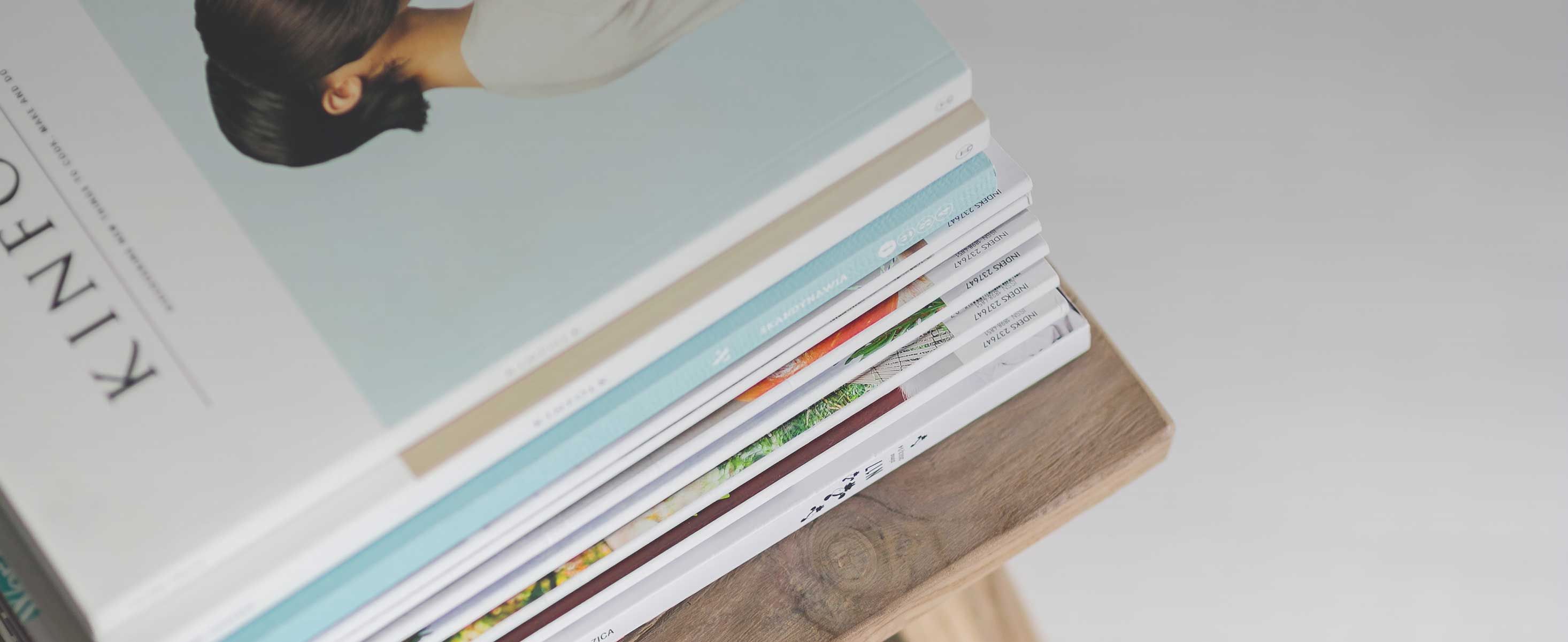
1 minute read
PLM-enabled Digital Transformation Benefits
from Economizing Oil & Gas Capital Projects with PLM-Based Digital Transformation – The LTTS Approach
by LTTS
In PLM-based data aggregator solution, every physical component, such as a shaft or a bearing, is assigned a tag, which essentially contains a 3D model of the component along with all its associated information. Considering that a typical offshore facility has over 150,000 tags, the benefits of using PLM-based solution are enormous.
Digital twin can be created in the most real sense, with dynamic updates happening parallelly in tags. 3D visualization of components enables better understanding of the associated data. Robust part management and management of change (MOC) control surplus and reduce material wastage, which has traditionally been one of the biggest challenges for O&G players. Massive cost savings result out of improved parts management and inventory control. Drastic reduction in operational time is made possible by providing correct information to all the stakeholders in a secured manner with role-based access control.
Transparency is established across the system owing to PLM’s philosophy of ‘Single Version of Truth’. Data that is made available to all the stakeholders, including project managers, engineers, regulatory bodies, and clients’ consultants, is essentially the same. The dashboard visualization may vary but the source of truth remains one. Greater trust ensues among stakeholders due to similar and unbiased data accessibility rights granted to all the parties involved. Speed and clarity of communication increase as the reliance on emails and other traditional mediums goes down. Instead, tag related queries are raised, relayed, addressed, answered, and stored in the PLM system for reference in the future. Seamless collaboration among individuals and globally dispersed teams is enabled due to greater trust and transparency across the system.