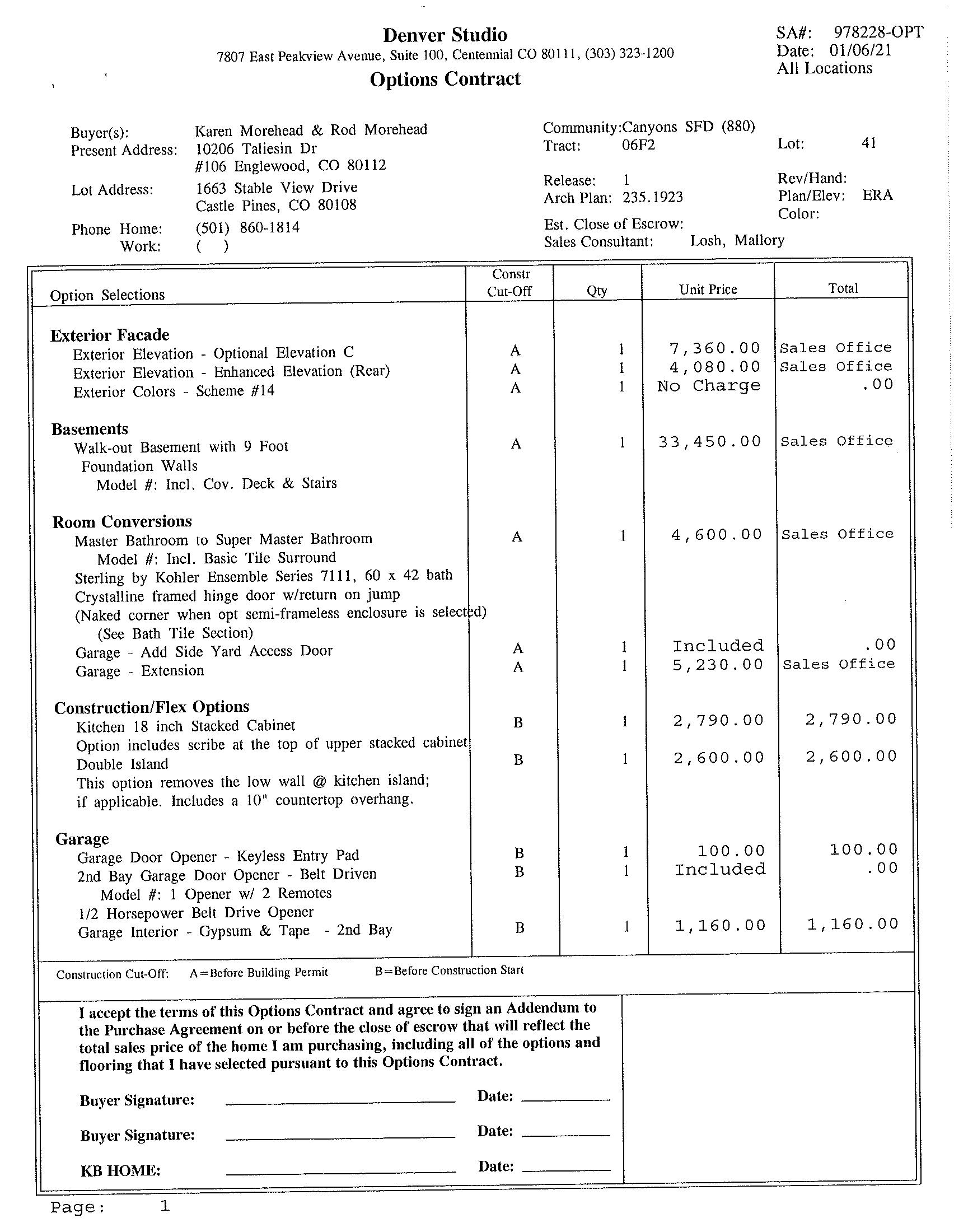
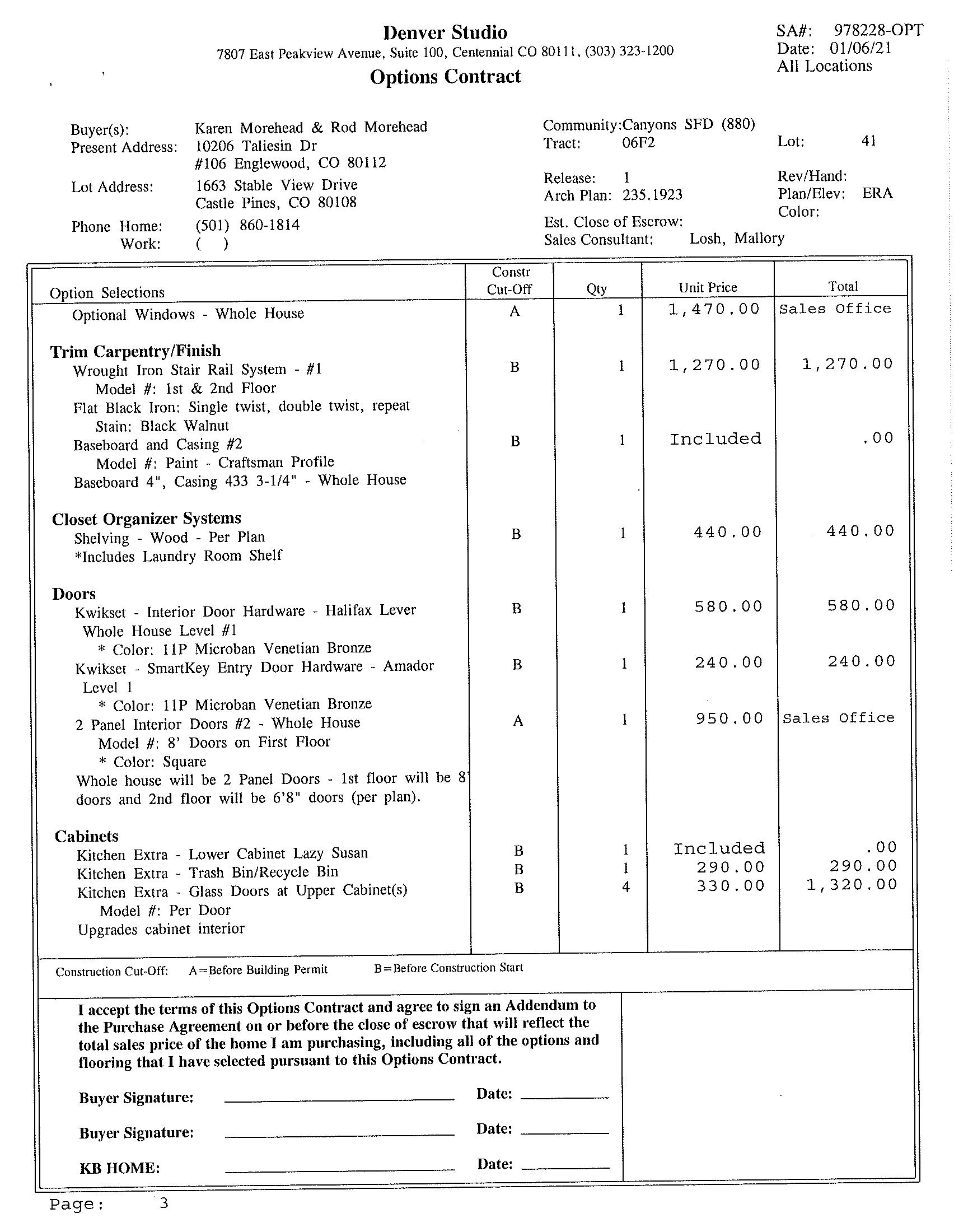
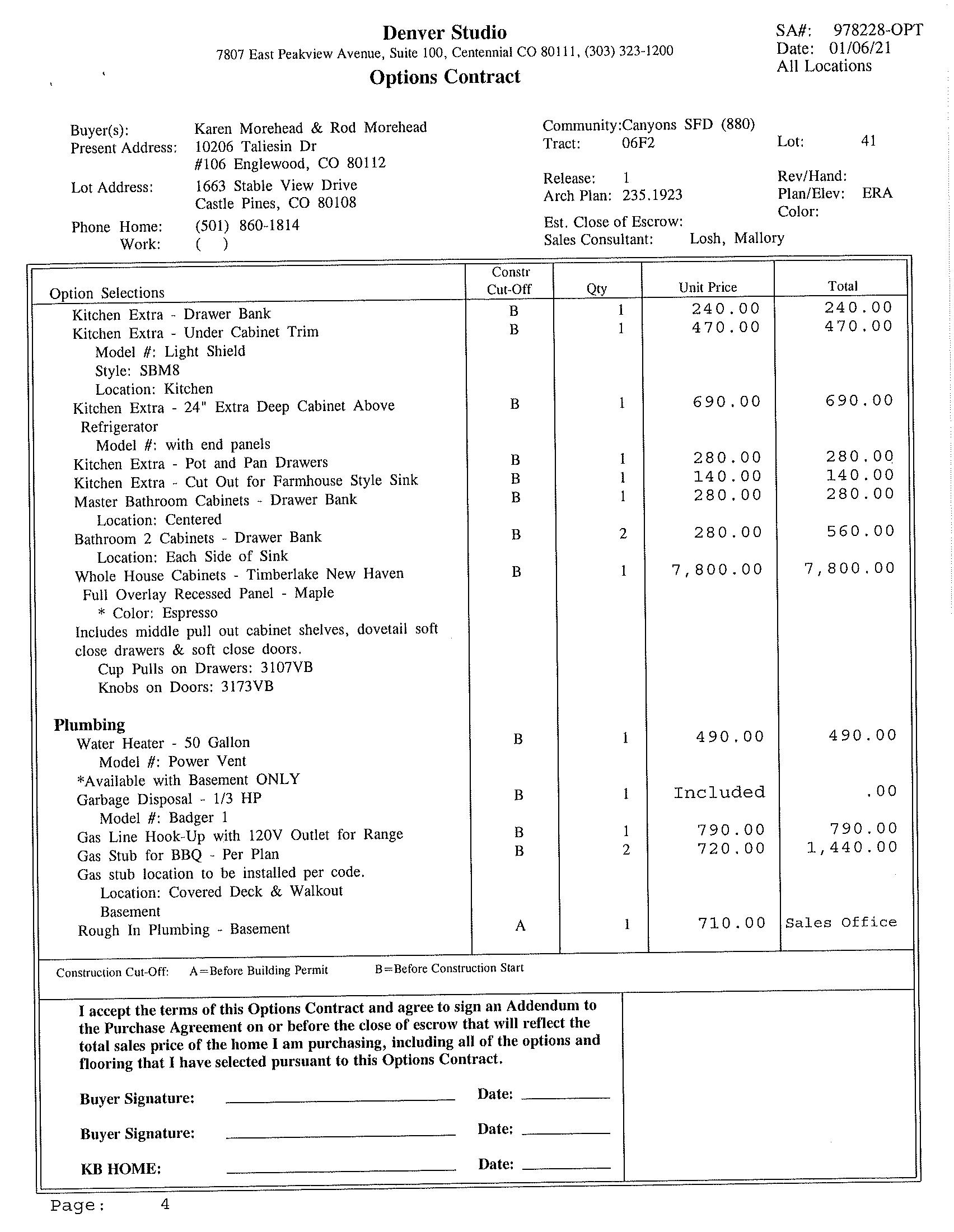

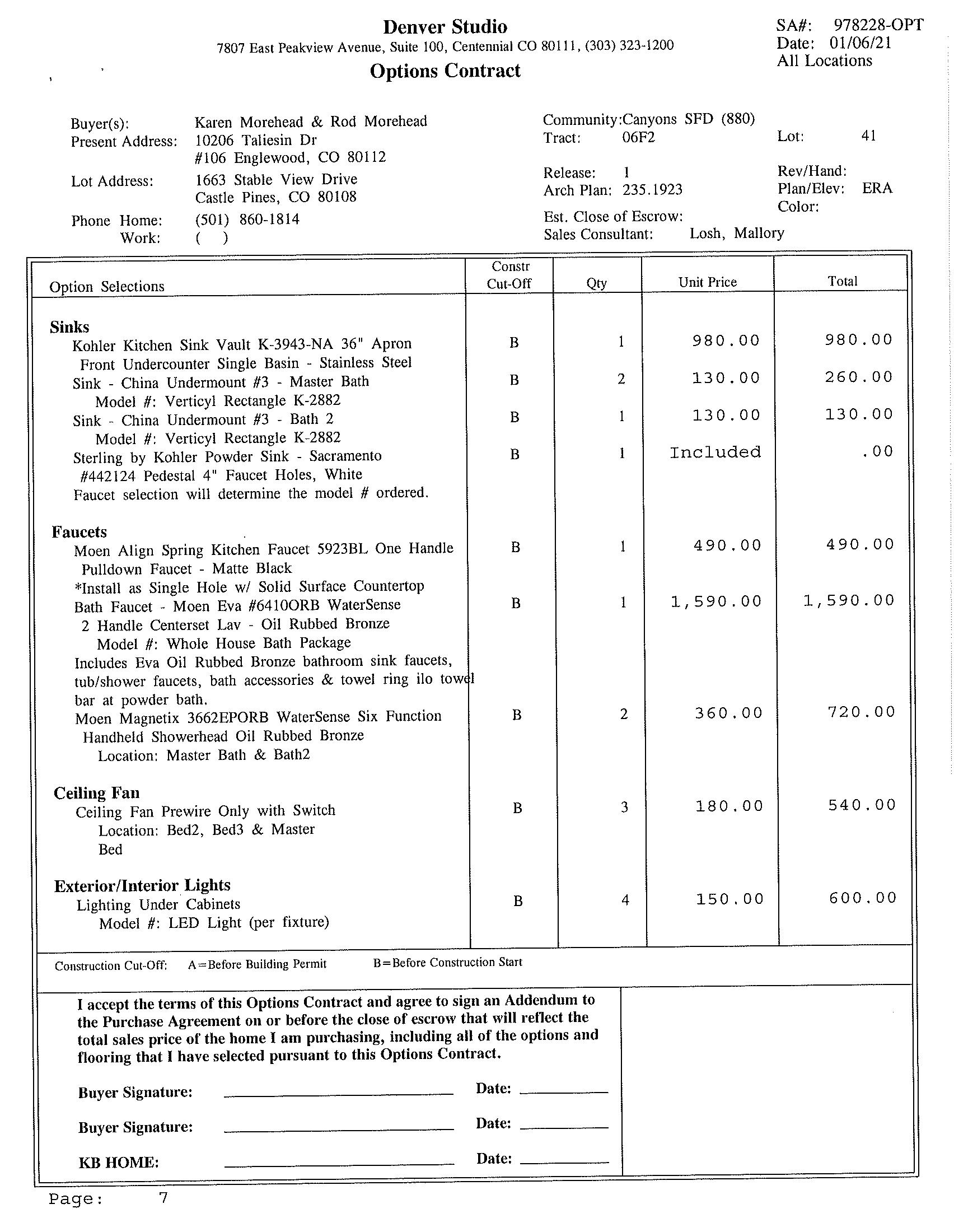
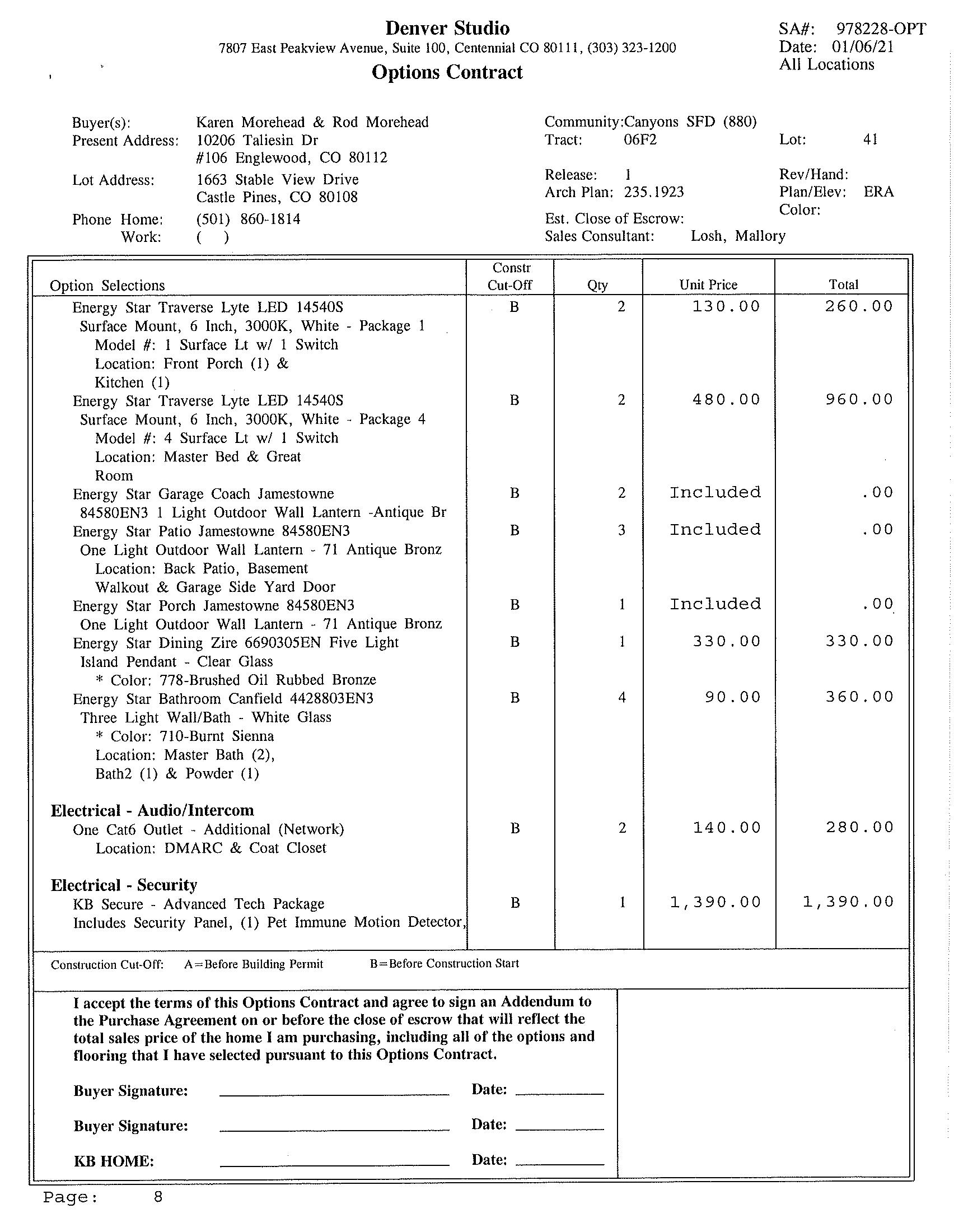

Canyons Filing No. 2 Castle Pines, Colorado
Scope of Investigation
RMG - Rocky Mountain Group drilled a test boring at the above-referenced address as part of a total of 86 borings performed for the design and construction of residential single family structures at the Canyons Filing No. 2 Area A development. Based on information provided, the test boring was drilled near the approximate center of the lot, as surveyed and marked by others. Our findings, conclusions and recommendations are provided in this report.
This report presents geotechnical engineering recommendations for design and construction of residential foundations. The following is excluded from the scope of this report including but not limited to geologic, natural and environmental hazards such as landslides, unstable slopes, seismicity, snow avalanches, water flooding, corrosive soils, erosion, radon, wild fire protection, hazardous waste and natural resources.
Previous Investigations
Reports of previous geotechnical engineering/geologic investigations for this site were available for our review and are listed below:
1. Preliminary Subsurface Soil Investigation, KB The Canyons, Area A, Castle Pines, Colorado, Rocky Mountain Group – RMG, Job No. 158823, July 31, 2017.
Site Description and Proposed Construction
The site of the development was vacant at the time of our subsurface exploration. The existing vegetation consists of native grasses and weeds and scrub oak. It is our understanding that a single family residential structure with an attached garage is planned at this lot for the proposed construction. It has been assumed that the residential structure will be one to two stories in height with basement and is to consist of light, wood framed construction. The site currently is undeveloped and has not had overlot grading to bring the final design grades. It has been assumed that excavation for the basement will not exceed 8.5 feet below proposed final grades. If the proposed construction differs from the information provided or the assumptions made, RMG should be contacted immediately to review the differences and how they may impact construction and design of the proposed construction.
Subsurface Materials
The subsurface materials encountered during the explorations were generally classified using the Unified Soils Classification System (USCS) and are exhibited on the Test Boring Log. The classifications shown on the log are based upon the engineer's classification of samples. Lines shown on the log represent the approximate boundary between subsurface materials, and the actual transition may be gradual and vary across the site. An Explanation of the Test Boring Log, the Test Boring Log, Summary of Laboratory Test Results, Soil Classification Data, and Swell/Consolidation Test Results are presented in the attached figures.
Canyons Filing No. 2 Castle Pines, Colorado
Groundwater Considerations
Groundwater levels were checked at time of drilling of the test boring and (if necessary) at a date subsequent. Groundwater depths based on existing grades at the time the RMG test boring was performed are presented in Table 1 below:
Fluctuations in groundwater and subsurface moisture conditions may occur due to variations in rainfall and other factors not readily apparent at this time. Development of the property and adjacent properties may also affect groundwater levels. Groundwater may be encountered on lots, even when not encountered in the subsurface exploration. It is the responsibility of the contractor to develop a groundwater mitigation plan in the event groundwater is encountered during construction.
Summary of Findings
The results of this investigation indicate that the site is suitable for the proposed construction, provided the recommendations presented herein are implemented and appropriate construction practices are followed. Significant site grading is anticipated at this site, prior to construction of the proposed duplex. The cut or fill depths estimated by RMG based on the cut/fill map provided by KB for the proposed area, are presented in Table 2 below:
It is assumed the basement foundations will bear approximately 8.5 feet below final grade. The proposed basement elevations, relative to existing grade, are presented in Table 3 below:
Based on the boring information and laboratory testing within the building footprint and surrounding lots, we recommend the overexcavation depth presented in Table 4 below:
Overexcavation may be terminated where sandstone bedrock is encountered, provided RMG is on-site to verify a minimum of 5 feet of separation from expansive materials. The minimum separation can be verified using test pitting in the field.
Overexcavation will require removal of the existing expansive materials and replacement with MoistureConditioned Structural Fill. The zone of overexcavation and replacement should extend that same distance beyond the building perimeter, including beyond the perimeter of counterforts and "T" wall footings. The structural fill should be observed and tested during placement as indicated under the Moisture-Conditioned Structural Fill section of this report, to ensure proper compaction. Lots that require the use of overexcavation may require addition testing after fill is placed to ensure reduction in expansive potential.
If overexcavation is not required then the bearing surface should be evaluated at the time of excavation by RMG to ensure that expansive material has been removed within the building footprint. Native soils and bedrock should be scarified, moisture conditioned, and recompacted to a depth of at least 12 inches to provide a uniform bearing material.
Foundation Recommendations
A spread footing foundation supported on moisture-conditioned compacted structural fill is suitable for the proposed residential structure. A maximum allowable bearing pressure of 2,500 psf with a minimum dead load requirement of 800 psf may be used for design. A 4-inch void material should be installed in areas where the minimum dead load cannot be attained. The foundation design should be prepared by a qualified Colorado Registered Professional Engineer using the recommendations presented in this report. This foundation system should be designed to span a minimum of 10 feet under the design loads. The bottoms of exterior foundations should be at least 36 inches below finished grade for frost protection.
Open Excavation Observation
During construction, foundation excavations should be observed by RMG prior to placing structural fill, forms, or concrete to verify the foundation bearing conditions for each structure. Based on the conditions observed in the foundation excavation, the recommendations made at the time of construction may vary from those contained herein. In the case of differences, the Open Excavation Observation report shall be considered to be the governing document. The recommendations presented herein are intended only as preliminary guidelines to be used for interpreting the subsurface soil conditions exposed in the excavation and determining the final recommendations for foundation construction.
It is recommended that excavation equipment remain on-site until the open excavation observation has been completed. If unsuitable conditions are identified during the open excavation observation, i.e. pockets of loose/soft soils, high groundwater, potentially expansive or collapsible soils, etc., additional earthwork recommendations and/or testing and potentially alternative foundation recommendations may be required at an additional cost.
Interior Floor Slabs
Slab performance risk evaluation is an engineering judgement which is used as a predictor of the general magnitude of potential slab heave, and the risk of poor slab performance. The Colorado Association of Geotechnical Engineers (CAGE) recommends structural floors where the slab performance risk is judged to be high or very high. The Slab Performance Risk for slabs bearing atop undisturbed on-site soils and bedrock is based on the criteria in the following table.
Note: Based on Colorado Association of Geotechnical Engineers, Guidelines for Slab Performance Risk Evaluation and Residential Basement Floor System Recommendations (Denver Metropolitan Area, 1996).
This risk is anticipated to be reduced by the recommended overexcavation and replacement measures specified herein. However, the owner must understand that the Slab Performance Risk for slabs bearing atop structural fill after the recommended overexcavation and replacement is still anticipated to be Low to Moderate. Vertical slab movement on the order of three inches is considered possible for floor slabs established on bedrock and granular, non-expansive structural fill and vertical slab movement on the order of four inches is considered possible for slabs established on moisture-conditioned structural fill. In some cases, vertical movement may exceed these ranges. If movement and associated damage to floors and finishes cannot be tolerated, a structural floor system should be used.
Floor slabs should be supported by the same material as the foundation bearing components. Fill materials placed below floor slabs should be consistent, type and compaction, as material below foundation components (or alternate approved by RMG). Floor slabs should be separated from structural components to allow for vertical movement. Control and construction joints should be placed in accordance with the latest guidelines and standards published by the American Concrete Institute (ACI) and applicable local Building Code requirements. Slabs should also be separated from any utility components by isolation joints. Mechanical equipment supported on slabs should be provided with expandable/collapsible sections in order to allow movement of the slab without damage to the equipment or structure.
Recommendations for exterior concrete slabs, such as patios, driveways, and sidewalks, are not included in this report.
Interior Partitions
Interior non-bearing partitions and attached furnishings (e.g., cabinets, shower stalls, etc.) on concrete slabs should be constructed with a void so that they do not transmit floor slab movement to the roof or overlying floor. A void of at least 1-1/2 inches is recommended beneath non-bearing partitions. Doors should be provided with at least a 1 inch gap at floor level. Voids and gaps may require reconstruction over the life of the structure to re-establish the void due to vertical slab movement.
Canyons Filing No. 2
Castle Pines, Colorado
Interior non-bearing partitions walls and other attached finishes do not require isolation from the structural floor system.
Lateral Earth Pressures
Foundation walls should be designed to resist lateral earth pressures. For moisture-conditioned, lowexpansive, on-site backfill materials, we recommend an equivalent fluid pressure of 60 pcf for “Active” conditions and 80 pcf for “At-Rest” conditions be used for design. Claystone bedrock is not suitable for use as backfill material at this site.
The above lateral earth pressure applies to level, drained backfill conditions. Equivalent Fluid Pressures for sloping/undrained conditions should be determined on an individual basis.
Excavations
Excavations for the project are expected to encounter primarily native soils and bedrock. The native soils will generally be excavatable with heavy-duty earth moving equipment. The excavated on-site soils may be reused as structural fill, provided the recommendations set forth herein are implemented. The excavation rate will be very slow within the bedrock and the use of more aggressive excavation techniques, such as single-shank rippers, hoe-rams, rock breaking equipment, and potentially blasting, may be needed to achieve proposed grades. The contractor for this project should anticipate increase wear and tear on equipment when excavated bedrock. The excavation activities may generate oversize material (particles larger than 4 inches) that will not be suitable for use as backfill.
The contractor should provide safely sloped excavations or an appropriately designed and constructed braced-shoring system, in compliance with Occupational Safety and Health Administration (OSHA, 2005) guidelines, for employees working in an excavation that may expose employees to the danger of moving ground. Appropriate slope inclinations should be evaluated in the field by an OSHA-qualified “Competent Person” based on the conditions encountered.
Site Grading
The following sections present recommendations for earthwork during construction including site preparation, structural fill, and exterior backfill.
Site Preparation
Prior to site grading and construction, the ground surface in proposed structure and improvement areas should be stripped of existing vegetation, debris, topsoil, undocumented fill, soft, loose, or disturbed native soils and other deleterious material. This includes areas below foundation and floor slabs. The existing soil stockpile is considered unsuitable material and will require removal within construction area. Care should be taken to reduce drying of the subgrade soil below the foundation during construction. Site preparation procedures should be performed such that the potential for standing and ponding of water around the site is reduced. During wet weather earthen berms, swales, or other means should be used to direct water away from excavations. Water that accumulates in excavations should be pumped out or otherwise removed and these areas should be allowed to return to their “natural” moisture condition before resuming construction.
Moisture-Conditioned Structural Fill
Areas to receive moisture-conditioned structural fill should have topsoil removed and the upper 6 inches of the exposed surface soils scarified and moisture conditioned to facilitate compaction (usually within 2 percent of the optimum moisture content) and compacted to a minimum of 95 percent of the maximum dry density as determined by the Standard Proctor test (ASTM D-698) prior to placing structural fill.
Moisture-conditioned structural fill placed on slopes should be benched into the slope. Maximum bench heights should not exceed 4 feet, and bench widths should be wide enough to accommodate compaction equipment.
Moisture-conditioned structural fill shall consist of moisture-conditioned, on-site native clayey soils and should generally be free of topsoil, organics, debris, particles greater than 4 inches in diameter, and other deleterious materials. Claystone bedrock is not suitable for use at this site without further processing and approval by RMG.
Moisture-conditioned structural fill materials shall be moisture-conditioned to a minimum of 1 percent to 4 percent above optimum moisture content (as determined by the Standard Proctor test, ASTM D-698).
The moisture-conditioned materials should be placed in maximum 8" compacted lifts. These materials should be compacted to a minimum of 95 percent of the maximum dry density as determined by the Standard Proctor test (ASTM D-698). Material not meeting the above requirements shall be reprocessed.
Materials used for moisture-conditioned structural fill should be approved by RMG prior to use. Moisture-conditioned structural fill should not be placed on frozen subgrade or allowed to freeze during moisture conditioning and placement.
Earthwork operations should be observed and compaction of structural fill materials should be tested by the project’s geotechnical consultant. It is the responsibility of the builder or contractor to schedule with this office to conduct compaction tests, retrieve or accept delivery of a fill sample, or certify the fill material. Early testing is recommended to demonstrate that placement and compaction methods are achieving the required compaction for the entire depth of fill. Without a strict quality assurance program, the fill may not be of sufficient quality to achieved required performance.
Exterior Backfill
Backfill should generally be free of topsoil, organics, particles greater than 4 inches in diameter, debris, or other deleterious material. Backfill should be placed in loose lifts not exceeding 8 to 12 inches, moisture conditioned to facilitate compaction (usually within 2 percent of the optimum moisture content) and compacted to 90 percent of the maximum dry density as determined by the Standard Proctor test, ASTM D-698 on exterior sides of walls in landscaped areas. In areas where backfill supports pavement and concrete flatwork, the materials should be compacted to 95 percent of the maximum dry density as determined by the Standard Proctor test, ASTM D-698.
Canyons Filing No. 2
Castle Pines, Colorado
Fill placed on slopes should be benched into the slope. Maximum bench heights should not exceed 4 feet, and bench widths should be wide enough to accommodate compaction equipment.
The appropriate government/utility specifications should be used for fill placed in utility trenches. If material is imported for backfill, the material should be approved by the Geotechnical Engineer prior to hauling it to the site.
The backfill should not be placed on frozen subgrade or allowed to freeze during moisture conditioning and placement. Backfill should be compacted by mechanical means, and foundation walls should be braced during backfilling and compaction.
Surface Grading and Drainage
Drainage is an important key to the successful performance of shallow foundations. The ground surface should be sloped away from structures with a minimum gradient of 10 percent for the first 10 feet. This is equivalent to 12 inches of fall across this 10-foot zone. If a 10-foot zone is not possible on the upslope side of the structure, then a well-defined swale should be created a minimum 5 feet from the foundation and sloped parallel with the wall with a minimum slope of 2 percent to intercept the surface water and transport it around and away from the structure. Roof drains should extend across backfill zones and landscaped areas to a region that is graded to direct flow away from the structure. It is imperative that homeowners maintain the surface grading and drainage recommended in this report to help prevent water from being directed toward and/or ponding near the foundations. Failure to maintain positive surface drainage away from the structure may result in localized differential vertical movement of foundations and slabs.
Landscaping should be selected to reduce irrigation requirements. Plants used close to foundation walls should be limited to those with low moisture requirements; and irrigated grass should not be located within 5 feet of the foundation. To help control weed growth, geotextiles should be used below landscaped areas adjacent to foundations. Impervious plastic membranes are not recommended.
Irrigation devices should not be placed within 5 feet of the foundation. Irrigation should be limited to the amount sufficient to maintain vegetation. Application of more water will increase the likelihood of slab and foundation movements.
The recommendations listed in this report are intended to address normal surface drainage conditions, assuming the presence of groundcover (established vegetation, paved surfaces, and/or structures) throughout the regions upslope from this structure. However, groundcover may not be present due to a variety of factors (ongoing construction/development, wildfires, etc.). During periods when groundcover is not present in the "upslope" regions, higher than normal surface drainage conditions may occur, resulting in perched water tables, excess runoff, flash floods, etc. In these cases, the surface drainage recommendations presented herein (even if properly maintained) may not mitigate all groundwater problems or moisture intrusion into the structure. We recommend that the site plan be prepared with consideration of increased runoff during periods when groundcover is not present on the upslope areas.
Perimeter Drain
A subsurface perimeter drain is recommended around portions of the structure which will have habitable or storage space located below the finished ground surface. This includes crawlspace areas but not the walkout trench, if applicable. A typical drain detail attached with this report.
A subsurface perimeter drain is designed to intercept some types of subsurface moisture and not others Therefore, the drain could operate properly and not mitigate all moisture problems relating to foundation performance or moisture intrusion into the basement area.
Concrete
Based on sulfate testing within the area, Type I/II cement is recommended for concrete in contact with the subsurface materials. Calcium chloride should be used with caution for soils with high sulfate contents. The concrete should not be placed on frozen ground. If placed during periods of cold temperatures, the concrete should be kept from freezing. This may require covering the concrete with insulated blankets and heating. Concrete work should be completed in accordance with the latest applicable guidelines and standards published by ACI.
Foundation Configuration Remarks
The configuration of the foundation system is critical to its performance. The position of foundation windows, jogs, steps and the relative elevation of adjacent and opposite walls can affect foundation performance. The nature of residential foundation construction does not allow for control of these conditions by the Foundation Design Engineer. Improper placement of the above can result in differential and lateral foundation movement not anticipated by the Geotechnical Engineer. The Foundation Design Engineer should be contacted regarding the foundation configuration.
General Remarks
The recommendations provided in this report are based upon the subsurface conditions encountered in the test borings, anticipated foundation loads, and accepted engineering practices and principles in the area at the time of report preparation. No warranty is made or implied in this report that this firm has an all inclusive knowledge of every portion of the subsurface materials on or under the site. There is no evaluation detailed enough to reveal every subsurface condition. The nature and extent of variations across the site may not become evident until construction commences or thereafter. The construction process itself may also alter subsurface conditions. If variations appear evident at the time of construction, our office should be notified. If additional mass site grading is performed at the site which results in elevations that vary significantly from existing grades (more than plus or minus 2 ft), our office should be informed about these changes. If needed and/or if desired, we will reexamine our analyses and make supplemental recommendations.
The recommendations are intended to reduce differential movement. However, it should be noted that geotechnical engineering recommendations are not an exact science. The recommendations presented in a geotechnical engineering report are not based only on the analytical and empirical tools but rely on engineering judgement as well. The fact that professional judgements must be used in making recommendations means that the conclusions and recommendations presented in a geotechnical
Canyons Filing No. 2
Castle Pines, Colorado engineering report should not be considered risk-free and, more importantly, are not a guarantee that the interaction between the soils and the proposed structure will perform as planned. Furthermore, it must be recognized that the foundation will undergo some movement on all soil types. Concrete floor slabs will likely move vertically. The recommendations for isolating floor slabs from columns, walls, partitions or other structural components should be implemented to mitigate potential damage to the structure.
Subsequent owners should be provided a copy of this report. The recommendations are based on accepted local engineering practice and are intended for individuals familiar with local construction practices and standards. The owner is also encouraged to read A Guide to Swelling Soils for Colorado Homebuyers and Homeowners, Special Publication No. 43, available from the Colorado Geological Survey. Recommendations contained in the report are also applicable for prevention of settlement due to wetting of support soils.
RMG does not assure the existence of and/or the compliance with the above recommendations. This is the responsibility of the client referenced on the first page. RMG provided recommendations only and does not supervise, direct or control the implementation of the recommendations.
Senate Bill 13
This report may be partial fulfillment of Colorado Senate Bill 13 (1984), C.R.S. 6-6.5-101, The Soil and Hazard Analysis of Residential Construction, if the purchaser receives this report at least fourteen days prior to closing.
The purpose of Senate Bill 13 is to inform the purchaser of the presence of expansive soil or hazards on the site. Geologic and environmental hazards are outside the scope of services of this report. Expansive soil and bedrock may result in movement of foundation components and floor slabs. The recommendations presented in this report are intended to reduce, not eliminate, these movements.
The homeowner and builder should review and become familiar with Special Publications 43 issued by the Colorado Geologic Survey.
This report and the recommendations contained therein are only valid if all parts of Senate Bill 13 are satisfied.
If we can be of further assistance in discussing the contents of this report or analysis of the proposed project, from a geotechnical engineering point-of-view, please feel free to contact us.
INTERBEDDEDSANDSTONEANDSHALE/CLAYSTONE
UNLESSNOTEDOTHERWISE,ALLLABORATORY TESTSPRESENTEDHEREINWEREPERFORMEDBY: RMG-ROCKYMOUNTAINGROUP 2910AUSTINBLUFFSPARKWAY COLORADOSPRINGS,COLORADO
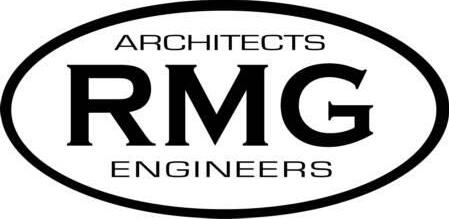
Symbolsandnotes
STANDARDPENETRATIONTEST-MADEBYDRIVINGASPLIT-BARRELSAMPLERINTO THESOILBYDROPPINGA140LB.HAMMER30",INGENERALACCORDANCEWITHASTM D-1586.NUMBERINDICATESNUMBEROFHAMMERBLOWSPERFOOT(UNLESS OTHERWISEINDICATED).
UNDISTURBEDCALIFORNIASAMPLE-MADEBYDRIVINGARING-LINEDSAMPLERINTO THESOILBYDROPPINGA140LB.HAMMER30",INGENERALACCORDANCEWITHASTM D-3550.NUMBERINDICATESNUMBEROFHAMMERBLOWSPERFOOT(UNLESS OTHERWISEINDICATED).
FIGURENo.1
DATE6/6/18
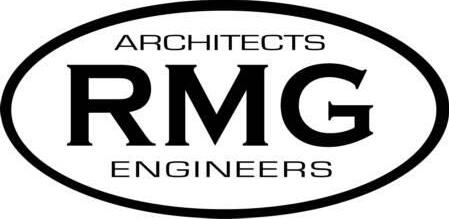
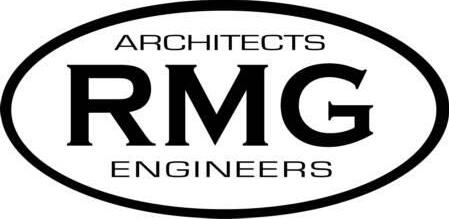
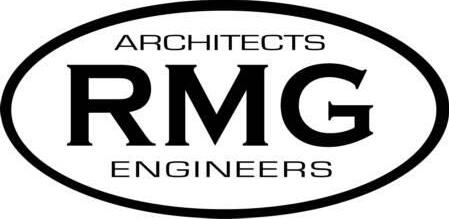
