
5 minute read
Waarom een spuitgietexpert gaat 3D printen
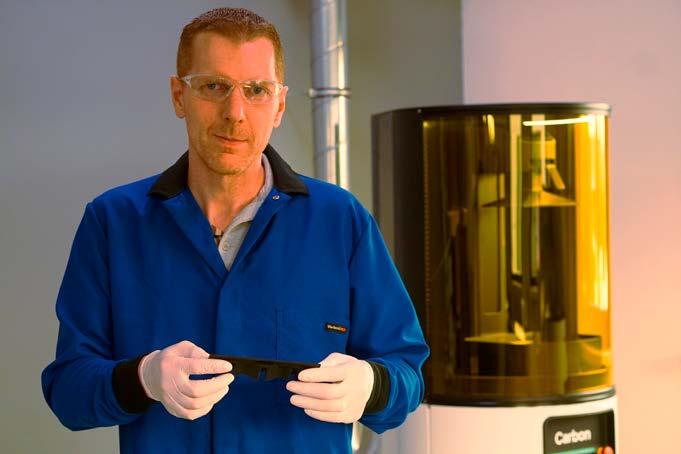
Maick Klaassen bij de Carbon M2, de eerste in de Benelux. De Carbon technologie heeft hem over de streep getrokken om functionele onderdelen te gaan 3D printen.
Maick Klaassen, eigenaar van QDP, volgt de 3D printindustrie al jaren met een kritische blik. Al die tijd hield hij vast aan zijn strategie om voor de in Nederland ontwikkelde producten in de Chinese vestiging matrijzen te vervaardigen en daarna de producten te spuitgieten. Sinds afgelopen voorjaar staat bij QDP in Duiven de eerste Carbon 3D printer in de Benelux, bedoeld voor het produceren van functionele onderdelen. Waarom stapt hij nu wel in 3D printen?
Advertisement
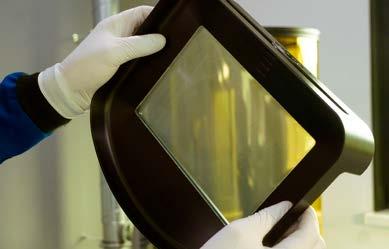
De cassette bevat een speciaal zuurstof doorlatend membraam. Dat is de kern van de Carbon 3D Digital Light Synthesis technologie.
Maick Klaassen komt uit de semiconductor industrie. Voor die sector heeft hij gereedschappen ontwikkeld voor de backend systemen. Vanuit die tijd weet hij de weg in Azië. Toen hij met QDP zijn eigen productontwikkelingsbureau startte, lag uitbesteden van het spuitgietwerk in China voor de hand. In 2010 vond Maick dat hij genoeg geleerd had over de Chinese markt om er zijn eigen productiebedrijf te starten. “Ik had geleerd dat iedereen in China interesse heeft in het maken van matrijzen en de eerste order. Als er een vervolgorder komt, hebben ze minder interesse.” En die vervolgorders hebben zijn Europese klanten regelmatig. Sinds 2010 maakt QDP daarom zelf de gereedschappen in China en spuitgiet er de kunststof producten. Het voordeel van bedenken en ontwikkelen in Nederland en vervolgens produceren in China, zit vooral in de prijs, zegt Maick Klaassen. Nog altijd. Matrijskosten liggen er een factor twee tot drie lager. Vaak gaat het om samengestelde producten, veel montagewerk dus. “Wij maken meestal kleine series, tussen de 1.000 en 25.000 producten, gemiddeld rond de 5.000. Dan is het niet rendabel om te automatiseren.” Overigens blijft ongeveer 20 procent van de producten die QDP in China produceert in Azië, meestal bij WestEuropese klanten die op de Aziatische markt actief zijn.
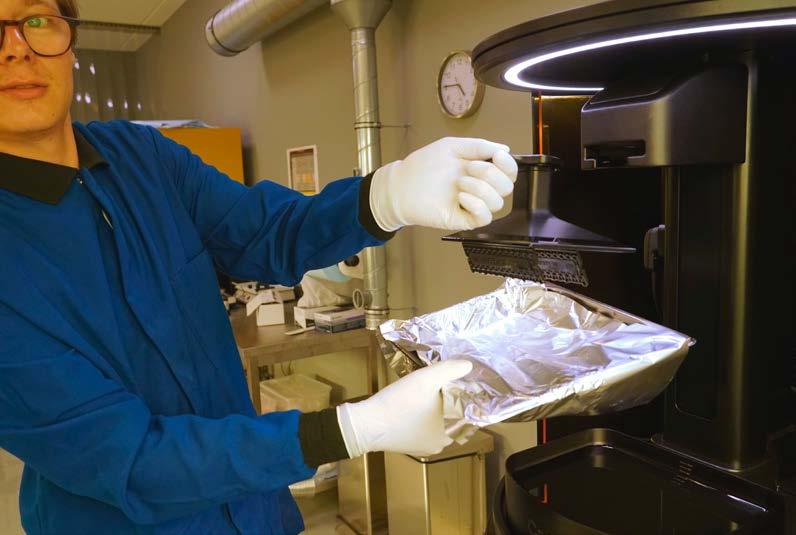
Waarom nu wel overstappen naar 3D printen?
De laatste jaren worden de series kleiner. Daarnaast ziet hij een groeimarkt, omdat Europese mkb-bedrijven een eigen ‘smoel’ aan hun producten willen geven door niet langer met standaard componenten te werken. Customizing is de drijvende kracht hierachter. Daar gelooft Maick Klaassen sterk in. En 3D printen Carbon is mede opgericht door Joseph M. DeSimone, die zijn hele leven als onderzoeker en ontwikkelaar met chemie is bezig geweest. Die achtergrond zorgt voor specifieke technologie die tot isotrope eigenschappen zorgt, vergelijkbaar met die van engineering plastics. Maick Klaassen vergelijkt het printproces van Carbon met koken. Elke stap is nauwkeurig beschreven per materiaal; qua maakt dat mogelijk.
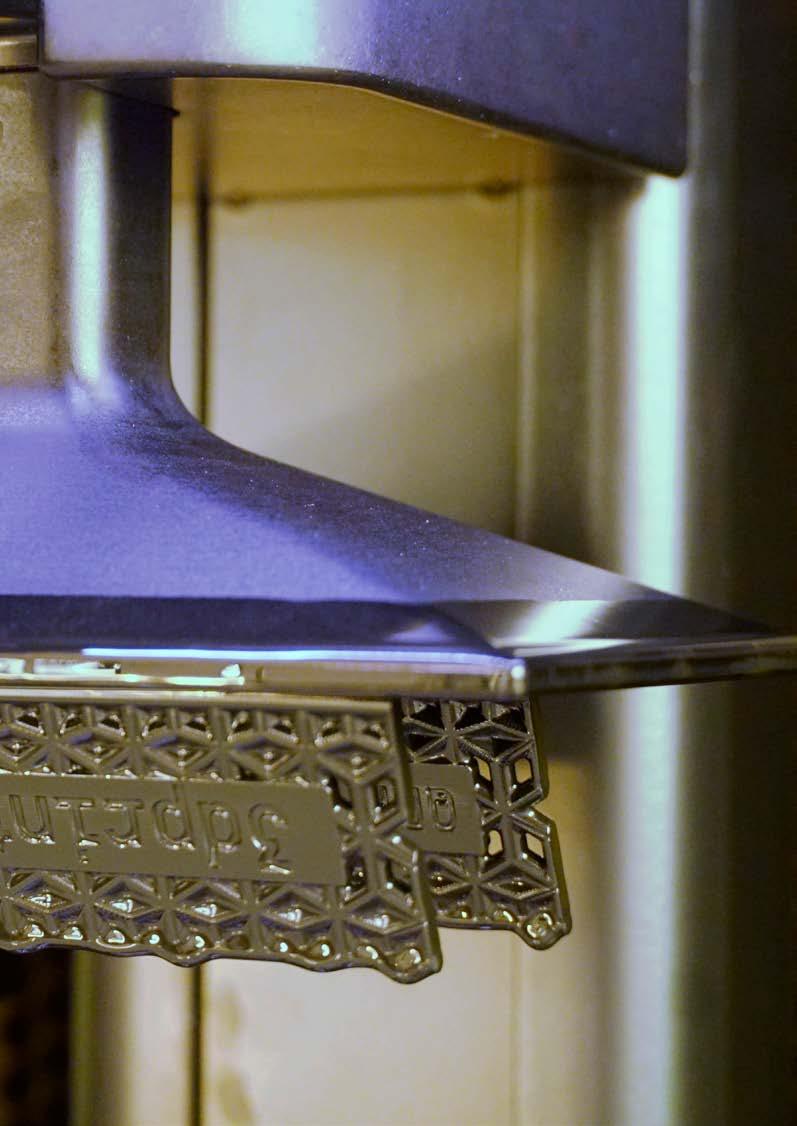
Desondanks is hij niet over één nacht ijs gegaan, wat wel blijkt dat QDP al in 2005 prototypes is gaan 3D printen. “Ik ben altijd kritisch geweest over 3D printen. Ronduit sceptisch. Voor prototypes prima; meestal doen we dat via servicebureaus; voor series vond ik de techniek niet goed genoeg.” Hij merkt echter dat klanten beginnen te vragen naar 3D printen. En er zijn nieuwe technieken op de markt gekomen waarin hij wel mogelijkheden voor het printen van eindproducten ziet. Met name de CLIP-technologie (Continuous Liquid Interface Production) van Carbon spreekt hem aan. De Amerikaanse fabrikant doet een aantal zaken anders dan de rest. Tussen het zuurstof doorlatend glazen membraam in de cartridge en het geprint product ontstaat een zogenaamde dead zone. Een dunne laag ongehard hars vloeit tussen het product en de glasplaat. Hierdoor print Carbon continu en verliest het geen tijd door na elke laag het product van de glasplaat af te moeten trekken, zoals bij andere DLP-technieken. Daarnaast voegt het een extra, warmtegevoelig materiaal aan het hars toe. Dat zorgt voor een tweede reactie in de oven, waardoor de polymeren crosslinken en het product isotropische eigenschappen krijgt. Dit uitharden in de oven varieert van enkele minuten voor een 1K materiaal in een UV-oven tot twaalf uur voor 2K materialen in een thermische oven. “De materiaaleigenschappen maken het verschil”, vat Maick samen.
Materiaalexpert ontwikkelt 3D printtechnologie
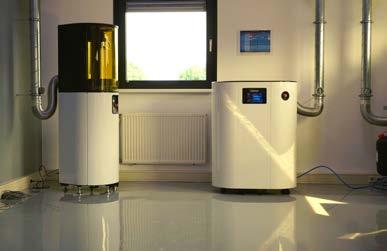
De fabrikant ziet er nauwlettend op toe dat in de ruimte waarin de printers staan alle voorzieningen zijn getroffen zoals centrale luchtafzuiging. Omdat de machines continu via het internet verbonden zijn met de fabrikant, kan Carbon ze eenvoudig updaten en wordt vanuit de fabriek bewaakt wanneer bijvoorbeeld een slijtdeel vervangen moet worden.
Alternatief naast spuitgieten
Voor QDP is 3D printen een alternatieve technologie naast het spuitgieten. Allereerst voor series die qua aantallen niet geschikt zijn voor spuitgieten. “Ik denk dat we een nieuwe markt kunnen pakken van orders die we vroeger niet konden produceren vanwege te geringe aantallen en de bijbehorende gereedschapskosten. Nu kunnen we deze printen”, zegt Maick. Zeker in de Nederlandse machinebouw liggen op dit vlak kansen: behuizingen bijvoorbeeld, of connectoren, een product waar Carbon samen met Ford hard aan werkt. Maick: “Connectoren is ook in Nederland een grote markt met de trailer- en aanhangwagenbouw. De tweede groep projecten waar QDP zich met de Carbon technologie op richt, zijn applicaties waarbij de meerwaarde in de nieuwe designmogelijkheden zit. Bijvoorbeeld producten met een latticestructuur. Als voorbeeld verwijst hij naar stoelzittingen, die nu uit schuim worden gefreesd. Producten van dergelijke afmetingen zijn geen probleem voor de Carbon 3D printers (met een maximaal bereik van 18.9 cm x 11.8 cm x 32.6 cm), denkt hij. “We kunnen de losse delen in de oven aan elkaar verbinden. In de oven ontstaat pas de crosslink tussen de polymeren.”
Valideren spuitgietproducten
De derde toepassing is het valideren van spuitgietproducten, bijvoorbeeld om te testen of een klikverbinding goed is. “We kunnen meteen vijf iteraties printen en de dag erna testen. De materialen van Carbon liggen dicht tegen de spuitgietmaterialen aan, dus dat valideren gaat prima.” Bridge manufacturing ziet hij ook als een optie. Terwijl in China de spuitgietmatrijs wordt gemaakt, zijn in Nederland al de eerste producten geprint en kan de klant met z’n nieuwe product de markt op. “Of omdat de klant eerst wil testen en pas als de markt reageert, investeren in een matrijs.”
Maick Klaassen verwacht dat hij de capaciteit van de huidige Carbon M2 komende tijd uitbreidt met extra 3D printers. Hij wil van QDP echter geen print servicebureau maken; productontwikkeling in combinatie met de productie blijft de kerntaak. instellingen kan de engineer noch de operator amper iets wijzigen. De machine zelf kan eigenlijk alleen bediend worden via de start en stop knop; parameterinstellingen gaan via de software van Carbon. “Daardoor printen we een constante kwaliteit en haalt Carbon de repeteernauwkeurigheid die de automobielindustrie eist”, zegt Maick Klaassen hierover.