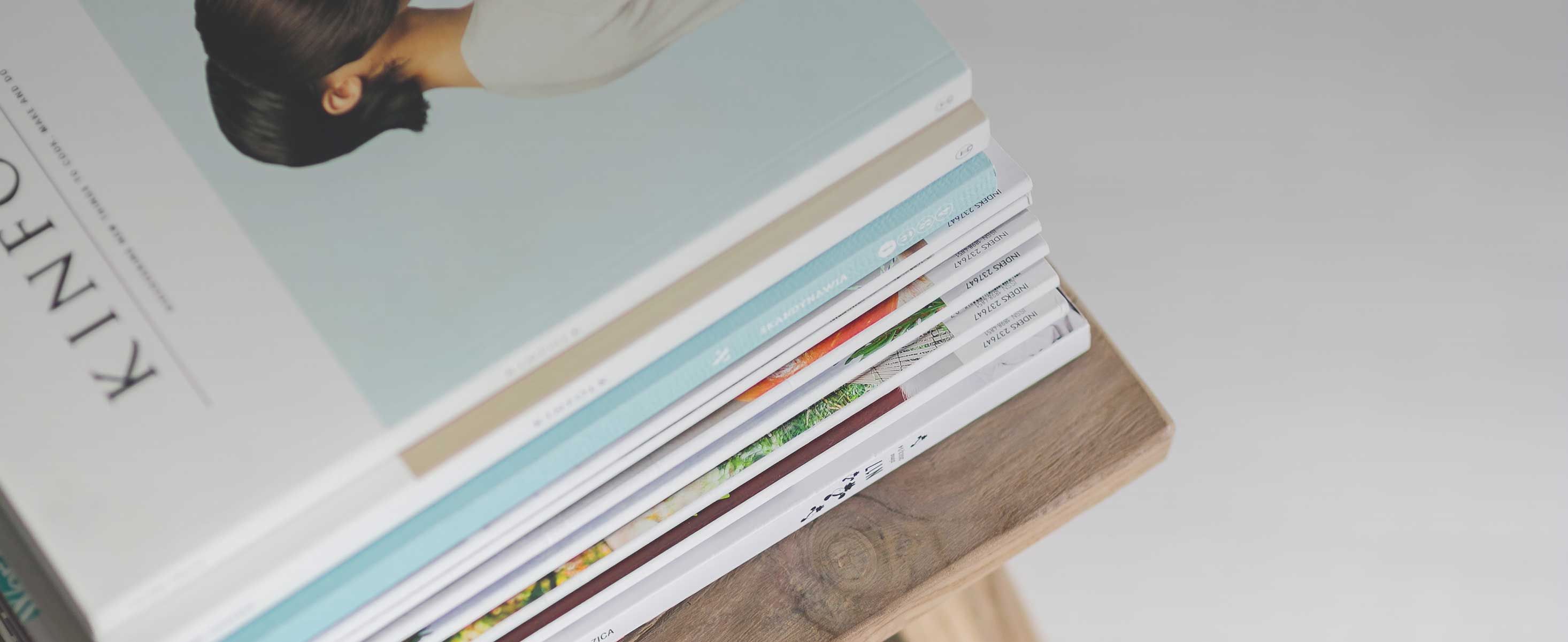
9 minute read
Case Study: Gmelina: Value additing to Gain Income
Improving wood quality through plantation management
a. silviculture b. choice of most suitable species/species mix (including prime hardwoods) c. de-branching d. thinning e. harvesting at an optimum age
Advertisement
Reducing the wastage during
a. harvesting b. hauling c. ripping d. sawmilling e. storage f. drying
Venturing further up the wood preparation value chain
a. felling b. hauling c. ripping d. sawmilling e. air-drying f. kiln-drying
Reducing or eliminating SOPs
a. for licenses b. checkpoints c. monitoring fee
Establishing a buyers’ information system for better linkage of buyers and producers Taking over trading function
a. eliminating one or more trading levels b. building up direct trade relations with further processors
Box 01. A summary of how improvements can be achieved to improve the competitiveness of farmers/Pos.
companies successfully. Further processing at the location where the wood is produced gives advantages at least up to the level of ready-to-sell lumber.
aDDIng VaLUE To gaIn InComE
CaSE STUDY: gmELIna
It can be seen from Table 4 that the net returns per cubic meter of Gmelina increase as the farmer is made to perform other functions higher up the value chain. The benefit at higher processing levels is not only higher sale prices, but increased income opportunities for community members and a broader range of possible buyers. This is of special importance since the supply of the most common plantation species like Gmelina and (Honduras) Mahogany seems to be higher than the domestic demand. Only higher quality and well-processed lumber can increase the competitiveness that might be necessary to operate profitably in the long run. Fig, 6 shows the value added per board foot of lumber as the material moves from the supply side to the consumer end of the value chain. These are based on the differences in prices as the product enters into and exits from one function to another in the plantation wood value chains. For purposes of simplifying the illustration, only the average prices are shown. Note that the closer the functions are to the markets, the higher are the profit margins associated with the products. The range of prices paid for lumber as of the end of 2008 at different levels of the chain and at different locations are presented in Table 6.
The selling prices can be represented by a simplified value chain for sales from Leyte Island to Cebu City as shown in Fig. 7.
In the National Capital Region (NCR), prices for Gmelina wood are on average Php3/ bd ft higher than in Cebu City.
The plantation wood value chain often includes hidden profits. Some examples of how these arise are through the following: (a) The trader has fewer expenses for the harvesting operation than calculated for determining the farm gate price when buying from POs; (b) Volumes are understated to save fees, government share, etc.; (c) The same low price for Gmelina is paid for all species harvested although selling prices are usually higher for other species; (d) Flitches are bought oversized and the lumber is sold undersized after re-
Value adding per board foot of Gmelina lumber up to furniture as final product.
Specific inputs Production
P12/bf
Harvesting1
Govt: P5.10 for fees & other charges
Lumber Processing2 Wholesale/ Retail Furniture Making3
P26-30/bf
Trade
P20/bf
P14/bf
P2 for hauling and other charges P6 for resawing & markup P6-P10 for conversion to furniture component
Farmers: P3.50 inclusive of inputs Buyer: P3.40 for operating costs
Consumption
Figure 6. Value addition along the different functions in the Leyte Island plantation wood value chain.
sawing. Sometimes one additional board can be gained from a flitch than what has been actually paid for. Oftentimes, the buyer makes deductions from the farmers for various reasons.
These are examples on how a higher income in trading can be gained. The surplus results in reducing the benefits of the farmers, the government and the final processor or consumer. For plantation-grown Mahogany, POs usually get the same price as for Gmelina. Private plantation and traders might get a higher price as they are paid at approximately 20% more than what is generally received by POs.
During the validation workshop, some PO making is also a very different trade compared to representatives mentioned that they would like plantation management and lumber production. to venture into furniture making. This is to The value of the stock would have to be • Existence of entrepreneurial skills and spirit maximize the use of the wood they own and In summary, being able to move vertically up to add more value to it. However, the decision the value chain has requirements that could to establish a furniture shop should be made pose as risks and limitations to POs/farmers. independent from owning wood supply for the Among these requirements are the following: a)financial resources for
Farm gate Delivered Cebu Delivered Cebu Delivered Cebu Lumber equipment, Green Air Dried Kiln Dried Yard structure, and 13 PhP 17 PhP 19 PhP 23 PhP 31 PhP working capital; b)additional Figure 7. Simplified value chain for Gmelina lumber produced in Leyte Island and sold documentation in Cebu City (in PhP/bd. ft.) requirements; c ) m o r e following reasons: entrepreneurial and production a) Owned wood supply might not be management skills; available all the time. Therefore, a bigger d) technical and product design skills; stock of lumber might be needed during e) access to utilities; and periods where no harvesting takes place. f) linkage with consumer markets. financed by the PO. It would take more than good intentions on b) If the lumber can be bought at the same the part of POs/farmers to embark into, much price as the one at which the lumber they less become successful in, venturing into the produce can be sold, then there is no functions further up the plantation wood value competitive advantage to have their own chain. There is a vital need to thoroughly assess wood over someone who buys wood. the technical, entrepreneurial and financial The decision to establish a furniture workshop readiness to move up the value chain and to should be made mainly on basis of factors like: perform functions other than production • Markets and market access and to some extent, harvesting so as not to • Availability of skilled workers unduly expose the POs to risks that can spell • Availability of supplies (glues, fittings, huge disaster on PO finances and relationships finishing materials, etc.) among members. sophisticated capacity of POs/farmers to determine their • Availability of capital This does not mean, however, that POs will • Available buildings or land and funds to forever be consigned as the lowest-income erect the needed buildings earning participants of the plantation wood • Availability and security of power and water value chain by merely confining themselves supply. to the supply end of the chain. Farmers can undertake improvements in their planting In most cases furniture makers will look for a and tree plantation management practices location close to markets, labor and supplies. to produce better quality timber that could In case a PO plans to open its own furniture command a higher price in the market. They shop, a location in or near to a city should be can also learn and adopt improved techniques considered. In case a location in the municipality that would increase the per hectare yield of their of the PO is the only possible choice, then the plantations. Farmers should also gain better size of the shop and the range of products access to updated market information so they produced should suit the potential market at can bargain for more favorable prices for their that location. products. The harvesting and hauling options are also within reasonable reach of the farmers, Seldom do forest or plantation owners operate requiring only minimal investments in the a furniture factory since forest management, acquisition of chainsaws, and perhaps, carabaos harvesting, sawmilling, drying and marketing and other low-cost transport systems, as well already require much attention on the part of as skills training in harvesting and tree felling, the entrepreneur to be successful. Furniture primary log breakdown and wood handling.
Support equipment 384,000 Main saw chosen: WoodMizer LT28; price USD 12,000.-; capacity 200 bd.ft./hr – and import 35,200 bd.ft./monthStorage building for air Investment cost440,000 PhP Assumptions: drying, etc. Sawmill 576,000 • Increased recovery rate from logs by 25%Support equipment and importTotal investment 1.4 M PHP 384,000 • Sales price of PhP 18 instead of PhP 12 (harvesting and hauling included) Storage building for air 440,000 • Capacity utilization of 75% = 26,400 bd.ft./month drying, etc.
Total investment 1.4 M PHP Operational cost PhP
Investment cost PhPMilling, handling, petrol, Sawmill overhead 576,000
Support equipment and import Total operational costs
384,000
Storage building for air drying, etc.
440,000
2Operational cost-4 PHP/ bd.ft. Milling, handling, petrol, ( used 3 PhP)
overhead Total operational costs 3 PHP/bd.ft. PhP
2-4 PHP/ bd.ft. ( used 3 PhP)
3 PHP/bd.ft.
Total investment 1.4 M PHP
Benefit
Operational costBenefit PhP 25% higher recovery = 78900 bd.ft./year at 18 PhP PhP/year
Milling, handling, petrol, overhead 2-4 PHP/ bd.ft. ( used 3 PhP) Higher sales price of the remaining 75% of lumber produced: 236,700 25% higher recovery = 78900 1,420,200
Total operational costs bd.ft./year at 18 PhP 3 PHP/bd.ft. bd/ft. × 4 PhP
Gross additional revenue Higher sales price of the remaining 946,800
75% of lumber produced: 236,700 Operational costs 316800 bd.ft .× 3 PhP Benefit bd/ft. × 4 PhP PhP/year Total gain in return
25% higher recovery = 78900 bd.ft./year at 18 PhP Gross additional revenue 1,420,200 Higher sales price of the remaining Operational costs 316800 bd.ft .× 3 946,800
75% of lumber produced: 236,700 bd/ft. × 4 PhP PhP
2,367,000
950.400
PhP/year
1,420,200
946,800
2,367,000
950.400
1,416,600
Gross additional revenue Total gain in return 2,367,000 1,416,600 Operational costs 316800 bd.ft .× 3 950.400
PhP
(A WoodMizer Bandsaw was chosen as example since the DOST at the Forest Products Research and Development Total gain in return 1,416,600 Institute (FPRDI) avails of a similar model. Training could possibly be provided by DOST).
Box 02. Brief economic estimate for a mobile or semi-mobile band-sawmill
The main advantages are reduced transport costs and reduced costs for land and labor. The success of a venture depends less on calculated possible profits but more on factors like management, skills, manpower, and market access.
However, to illustrate how fast investments could be recovered, an example is presented in Box 02. In here, the main benefit is gained from higher recovery rates. Sales prices and operational cost were conservatively assumed.
Box 02 shows that the return of investment seems possible in 1 year time, provided charges on the part of the government remain the same based on the raw material input in currently used system. If the higher recovery rates would result in additional charges for government share (30% based on 12 PhP/bd.ft.) and monitoring fee (1.5 PhP/ bd.ft.), then the additional cost would be 402,390 PhP/year The return in investment would be approximately 4 months longer.
This scenario is estimated for conditions where logs for cutting are available all the time and all lumber produced can be sold. Stand still times are maximum 25% (at 8 hours/day). Based on experience, the reality looks usually different with many delays and stand still times as well as management faults. To expect a double or even longer time for the return of investment seems to be advisable.