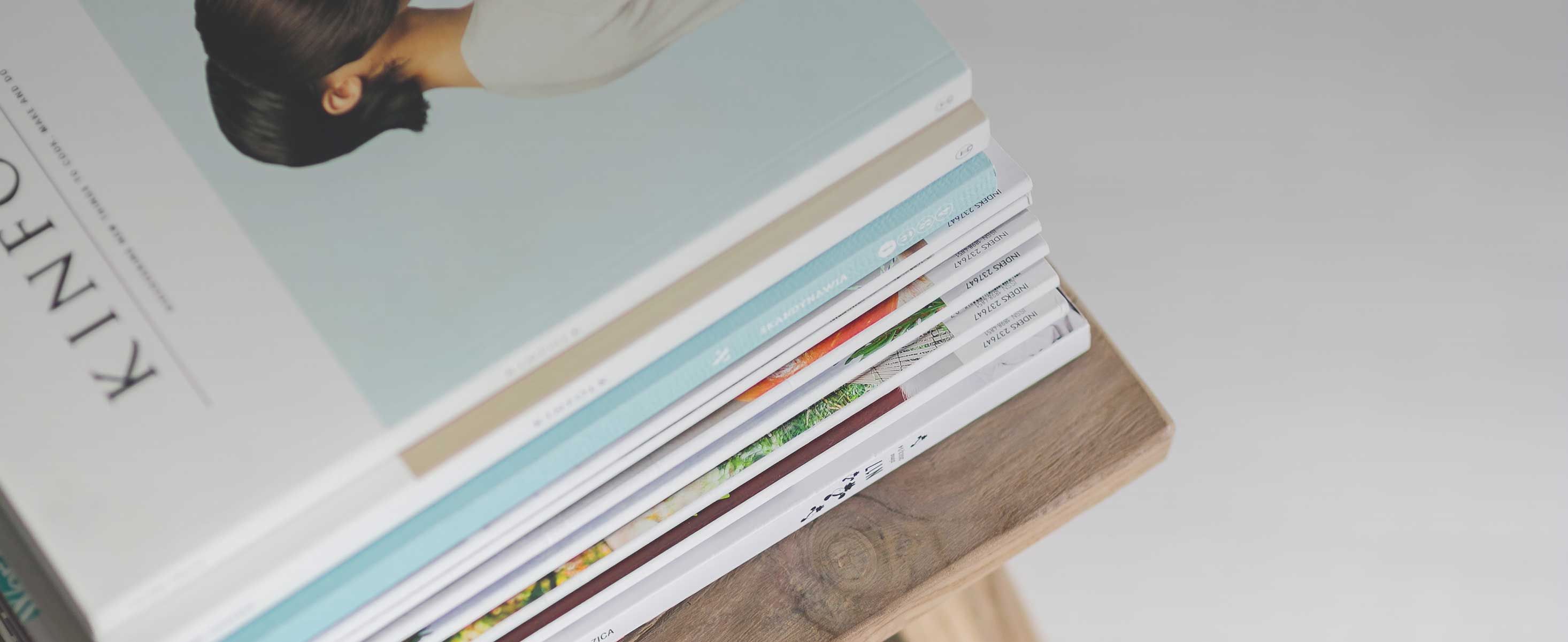
3 minute read
GR PRO SECATEURS
Jake Hobson, co-founder of Niwaki, on the work that went into creating the brand’s signature secateurs
Interview: Viel Richardson
Requirement
For most gardeners, their secateurs are likely to be the single most important tool they have in their toolbox. This is because they’re such a useful all-round pruner. You can use them for cutting anything from slender flower stalks, right up to finger-thick stems or wooden branches. You would use them for pruning your roses or for cutting back bushes such as lavender. You would also use them for harvesting fruit and vegetables. They’re a hugely versatile tool. The key thing is that they have to cut cleanly and consistently, and this is not just a matter of them being sharp – the design has to be good as well.
Inspiration
I initially got deeply into pruning while spending time in Japan, where I became a professional pruner, specifically a topiary specialist. In Japan, most gardening tools are used by landscape professionals, because Japanese gardening tends to be a very professional business. Recreational domestic gardening, which is such a popular activity in the UK, does exist in Japan but on a much smaller scale. So Japanese secateurs are made for professionals, which is why they’re so good. The problem when we started selling them was that their strong spring and heavy-duty construction could make them quite hard to use for long periods by a home gardener. Our idea was to create a set of secateurs that maintained the high quality of the professional tools but were more suited to a domestic setting.
Process
We work closely with a blacksmith in Yamagata in the north of Japan. The area specialises in secateurs, which are traditionally made for the orchard industry. The family we work with has been doing this for generations, so before asking them to change any element of their design you’ve got to show a real understanding of the tool and earn their respect. The key change we asked for was a lighter spring with a softer feel that you didn’t need such strong hands to use. Secateurs have a sharp blade on the top and a thick blade called the bypass on the bottom. The sharp blade cuts into the twig and effectively pushes it over the bypass to complete the cut. The intersection at that point is key. If it’s done well, it’s effortless; if it’s set badly, it will catch or be too tight, and it won’t cut properly. Getting this right involves the interplay of the nut and bolts and the tension of the spring. Making any changes without degrading the performance takes a great deal of knowledge and skill on the blacksmith’s part.
Materials
These secateurs are made from a type of carbon steel called KA70. Different steels have different properties which can affect things like edge retention, toughness and rust resistance. Our blacksmiths believe that KA70 hits the sweet spot. The tool is made using a process called drop forging, where a single bar of steel is cut in half, heated up and forced into a mould, which gives you the basic shape. This is then refined by hand. The finished tool is very strong, as each blade and handle is a single piece of steel, rather than being an assembly of parts. After that, each half is heated to a precise temperature and then cooled rapidly in oil, which sets the hardness of the steel. This whole process means they’re stronger than non-forged secateurs and keep an excellent edge. The handles are covered in bright yellow vinyl. Lot of makers leave the black steel handles bare, which looks lovely but is slightly impractical, because if you put them down in the garden you lose them instantly. Ours are easy to spot. The final piece is the bolt that holds the two halves together, which is made from brass.
Philosophy
For me, the fundamental point of any tool is that it works. That it does the job it is meant to and does it well. That it helps bring a deeper enjoyment to any task. You can ignore what it looks like, how expensive it was, who made it – if it works, it’s a good tool; if it doesn’t, it isn’t. A lot of people, myself included, also enjoy knowing the history behind a tool, its story, who made it, where it was made, who the blacksmith trained under. In Japan, the heritage of a blacksmith is very important. Understanding and appreciating the generations of knowledge that have gone into crafting the tool in your hand is part of the joy of using it. But that feeling of appreciation won’t last for very long if the tool doesn’t actually work!
NIWAKI 38 Chiltern Street, W1U 7QL niwaki.com
RUGS & THROWS
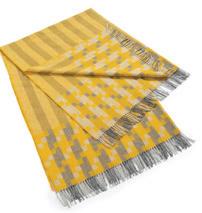