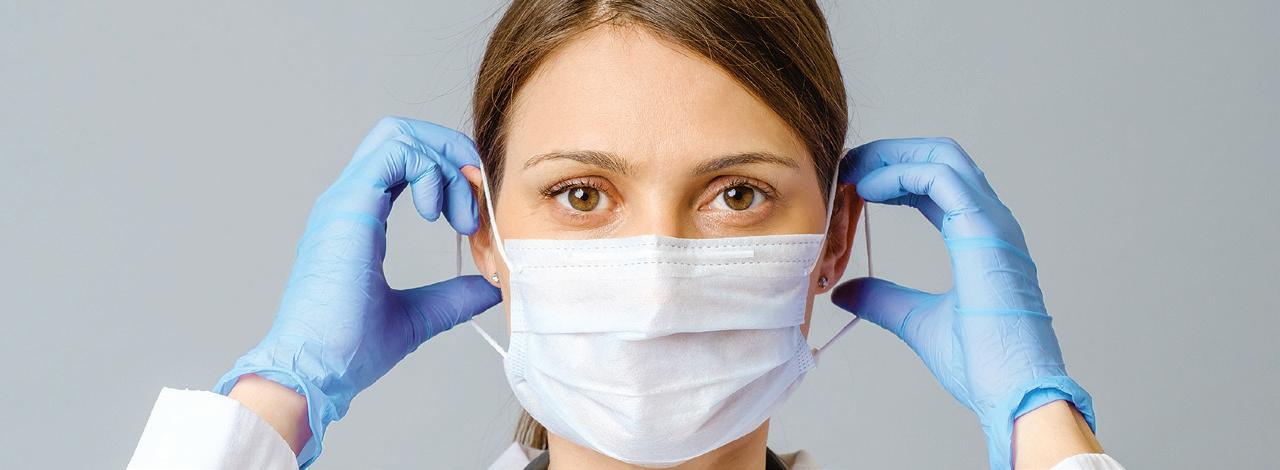
10 minute read
Providing PPE: The Right Thing to Do
Providing Personal Protective Equipment:
The Right Thing To Do
WaterShed can be hard to find.
Google Maps will tell you you’ve arrived at their building as you drive under the train tracks that go over Portland Road in Northeast Salem. But, if you keep driving, make a few turns, wander behind a small neighborhood and few indus trial buildings, you’ll find a bright blue building that houses a key manufacturer of medical gowns in the Willamette Valley.
Right as you get out of your car, you’ll be blasted by the fresh scent of tortillas coming from the nearby Don Poncho plant. A small, metal staircase will lead you to a blank glass door. You’ll be buzzed in and asked by a small paper sign to practice social distancing.
Put as simply as possible, WaterShed makes rain gear. More specifically, they make semi-custom rain gear for first responders: military, police, and firefighters.
As owner Russ Monk puts it, “We innovate.”
Russ is as unassuming as his building. He greets his guests with a broad smile under a thin, salt-and-pepper beard. He has the look and demeanor of a humble craftsman. He is Ron Swanson, if Ron Swanson had a couple dozen patents.
He and his team at WaterShed have made an art and a science of creating custom rain gear for first responders.
But earlier this year, the definition of “first responder” expanded rapidly. Without much warning, the category reached far past those showing up to war zones and fires. Now, first responders included doctors, nurses, medical as sistants, nursing home staff, janitorial staff, delivery drivers, and more.
And their need for Personal Protective Equipment (PPE) was immediate and immense.
They needed gloves, masks, gowns, face shields, and hand sanitizer.
As COVID-19 moved quickly through Oregon’s population, PPE stockpiles quickly dwindled. Soon, hospital staff and those who were most exposed to the virus did not have what they needed to protect themselves.
TIMELINE AND CAPACITY The problem was clear. And to Russ and the entire leadership team at WaterShed, the solution was even more clear.
“We’ve always existed to provide equipment to frontline workers. We’ve spent 30 years building systems and pro cesses and fostering a mindset that allows us to respond to something like this. We simply asked the hospital, ‘What do you need?’ Then we got to work.”
For Russ, everything hinged on materials.
“If you have the right materials, you have options. Without it, all you have are choices.”
Just behind the two roll-up doors at WaterShed are 60 rolls (about 120 miles) of soft-blue fabric. To Russ, these rolls are what made their response possible. “I got this material from a supplier in North Carolina. This was just before most of it was bought up; it made it nearly impossible to find. We got it just in time.”
Russ went to the leadership at Salem Health and said he had a way to get them custom-designed gowns. And lots of them.
Dr. Lloyd Hiebert, who worked closely with WaterShed
Our region’s manufacturers have given immensely of their time, resources, systems, and creativity to ensure our frontline workers are kept safe.
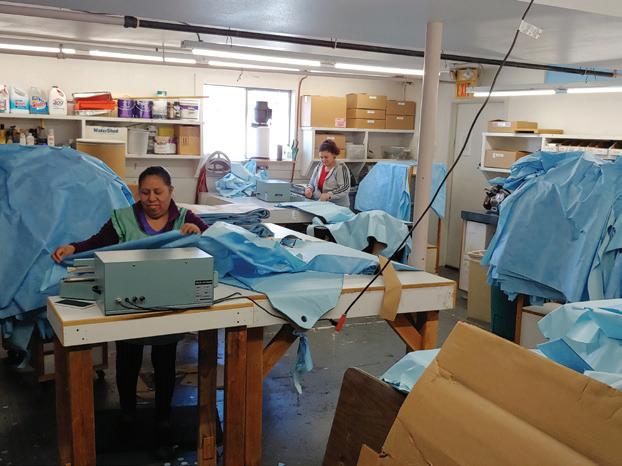
during this process, said he was incredibly glad WaterShed came forward. “The hospital’s need for PPE was dire, espe cially for disposable cover gowns. They had an approximate 7 to 10 day supply remaining. Their major medical supplier, upon which the hospital had long relied, was unable to meet the hospital’s PPE needs now or in the foreseeable future. Their PPE gas tank was on empty.”
It was up to WaterShed to help fill the tank.
According to Russ, “The head nurse at the hospital was overjoyed when we told them our timeline and our capacity.”
Here is the quick story about how WaterShed provided the gowns to Salem Health.
On Friday, WaterShed received the raw material. On Sun day, they had a design.
On Monday, they had a prototype. That evening, the proto type was approved by the team at Salem Health.
On Tuesday, they were starting production.
By that Friday, Russ personally delivered neatly packed boxes of bright blue gowns to Salem Health from the back of his wife’s SUV.
“These days, I am going all over with that SUV! We are cur rently delivering a couple thousand gowns to Salem Health. We’ve also started delivering gowns to places like Santiam Health and Samaritan down in Corvallis.”
As of press time, WaterShed is producing over 2500 gowns every day. They hope to be producing 5000 a day by the end of the month.
THE ADVANTAGE OF LOCAL “We always ask the same questions of our clients,” says Russ Monk. “It doesn’t matter if it is for a snow jacket for the mili tary or a rain coat for a local fire department. We ask, ‘What do you love about what you have now? And what do you not love?’ From that, we know how to design the product.”
When Salem Hospital received their first batch of gowns, they had only one complaint. “They said we made it too strong.”
The strength of the fabric and the design made the gown Continued on page 6
How To Make Gowns, Step-By-Step We asked Russ Monk to take us through a step-by-step process for producing protective gowns. “It all starts with the right raw materials to meet the protection levels for our frontline people. We were lucky enough to acquire 160 miles of fabric that can be converted into PPE.” “All of the base pattern work starts in 2D and is then converted into automated cutting patterns.” “Watershed has a computer spreading table that lays out 60 fabric layers at a time preparing it to be cut into 240 raw cover gowns.” “The raw parts are then heat welded to make a 3D gown. The gowns are folded and then packaged in boxes of 50 for ease of distribution in the facilities.”
WaterShed staff seal, fold, and box thousands of gowns every day.

hard to remove which made it more likely physicians would make contact with the viruses.
“They obviously loved the durability of the gown,” says Monk. “But they still had to remove it quickly and efficiently. So, we quickly augmented our design to include perforations on the back. Now, the staff could reach back, tear off the gown, wrap it up in their gloves, and throw it away safely.”
WaterShed is only 2.8 miles from Salem Health’s front door. The proximity of WaterShed and the all-in-house na ture of their operations allows for changes and adaptations that are relatively instantaneous.
“It took us days to make this change for the hospital staff. Days! With an international manufacturer, this change would take weeks. That’s the advantage we have.”
According to Dr. Hiebert, “It was a heart-felt pleasure to be involved in providing personal protection for health care staff I had served with since 1983. Working with local caring people and local resources to protect local health care work ers is the definition of community partnership.”
A REGION OF MANUFACTURERS Mike Vanier, Vice President of Client Engagement at the Oregon Manufacturing Extension Partnership (OMEP) said manufacturers all over Oregon were uniquely positioned to handle the PPE shortage crisis.
“I think our state and our region has always had a deep spirit of innovation. I can name about 15 manufacturers off the top of my head who retooled--turned on a dime--to make needed PPE.”
Vanier said this goes way beyond gowns. “We saw some of our clients, those who machine metal, making parts for ventilators. Others, like distillers, started producing hand sanitizer. This list goes on. And it’s a long list!”
According to Vanier, this crisis has demonstrated the im portance of a strong, resilient strength sector of local manufacturers.
“We saw how fragile an international supply chain can be Continued on page 8
Reviewing risks and managing exposure.
Good insurance protection begins with an in-depth analysis of risks that face your workforce, buildings and assets. We make sure our clients are protected from the liabilities their companies face.
Contact David White for a review and a free quote.
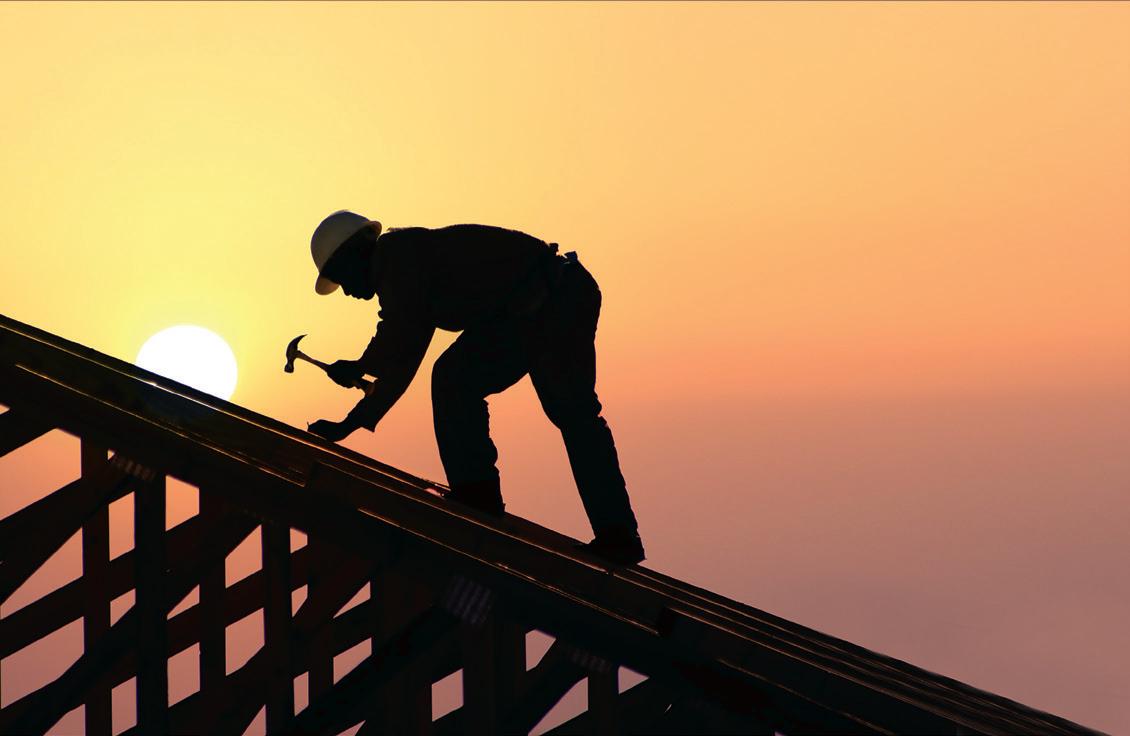
David White 503-585-2211
Stand secure. Be protected.
Huggins.com
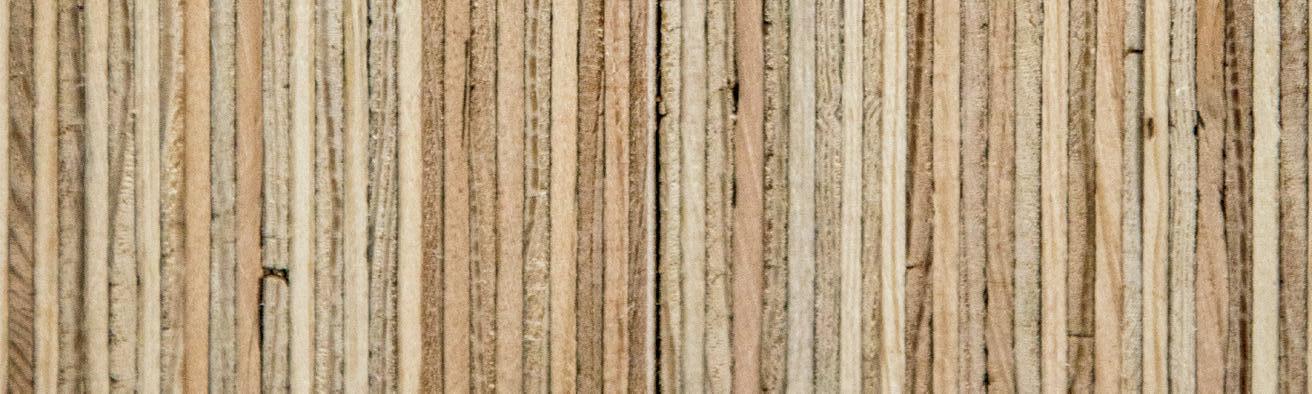
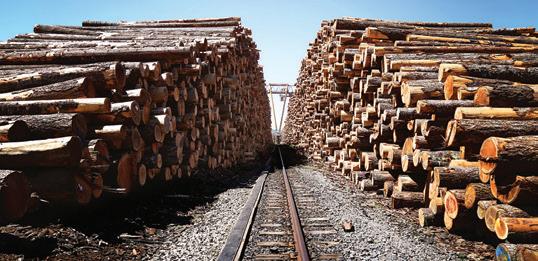
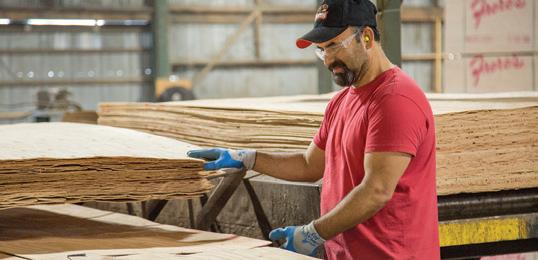
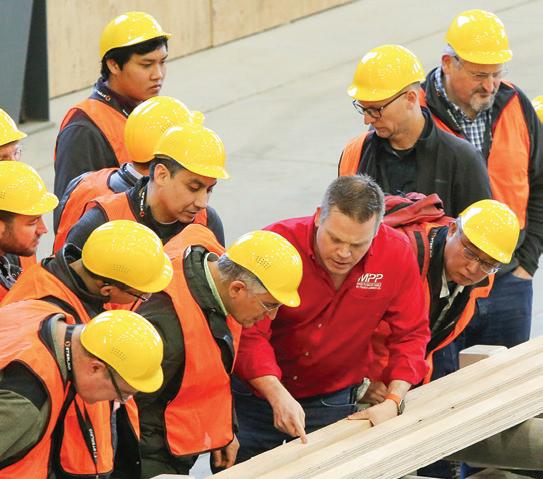
Established in 1922 above the Santiam River, Freres Lumber Company has provided quality wood products and local jobs for almost 100 years. We manufacture a range of products such as veneer, plywood, lumber, and now our own patented product, the Mass Plywood Panel (MPP). MPP is a massive veneer based panel up to 12’ wide and 48’ long and is designed to be an environmentally superior, sustainable alternative to concrete and steel in construction.
An Equal Opportunity Employer
Visit frereslumber.com to learn more about the company.
If you are interested in employment opportunities at an established, innovative business, current job openings are listed on the site.
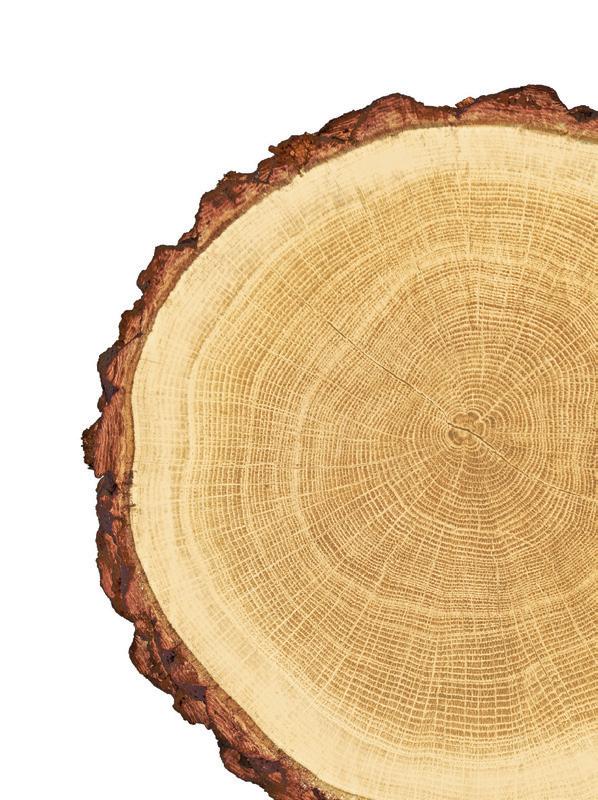
Please join us on Facebook at facebook.com/frereslumberco to join our family, friends, and local community. Freres mills and cogeneration facility are open for tours. f l 4
MAIL: P.O. Box 276, Lyons, OR 97358 OFFICE: 141 14th St, Lyons, OR 97358
PHONE: 503.859.2121 FAX: 503.859.2112
PROVIDING PPE continued from page 6 in a time of crisis. I think there was already a move for firms to on-shore some of their production. The way our manufac turers have stepped up is just going to speed up that process.”
Like many local manufacturers, WaterShed is not using their retooling as an opportunity to make a buck. According to Russ, they see this as an opportunity to do what’s right. “We added a lot of capacity to make this happen. We got to hire people to make this happen. And, as we get better at making these, as we get more efficient, our costs go down. When our costs go down, so do the prices we charge the hospitals.”
“Really, it is just the right thing to do,” says Monk. Many manufacturers in the region felt the same way.
Since the outbreak, numerous manufacturers in the region have donated the PPE they produced.
For instance, DCI in Newberg donated 100,000 surgical masks to frontline workers.
In another case, one gentleman in Silverton is using a small bank of personally-owned 3D Printers to produce hundreds of face shields, which he gives away.
THE NEED IS NOT GOING AWAY By all accounts, the need for PPE regionally and nationally is not going away any time soon.
“We’ve done a lot to fill in the immediate gap for PPE, which is great,” says Monk.
“In the future, it might not be hospitals needing PPE, but those second and third tier users. This would be nursing homes, dentists, surgery centers. Third tier would be other frontline workers like mail carriers, bus drivers, and others. Even restaurants, retail stores, and gyms will want to keep their staff equipped with gloves and masks.”
Russ has a plan for this inevitability, too.
“We have a saying around here,” says Monk. “If you don’t have the thing, you invent the thing.”
Practically no one has access to material. So, Russ and his team have taken it upon themselves to invent it.
Russ Monk stands before hundreds of miles of material at WaterShed.
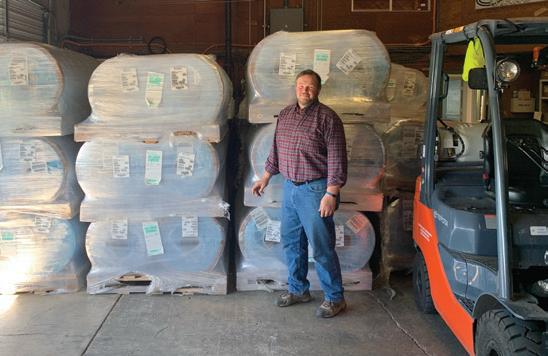
If you don’t have the thing, you invent the thing.
“I took a material that is much much easier to find and buy. Then, basically, I was able to figure out a chemical process that makes it suitable to use in hospitals, nursing homes, den tist’s offices, wherever you need people to be protected.”
Russ sees time soon when manufacturers from all over Oregon can access the material, the design, and the process to make material as needs arise.
“We have so many great manufacturers all over the state who can produce quickly and efficiently,” says Monk. “Being prepared is all about taking care of your own backyard. When you do that, you take pressure off the rest of the system.”
Before leaving the WaterShed facility, Russ will most likely give you an elbow-pump and his “Bad Joke of the Day.” Then, just before he closes the glass door, he will reflect on his team.
“I am just so honored to get to work with such a great, hard working team. There are so many incredible people doing what they can to make this project happen. I’m just blessed to be a part of it.”
CCB# 111431
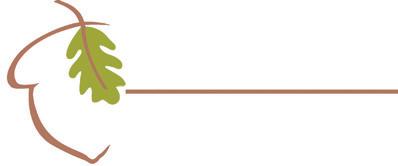
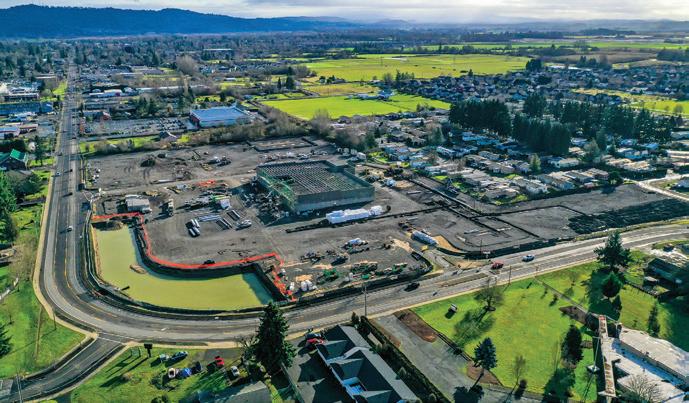