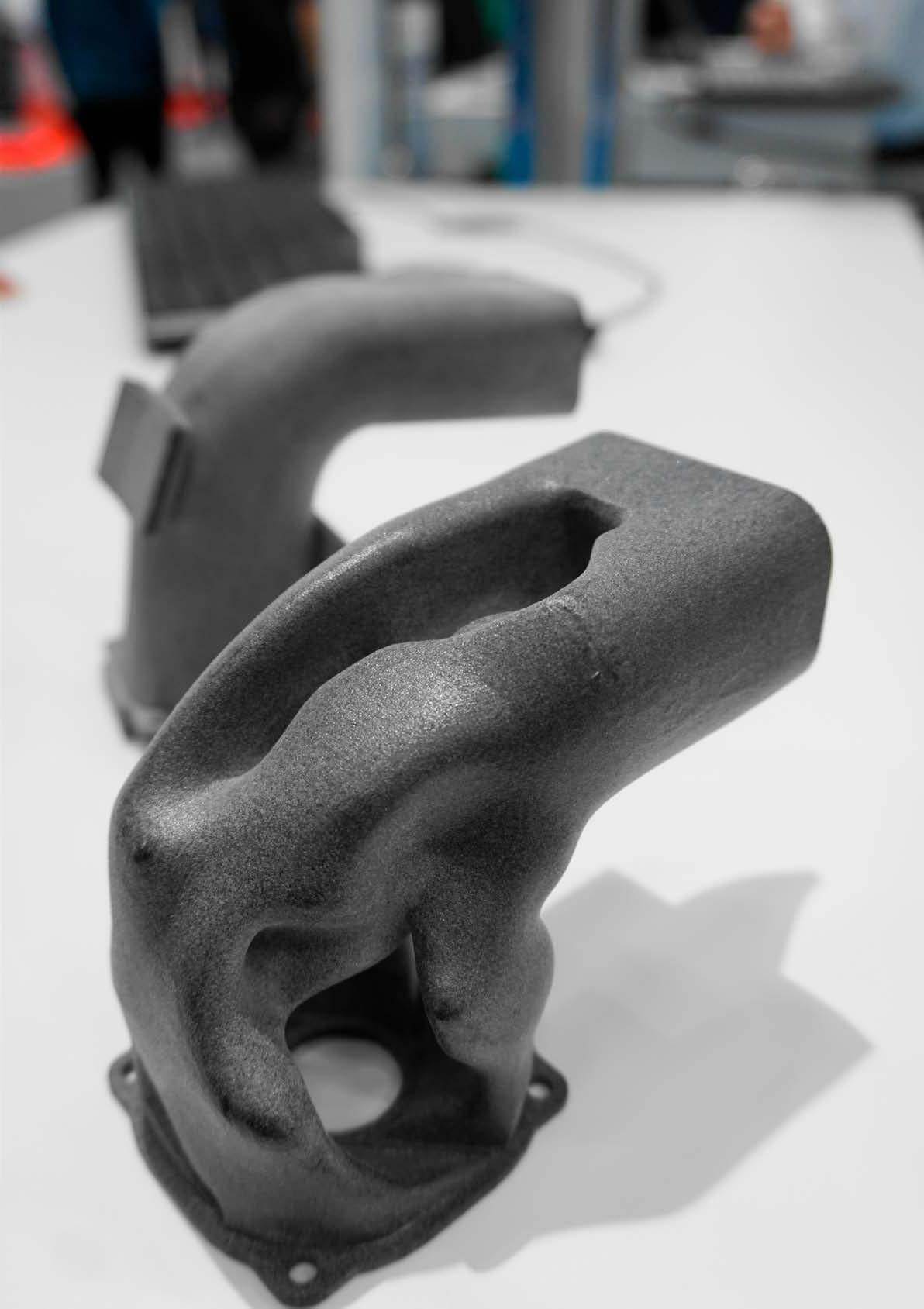
6 minute read
Optimaliseren voor 3D printen én performance
HP en Siemens intensiveren hun samenwerking met als doel digitaal produceren verder te ontwikkelen en breder te laten landen in de maakindustrie. Met de toepassing van digital twins en de geïntegreerde AM workflow in Siemens NX, optimaliseren engineers in dezelfde omgeving niet alleen voor 3D printen maar ook voor betere prestaties van onderdelen. En BMW gebruikt de digital twin en simulatietools van Siemens zelfs voor de optimale inrichting van de AM-fabriek voor serieproductie op de HP printers.
Advertisement
Onderdelenreductie door specifiek voor additive manufacturing te ontwerpen, is eigenlijk niks nieuws. HP heeft dit samen met Siemens in het Additive Manufacturing Center in Erlangen gedaan voor een onderdeel van het koelsysteem van de Multi Jet Fusion 3D printers. De luchtinlaat bestaat niet langer uit zes onderdelen, maar wordt in één geheel op de MJF printer geproduceerd. Kostenreductie: van $30 naar $20. “Daarna hebben we met de engineers van Siemens nog een tweede optimalisatieslag gemaakt, nu gericht op de prestaties van de luchtinlaat”, zegt Philipp Jung, Chief Strategy Officer bij HP. “Hierdoor realiseren we een 20% betere performance.”
Virtueel optimaliseren
Dit HP-product toont de mogelijkheden van een geïntegreerde AMworkflow zoals Siemens NX die biedt. “Je kunt scenario’s doorrekenen zonder dat het productietijd kost”, zegt Thomas Duerr, Business Development AM bij Siemens. Stromingssimulatie bestaat al lang in de industrie. Maar: tot nog toe is dat specialistenwerk met aparte software. Siemens integreert deze in NX en geeft de design engineers de mogelijkheden om zelf te simuleren hoe de lucht door de inlaat stroomt en welk effect dit heeft op de koelcapaciteit. Dus zonder dat er een enkel stuk is geprint en fysiek getest op een machine. Thomas Duerr: “Hiermee kun je in je CAD-omgeving al bepaalde zaken controleren. Daarmee kom je sneller tot nieuwe design ideeën.” Bij de luchtinlaat van de HP 3D printer blaast een ventilator met 20.000 omwentelingen per minuut de lucht in het koelsysteem. In Siemens NX is de maximale bouwruimte voor het onderdeel aangegeven, samen met enkele andere uitgangspunten en daarna zijn de algoritmes het juiste model gaan zoeken om de luchtstroming te optimaliseren. Dat leverde uiteindelijk een nieuw model op dat volgens de simulatie 20 tot 23 procent beter zou presteren. Thomas Duerr: “De hele simulatie heeft 7,5 uur in beslag genomen. Al met al hebben we het ontwikkelproces met 75% kunnen versnellen.” Het belangrijkste winstpunt zit in de betere prestaties. Hierdoor kan HP de printers bij een gelijk energieverbruik 15% sneller laten printen. De echte praktijktest wees overigens uit dat de luchtdoorstroming met 22% verbeterd is, precies dus zoals met de digital twin was voorspeld. Thomas Duerr haalt nog een tweede voorbeeld aan: een onderdeel voor de koeling van de accu’s van een elektrische auto. EDAG, een Duits engineeringbureau voor de automotive industrie, heeft eveneens met Siemens NX de luchtinlaat geoptimaliseerd voor zowel 3D printen als prestaties. Ook hiermee werd de efficiency met 20% verbeterd. “Design engineers gaan nadenken over verbeteringen als ze de mogelijkheden met Siemens NX zien”, zegt Tim Weber, Head of AM bij printerfabrikant HP. “Dit kun je in heel veel industrieën toepassen.” Uiteindelijk voeg je daarmee waarde toe aan de toepassing waarvoor je een onderdeel print, zoals sneller 3D printen bij HP of sneller opladen bij de elektrische auto van EDAG.
Op de stand van Siemens werd de robot 3D printer van CEAD uit Delft gedemonstreerd. (Zie pagina 11)
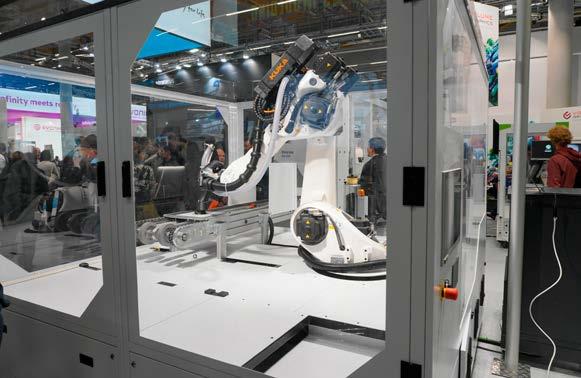
3D geprinte luchtinlaat kost 33% minder en presteert 20% beter
Layout AM-fabriek plannen
De digitale tweeling van een product kun je vervolgens inzetten voor het inrichten en plannen van de fabriek layout, inclusief het berekenen hoeveel machines én medewerkers nodig zijn om een bepaald aantal onderdelen op jaarbasis te 3D printen. Met de Siemens Digital Enterprise Portfolio voor AM liet Siemens op Formnext de bezoekers zelf experimenteren met de layout van een AM-fabriek waarbij effecten op de capaciteit snel zichtbaar worden. Tijdens mtc3, de conferentie van Oerlikon en TUM afgelopen najaar in München, presenteerde BMW hoe men met behulp van de digital twin van de lifter guide voor de cabriokap van de i8 Roadster de optimale AM fabriek heeft gepland. BMW print ongeveer 82.000 van deze onderdelen per jaar met 6 MJF 5200 machines van HP. De autofabrikant heeft met de software meerdere simulaties gedaan, zowel om het verschil qua productiviteit te ontdekken tussen de HP 4200 en HP 5200 machine alsook om de optimale personele bezetting vast te stellen. Dominik Rietzel, Head of AM Non Metals bij BMW: “De digital twin heeft ons geholpen om de kosten te verlagen. In de simulatie zagen we de bezettingsgraad van de machines en wat de medewerkers doen. Dan kun je gaan vergelijken, bijvoorbeeld tussen de 4200 en 5200 machine, het aantal trolleys dat je nodig hebt etcetera.” Te weinig trolleys met daarin het materiaal bleek een bottleneck te zijn in verband met de afkoeltijd van de HP printers. Nadat meerdere screnario’s zijn doorgerekend, blijkt bij BMW een opstelling met 6 HP 5200 printers en 35 trolley’s met een afkoelstation de beste oplossing te zijn. “Het bleek dat we niet meer machines nodig hadden maar meer trolleys en een extra afkoelstation. Dat laatste is een minder dure oplossing dan een extra 3D printer.”
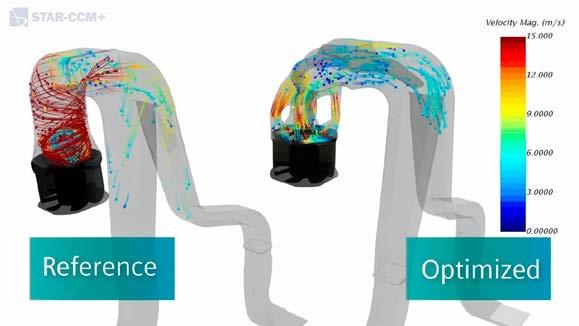
BMW gebruikt digital twin om optimale inrichting van de AM fabriek te bepalen

Printproces monitoren
Hiermee houdt het verhaal voor Siemens niet op. Door de 3D printers te verbinden met Mindsphere, de IoT-cloud van Siemens, wordt het volledige proces bewaakt. In de toekomst wil Siemens hiermee digitaal de kwaliteit van het AM-proces borgen. Daartoe experimenteert men in Erlangen met beeldherkenningssoftware. Van elke laag wordt een opname gemaakt. Algoritmen analyseren deze beelden en herkennen de plekken waar zich eventueel een probleem kan voordoen. Afhankelijk hiervan wordt op een schaal aangegeven hoe groot de foutkans is. Daarna kan de AM operator naar de parametersettings voor die locatie gaan om de oorzaak te vinden. Op langere termijn wil Siemens naar een closed loop systeem gaan, waarbij de software zelflerend is. Daarvoor is het momenteel nog te vroeg. De systemen zijn nog bezig om de bandbreedtes te leren waarbinnen een 3D print goed is. Wat wel kan met de nieuwe versie van Siemens NX, is het printproces voorbereiden waarbij én rekening wordt gehouden met een ideale nesting om de kosten laag te houden én de effecten daarvan op de kwaliteit. De software zoekt de optimale nesting, op basis van een strategie die vervormen doordat te veel warmte wordt ingebracht vermijdt. de praktijk betekent dit dat in het designproces al veel meer gekeken wordt naar de maakbaarheid van de componenten. In de gebruiksfase van een machine of product, wordt de digital twin gebruikt om met behulp van echte data uit de praktijk predictive maintenance toe te passen. Siemens heeft hier in de elektronicafabriek in Amberg al ervaring mee opgedaan. Bij het boren van gaten in de printplaten komt stof vrij dat op termijn funest blijkt te zijn voor de spindels. Vroeger verving Siemens deze preventief na 12 maanden, om ongeplande stilstand van de lijn te vermijden. “Nu analyseren we in Mindsphere de data van de asbewegingen en voorspellen de algoritmes wanneer een spindel stuk gaat. Sinds het systeem op 18 machines draait, is er geen enkele spindel meer onverwacht stuk gegaan. De besparing daarvan is meer dan € 200.000 per jaar”, geeft Daniel een voorbeeld uit de eigen praktijk van Siemens. De algoritmes voorspellen op 3 dagen vooraf wanneer een spindel vervangen moet worden.