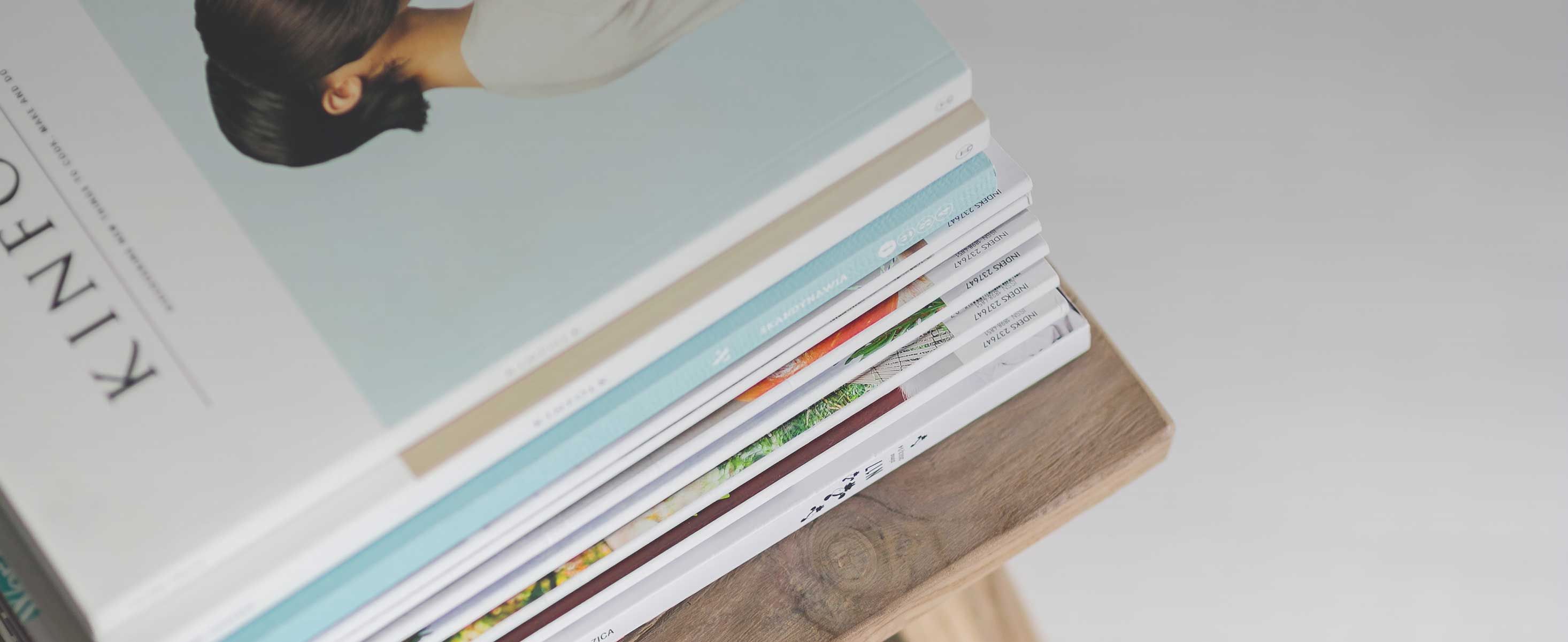
3 minute read
Decisions Underfoot
Carpeting for Common Areas of Condos
For those of you who have ever been a part of a condominium refurbishment project in your common areas, you know that the carpeting is a large part of the overall design, functionality, and cost of the project.
Advertisement
For the most part, the quality of any materials that condo designers specify for a condominium refurbishment are referred to as mid-grade commercial products. Which, for condos, generally means that they are durable enough to withstand multi-residential traffic without having to be replaced for about 12-15 years provided they are properly maintained. Within the spectrum of mid-grade commercial quality products, it is important to note there is a range of costing. Each product has factors that impact the cost.
Although this is more information than you need or will likely be given by a condo designer, some knowledge may go a long way in understanding why certain carpets are specified and what attributes will affect the cost, quality, and durability of a carpet.
Carpet Face Weight refers to how much a carpet’s fiber weighs per square yard; it is a measurement made in ounces. (Note - it is not necessarily true that the heavier the carpet the more durable it is). Condos can see designers specifying carpet with ounces typically ranging from 28 oz to 42 oz (under pad can be used with some lower weights of carpet to add cushion but reduce cost compared to a higher oz carpet). There are also some high-performance carpet products with face weights as low as 14 oz/sy that could be specified.
Carpet Density refers to how close together the fibers are stitched (or tufted) into the carpet backing. Generally, the closer the fibers the more durable and possibly more expensive it will be. A density of 5,000 per cubic yard or higher for extra heavy traffic conditions is usually recommended.
Fibre Twist is how many times a 1-inch length of fibre has been twisted. This is not usually talked about by the carpet manufacturers – perhaps because it is too much information, but it is a factor in the durability of a carpet. The more twisted, the more durable and more costly it is. Anything above 6 should be acceptable for commercial use.
Solution Dyed or Printed are two methods by which a carpet gets its patterns and colours:
• Solution dying is the process of adding colour to the entire carpet fibre before the carpet is manufactured. The process creates the most colour fast yarn. The colour is locked in and goes all the way through the fibre. This method is more environmentally friendly than printing carpets. Although solution dyed carpets may take a little longer to produce, they are generally less expensive than printed carpets.
• Printed carpets get their colour after the carpet is made. This method can provide brighter tones and a wider variety of colours. The dye only penetrates the outer surface of the fibers. For that reason, the rest of the flooring material does not absorb the color. This method of colouring is not as eco-friendly as solution dying. Stains are also more likely to settle into printed carpets and it is generally more expensive.
Condo designers tend to specify solution dyed carpet as it is more stain resistant and less vulnerable to colour change and fading.
Design, patterns and colours for carpets are worth discussing for several reasons. Condos with a large pet community may want to choose patterns and colours that camouflage stains. More intricate patterns and number of colour palms may increase carpet costing as will print repeats as they relate to carpet widths. How carpet is laid in your condo (especially with irregularly shaped corridors and suite door drops) can also contribute to cost as well as additional boarders.
Fibre type used in carpets are synthetic fibers and natural fibres, and the various types contribute to quality and determine best use. Most commercial carpets used in condominium corridors are made of nylon, olefin or polypropylene. Though all three can be solution dyed, nylon is the most durable of the three, and though it may be a little more expensive, it is most often specified for condominiums for this reason.
Manufacturers’ warranty – typically a commercial quality carpet will have a basic warranty of 15 years provided that the maintenance manual recommendations have been adhered to.
Manufacturing methods of commercial carpets have changed since the 1950s moving from woven to tufted. Tufting essentially involves stitching close rows of carpet fiber loops through a backing material. The visible material tufts in the carpet are known as its pile.
Most carpets today use this method as it produces a durable and sturdy carpet at a fraction of the cost of weaving. Tufted carpets can be looped, cut or both.
Types of carpet include cut pile, loop pile or a combination of each. Both are used most often in condominiums residential corridors as they provide durability. Qualities of each are as follows:
Loop Pile
• fibers that are woven to loops that are attached to the back of the carpet
• excellent durability and unmatched resistance to stain, loop pile carpets are perfect for areas with high traffic
• smoother flatter texture to cut pile which makes them less resistant to signs of tracking or matting
• strands may run if pulled