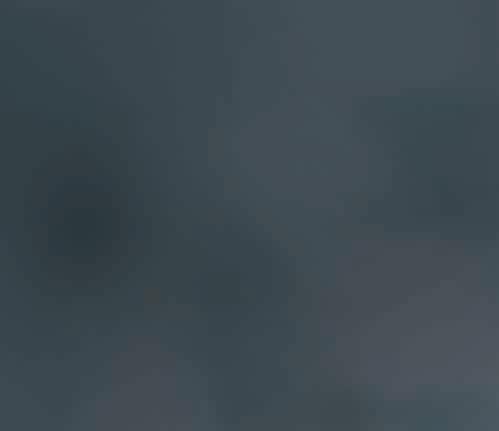
8 minute read
A closer look at corrosion
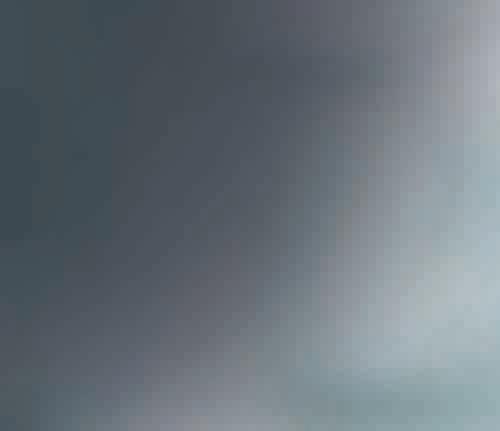
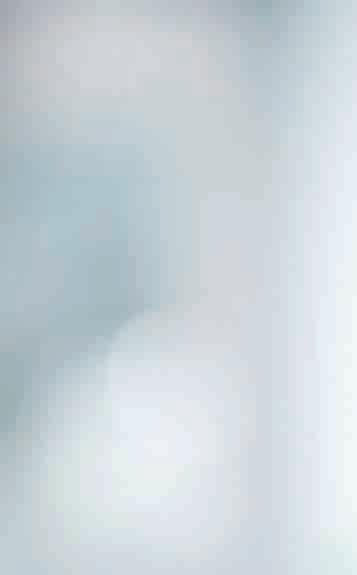
NEW DNV GL RESEARCH BASED ON MORE THAN 1,000 FAILURE CASES HAS REVEALED THAT TUBES AND PIPING ARE THE MOST FAILURE-PRONE COMPONENTS IN THE OIL & GAS AND MARITIME INDUSTRIES. FATIGUE AND CORROSION ARE THE MOST COMMON FAILURE TYPES.
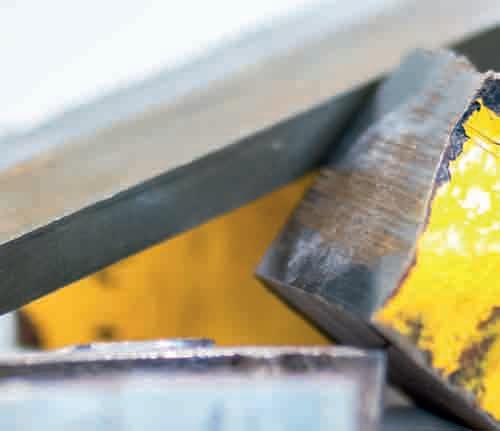

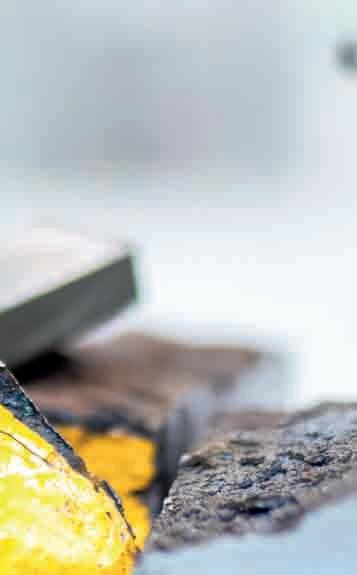
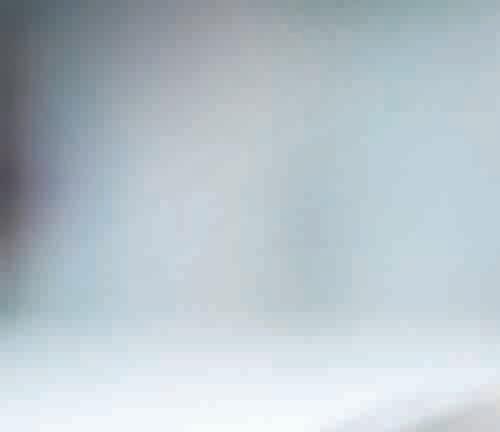
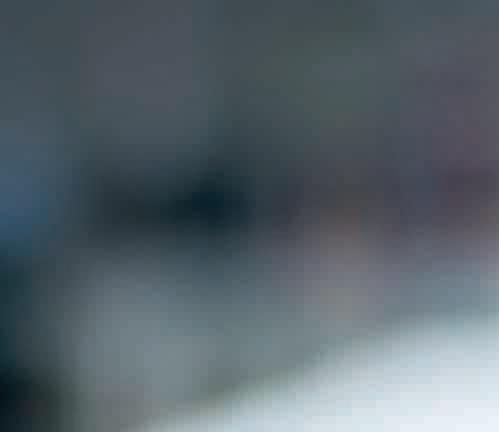
WORDS BY DR TIM ILLSON, PRINCIPAL SPECIALIST AT DNV GL – OIL & GAS. ALL PHOTOS COURTESY OF DNV GL.
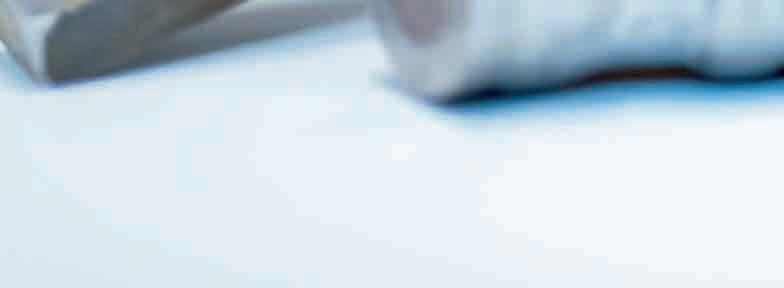
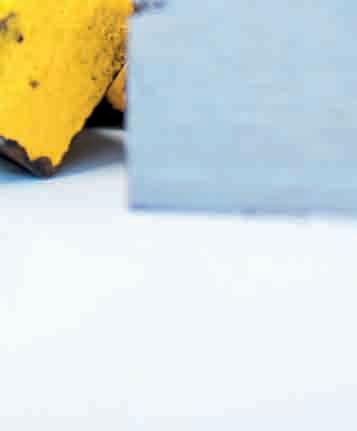

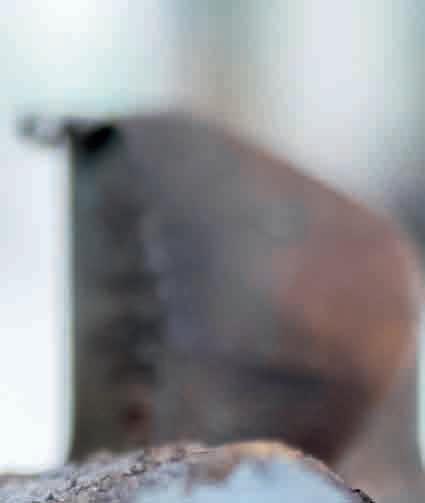

The research is based on cases from
DNV GL’s global network of five laboratories in the United States, Europe and Asia, which specialise in failure investigation. Fatigue was seen in nearly a third (30%) of cases, and corrosion in almost a fifth (19%). The research identifies which components and equipment in the oil & gas and maritime industries fail most. More than a quarter (27%) of failures were in tubes and piping, and a fifth (20%) in rotating machinery. The cost of prevention, monitoring, repair or replacement as a result of these forms of component degradation can run into billions of euros. Potentially, financial penalties can occur if major incidents result from such a failure.
High volumes of data To obtain the data for its research, DNV GL’s laboratory experts applied several methods to analyse data and documentation to assess failure trends and predict what components are most likely to fail. This included innovative approaches applying advanced search engine technologies combined with technical subject matter expertise. DNV GL continues to enhance this approach with its customers. This systematic analytical approach means high volumes of data can be examined far more rapidly than using traditional databases and spreadsheets. The accumulation of more and better data and learnings from failures can be applied in the front-end engineering design phase of development projects to engineer more robust assets. During operations, learnings can enhance optimisation of inspection, repair and maintenance for more efficient and safer use of capital and people.
The many faces of failure Failure of materials in equipment, piping, structures and associated facilities in offshore assets and on vessels could lead to severe health, safety and environmental consequences. Defining the degree of failure helps to determine approaches that can be taken to investigating why the failure has occurred and how to prevent it in the future. Failure can be defined on several different levels of security according to the ASM Handbook Volume 11 – Inoperable, loss of service life or loss of function. DNV GL believes the most serious loss of function is loss of containment, for example gas/oil escapes, that can cause fire or explosion. Failure of engineering materials usually manifests as specific physical damage. There are many ways to categorise failure damage to help prioritise methods of investigation. Failure analysts most commonly use four general descriptions of failure mechanisms: fracture, corrosion, wear, and distortion (or undesired deformation).
Understanding the root cause Failure analysis is a proven and vital discipline for finding physical root causes so action can be taken to avoid a problem reoccurring. Analysis is complex, involving several observation, inspection and laboratory techniques. The scope of failure analysis could lead to determining a correctable root cause of failure. Applying principles of root cause analysis (RCA) may ensure that the root cause is understood along with what corrective actions would be appropriate. Effective RCA often requires an interdisciplinary approach. Its objectives determine how deeply it goes into the root causes. It may take place at three levels based on the complexity of the situation and the risk of a failure happening again
Applying global expertise To be properly performed, failure analysis and RCA usually require the involvement of multi-disciplinary experts with an unbiased >>
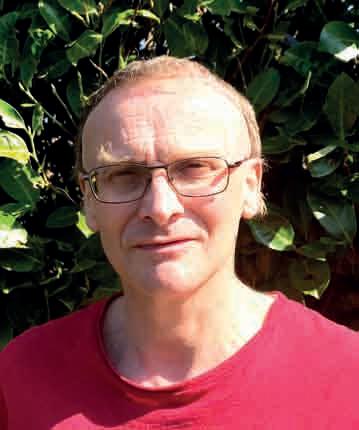
Tubes and piping are the most failure-prone components in the oil & gas and maritime industries.
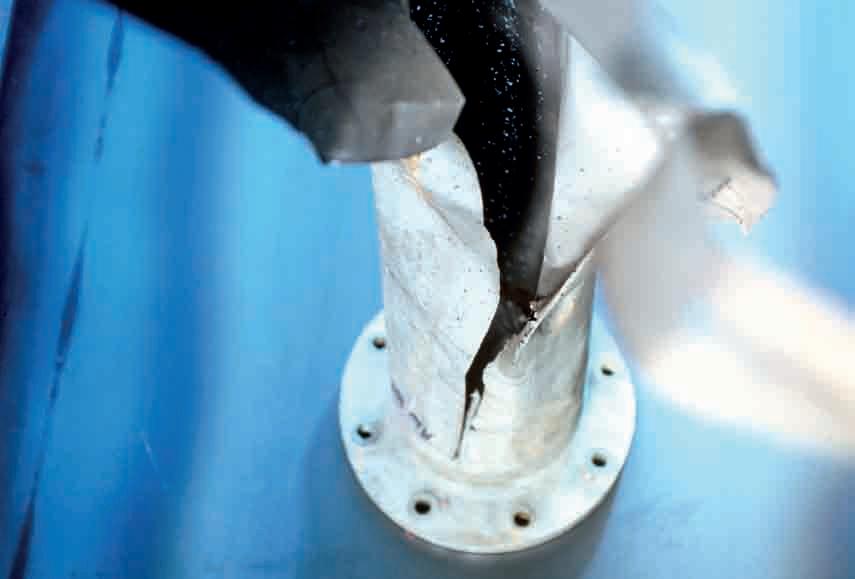
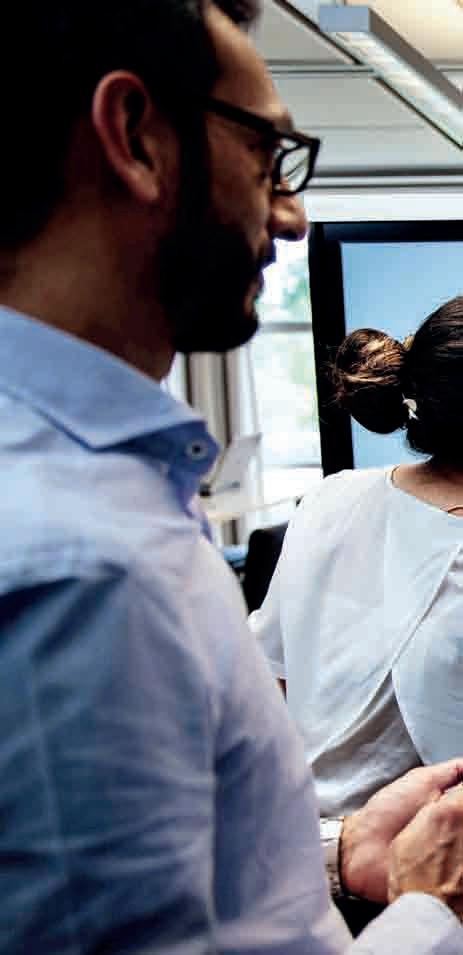
perspective of the failure. They often need access to various failure analysis tools including well-established laboratories that are experienced in handling such investigations. Using management expertise to look for management systems failure that could be the root cause is another important aspect. An example is inadequate change management procedures when changing equipment or materials.
A closer look at corrosion One of the main causes of failure after fatigue, as the DNV GL research reveals, is corrosion. External corrosion is a threat to most equipment in every process facility and deserves closer analysis and prediction than it currently receives. Inspection and maintenance to counter corrosion support safe, cost-effective operation in process industries. For internal corrosion, industry guidance and factors like fluid type, pressure and temperature help asset integrity specialists to decide which threats are credible. It is rare to find a similarly detailed focus on analysing and predicting external corrosion, however. The internal form is seen as statistically more likely and is easier to quantify and predict. Yet external corrosion is a common threat to almost all equipment in process industries where the cost of a major incident caused by hydrocarbon releases can run into billions of dollars. It is worth asking if we are so used to seeing rust on familiar items like cars in our everyday lives that it can become effectively invisible to us, even on process equipment.
Getting to grips Well-established risk-based inspection codes such as API 581 address general external corrosion attacks and corrosion under insulation (CUI). They involve considering factors such as climate, condensation and how close equipment is to sources of potentially corrosive water mists, such as cooling towers. Even though general external corrosion can often be slow, it can do much damage over a construction’s lifetime. It can be aggressive, especially along coasts in hot climates when salt fogs wet steel surfaces in the morning. Water evaporation during the day drives up the salt concentration to cause high rates of corrosion that damages coatings. High external concentrations of sulphur oxide pollution greatly accelerate external corrosion of plant by acidifying water and destabilising rust layers.
Laboratory services DNV GL has specialised corrosion testing laboratories located in the USA (Columbus, OH), Norway (Bergen), Singapore and the UK (Loughborough) that test both metallic and non-metallic materials, with specialties in harsh environments such as H 2 S sour service testing and high pressure – high temperature (HPHT). Skilled and experienced materials scientists and engineers study a variety of material
DNV GL has investigated major issues with external corrosion of flange faces, bolting and piping for various industries.
threats. The corrosion laboratory services cover material and corrosion technology – general and local corrosion, H 2 S sour service, coating degradation, materials compatibility, stress corrosion cracking, corrosion fatigue, thermal fatigue, creep, high-temperature corrosion, microbiologically-influenced corrosion (MIC corrosion), and fracture mechanics. DNV GL has investigated major issues with external corrosion of flange faces, bolting and piping for various industries.
Joint industry project DNV GL completed a joint industry project on CUI which, just like Corrosion Under Pipe Supports, can rapidly lead to serious piping damage, potentially leading to pipe failure. CUI is thought to account for 40% to 60% of pipework maintenance costs. The outcome of the JIP has resulted in a new
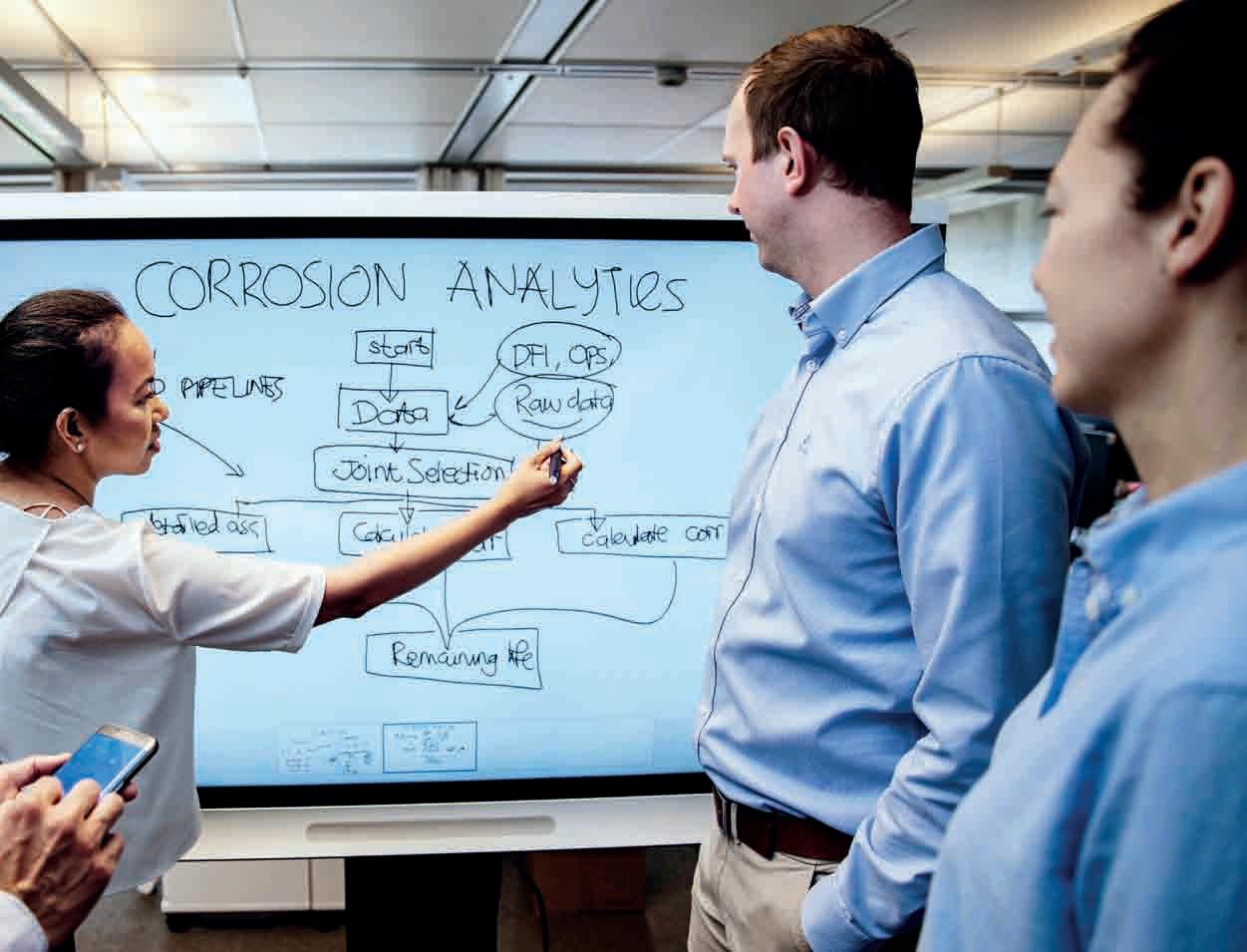
methodology designed to address the major safety threat and multi-billion-euro cost posed by CUI. Recommended Practice (RP) DNVGLRPG109 was developed in collaboration with several regulatory bodies, international oil and gas operators and major players in the supply chain to deliver a practical and cost-effective methodology for managing the threat of CUI and is setting a new standard for managing CUI risk. A digital tool, CUI Manager, has also been launched to support the implementation and use of the methodology. This tool applies machine learning to CUI data gathered from operators with the methodology from DNV GL’s Recommended Practice, to continuously assess and calculate the risk of CUI in process plants. According to estimations the tool can reduce the cost of CUI-related maintenance by up to 50%.
Choosing coatings The industry coats and paints vessels and pipework as a main defence against external corrosion. This can work well if the coating is carefully selected and qualified for site conditions. In some failures, a coating against atmospheric corrosion was used on cool pipework exposed to heavy condensation from a humid atmosphere, while in other cases an immersion-grade coating is required. Coating systems need inspecting regularly. Many operators have internal standards for assessing the severity of corrosion and coating degradation such as the ISO 4628.
Consistent approach To assess degrees of coating degradation and substrate surface rusting, the standards use a comparison library of pictures showing coatings and steel substrates with varying levels of damage. However, they do not address the depth of attack, and the severity judgement depends on the experience of inspection personnel. It is important to ensure a consistent approach throughout the analysis, which is why our laboratory uses trained assessors to conduct site surveys for external corrosion, CUI and CUPs. To address the major problems highlighted by corrosion DNV GL believes that a systematic, rigorous and detailed approach to material science supported by in-depth knowledge of applicable codes, standards and regulations with state-of-the-art corrosion laboratory and modelling tools is vital to address this key challenge for the industry.
i. dnvgl.com