
9 minute read
Commercial diving
Offshore technology for inshore challenges
Inshore diving from a new perspective with technologies developed in offshore work adding real benefits for inshore and inland contracts.
Words: Paul Edwards, EDS
For decades, the best resourced commercial diving sector has been around offshore oil and gas, a now life limited sector. But there are many developments in equipment, methods and working practices from offshore that the inshore sector can usefully incorporate to make our work easier and better. In this article, we’ll look at a few that have already proved their worth in the onshore sector.
INSHORE DIVERS LEVELLING UP
Offshore has, in recent times, enjoyed eye watering budgets which have supported huge technology advances and, if it is to survive, the inshore sector must also take advantage of those developments. As readers will know, there is a growing quest for alternative energy supplies which means that, for inshore Diving Contractors, opportunities abound. Solar, Wind, Hydropower and Nuclear are areas in which the specialist skills of inshore divers can help create a cleaner/greener environment. But we’ll need to educate potential clients in those industries about what we can bring to their programmes.
OFFSHORE TECHNOLOGY UTILISED INSHORE
I recently saw this old ROV (Remotely Operated Vehicle) used as a garden ornament in a hotel; it reminded me of my time in the Navy more than thirty years ago when these were an effective way for disposing of mines.
Then, an ROV will have cost hundreds of thousands of pounds (probably more). Since then, the world’s Navies have spent a fortune researching and developing this technology (see below) so we don’t need to. Modern ROVs are a cost-effective tool for any diving company.
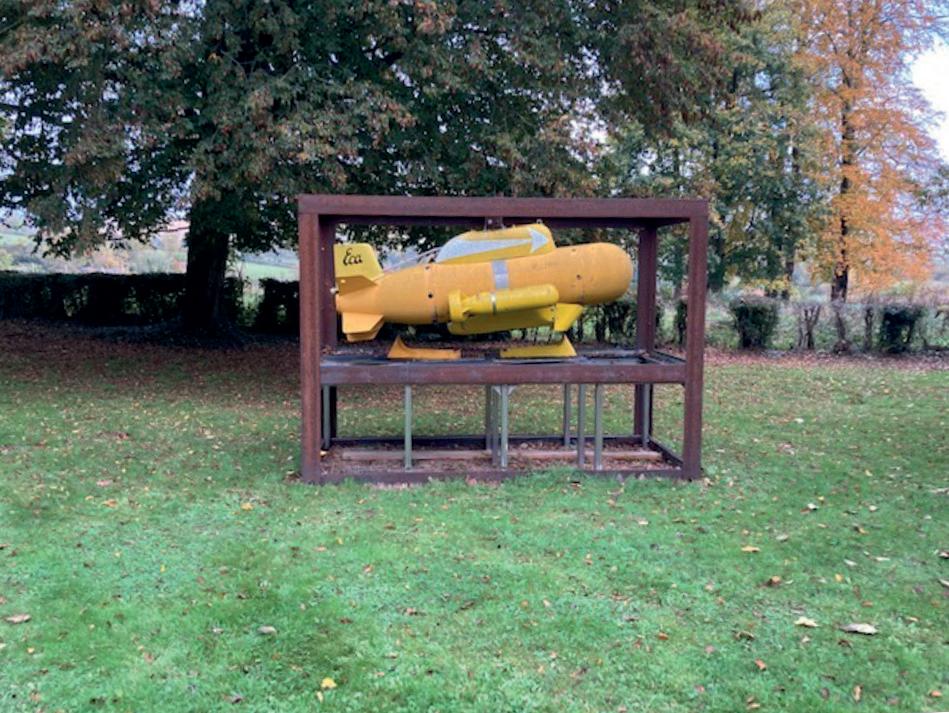
ROVs won’t ever replace human divers but they can form part of the diver’s toolkit. Often an ROV can make a site safer and get safety critical information faster and more easily than a diver. They should be considered more in our everyday work.
Let’s look at few real world examples where the deployment of technology developed for offshore work can add value and safety to inshore and freshwater diving work.
WORKING SMARTER NOT HARDER
The first case was a Reservoir which required de-watering. It was a classic example of not knowing what was there before we deployed the ROV. We knew that none of the valves were working, so they were not able to draw the reservoir down, but nobody had any idea why the valves would not work and what, exactly, was there. If a diver had been drawn into a pipe, the consequences could be catastrophic; but an ROV ran less risk.
There were six platforms within the tower, with the only valve low enough and known to be working being blocked. An ROV was deployed within the tower and identified an additional flange that was open to the elements. The ROV was sucked into the pipework identifying a DPDZ (Differential Pressure Danger Zone) and had to remain there for 18 months. When, after much negotiation, a diver was deployed, they were able to avoid the DPDZ and repaired the other lower valves enabling the reservoir to be drained at a controlled rate. Knowing that there was a differential pressure at a certain level made it a lot safer because the risk could be managed and controlled accordingly. As the reservoir drained it revealed a body chained to a kitchen sink blocking the lowest scour valve. The woman whose body it was had been missing for 20 years and could now eventually be laid to rest, her husband was convicted of her murder but would not confess to where he had hidden her body.
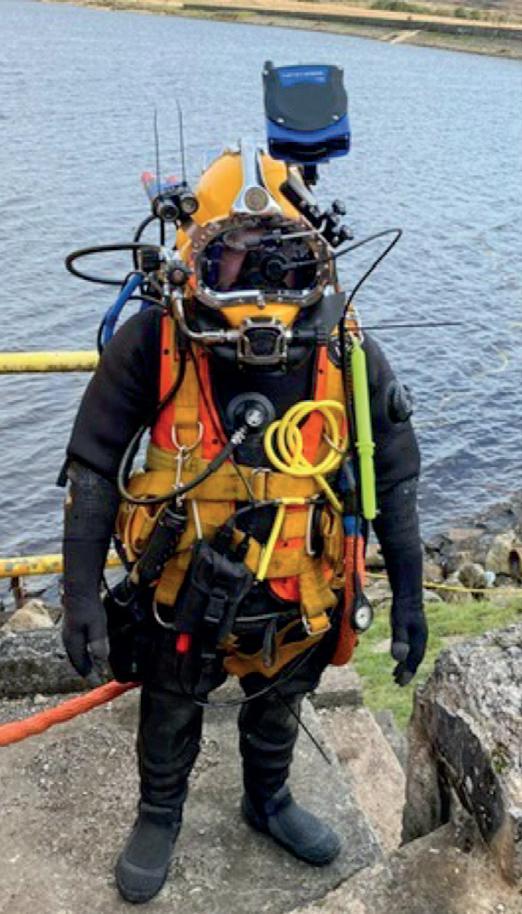
USING ROVS INSHORE
Another challenging case was to isolate a dam from the wet side of a tunnel, 30m deep, 66m long and 5m wide. The original scheme was to carry out the work without divers because the perception is that diving is dangerous, but the ROV sonar detected a tighter space than the as built drawings had indicated so we carried out a tactile divers’ survey and amended our plans accordingly. A good case where the ROV complemented the diver.
Initially the direction on this job was that it was far too dangerous to dive in the tunnel, but with proper planning it was possible to demonstrate that it could be made safe; ultimately, we changed the design of our isolating methods which proved very successful and the downstream valves were changed within a couple of days. If we had used the original design, it simply would not have worked so, again, this is a great example of having ROVs as a tool for the dive team. The visibility on most inshore tasks is usually poor at best. Most, if not all of you will have fumbled about in murky water and I think it makes for better divers; if they can complete a task without having seen it, divers will be even better when they can see what they’re doing.
With visibility being what it is we are carrying out trails on a Tritech diver mounted sonar to take the diver to the job. The diver has a monocle attached to the outside of the helmet the same way you would mount a CCTV camera and light; the sonar picture is what the diver sees.
This cutting edge technology works very well in poor visibility. How robust and diver friendly it might be remains to be seen, but initial trials have proved successful.
The next level of multibeam sonar
As part of a demonstration, we carried out a trial whilst undertaking a night dive on an intake tower, it had to be carried out at night due to water supplies being so critical in the day with not enough storage to allow for uninterrupted supply to the end user.
We had been looking into multibeam technology for a while, but COVID delayed its progress, there are several different manufacturers making this type of equipment but, on this trial, it was so successful we placed an order the next day.
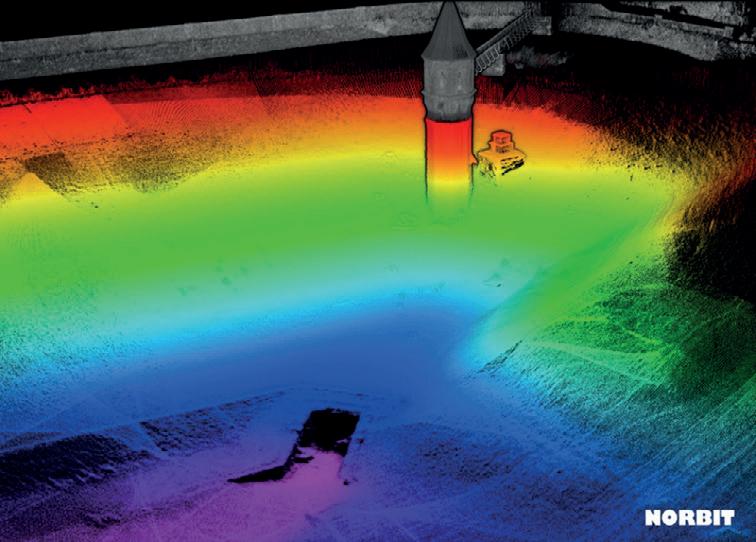
This is what we saw from the small boat whilst circling the intake tower, the sonar, combined with a laser scanner, stitches the image together to give a 3D point cloud image. It really is like removing the plug from a bath. The alarming problem we identified was that we were about to dive on the intake tower to repair one of the flap valves right next to what appeared to be another larger intake of which nobody, neither we nor the customer carrying out the isolations, had been aware.
Before we dived the ROV carried out a detailed survey to ensure there was no draw and it was safe to dive. That survey showed that the previously unknown intake was probably an old intake that had been filled in after construction of the tower, if it had been a live intake, that could have had very different ramifications. Nobody knew the state or condition, so checking it with the ROV was essential. Images using the technology are on a point cloud so users can look at whichever angle they prefer.
AN ROV WITH MULTIBEAM SHOWS THE SAFE WAY
The existing water company had to carry out some isolations on the wet side of a dam and there was an alleged diver’s hatch that we previously failed to find with an ROV. With poor visibility, nobody knew what the hatch looked like, so we needed a more accurate way of finding it. The multibeam sonar revealed exactly where it was. We had a GPS fix, dropped a shot line attached to a buoy and the divers did the rest.
On this image you can see the entrance to the tunnel which was not accessible, so the diver dropped through the hatch and carried out a tactile survey of what was required, all completed in a single 25-minute dive.
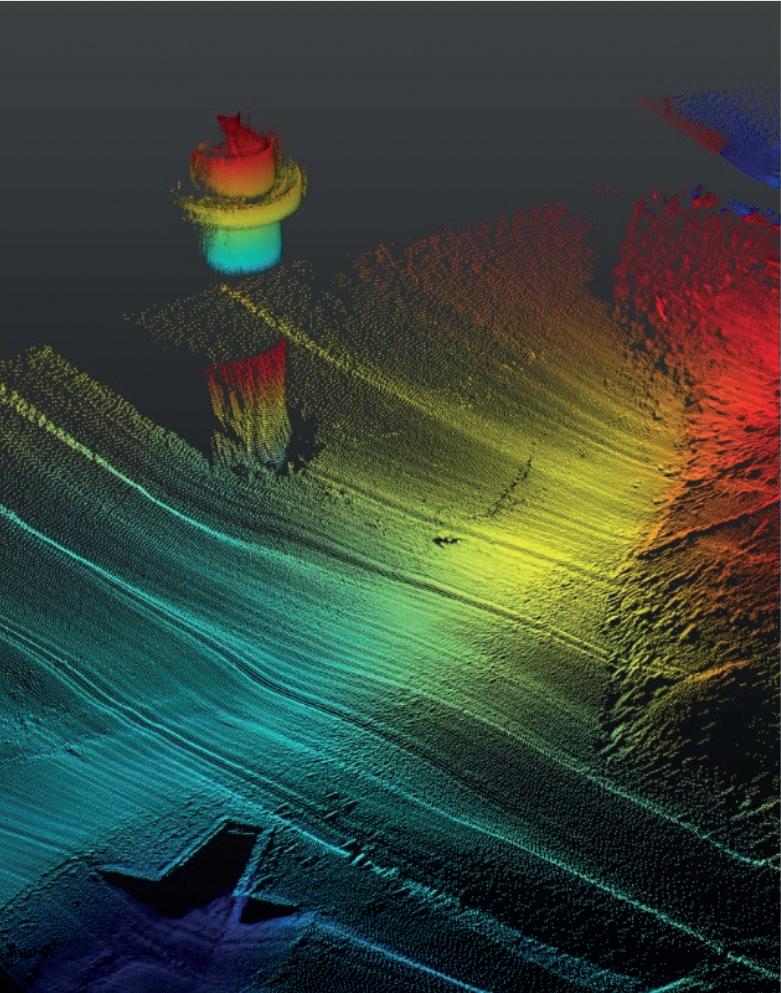
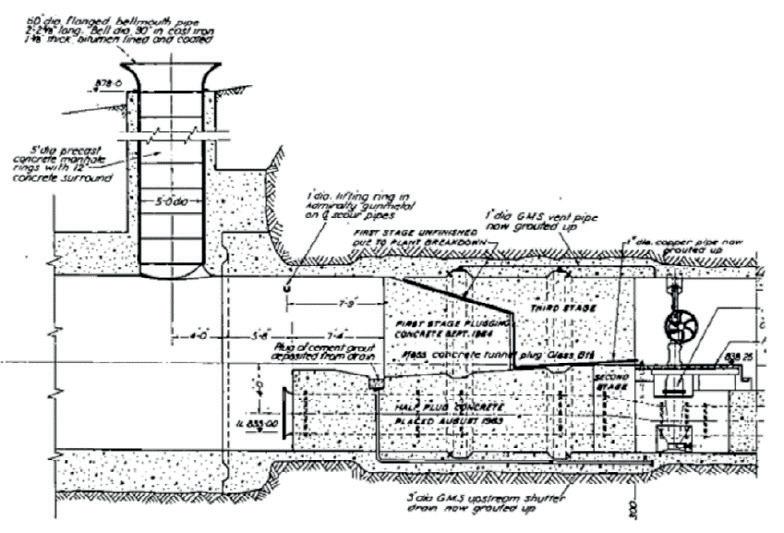
INSTALLING PIPES IN POOR VISIBILITY
This job was finished off earlier this year where we had to install a series of pipes (2 x 450 1 x 280 1 x 150mm) over 80m long supported on concrete blocks within a reservoir to a level of
+/- 50mm, the customer didn’t think we would achieve it as visibility was so poor. The divers dug the trench by hand with airlifts and hydraulic pumps, the levels along the 80-metre section were to a tolerance of less than 15mm. Like most jobs, preparation was everything but when you can use sonar imagery to produce a usable image it really can show the doubters what can be achieved.
MEASURING A TUNNEL
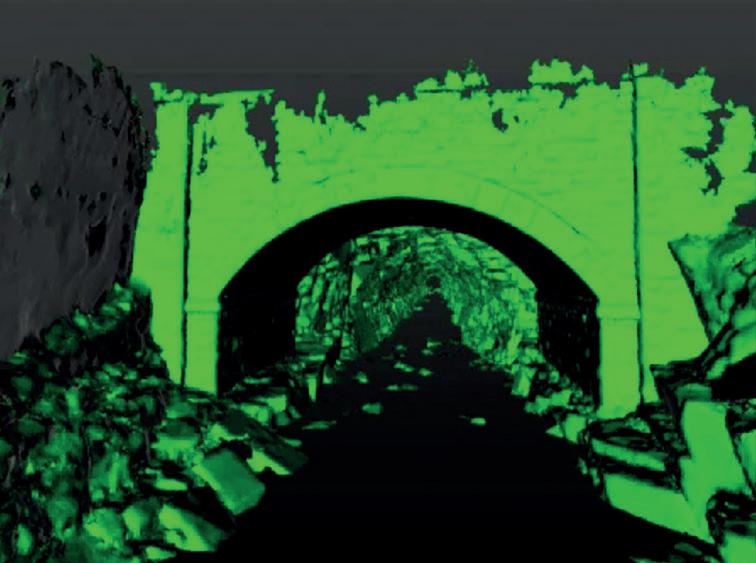
This is a point cloud laser survey that has been meshed to create a fly though, it works on the same principal as the multibeam sonar. This was a culvert/tunnel that required measuring to understand what its maximum capacity would be under flood conditions. Because the tunnel was not symmetrical, and the customer required detailed measurements which, taken conventionally, would have taken an age, we opted for the laser survey which was millimeter perfect and completed in the same timeframe.
FINISHING THE JOB AFTER A RESEVOIR IS FLOODED
This was another flythrough with a point cloud 3D laser. For this job we had already removed the pipe from within the tunnel and placed an isolation to the existing pipework whilst it was dry. When the reservoir was flooded, we were able to go back to remove the blanking flange. The information shown here was very useful for the diving supervisor and, particularly, the diver; it formed part of our risk assessment and method statement and gave them as much information as they needed.
THE BENEFITS OF EMBRACING TECHNOLOGY
Technology is becoming more readily available and less expensive, and really does benefit everybody, from the diver doing the task, to the operational planning for getting the job done. It is also beneficial to give customers detailed information, something they would have most likely never seen before. But technology will never replace the human diver it simply makes their job easier.

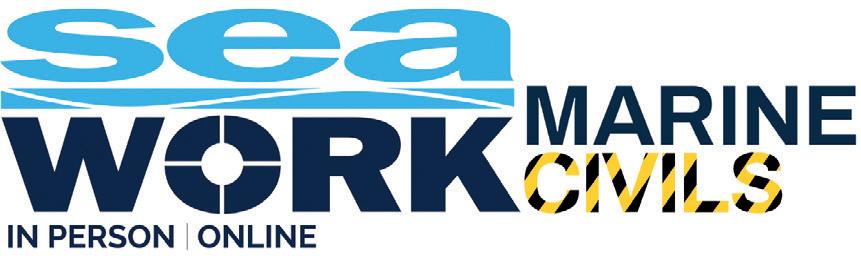
Seawork is open for business – all year
Reserve now for 2023. Keep your full business profile and capabilities in front of your customers 365 days a year.
Europe’s leading commercial marine and workboat exhibition
DiveWork at Seawork is a showcase for the professional diving and subsea industries. DiveWork consists of a pavilion and a trail, with a Dive Tank on the Quayside where all the latest underwater equipment and services can be demonstrated. Look for the Diving & Underwater Services, Hydrography category on Seawork.com to connect with this industry sector all year.
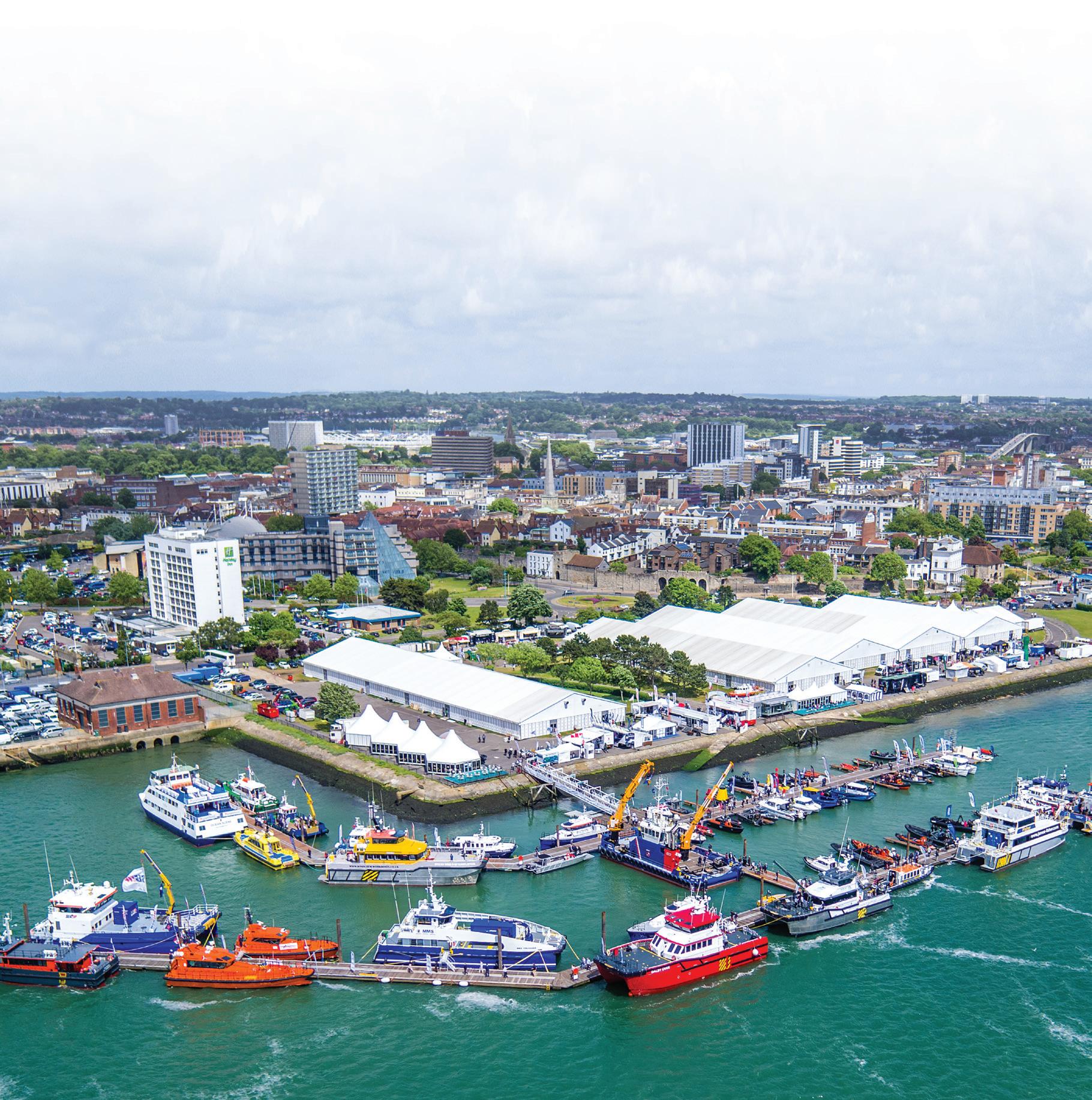
JUNE 2023 13 15 TO
Southampton United Kingdom
Co-located with: Also returning in 2023 Speed@Seawork
Sea Trials & Conference
For more information visit: seawork.com contact: +44 1329 825 335 or email: info@seawork.com
Media partners: MARITIMEJOURNAL