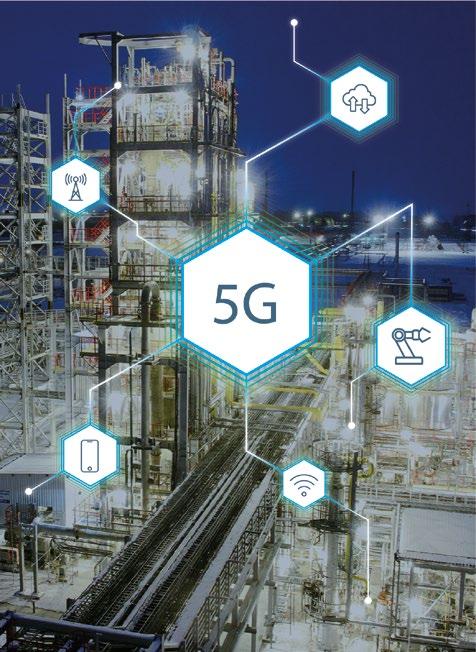
6 minute read
NextPlant: our way to Digital Transformation
by MAIRE
To help its EPC clients succeed in their digital transformation, Maire Tecnimont has launched its NextPlant platform, a portfolio of digital solutions and services that, becoming a source of differentiation and competitive advantage, creates cost-competitive EPC processes and unlock value for plant owners.
The Group’s digital transformation program has two main areas. The first is the digitalization of our own core processes in several different ways: by using digital enablers to increase competitiveness by reducing costs for Maire Tecnimont Group companies and for their customers, and by speeding up the bidding process and project execution.
Advertisement
Digitalization of our own core processes enabled us to guarantee business continuity during the pandemic. During the spring of 2020, meetings on the Group's collaboration platform (Teams) increased from a few hundred to over 3,000 events per day.
The second main element is to create a digital advantage as an EPC contractor by incorporating digital services for new and existing clients by improving plant productivity, by reducing operating costs and by increasing plant sustainability. We are identifying new value based on technologyenabled offerings; improving customer experience and therefore our business proposition; deploying opportunities to enhance the generation of In-Country Value (ICV) in the regions where we do business.
The portfolio as a whole contributes to reduce the Total Cost of Plant Ownership (TCO) that we can offer our clients. Our progress has allowed us to better manage our EPC work sequences, leading to improved control of project execution in time and quality, and also greater control of HSE aspects during construction. At the same time, by developing an ecosystem of qualified partners, Maire Tecnimont is expanding its digital portfolio (NextPlant) to include products and services that can reduce the operating costs of industrial plants, helping to increase their sustainability by lowering CO2 emissions (for example by using process optimizers), reducing the risk of accidents affecting people and the environment through predictive maintenance, facilitating the transfer of skills and creating new job opportunities (such as advanced training systems).
SUSTAINABLE DIGITAL TRANSFORMATION
Digital transformation plays an important role in all sustainability issues. On the one hand, it dematerializes the physical concept of the workplace in favour of remote working, while on the other, it makes information and data fully transparent and accessible, eliminating role and generation gaps as well as gender and disability gaps.
Our digital transformation is therefore intertwined with our sustainability strategies. Three quarters of our digital solutions support transparency and inclusiveness. Seventy percent of these solutions support good HSE practices and C02 reduction. And 25% support knowledge and skills transfer in the countries where we do business.
The Covid-19 pandemic made us experience major changes in many of the basic aspects of our working environment: our concept of the workplace, the way we relate to each other and our colleagues’ work-life balance. Remote working for office staff is just part of this shift. By dematerializing work processes, remote digital solutions also significantly reduce the environmental impact of the Maire Tecnimont Group's activities and of the operational plants.
Digital transformation also encourages the transfer of know-how to local workers in the countries hosting our projects; for example, remote collaboration tools
facilitate on-the-job training throughout the various stages of project development.
Digital solutions increase worker safety during plant construction and commissioning stages, as potentially dangerous inspections can be carried out remotely, and they allow for a better analysis of “congested” work areas. Concerning the enviromental impact, the reduction of 2% of steam and of 0.5% of electricity yearly consumed by a medium-sized fertilizer plant (1,500 MTPD) leads to avoiding emission of around 1,600 tonnes of CO2 per year. We can pursue this target using the new generation of process optimizers, which are under development for all the licensing companies in the Maire Tecnimont Group.
CYBERSECURITY
As part of the acceleration of the digitalization process in 2020, we maintained the highest standards of IT security as an essential and integral part of our development model. As a result, no security vulnerabilities were found in the system. In 2020, the Maire Tecnimont Group obtained ISO:27001 certification for the management of corporate information. As an EPC contractor with half a century of industrial experience, Maire Tecnimont has the know-how to design industrial plants with a “security design driven” approach. A deep understanding and long experience with plant design, construction and operational management allows Maire Tecnimont to take a holistic approach to cybersecurity over the full life of the plant with an end-to-end approach.
FEASIBILITY FEED
DIGITAL SUITE FOR EPC
Optimized tendering & estimating
Fully collaborative advanced engineering Optimized sourcing & supply chain orchestration
Digital construction suite
ENGINEERING PROCUREMENT CONSTRUCTION & COMMISSIONING
Advanced E-P-C planning & monitoring +
E2E document & deliverable management
E2E material management
OPERATIONS
Digital Suite for Operation & Maintenance
DIGITAL SUITE FOR O&M NEXTPLANT OUR DIGITAL COMPREHENSIVE SUITE IS DEVELOPED TO PROACTIVELY MEET CLIENTS NEEDS
ADT Asset Digital Twin & 3D based CMMS
POE Process Optimization Engine
PMS A.I. based Predictive Maintenance
OTS + VR Operator Training Simulator w. virtual reality
HSSE Geo-tracking of personnel
DFF + AR Digital Field Force w. augmented reality
OUR DIGITAL SOLUTIONS ENHANCE EPC EXECUTION EFFICIENCY AND UNLOCK VALUE FOR PLANT OWNERS
Increase E ectiveness & E ciency of EPC processes Mitigate Risks Improve Plant Operational E ciency
Reduce Plant Carbon Footprint
Digitalization delivers a reduction of operational expenditure and increases the plants’ productivity, reliability and maintainability by gathering and elaborating data through Artificial Intelligence and Machine Learning techniques.
The Asset Digital Twin (ADT) is the core of digitalization. It consists of a 3D model as a single repository of asset information, based on CHFIOS standard, starting with the technical documents produced during EPC phases. The ADT grows along with the plant lifecycle, to include maintenance plans developed by vendors, and is continuously updated with maintenance and inspection reports, becoming a fundamental backbone for future solutions for plant and people productivity, and connected field operations.
Process Optimization Engine: by capturing process data from plant operations in a digital replica of plant processes that use thermodynamic/kinetic equations up to statistical correlations, plants can run at the nearest possible level of optimum design, in a safe and efficient manner. This cuts energy consumption, thereby reducing a plant’s carbon footprint.
Prescriptive and Predictive Maintenance Suite:
traditional maintenance suites are improved by merging a prescriptive maintenance database with a 3D model of the plant. Moreover, statistical and machine learning algorithms are used to identify abnormal operating conditions and predict failures in advance. This reduces OPEX by reducing unplanned maintenance and unexpected shutdowns.
Operator Training Simulators (OTS) combined with
Virtual Reality (VR) environment: the virtual simulation scenario allows for safe tests for any potentially dangerous plant conditions, without creating any real risk for human beings and the environment. Plant operators are trained in advance using these tools ahead of start-up, maximizing effectiveness from the very first months of plant operation. Connected field operations: a digital HSSE platform connects operators via smart devices so they can be monitored remotely to avoid potential harm to themselves or the environment. In a fully connected plant, a Digital Field Force has data at its fingertips through mobile applications linked to a central repository and experts. Remote assistance can be provided in real time while limiting the circulation of experts across geographical regions. This approach saves money and also reduces injury risk. The backbone to unlock any digital field service is the plant connectivity characterized by a very wide band and very low latency time. Therefore, new communications paradigms (like 5G technology) are crucial within the plant.
Being a technology-driven contractor makes Maire Tecnimont the single orchestrator of the EPC value chain to envision a digital plant that will meet plant owner business needs to generate significant positive impacts on plant capex and opex. We are industrializing cutting-edge technological concepts like wireless plant based on 5G, block chain application to industrial complex, etc. thus to create a “NEW INDUSTRY STATE OF THE ART”.
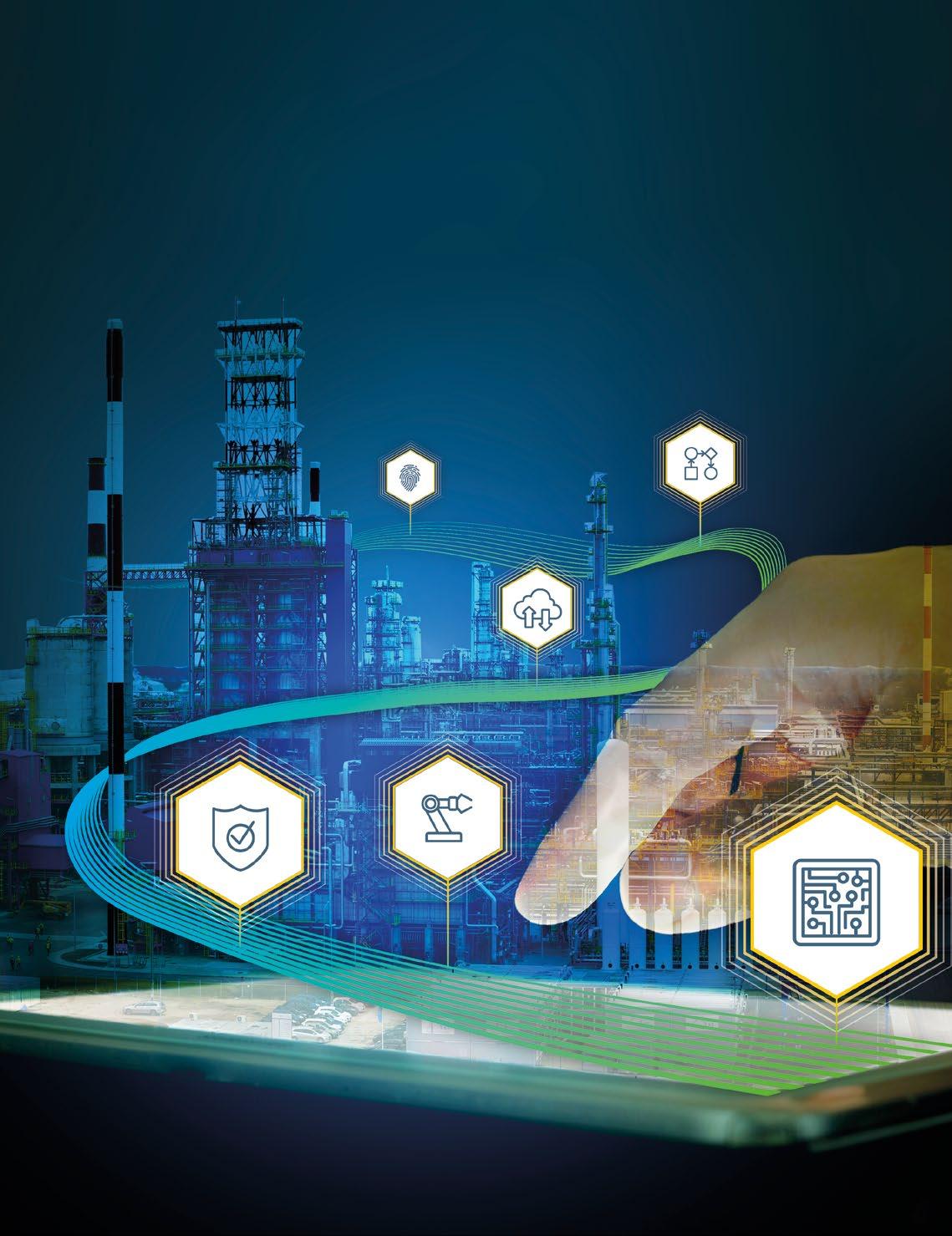
Maire Tecnimont Group Operative Headquarters
Via Gaetano de Castillia, 6A 20124 Milan, Italy P +39 02 63131 info@mairetecnimont.it