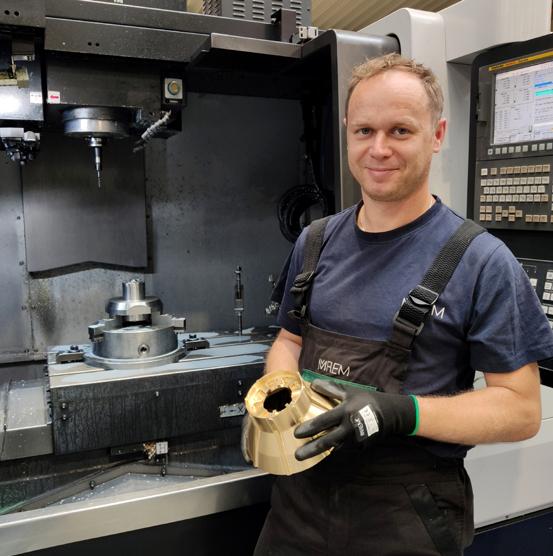
3 minute read
Don’t do this at home
from MAEM MAGAZINE 11
by MAEM
Even the best cake from a pastry store will never be as good as a home-made one, and a tailor-made suit will always be better than one bought in the best chain store. There are certainly more examples of homemade products or products made in workshops which undoubtedly surpass those made in mass production.
The case is completely different, when the precision and repetition of details has a direct impact not only on economic considerations, aesthetics, but mainly on health and human life. What makes two identical-looking elements, working in the same conditions, can have different periods of correct operation? Behind a seemingly uncomplicated element there are usually dozens of operations performed in the right sequence. Some of them can probably be omitted, making the final product look similar to the full-value one and it will be cheaper. The answer to the question is one of the key words for MAEM - durability. The story of durability and high quality of MAEM products is the story of a production process closely monitored at each of its stages. It is a story of hundreds of pages of documentation, instructions and procedures guaranteeing the correctness of processes. It is a story of production machines and measuring equipment which are inaccessible to most small manufactures. Above all, these are experienced specialists who, having access to described technical solutions, have developed unique technology, thanks to which we can be sure that products manufactured by MAEM meet the highest quality requirements.
In this article, we will show you some of the more important operations from the manufacturing process of one of the essential parts of any separator.
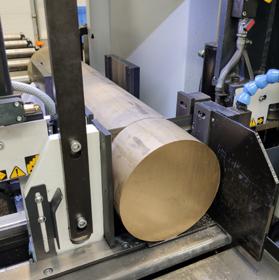
The first stage of production is cutting of raw material, which is a brass rod, into semi-finished products, disks of appropriate height. The process is fully automated, numerically controlled from a touch panel. Our new band saw is described in the Made in MAEM section of the 10th edition of our Magazine.
Next, the workpiece goes to the lathe, where the first turning operation takes place. At this stage, the workpiece is given an external shape. In addition, the central hole and the face groove are made.

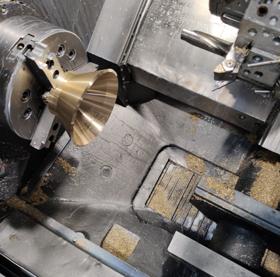
The following operation is also performed using the lathe. During this operation we perform boring of the inner profile and this is the last operation performed on this type of machine.

After two stages performed on lathes, our workpiece begins to resemble the final product. Now the carriers are milled on the bottom of the workpiece from the inside. The semi-finished product is clamped in soft jaws in a three-jaw chuck.
In a further step of production, special tooling is required to clamp the workpiece. The tooling was designed and made by MAEM's Production Department employees. It is one of our original ideas. At this stage of production we make the rotor socket. The trochoidal milling method has been used to make the socket.
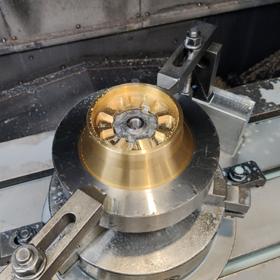
The last stage of production is external contour milling, in which we used an innovative milling method called plunge milling. By using this method, we have managed to significantly shorten the time of this operation in comparison with the previous version of the technology.

The final moment of the whole production process is the inspection of the detail by the MAEM Quality Control Department. Only after all the guidelines have been met can our product be put into the finished products warehouse. On the photo - dimensional control with the use of coordinate measuring machine.
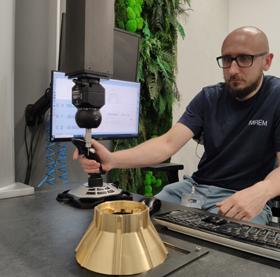
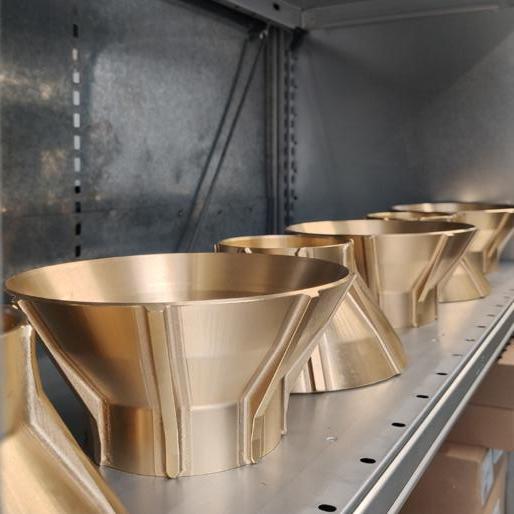
Now, the distributors made by MAEM will be secured, they will go to the warehouse shelves and from there to the engine rooms of the ships of customers who pay attention to the quality of the spare parts they use. To see more photos and videos of the detail production process at MAEM, visit our profile on Instagram @maemcompany. | pinned 'Production' section.