
7 minute read
Summary
In times of great fear and uncertainties, we tend to use familiar and easy solutions for our problems.
In the case of the COVID-19 pandemic, a lot of people and companies use plastics to make protection gear; like cashier protection screens and faceguards. Typically, these protection items are made out of Polymethyl methacrylate (PMMA). PMMA is a rigid and transparant plastic. The downside is that PMMA is environmental unfriendly. This is due to complex production processes and long supply chains. When we are done with these products, we can recycle them. The downside however is that it costs a lot of energy. ¹ Additionally, it is almost impossible to make such items by yourself at home. Here comes my project in place; I want to show that anybody can fabricate appropriate and safe protection gear with everyday ingredients. To do so, I use bioplastic made from gelatin. It only takes 3 ingredients to become a maker of your own bioplastic faceguard. Bioplastic is great, because it is environmental friendly, and you can recycle it at home.
Advertisement
Faceguards are a good addition to the regular face masks, because it protects the eyes and it will prevent you from scratching/touching your face. In this way infection is prevented.² When we don’t need our faceguards anymore, they can be recycled easily at home.
Why would we seek for the best care for ourselves, but not the planet? Let's change that.
¹ Heathland.com, PMMA – Polymethyl methacrylate recycling ² AARP.org - Some Experts Say Face Shields Better Than Masks for Coronavirus Protection
Larger context
When I started with my project, I wanted to design a corona solution for a specific target group that I have a close connection with: elderly people. I worked for a house nursing company and in addition to that I worked as a taxi driver for elderly and physically impaired Amsterdammers. I am still in touch with some of my former clients and passengers. To see how they are affected by the pandemic touched me, and I felt like I could really help them with my project.
When I spoke to them, they told me they are affraid to go to the supermarket, and to take a taxi. Because they have a low mobility, they are dependent on transportation. When I heard this, I brainstormed and came with an idea to make protection screens for in cars. In this way, the passenger is protected from corona virus particles in the car. I started to sketch and design my protection screen and made some mockups.
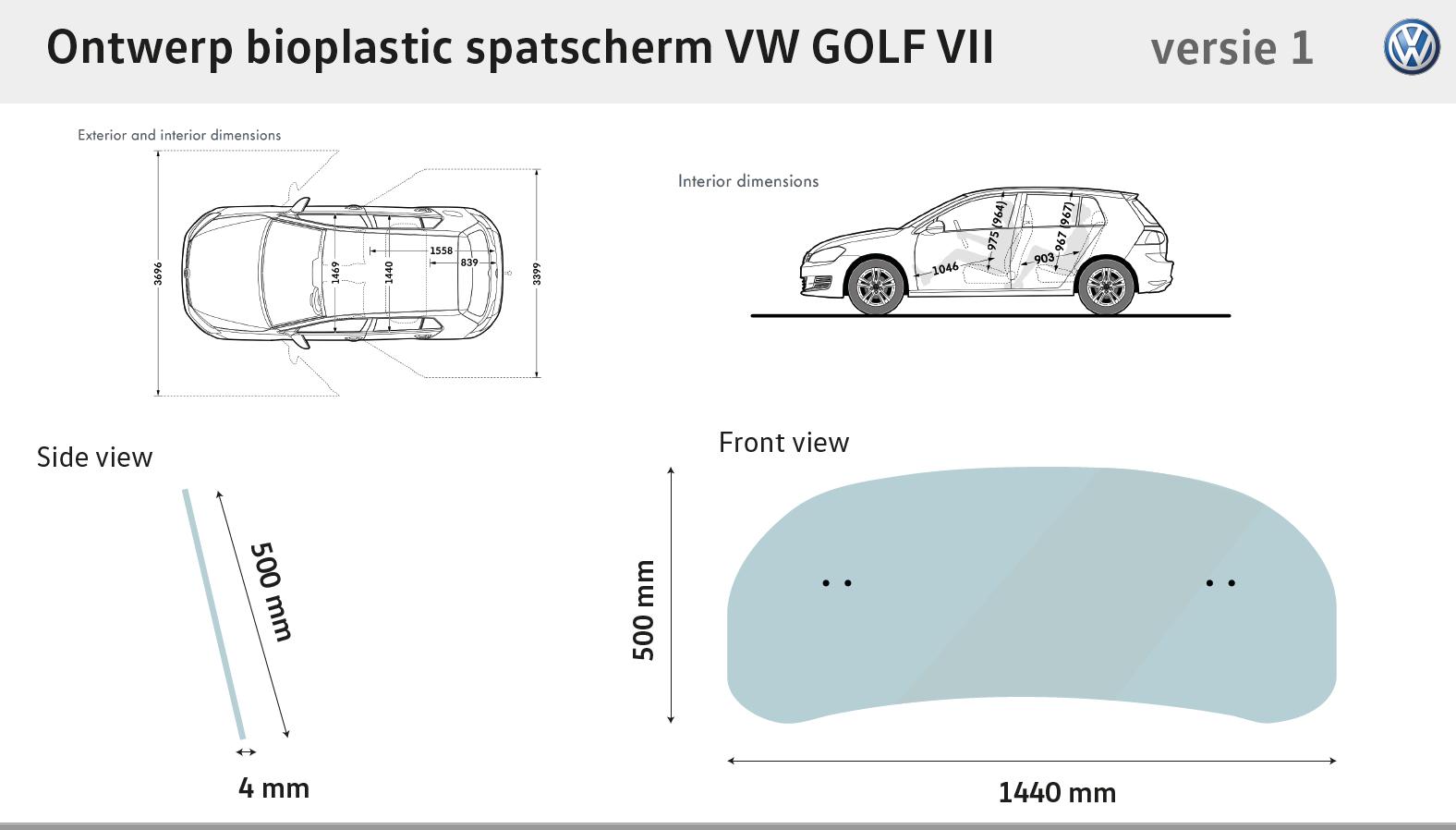
At that moment I was ready to buy my ingredients to fabricate
protection screens. I wanted to use bioplastic to create them,
because it’s bio degradable. You can reuse it, or discard it by
boiling it down with salt and flushing it down the toilet.
Then came to problematic part. To cast my screen, I wanted to
pour my bioplastic mixture on top of a Polymethyl methacrylate ( PMMA) plate that is large enough for my design.
PMMA is suitable for this purpose, because it is heat resistant
and the bioplastic can be easily removed. However though,
everywhere I looked PMMA plates were sold out. When I started to
look further for other plastic based casting surfaces, I was
shocked to discover that almost every plastic plate material was
sold out at every building market and webshop.
A lot of companies and shops use these plastic plates to make
protection gear for their own. It was so massively wanted that it is
almost impossible to get your hands to it. The issue here is the moment when we don’t need those plates
anymore. When the corona crisis is over, the protection gear that
everyone has made is obsolete and will be discarded. PMMA and
other plastics require a long production chain and transport
before they land in the shops. And when we are done with them, it
takes a lot of energy to recycle it. ¹
To put this in another perspective : when we are under attack
from a pandemic, we react by using even more harmful
solutions to tackle the problem. In fact we are digging another
hole for ourselves.
These findings drove me to the conclusion that I still want to make
protection gear made of bioplastic, but I want to reach the mass
and make an easy DIY faceguard that everybody can make. In this
way I hope that we look further than the panic instinct that we all
followed, and be more cautious when we are trying to defend
ourselves.
Summary of project and outcomes
Now that I’ve got a new point of view for my project, I started to
sketch once again. The reason why I’m making a faceguard is
because they are a great addition to the self made facemasks that
everybody is making right now. Facemasks cover your mouth and
nose, but it leaves the rest of your face and eyes vulnerable for
infection by the corona virus.
By using a faceguard you will protect your eyes and face. Because
you have to guard in front of your face, you cannot accidently
touch or scratch yourself. This will minimalize the possibility of
infection. ¹
I was looking up designs on the internet. I came across a lot of
good ideas, and finally I chose an ecliptic shape. This is easier to
shape around the face. I made a template so I can follow the
design when casting my faceguard.
Faceguard template
Width : 220 mm Height : 290 mm
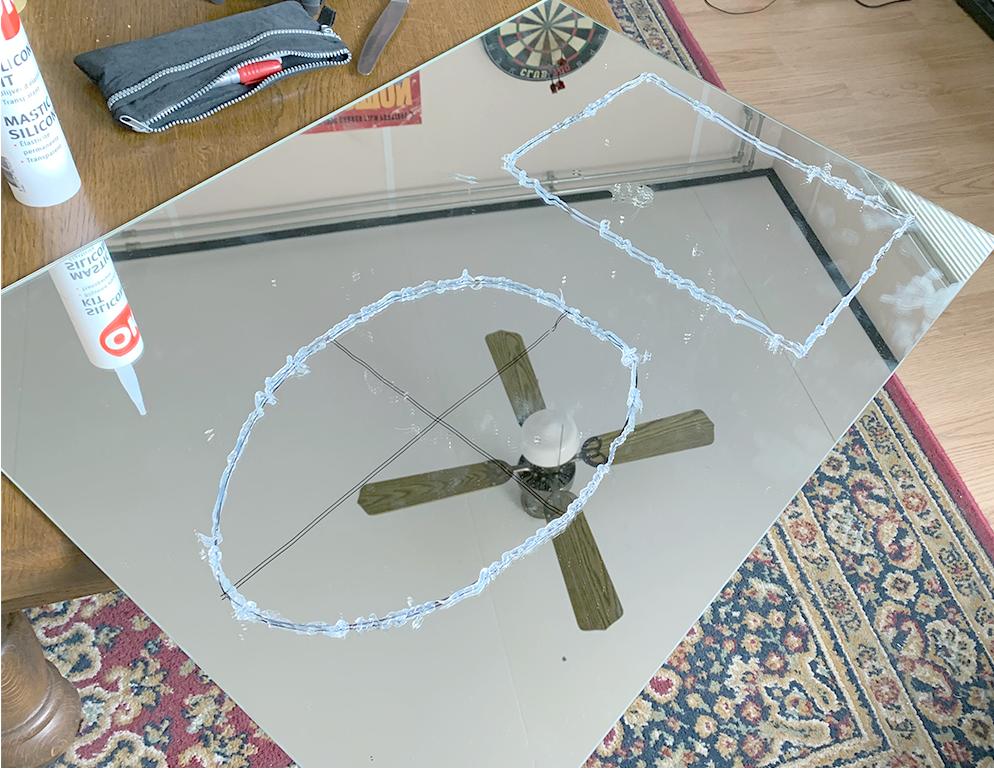
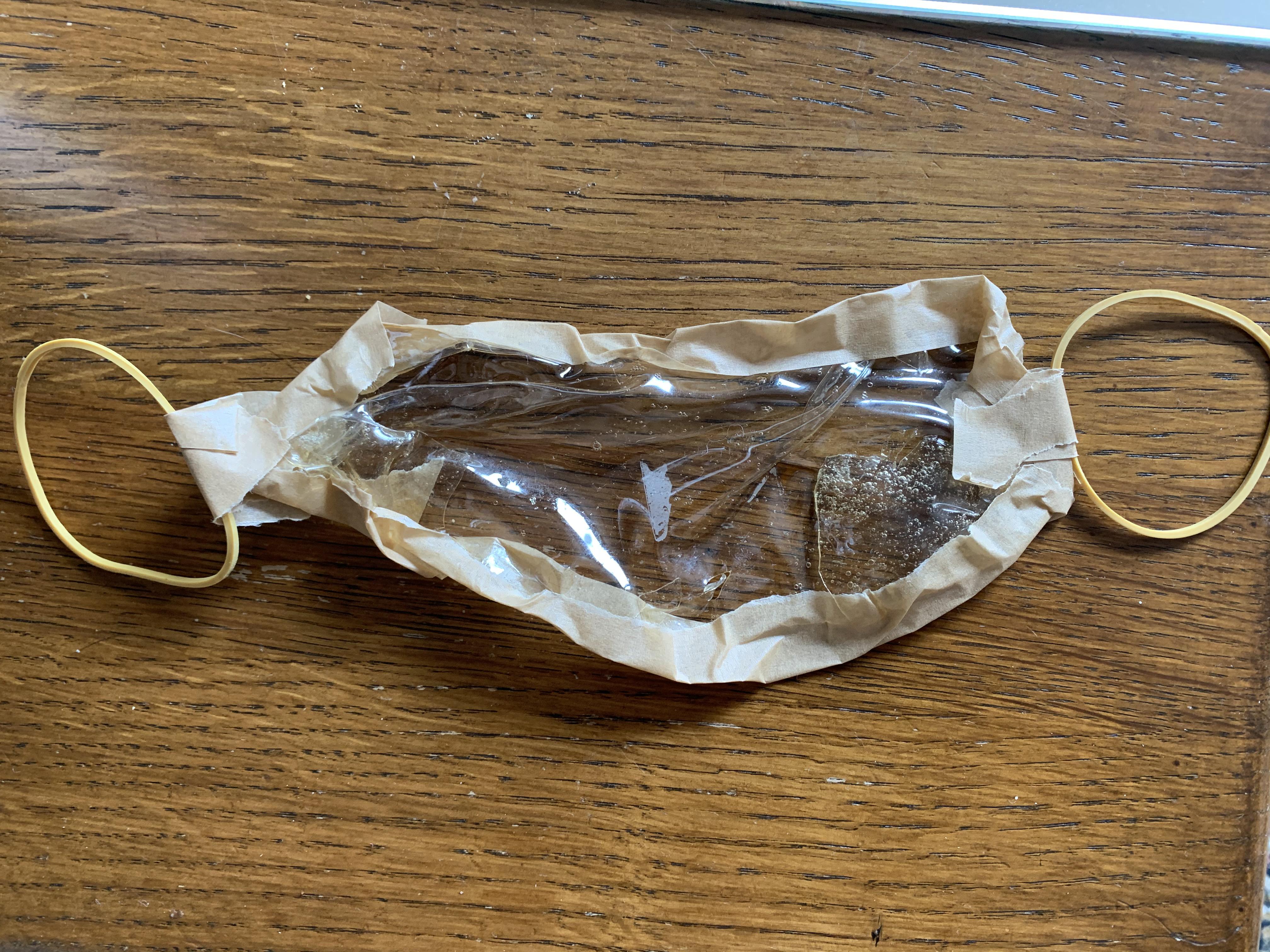
To cast my bioplastic faceguard, I need a surface to pour my
bioplastic mixture on. Because ofcourse the PMMA plates are
unavailable, I used a 70 x 50 cm mirror. To draw my template I
used silicon kit. First, I drew the template with a sharpie on the
mirror. Then I filled in the lines with the silicon kit. This will
act as the mould for my faceguard.
While I let the silicon kit dry on the mirror, I proceeded to cook the
bioplastic. I use gelatin for my bioplastic, because it will create a
rigid and transparent plastic. Glycerin is also added in the recipe
because it will make the plastic flexible. The first time when I
made a large batch of gelatin bioplastic I added too much glycerin.
This resultated in a sticky and sloppy plastic that I couldn’t really
use for my faceguard. I decided to make a facemask out of it to
test if it was suitable. Unfortunately, it will become moist when it’s
placed on the mouth, and cannot be used as facemask.
For my second try, I got the ingredients right.
I used the Bioplastic Cookbook gelatin recipe by Margaret Dunne.
After I cooked the bioplastic, I left it to dry for 2 days. When I
removed the plastic from the mirror it was perfectly rigid and
transparent.
I have the bioplastic screen right now, but I still have to make a
strap or attachment so you can wear it. To do so, I cutted the strap

of an old cap I had laying around. You can use whatever piece of
strap or band you have available. I made 5 incisisions in the upper
part of the bioplastic screen. I laced the strap through the holes I
made and the mask was ready to use!
The material is transparent and does not smell. Because you wear
the mask in an angle, it will not touch your mouth and nose.
Because of this it will not get moist. You can easily wash it with a
cloth dripped in alcohol. Just make sure that you don’t use a
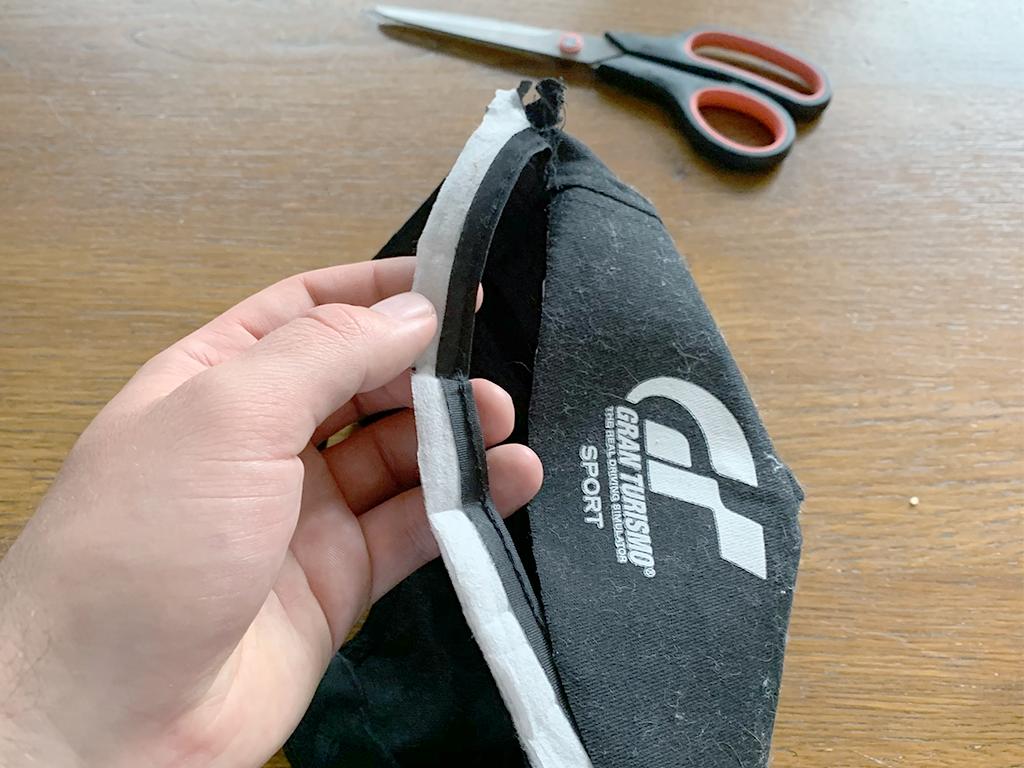
drenched cloth, because otherwise you can damage the bioplastic.
I will also suggest to not wear it in moist places or in the rain,
because the plastic can break down.
I tested the mask on my girlfriend and a bunch of friends. They
were all quite pleased with the end result, and couldn’t believe
how easy it was to make. They also said that they didn’t expect the
material to be so strong and rigid. It’s also important that they

valued the aesthetic aspect of the product.
When you want to recycle the faceguard, you can cook it in a pan.
It will melt and can be casted again. This is important because my
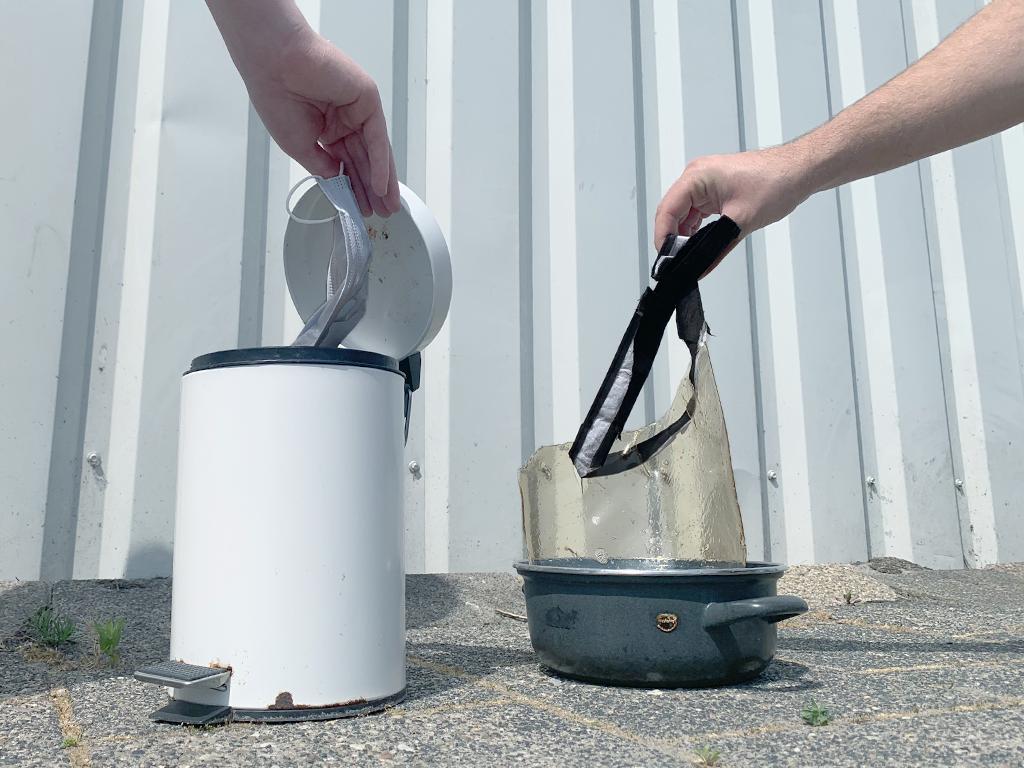
goal is to create a durable product.
Pictures: recycling, mirror and faceguard, faceguard profile - Thijs Uffen
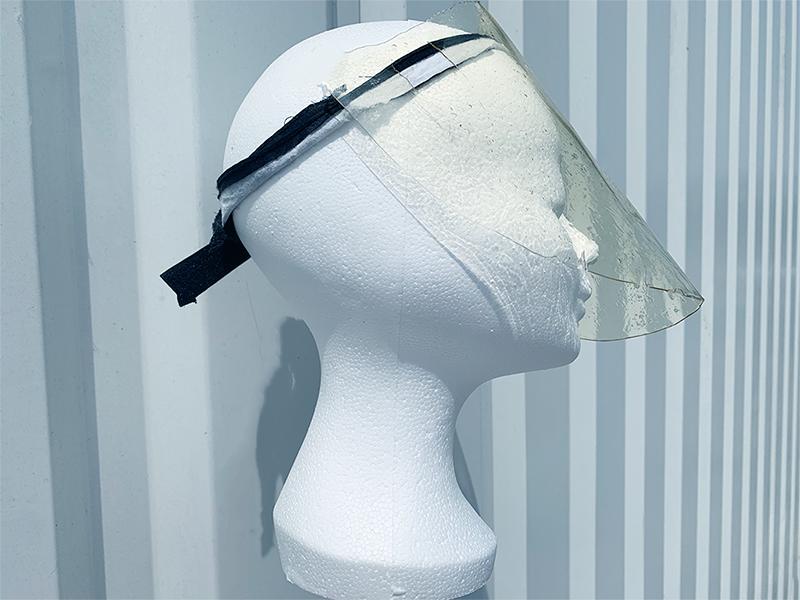
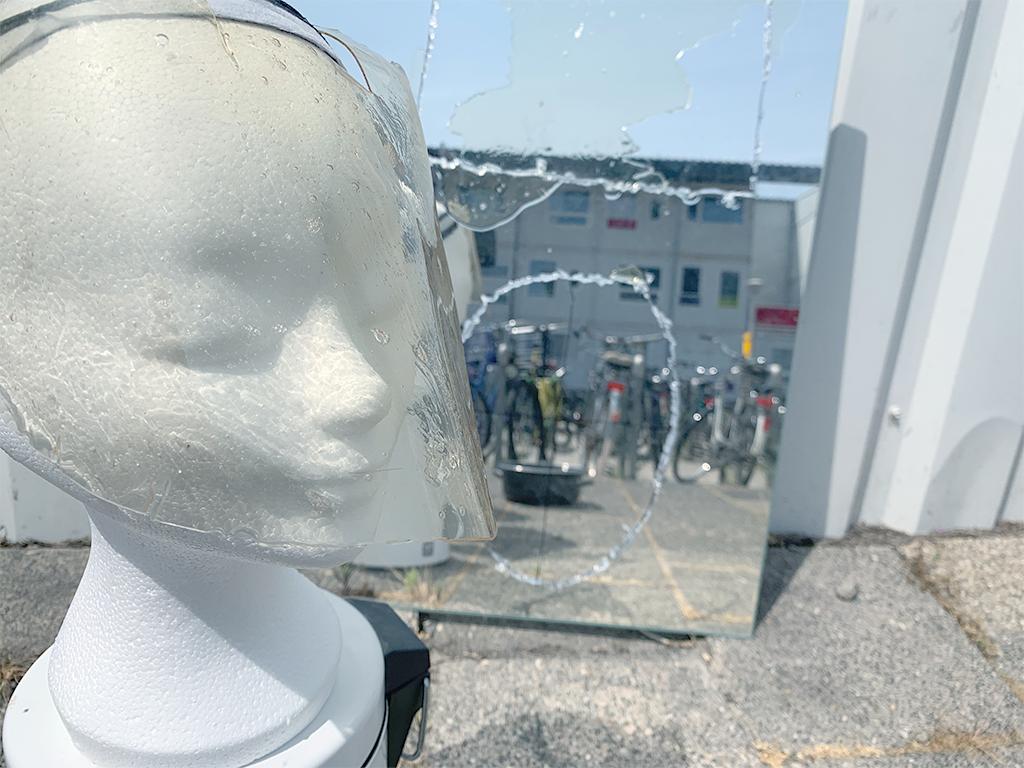