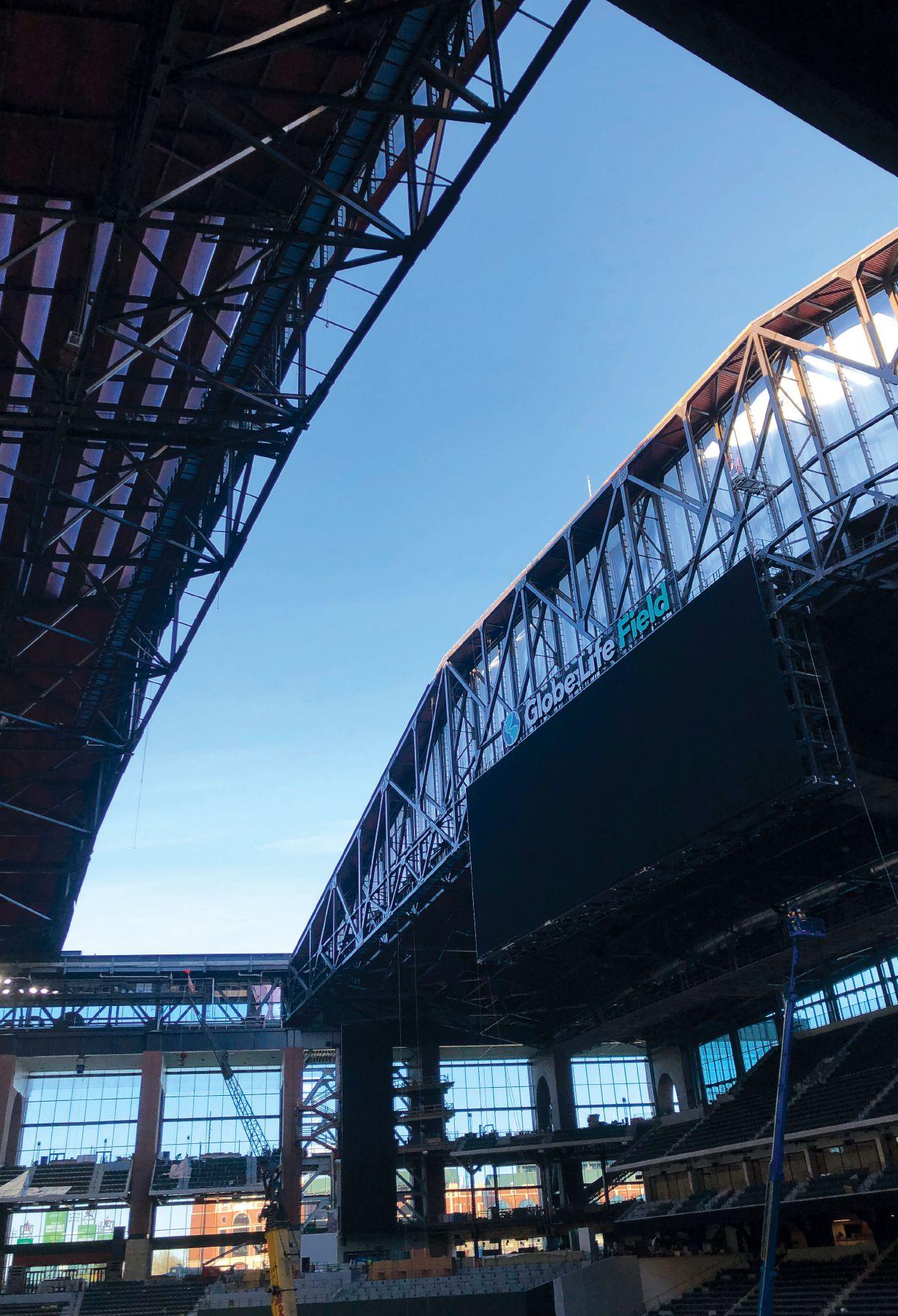
7 minute read
POWER HITTER: Rangers’ Rolling Roof
BY ERIN PINKERTON
The roof of Globe Life Field is 5.5 acres — or 240,836 square feet — and it rolls all at once. It’s the largest single-panel operable roof in the world, and its construction required 19,000 tons of structural steel, a top-notch construction team and the world’s largest American-made conventional crawler crane to put it all together.
Other major sports stadiums have movable roofs, but many have multiple panels. Globe Life Field has only one.
“The one panel operable roof structure has a continuous seal system around the perimeter. The bulb seal on the east and west are under compression while the flap seal on the north and south allow for movement in the structure,” said Telissa Hubbard, assistant project manager at Manhattan Construction. “The roof seal is a critical part of a building with this design.”
When the roof is closed, the outdoor elements are kept at bay by a white rubber membrane on the north and south sloped planes, and the flat center is covered with clear panels made of ETFE (ethylene tetrafluoroethylene). Donald Veitenheimer, structural superintendent at Manhattan Construction, described ETFE as resembling a moon bounce, two pieces of plastic with air blown in between.
“It has this new aspect called intelligent shading,” added Grant Phifer, senior project engineer at Manhattan Construction. “When the pillows blow up, they get air sent through them, and the foil inside separates to create a gap. If you’re looking directly underneath, it blocks the sunlight, so sunlight comes in only at a certain angle.”
The roof structure consists of five huge pairs of steel trusses and tie-in steel between each truss, and the roof can open in about 12 to 15 minutes so Texas Rangers fans can enjoy the ballgame under the shining springtime sun. “The operable roof consists of 10 trusses, which were erected in pairs and are supported by the north and south rails. The roof actually rolls on a rail similar to a railroad track,” Hubbard explained. “Once the system is complete, 10 motors will operate the roof.”
Under all the innovative roofing materials and powerful mechanization, there is steel — lots and lots of steel. In all, the roof steel weighs about 19,000 tons, Phifer said. That’s about 38 million pounds. The steel was furnished and fabricated by W&W/AFCO Steel and erected by W&W Steel Erectors.
The structural steel was brought in and assembled on-site in the stadium bowl. Each of the roof’s 33 steel truss sections were erected in three parts: the north section, the middle section and the south section. After one truss was completely erected, it was slid down the rail to the west so the next truss could be set. Once the first and second trusses were completely erected, they were tied together with more steel. Moving this much steel required many work hours and enormous equipment.
“We had up to 11 cranes on-site at a given time,” said Charles Dougherty, president of W&W Steel Erectors. “The main heavy-lift crane that we used to erect the roof truss assemblies was a Manitowoc 31000 heavy-lift crane, and it is the largest crawler crane manufactured in the United States.”
The Manitowoc 31000 was positioned in the stadium bowl so crews could assemble and erect all three pieces of each truss one after the other, Phifer said.
–GREG MCCLURE, MANHATTAN CONSTRUCTION, SENIOR VICE PRESIDENT

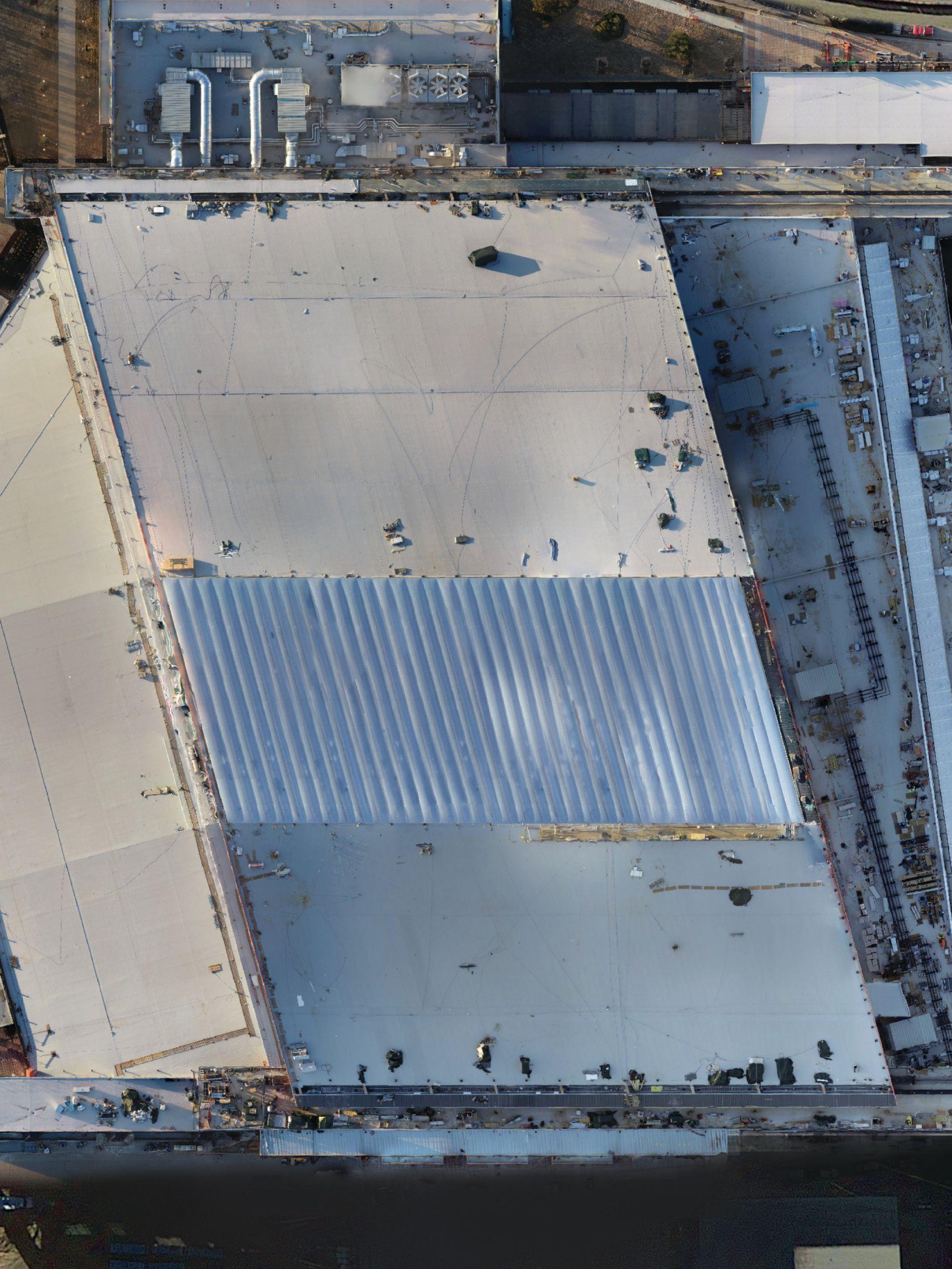
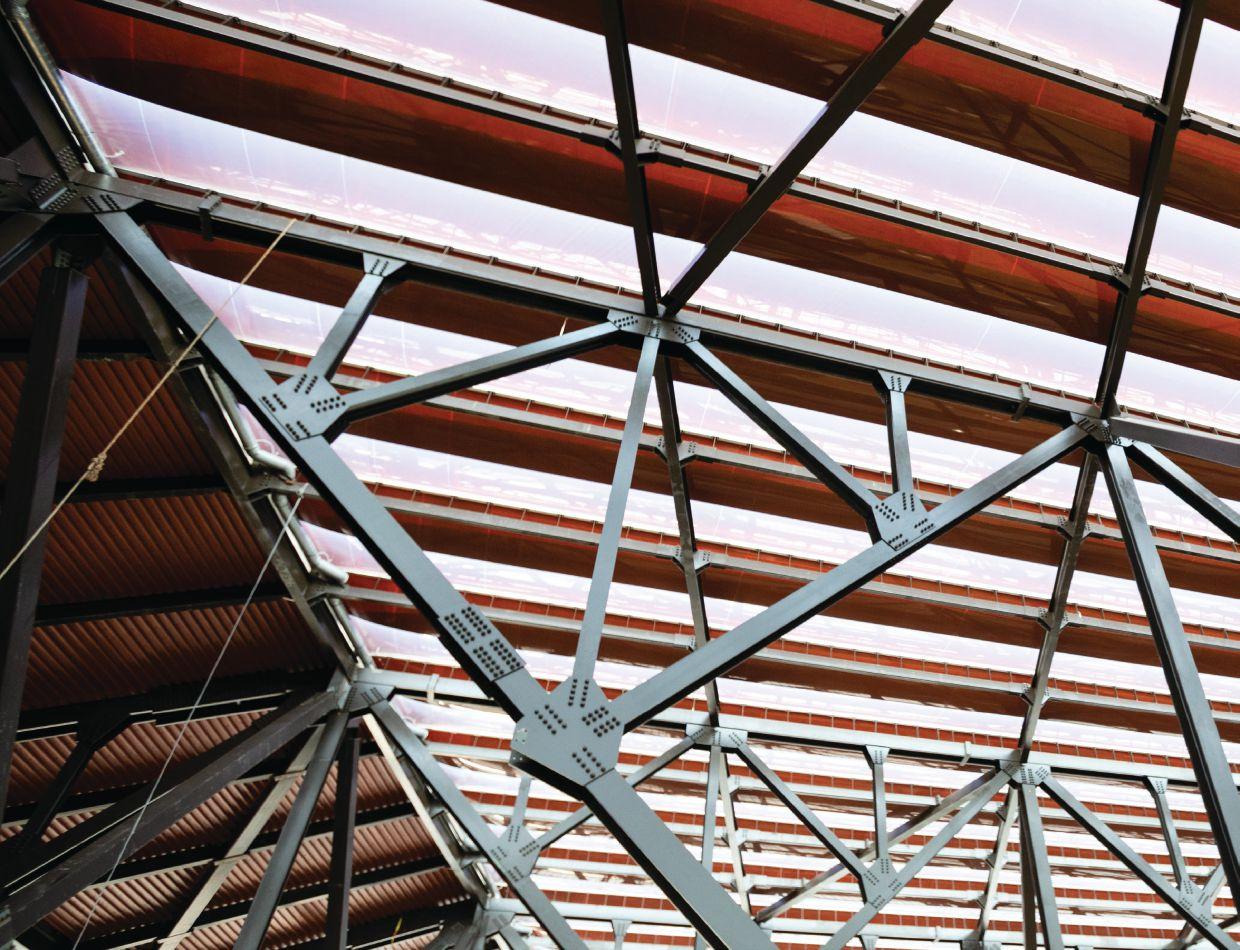
“Once we got the north end ready to pick, we would lift it off the ground, set it and connect it to the bogies on the north, and then they would sit on a shoring tower. We had two shoring towers in the middle of that span so it could support itself with just one end, the north end, of the truss,” Phifer explained. “Then we would erect the middle piece and then the south piece. Once it was on the shoring towers and connected at both ends, the shoring towers would drop it until the truss would be able to support itself.”
As the structural steel was going up, time and space were two of the biggest challenges. To keep up with the tight schedule, crews had to pick and set the trusses quickly, all while maneuvering around a stadium bowl full of steel beams, cranes and workers from various trades. MANITOWOC 31,000 CRANE 400 feet – The crane’s maximum height 3 weeks – Time to assemble the crane
3,000 tons – The weight of the crane 140 truckloads – The amount of freight to deliver the crane for assembly 5 million pounds – The weight the crane can lift “Manhattan did a very good job coordinating the construction of the arena’s foundations, the bowl structure and the roof structure. At many times during the construction of the project, all three of the areas were being built simultaneously in different phases,” Dougherty recalled. “Manhattan developed a very good management plan to enable the project schedule to be completed on time.”
The Manitowoc 31000 crane was also helpful in handling the time crunch and the limited space.
“It definitely took up a big footprint, but it also made picks that would have required two cranes to make, or we wouldn’t have been able to put it up in quite as big of pieces,” Veitenheimer stated. “Another crane is not capable of moving the way that crane was. With this crane, we were actually able to lift the truss and crawl while we had that hanging from the crane to get in a better position to set it.”
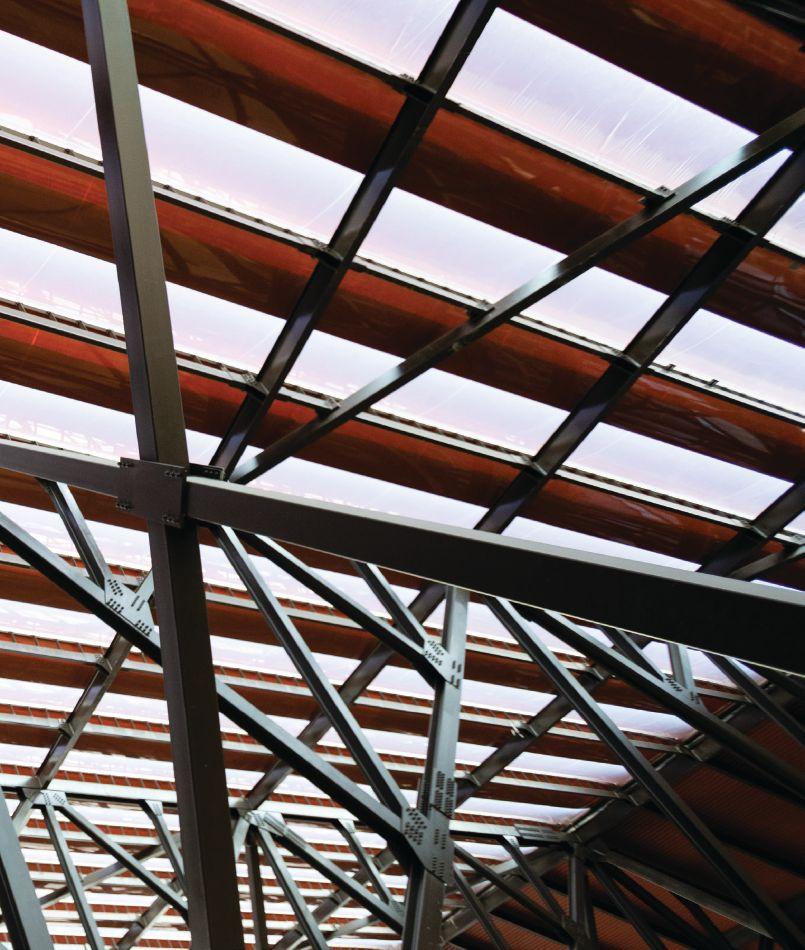
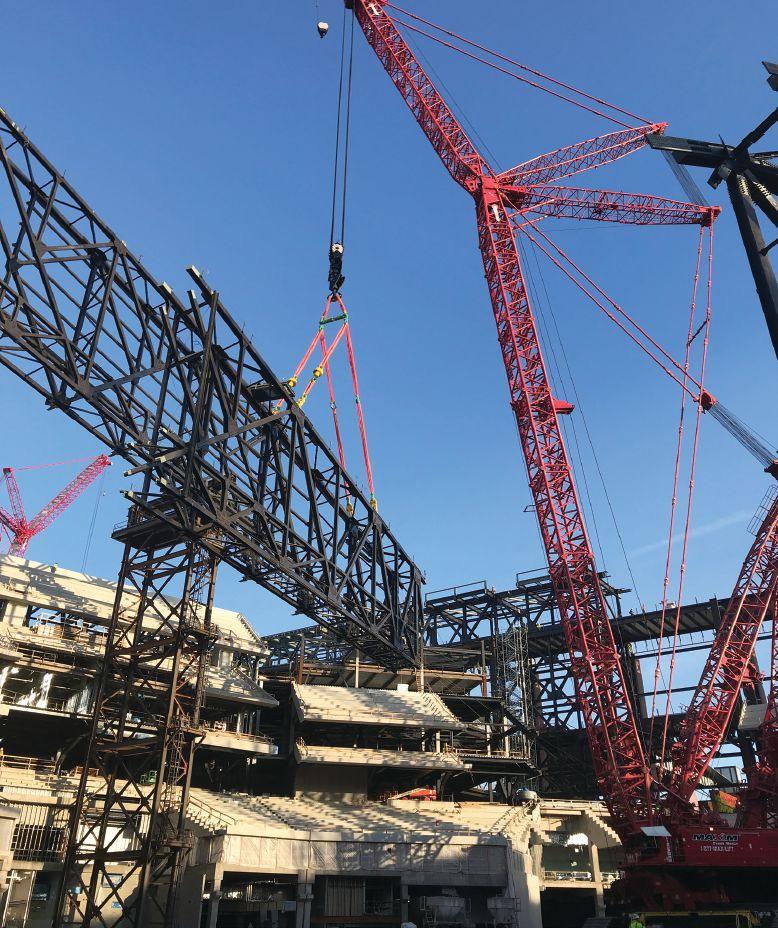
–JEFF JANSING, PRINCIPAL AT WALTER P MOORE
The biggest pick made by the Manitowoc 31000 at Globe Life Field was over 1.4 million pounds, Veitenheimer said. That’s like lifting every Major League Baseball player on the active roster at once — times 10.
The Manitowoc 31000 used at Globe Life Field is one of only two in the world, the other being in South Korea. The crane came from Atlanta, where it worked on Mercedes-Benz Stadium, to Arlington to work on its second project ever.
It took about 140 freight truckloads to bring each piece of the crane to Arlington, and the crane took about three weeks to fully assemble in the bowl, Hubbard noted.
“The crane is not used very often, as you can imagine. These type of projects aren’t around all the time,” she said.
In the end, Manhattan Construction and the rest of the building team at Globe Life Field worked thousands of work hours, lifted and set millions of pounds of steel, and made countless decisions about how to make it all fit in the bowl and in the short schedule. After all that effort, they have one thing to show for it. Fortunately, that one thing is a big thing — a state-of-the-art ballpark with a 5.5-acre, single-panel rolling roof — the largest of its kind in the world.

Baseball’s First Retractable Texlon® ETFE Roof
For the past 38 years Vector Foiltec has been helping clients create successful projects that are both innovative and sustainable, many the first of their kind.
When the design team for Global Life Field needed help figuring out a way to design the ETFE enclosure to keep the sun’s glare out, our team was there to provide expertise. It was the goal to maintain a certain amount of transparency, while protecting the ball player’s view of a baseball in the air.
Vector Foiltec developed an intelligent shading system. After conducting a solar study, Vector Foiltec was able to identify which areas and at which angles would be most affected by direct sunlight. Through a combination of a special custom coating, color on the foil and strategic positioning of printed and transparent foil, we were able to reduce the danger of glare, while at the same time achieving the maximum amount of light transmission. This development contributed to significant cost savings, as the need for a suspended baffle system was no longer required.
With 18 offices around the world, we provide local service with global knowledge, continuously delivering great design and engineering, as well as on time performance for successful projects. Vector Foiltec would like to help you develop the best solution and execute your design ideas successfully.

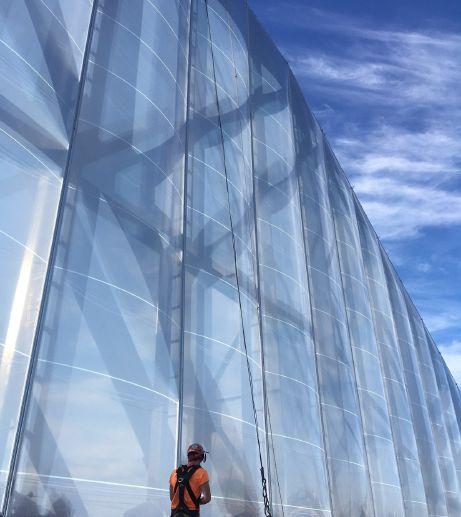
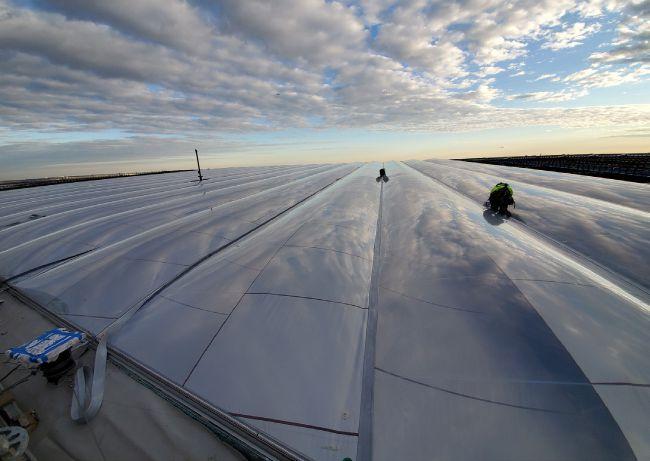