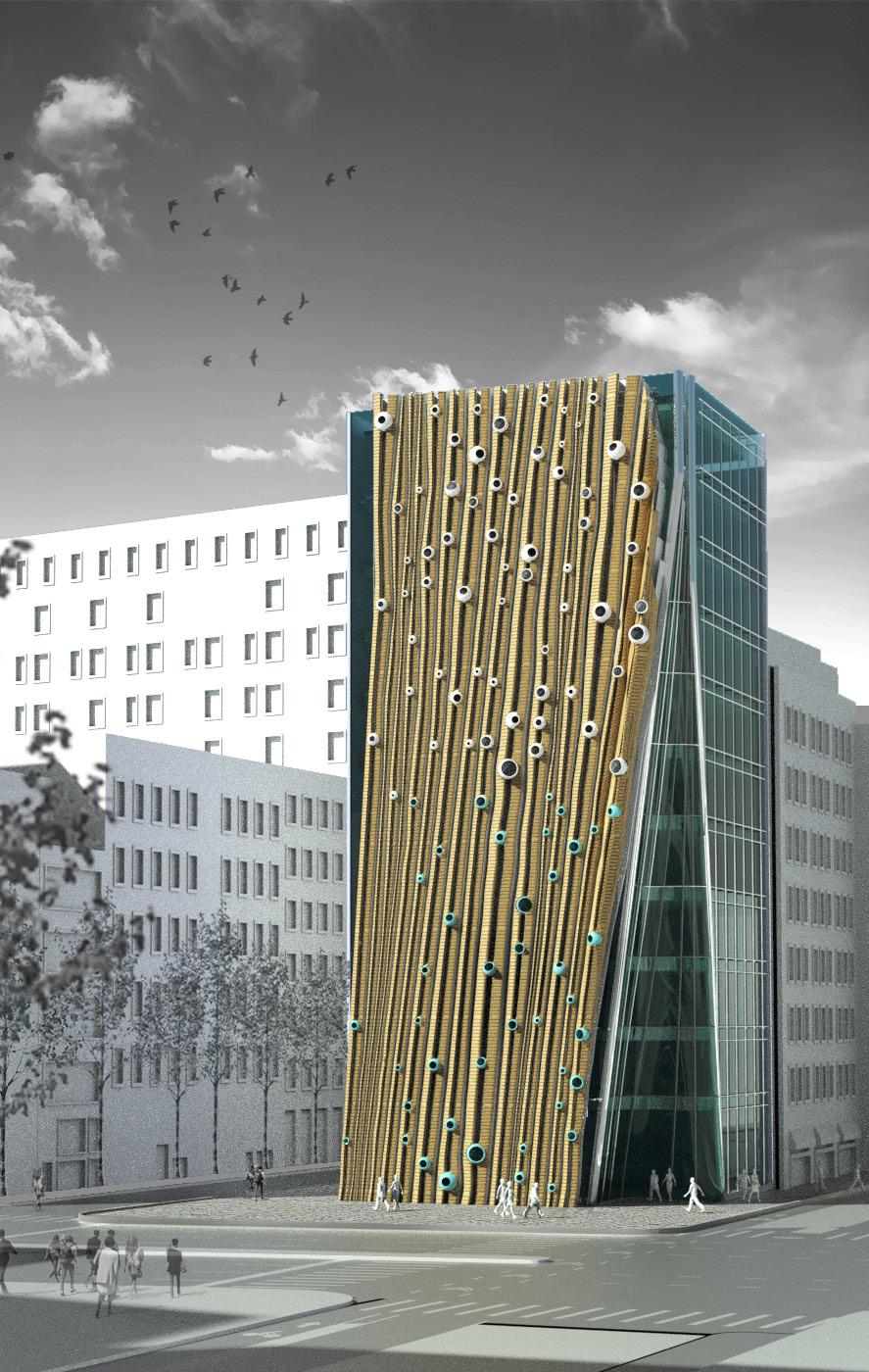
1 minute read
Vita wall
from Portfolio 2022-2023
Academic project - Group Work - UPENN
Teammates: Cem Akgun, Aisha Alshehri ,Adhityan Anbumozhi
Advertisement
Instructor: Robert Stuart-Smith
The objective of this project is to enhance the design of ceramic facades using nature as inspiration and robotics as a tool. The aim is to create a mono-material for architectural ceramics by incorporating slip-cast geometries into robotically clay additive manufacturing. This will result in nesting architectural prototypes that are porous and made from a single material. The project builds on prior research, including studies on porosity, robotic additive manufacturing (RAM), and multi-material embedment.
To increase the nesting surface area, the proposed workflow involves embedding unfired slip-cast components into 3D-printed clay using a specific linear material deposition. This approach will be demonstrated through a proof-of-concept architectural prototype. The project inspired by both ancient pottery practices and ongoing research on robotic additive manufacturing, blending traditional and innovative methodologies.
Contribution To The project
Idea
Modeling+Scripting
Diagram Development
Presentation+Video+Photography
Robotic
Our goal is to improve the versatility of clay through the use of rotatable geometries. To achieve this, we conducted several physical and computational experiments that involved combining two manufacturing processes: slip casting and clay additive manufacturing. We also created customized hardware and software tools to address the challenges of ceramic-to-ceramic joints. By combining bone-dried and unglazed slip-cast geometries with wet clay additive manufacturing, we were able to achieve a unique post-processing behavior, which allowed us to rotate the slip-cast components. Overprinted clay geometries, nozzle size, printing velocity, material deposition, clay supports, and final ornamental effects were designed accordingly.
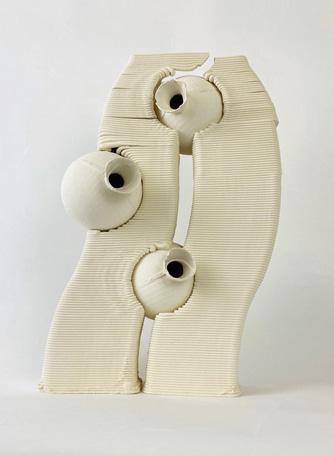
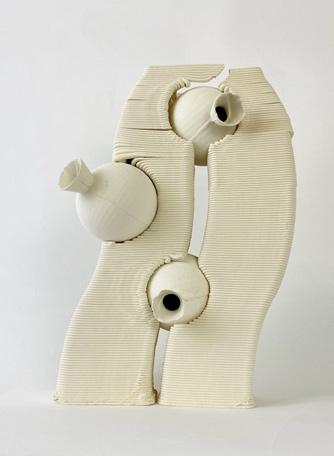
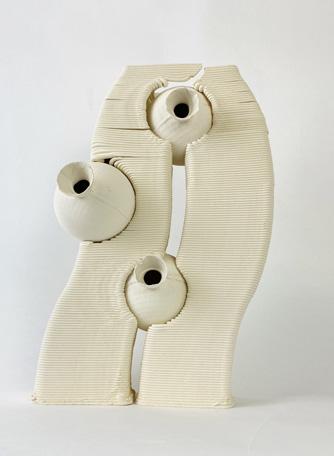
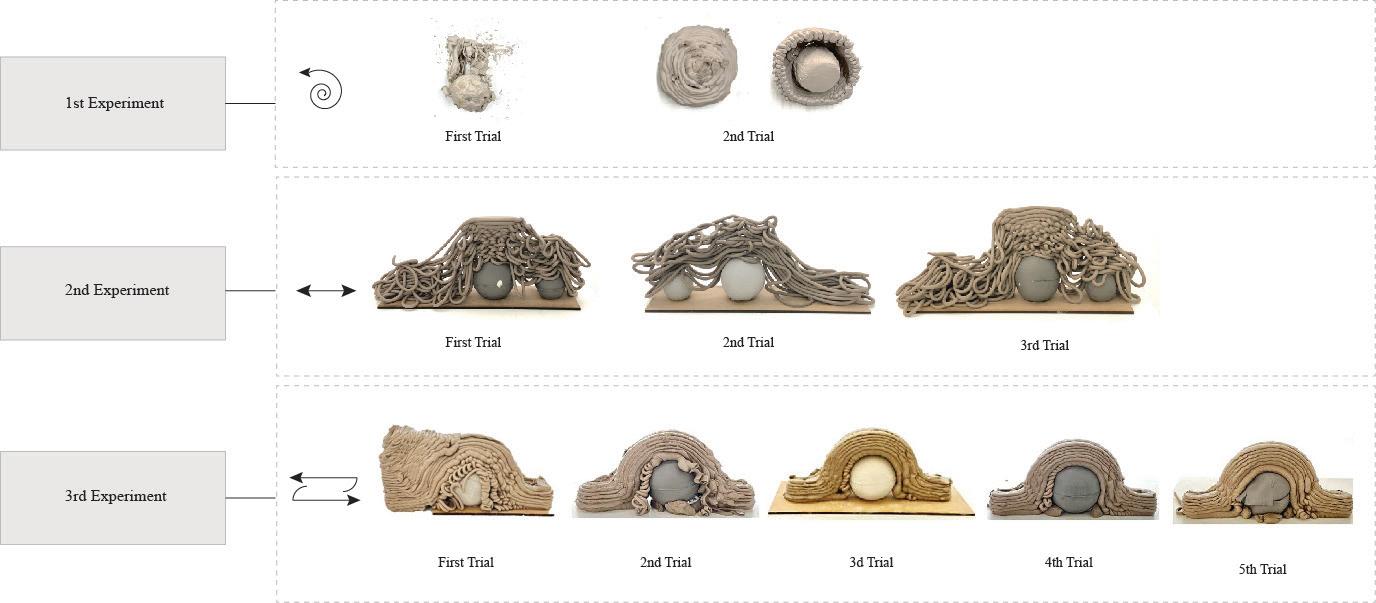
Material Deposition Experiment
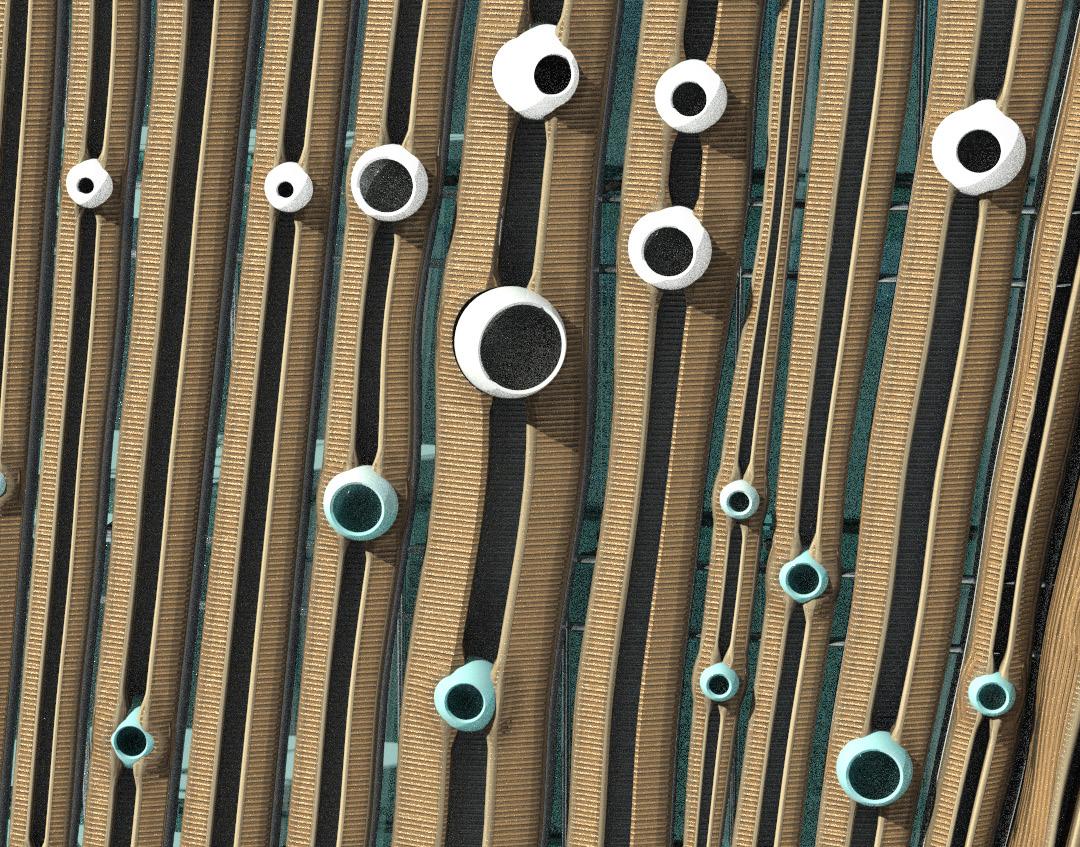
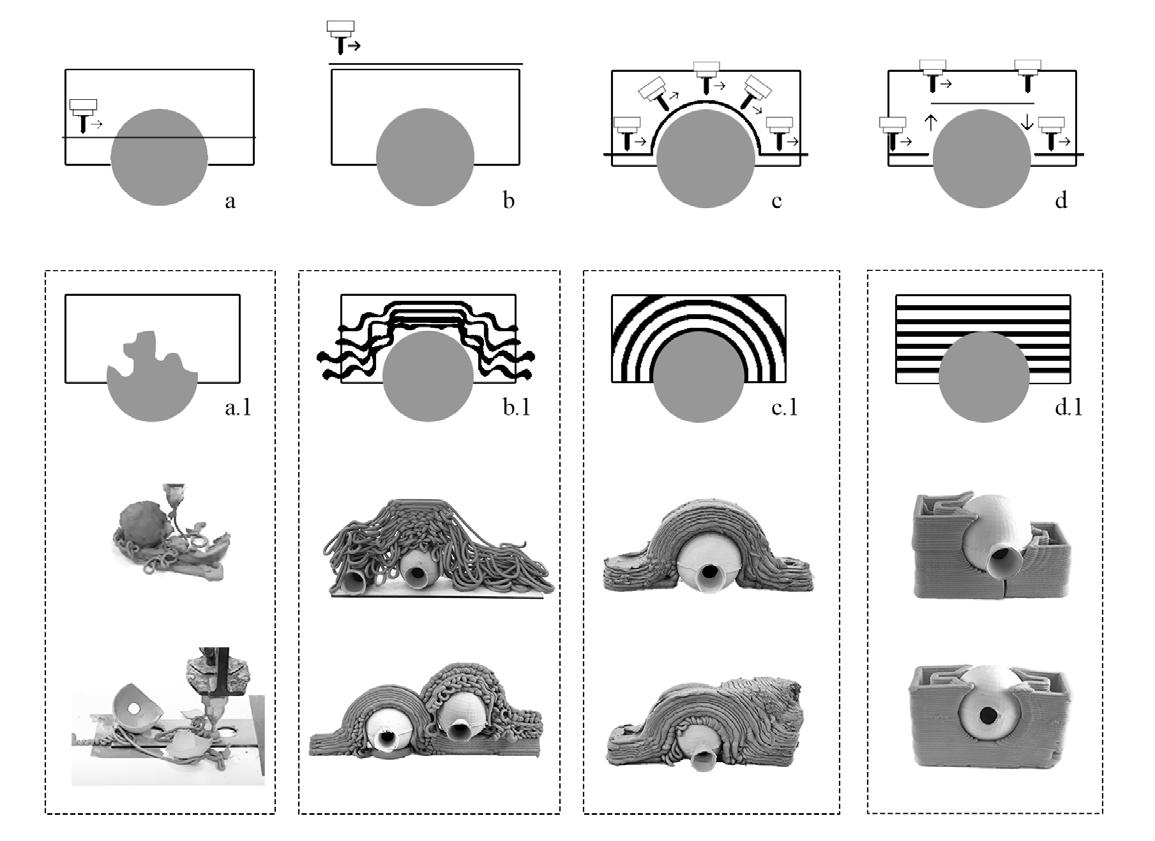
Project Development
The left image shows the Fabrication of one piece of the final prototype, portraying clay-printed internal supports, cylindrical slip-cast support, and sphere contours necessary for embedding the slip-cast sphere and its rotation (a: mesh geometry, b: contour layers of geometry, c: actual clay printing before completion of the piece)
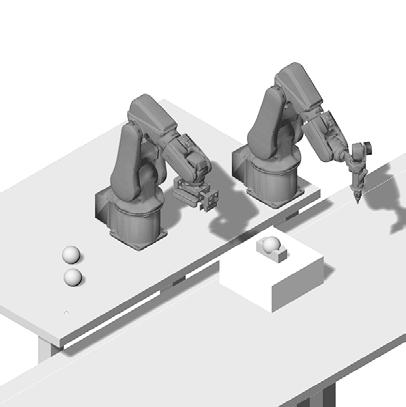
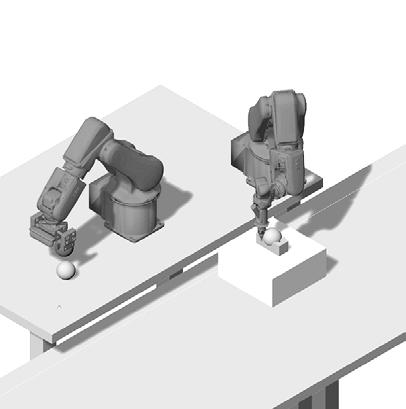
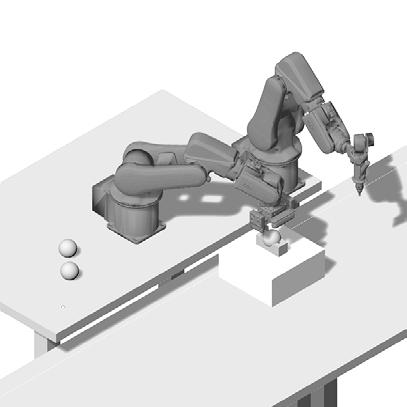

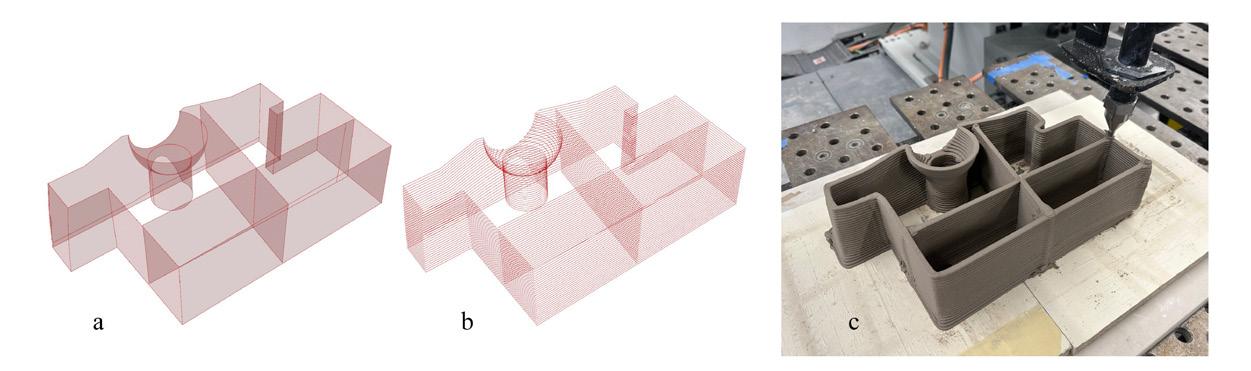
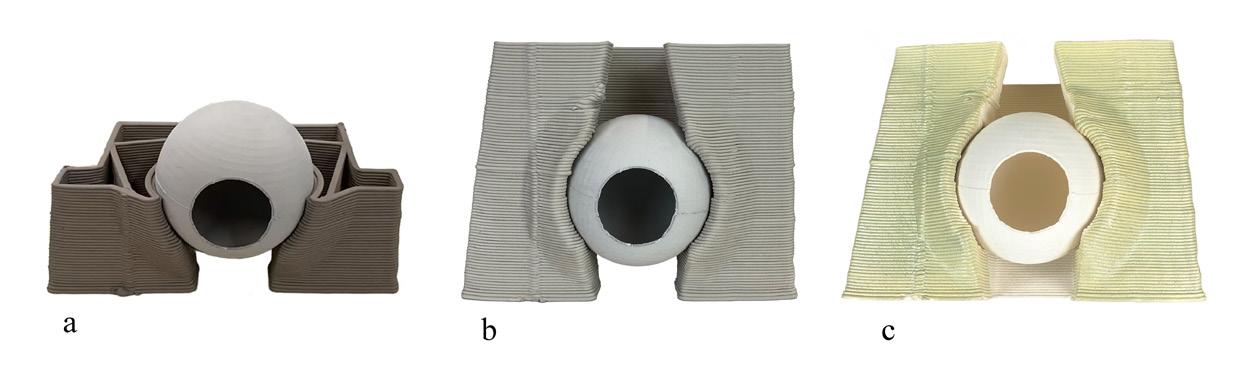
The right image shows one of 12 glazed 3D printed pieces from the final prototype in different phases (a: wet clay, b: boned dry clay, c: bisque fired clay) which embedded a boned dry 150mm diameter slip-cast sphere. This piece demonstrates the shrinkage rate between clay 3D printing and slip-cast which has no gap in between during the printing and has a 1 mm gap after shrinkage.
Prototype Production
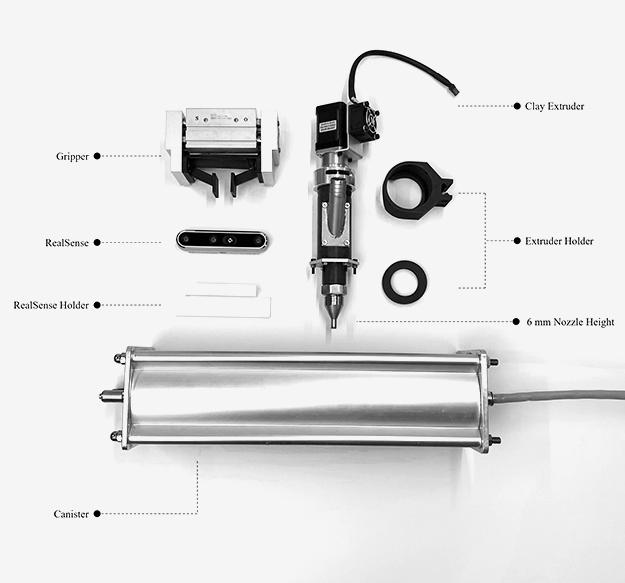
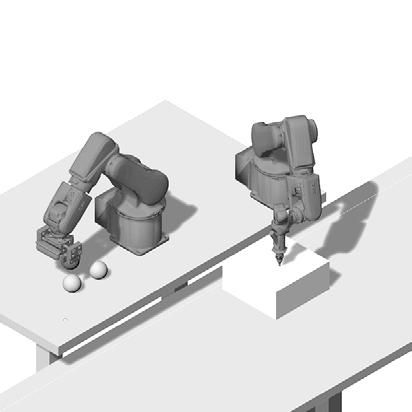

Fabrication Workflow
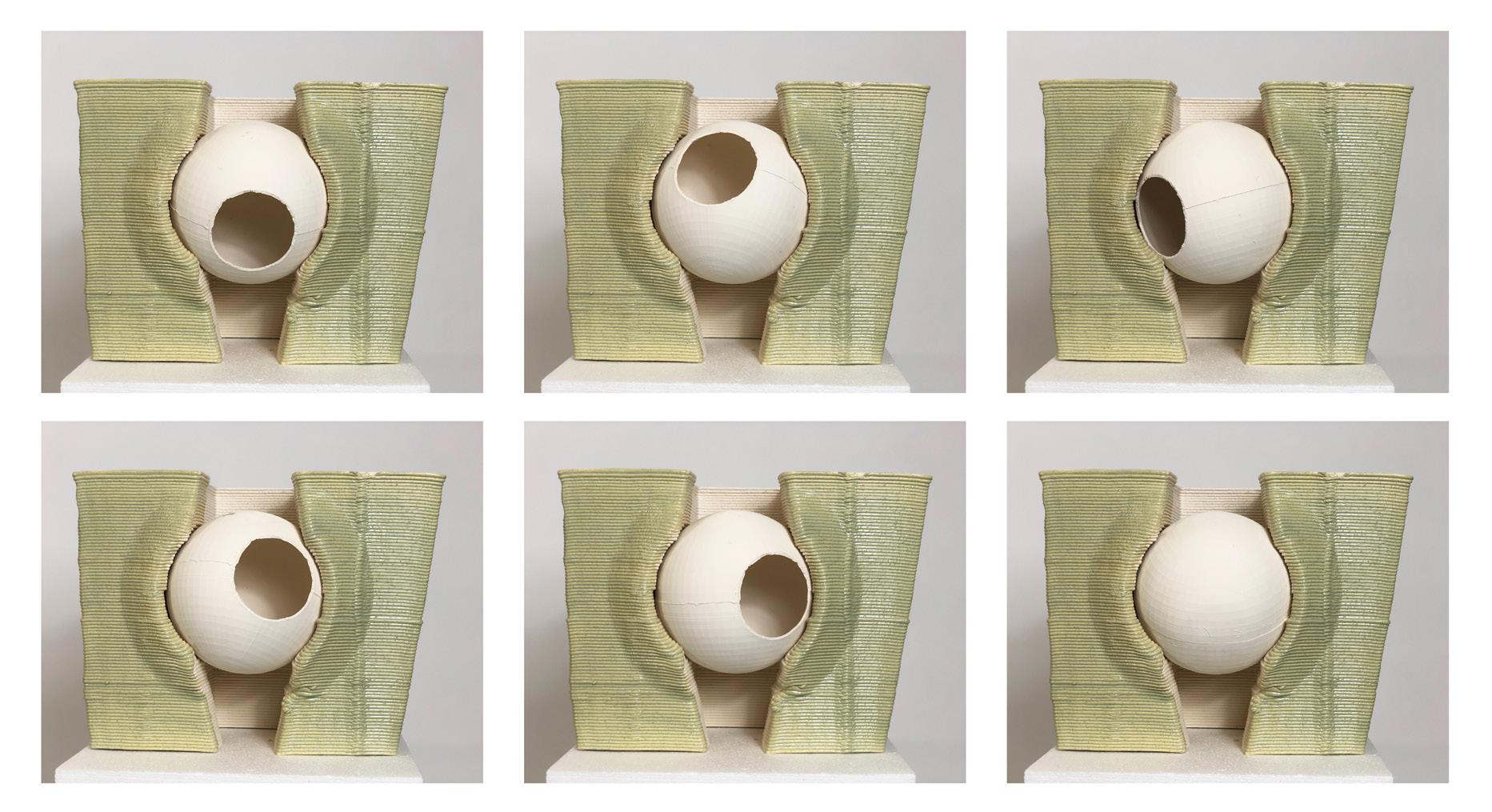

Two Robot Arms Collaboration to create one piece

Half-scale Prototype
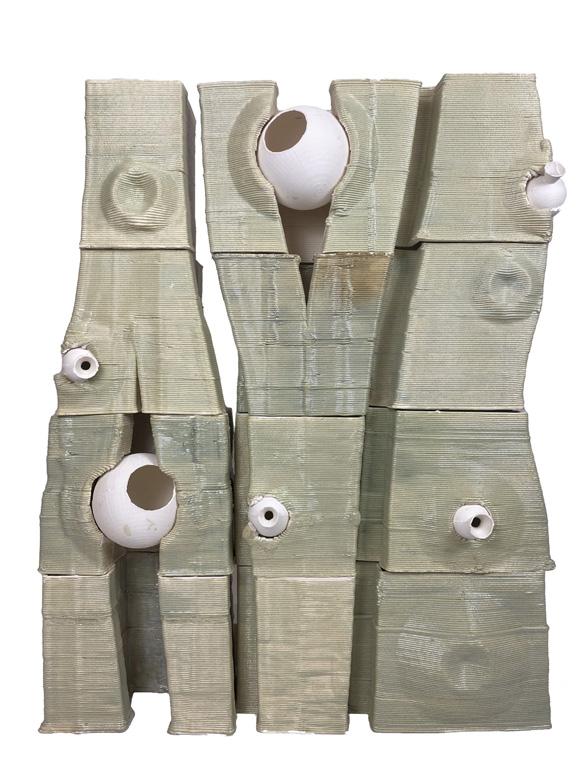
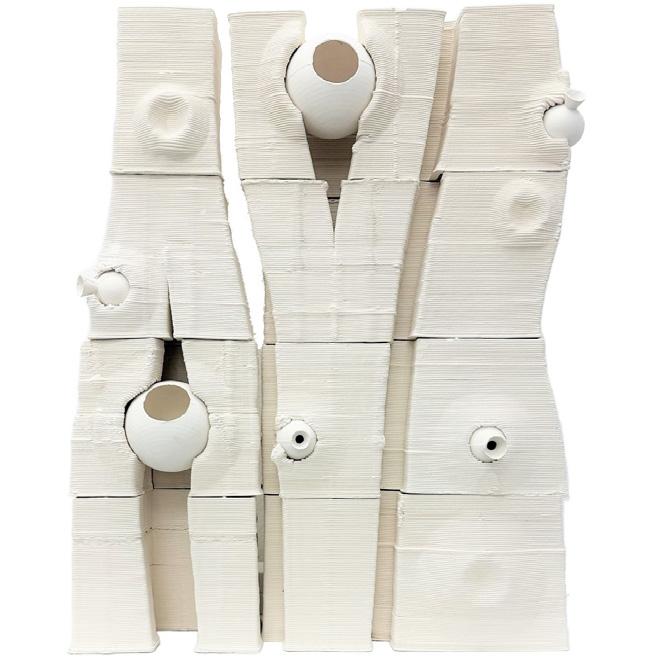


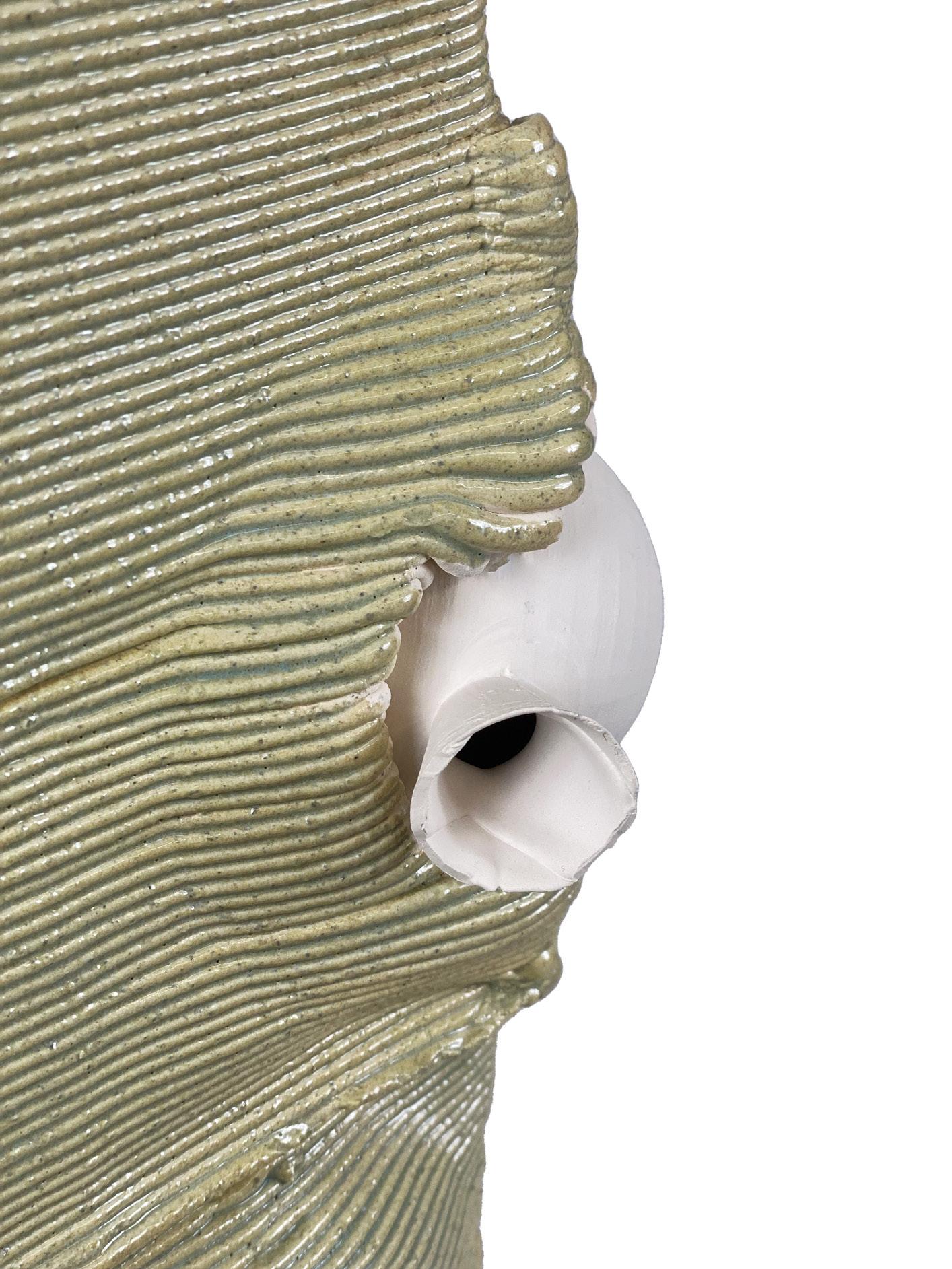
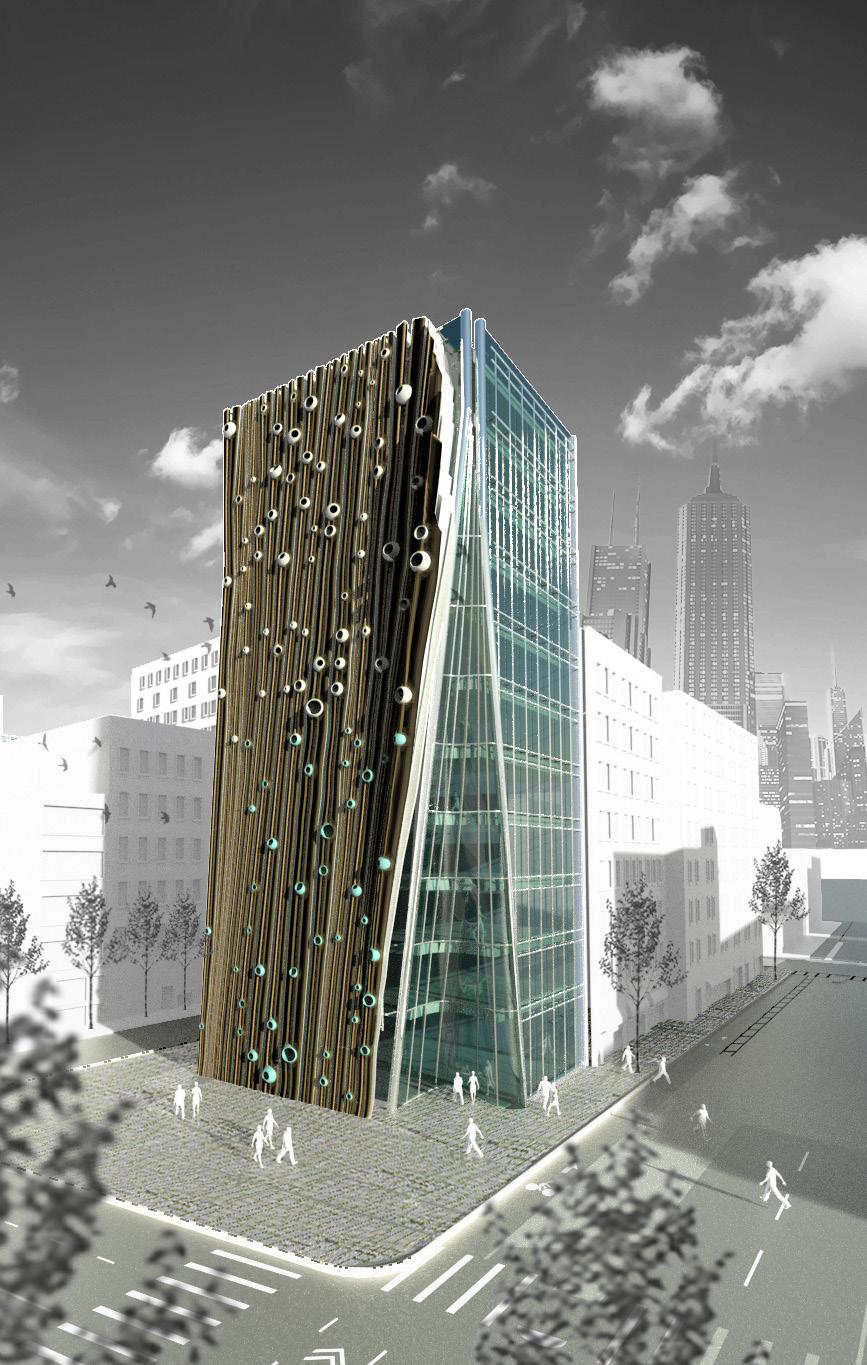