
11 minute read
Voices of Growers
How Vertical Integration Can Help Family Farms Weather Financial Storms
by Barb Iverson, Wooden Shoe Tulip Farm Growing up on a farm is an incredible experience. You learn early to see what needs to be done and step in to help. Our work in not measured in hours but in the job that needs doing now. As a kid, our family had a lot of tight years; you think you’re living in paradise but don’t really see or understand the struggles. I remember my mother once telling me about the time there was no money in the account and the mortgage payment was due. She was sure this was the beginning of the end of the farm when a bonus payment came in expectantly for one of their crops. Now, as an adult (and throughout my farming career) this economic uncertainty continues. I have had loans called in, held my own paycheck for months so my employees got theirs, and had to sell land to pay the bills. Living on the edge of economic sustainability is a major issue for today’s farmers. As farmers, we are land rich and cash poor. One of the ways our farm has addressed this is through vertical integration. Our vertical integration started with a crop we began growing in 1974: tulips. When another farmer retired, we bought his crop but soon realized that tulip bulbs sales wasn’t very easy for a small-scale grower. From this struggle emerged Wooden Shoe Bulb Company. Several family members thought it would be great to sell direct to the home owner. Our small retail and mail-order business almost folded after attending garden shows the first two years. It wasn’t until our third year that we decided to open our tulip field to the public and Wooden Shoe Tulip Farm started to take off.
Our first years of the festival focused on cut-flower and bulb sales. Admission was free and although not very prosperous, we were able to pay the bills. This changed in the late 1990’s and early
Photo: Wooden Shoe Tulip Farm
2000’s when we witnessed a shift in our visitors; flower sales slowed and bulb sales dropped in half. There are a number of market factors for this happening, but at the end of the day, we weren’t even breaking even. At this point we made the difficult decision to start charging admission to see the tulips. I have to admit, the abuse and negative comments were difficult to hear, especially when the entire farm was struggling. But what happened after we started charging amazed us…our attendance went up! Because we were charging a fee, customers thought there must be something worth seeing. We created value.
Years later we are still creating memories for thousands of visitors. Also, as an overall farm, we are on better financial footing. We have discovered that there is a desire for people to get out on a farm. They want to reconnect with the land, meet a farmer and understand what we do.
Some call what we do agritourism. I call it keeping the family farm alive.
CBCRE.COM
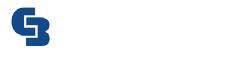

MOUNTAIN WEST REAL ESTATE COLDWELL BANKER COMMERCIAL B U Y · LI ST · SELL
503-588-3508
Voices of Growers New Cold Storage Warehouse Solves Hop Dilemma
by Peter Weathers Hop growers and brokers in the mid-Willamette Valley have faced the same problem late each summer over the last few years: millions of pounds of hops would flood the handful of older cold storage receiving stations at the same time. This has caused production bottlenecks, risk to quality, and more than a few hot tempers.
Those were the challenges that drove Salem-based Sodbuster Farms and its partners to propose, construct, and begin operating one of the newest energy-efficient, food-grade cold storage facilities in the valley, Hopmere Cold—all within the span of a few months.
Judging from the thousands of hop bales that sailed through the facility last August and September, it was a successful investment and offers a great new cold-storage resource for the Mid-Valley.
Without a dedicated receiving station for their hops, Sodbuster Farms had struggled in recent years to make sure their hops were stored safely in Salem before making the trek to their partner Yakima Chief Hops (YCH) in Yakima, WA. YCH is a grower-owned, brewer-centered supplier to the brewing industry worldwide and purchaser of Oregon, Washington and Idaho grown hops. YCH also understood the benefits that a dedicated cold storage receiving warehouse would bring and put out a bid to the community for proposals. In late 2018, Doug Weathers, president of Sodbuster Farms, made a compelling case to his Oregon Seed Cleaning partners Doug Zelinsky of Alpha Nursery and Bob and Tom Fessler of Fessler Farms.
A new cold storage plan began to take shape.
Construction of Hopmere Cold began in early 2019 and was made possible by special municipal abatements and tax credits, which were brought to Sodbuster’s attention by Nick Harville of SEDCOR. In fact, Hopmere Cold was the first business in the state to receive the new rural industrial tax exemption sponsored by Marion

county, part of Oregon Senate Bill 1565 that was passed in 2016 (ORS 307.340(5(6))). Additional Energy Trust of Oregon tax credits were earned for energy efficient building designs and equipment. With the hard work of Salem Concrete, Ingleman Electric, APPCO, InfinityMicro, and TriPly Construction, the 28,000 square foot facility was up and operational just in time for hops harvest.
The increased capacity, process control, and reliability that Hopmere Cold brought to the 2019 harvest was a boon to many and was especially beneficial to Sodbuster Farms. The fifth-genera tion hops farm prides itself on the quality of its hops, and Hopmere Cold allowed the farm to monitor and respond to quality issues faster while facing no delivery hiccups.
The facility reduced strain on other cold storage warehouses and easily stepped into its role as the centralized receiving and shipping station for YCH’s Oregon-consigned hops. YCH also benefited from the warehouse’s improved product monitoring, supply chain management, and high-speed internet for inventory control.
Hopmere Cold is ready to make sure next harvest’s hops remain at the highest quality and are received and shipped efficiently. And because the facility is empty from December until August, Hopmere Cold might be the right place for your next harvest, too.
FULL SPECTRUM ENGINEERING AND SURVEYING SERVICES.
ENGINEERING SERVICES, INC

Celebrating over 30 years in the industry.
We are here to take you from start to finish.
• Residential Subdivisions • Apartment Complexes – Site and Building Design • Commercial – Site and Building Design • Geotechnical Services • Land Planning – Comp Plan Zone Change, Conditional Use • Land Surveying and More
CALL FOR AN APPOINTMENT 503-363-9227.
Known widely for its lime business but growth could redefine Marion Ag Service as the “7-Eleven of fertilizer”
Since its inception in the 70’s Marion Ag’s visible flagship business can be seen from the freeway to the gravel back-roads across Western Oregon. Chances are if you if you’ve seen the iconic lime trucks and buggies you may not think twice about the team of drivers, dispatchers and support staff that are involved in safely helping area growers amend their fields. It’s an intensive business that covers a lot of ground… literally. Fast forward nearly 50 years and the premise at Marion Ag is that behind every opportunity and effort is a team of people that make it happen. In 2017 the company made a sizable investment to create efficiencies for the local fertilizer market. The new 30,000 ton, rail-served fertilizer plant checked a lot of boxes for the company, it’s customers, suppliers and the community:
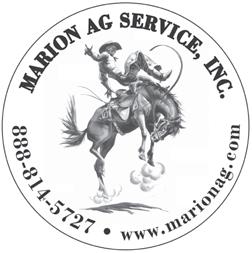
Marion Ag Service consolidated storage of its bagged fertilizer business by increasing it’s warehouse footprint to over 150,000 sq. ft. This significantly reduced the amount of road miles involved in shuffling inventory among three locations. The footprint and expertise of their staff allows Marion Ag to carry the widest variety of fertilizer products to serve wholesale and retail customers as a “one stop shop”.
Bulk fertilizer storage was made available to manufacturers who desired more opportunities to place their nutrients in-market for timely access by area ag retailers. Most of these tons arrive by rail rather than truck. The facility functions as a key element in the regions supply chain of Nitrogen, Phosphorus and Potassium all while increasing safety on rural roads.
Nick Harville, SEDCOR Business Expansion and Retention Manager, has collaborated with Marion Ag to understand the
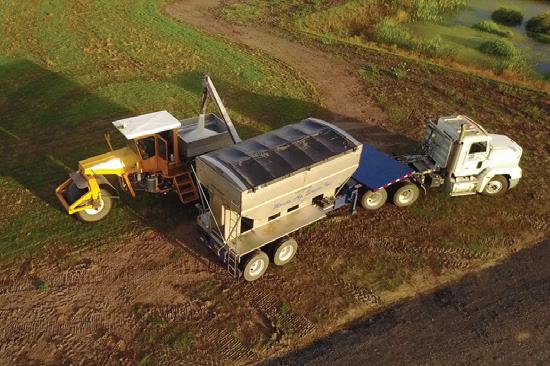
economic and social impact of its investments. By helping Marion Ag outline the impact on transportation it helped change the bottom line of the business through application of programs like the Rural-Industrial tax exemption.
Growing practices and crop mixes have changed in the last 50 years as well. Collaborating and advising growers to achieve long term yield, quality and profitability is at the forefront of their business as these changes occur. Over a decade ago Marion Ag had the opportunity to add Gale Gingrich to our team as a research agronomist. Gale’s independent and objective work in cooperation with local growers help growers learn how to apply the latest management techniques.
With technology in agriculture advancing at breakneck pace the company only sees additional demand for vetting new tools to be applied on our local cropping systems. The recent addition of Anne Iskra to the team as Technical Services Manager is the conduit to Gingrich’s historical efforts and a foundation of a vision for vetting solutions efficacy here in our local market. Marion Ag’s staff has developed a dialogue with Alex Paraskevas, SEDCOR Polk County representative, seeking to find ways of bringing meaningful technology to area growers.
Whether Marion Ag’s business development plans involve managing the impact of capital investments or leveraging people’s knowledge to create better solutions for growers SEDCOR is a great addition to the team.
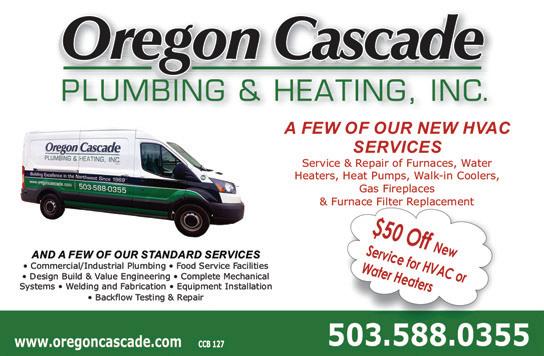



Grow With Us!
Holly Nelson, Executive Dean, Regional Education & Academic Development
On Chemeketa’s Salem campus, spring will not just bring on a new crop of nursery plants in our greenhouse and fresh veggies in our organic gardens. It will be a spring to remember for our Agricultural Sciences programs! This spring marks a time our department has dreamed of happening. Maybe, just maybe, dreams do come true!
Three years ago, the college received $6 million dollars of matching funds from the state to construct a new agricultural sciences space. The word Chemeketa means “a gathering place” and we hope to build a space that partners can come together and create a synergy amongst the agricultural community.
There are many opportunities for collaboration, partnerships, and thought sharing around the future of ag and needs of our community. We are excited to be part of conversations about training needed for jobs of the future and the needs of technology within agriculture.
The department has been in planning stages for over two years on their new agricultural sciences building and community hub. Major construction and dirt moving will get underway in April, and the building is set to open winter of 2021. This 12,000 square foot building will incorporate classroom and lab space to support our Horticulture, Agribusiness Management, and agriculture workforce training programs.
The space will offer small and large classrooms, flexible and interchangeable classroom spaces, informal learning space for students, community hub meeting rooms, and spaces to promote technology usage in agriculture.

The plan not only incorporates a building to engage learning, but outdoor learning gardens, a woody ornamental research lab, organic garden spaces, a state-of-the-art greenhouse, and outdoor pavilion. These spaces have been badly needed by our programs and will promote learning opportunities and programming for students of all kinds on the campus.
One major concept we have focused on building into the space has been around creating a hub to support our local agricultural community. We look forward to being part of conversations in the future and encourage groups to connect and utilize the space once we are open.
We hope to host events and learning opportunities for high school students, Future Farmers of America (FFA), commodity groups, Master Gardeners, and more.
Watch for new and exciting things from Chemeketa’s Ag department!

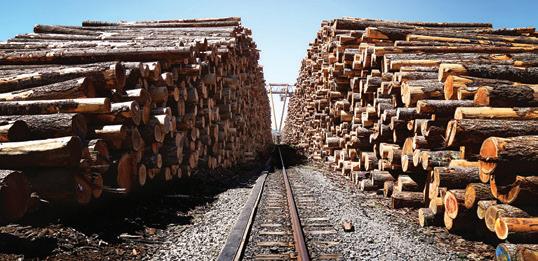
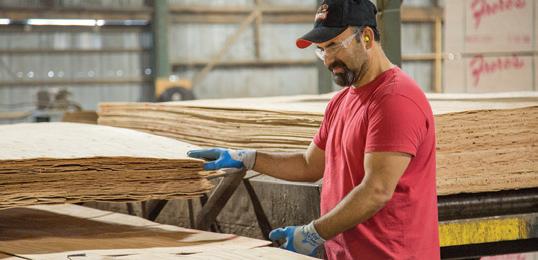
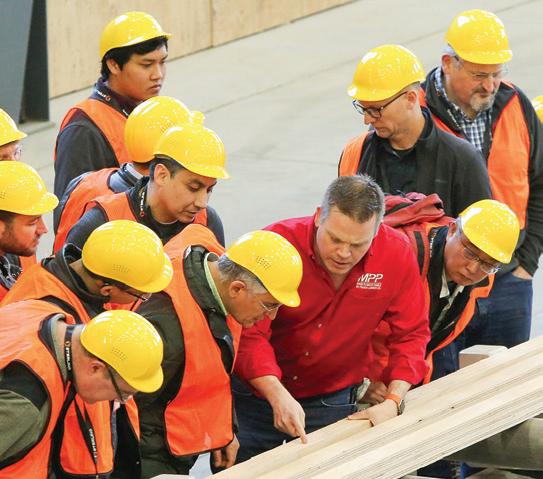
Established in 1922 above the Santiam River, Freres Lumber Company has provided quality wood products and local jobs for almost 100 years. We manufacture a range of products such as veneer, plywood, lumber, and now our own patented product, the Mass Plywood Panel (MPP). MPP is a massive veneer based panel up to 12’ wide and 48’ long and is designed to be an environmentally superior, sustainable alternative to concrete and steel in construction.
An Equal Opportunity Employer
Visit frereslumber.com to learn more about the company.
If you are interested in employment opportunities at an established, innovative business, current job openings are listed on the site.
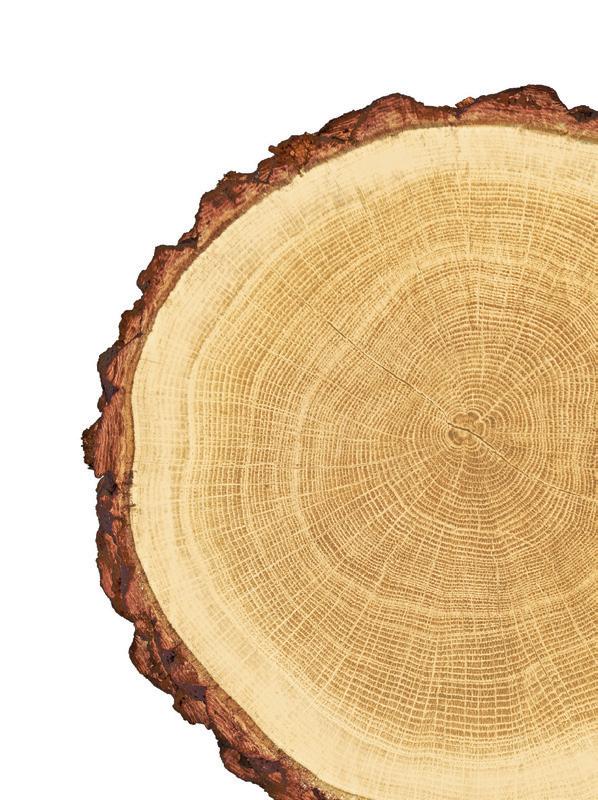
Please join us on Facebook at facebook.com/frereslumberco to join our family, friends, and local community. Freres mills and cogeneration facility are open for tours. f l 4