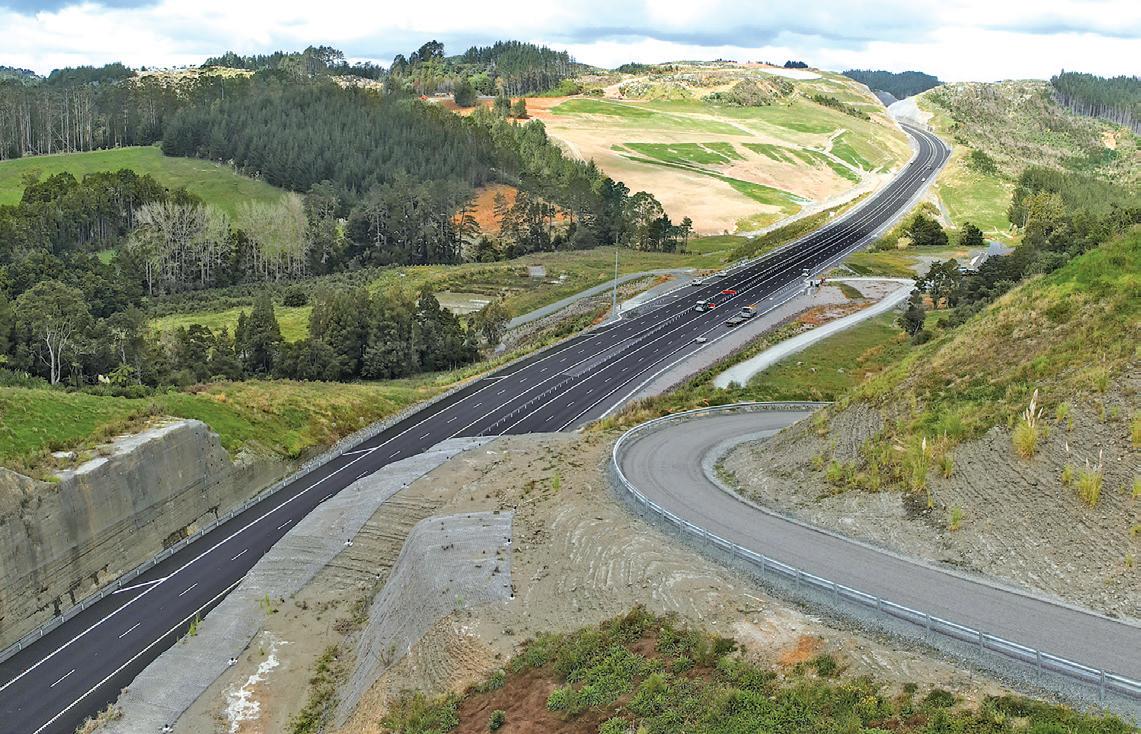
3 minute read
Award winning erosion control feature of motorway design
By Allan Barber allen@barberstrategic.co.nz
Environmental management has been an integral part of the Ara Tūhono – Pūhoi to Warkworth motorway project from the start.
Advertisement
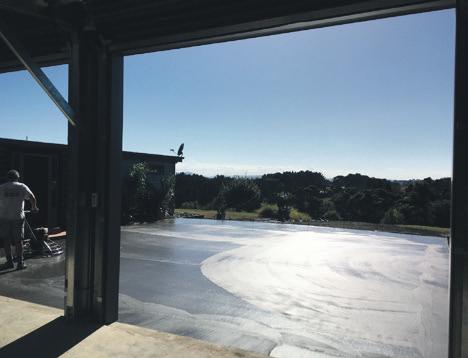
The 18.5km route over steep hills and flat country, much of it unstable, is estimated to have produced up to 10 million cubic metres* of cut material including rock and soil, which was moved by a combination of blasting and earthmoving equipment.
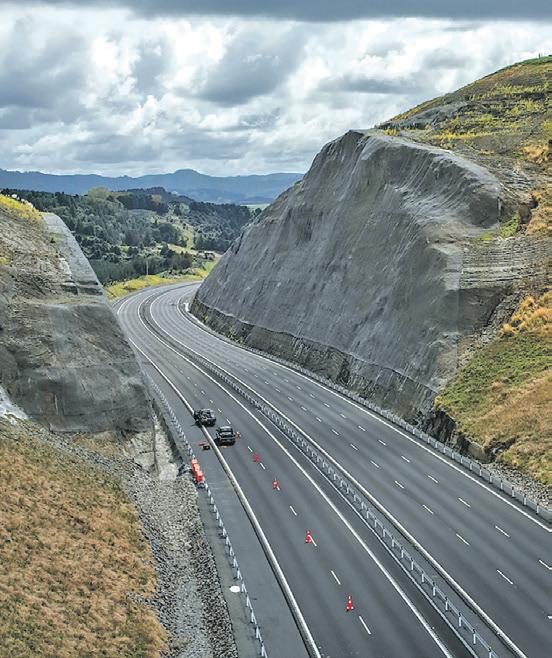
Much of this material was reused to fill valleys and create the road alignment and modified landscape now visible.
Environmental manager Karsten Stevenson was involved from the beginning and saw it as essential to build a team with specialist expertise and experience in erosion and sediment control, who would be able to communicate with the motorway construction engineers, supervisors and operators.
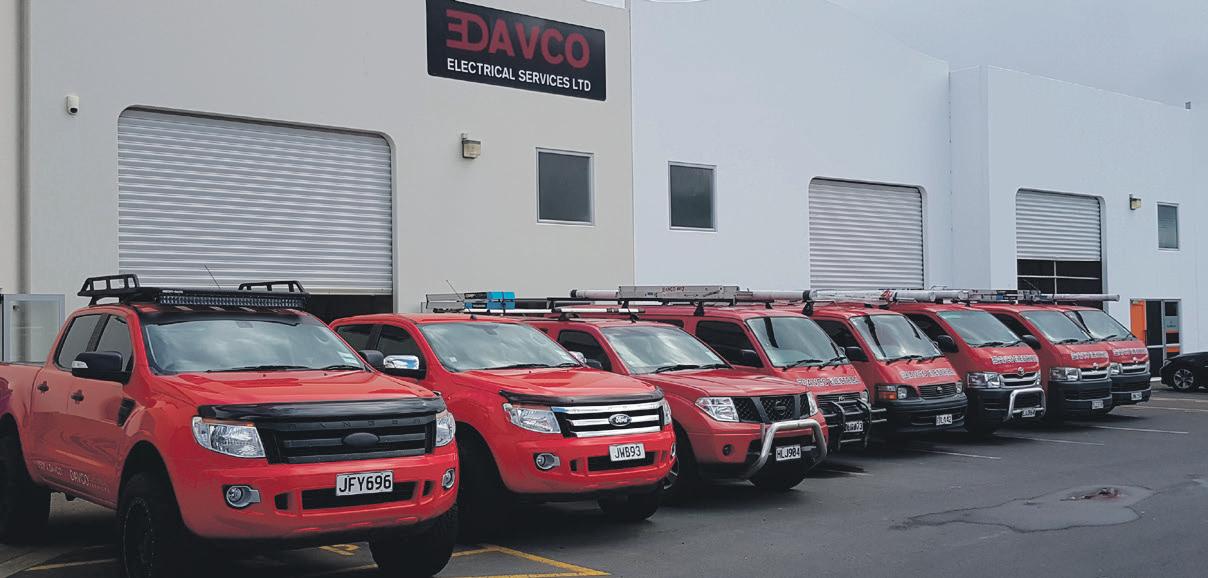
At the peak of the project, the team comprised the manager and four team members who developed and designed all the erosion and sediment control plans inhouse.
The plans had to be designed to cope with the constant threat of both engineered and natural soil movements. These were addressed by using an adaptive management approach, which involved taking water samples before, during and after each rain event to check the sediment concentration in the water being discharged from the work site. Regular tweaks to the methodology were made on the basis of these results. There is a big difference between sediment runoff during construction, which was managed by chemically treated sediment retention ponds, and the runoff from the completed motorway, which is passed through planted wetland ponds before being discharged offsite.
One particular innovation was that the sediment retention ponds were built to have double the chemical treatment capacity so they could handle major storm events, as mandated by the resource consent conditions.

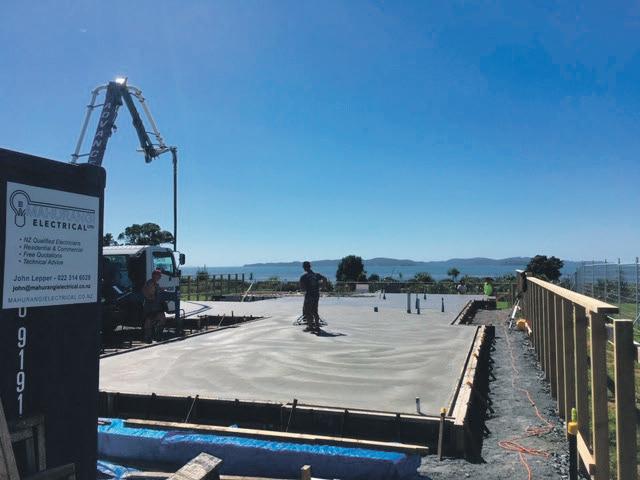
This environmental programme design won the International Erosion Control Association of Australasia Award in 2021. The team was asked to make a presentation by Zoom to the global IECA Conference in the United States, which was a great accolade for the team’s work on very challenging terrain.
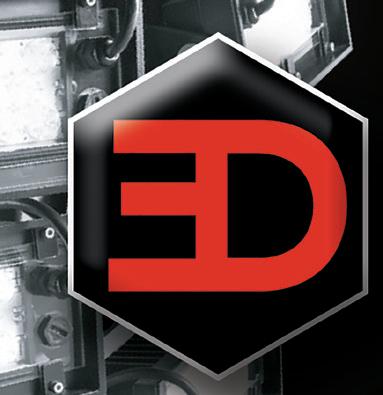
The team has also spent a lot of time testing the quality of the imported and in-situ topsoil to ensure the best landscape and planting outcomes. About 12ha of native vegetation was removed to make way for the new motorway, but to compensate, more than 150ha of native vegetation has been planted. This planting was undertaken in two stages with stage one plants providing a nursery for the stage two canopy species. The intention is that ultimately, this will replicate the natural forest ecosystems.
* If 10 million cubic metres of soil and rock were spread evenly over a flat area, it would cover about 200 hectares (equivalent to about 285 rugby fields).
Big sucker keeps crews safe
Wellsford-based company Wharehine has taken delivery of its first Smart Dig hydroexcavator and vacuum truck, manufactured by Warkworth-based ITSS Engineering. At the recent handover, Wharehine managing director Rob Gibson welcomed the new machine, which he says takes the guess work out of where services such as power, gas, telephone and fibre optic cables, are located. He says there are so many services underground that it can be a “real nightmare” for contractors. The new trenchless excavator will ensure our teams remain safe, provide certainty and protection of clients’ assets, and ensure minimal disruption to road users.
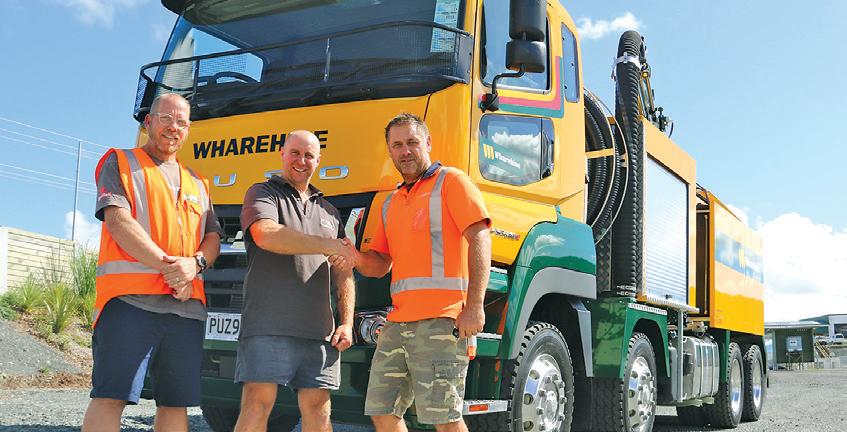
“Also, having our own unit based in Rodney will mean we’ll be able to quickly respond to any emergency clean-up events on the state highways, helping to get the road open as quickly as possible,” Gibson says. The hydro excavator uses high pressure water to excavate around or locate services, then a vacuum removes the spoil created in the process and transports this offsite to be recycled.

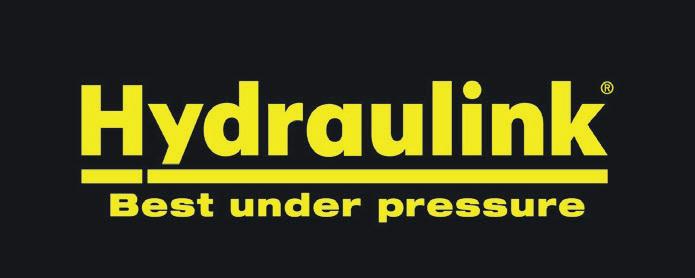
“We investigated several different build options from United States, Australia and around NZ, but in the end it was an easy decision to go with the Smart-Dig unit.
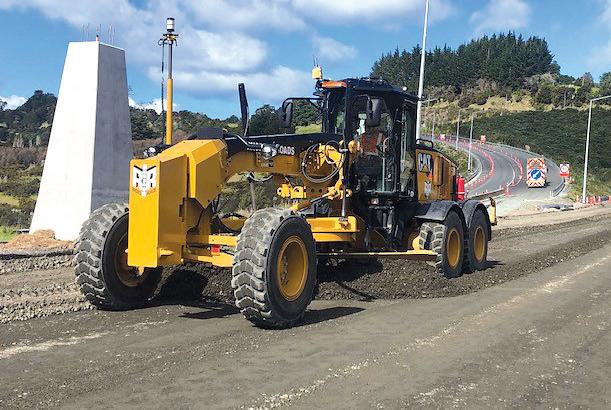
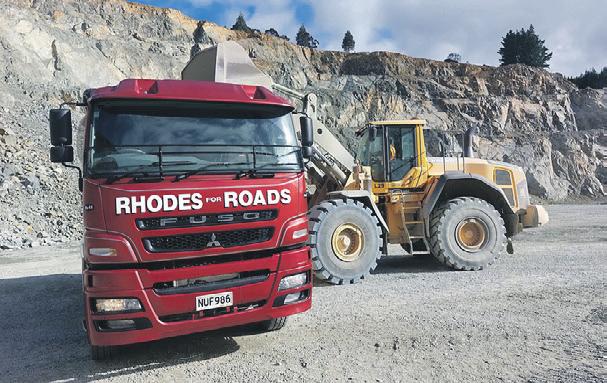
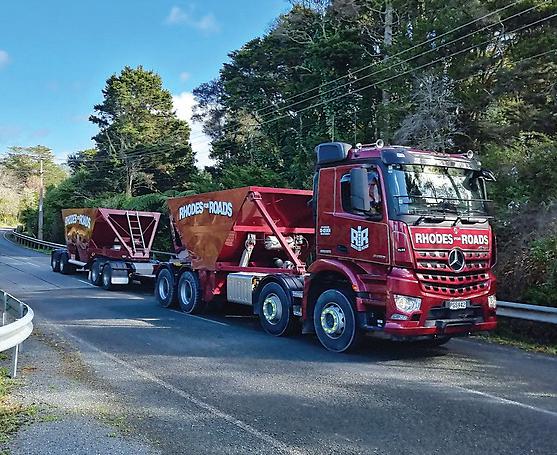
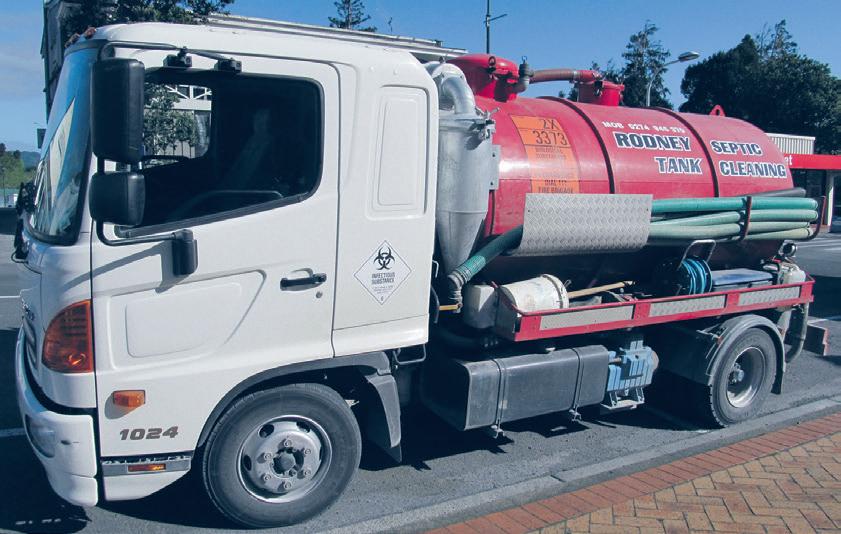
“To begin with, it is locally made and supported, and built for our environment and conditions.
“The machine has a well thought out design, large capacity and extra added features not on other international units.
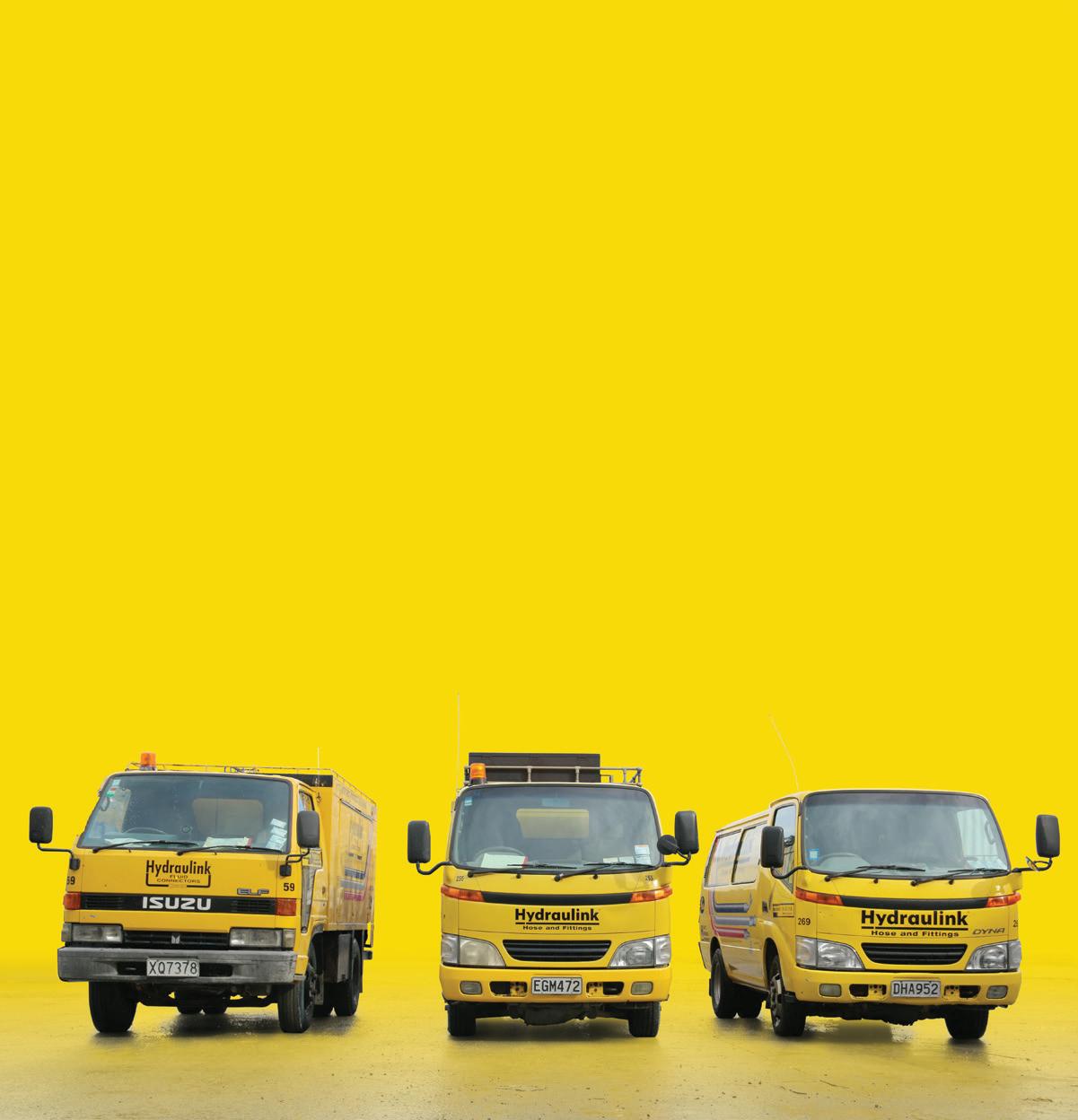
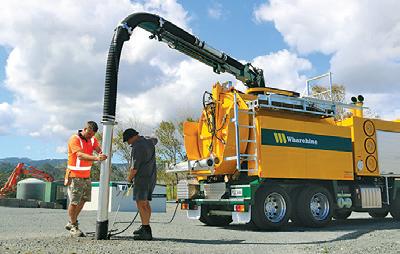
“Being locally made from a 100 per cent NZ owned company was a massive plus for us, ensuring the dollars spent stayed in the local community and NZ.”
Smart-Dig is a partnership company between Rob Southey (Southeys Group) and Hugh Harvey (ITSS Engineering) and has been operating for 10 years.
ITSS’s workshop produces 90 per cent of the unit, with the rest being made or imported through other New Zealand companies. ITSS Engineering has a production line currently capable of building 12 to 15 units a year.
Our fleet includes excavators of varying sizes, bulldozers, graders, loaders and compacting rollers and our team of highly trained truck drivers and machine operators have been digging, levelling, land sculpting, moving dirt, rocks, rubble and spoil for years. We provide professional excavation, delivery and removal services to residential and commercial clients for earthworks projects such as driveways, house and shed sites, retaining walls, subdivisions, carparks and pavement rehabilitation and land sculpting.
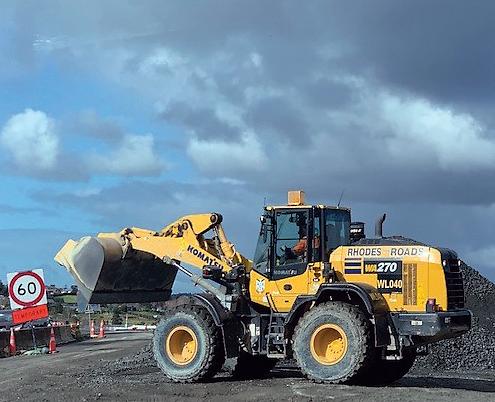