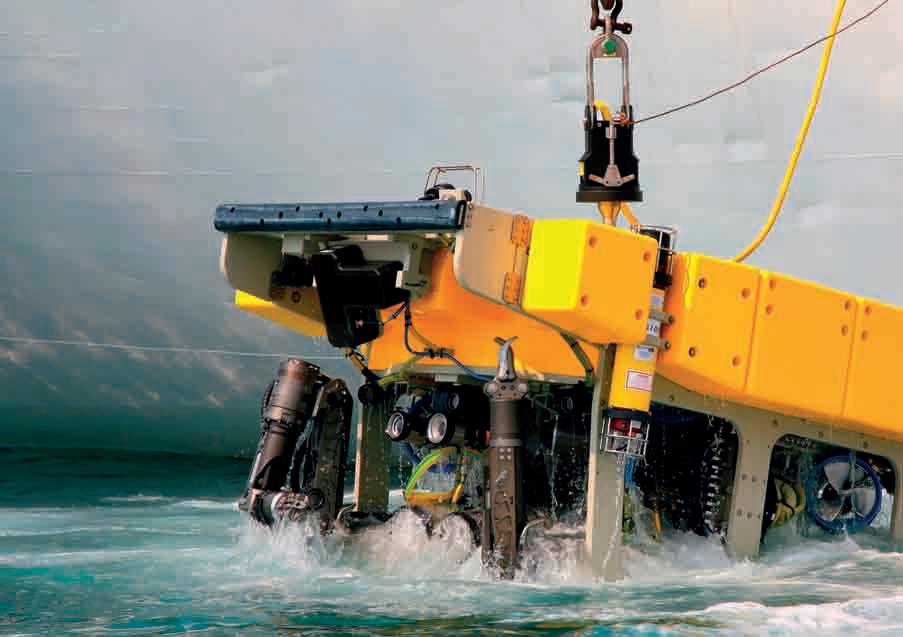
6 minute read
Hydraulic products in remotely operated underwater vehicle applications
Hydraulics power most industrial Work Class ROV’s primary functions including the thrusters, manipulators, and auxiliary tooling.
REMOTELY OPERATED VEHICLES (ROVS) PERFORM MOST UNDERWATER TASKS BEYOND THE DEPTH LIMITS OF COMMERCIAL DIVERS. THESE SUBSEA ROBOTS ARE WIDELY USED IN THE ENERGY INDUSTRY, MILITARY, AND DISASTER INVESTIGATION.
WORDS BY STEVE BARROW, SENIOR APPLICATIONS ENGINEER AT WANDFLUH OF AMERICA. ALL IMAGES COURTESY OF WANDFLUH.
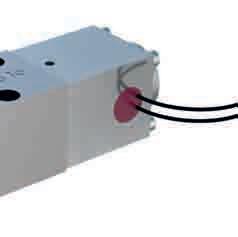

NG3-MINI proportional spool valve WDPFA03 with potted cables for easy installation.
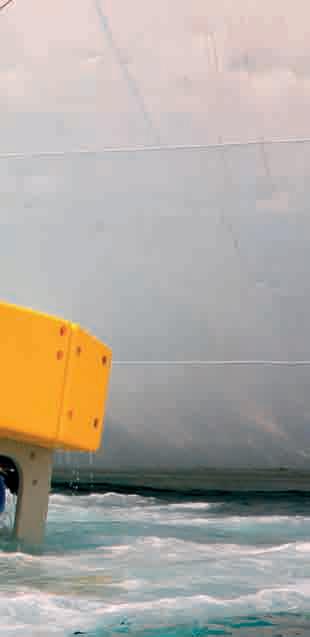

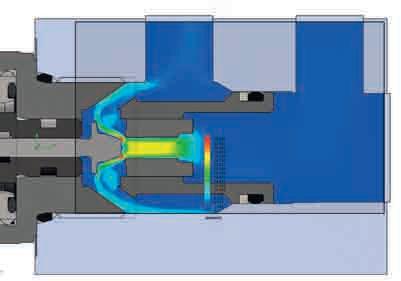
Valves designed for fluids with low viscosity and high water content.
Hydraulics power most industrial Work Class ROV’s primary functions including the thrusters, manipulators and auxiliary tooling. Electrical power is provided from the surface vessel to the ROV by means of an electrical ‘umbilical’ cable, which powers a hydraulic power unit (HPU), typically in the 150 to 250hp range. A proportional pressure relief cartridge is used to control the system’s pressure.
A paramount concern Vehicle weight must be kept at a minimum, so smaller hydraulic actuators are chosen to provide the best power to weight ratio. Specific hydraulic fluids are chosen for their tolerance to water ingression – an accepted inevitability – and the fluids used are often required to be environmentally friendly. ROVs are frequently required to remain submerged continuously for weeks to accomplish a task. If a system failure occurs and recovery of the ROV is necessary, approximately eight hours ars required to raise and return to a depth of 4,000m. This does not include the additional time needed to diagnose and make repairs while the vehicle is on deck. During this time, the entire vessel and crew may be brought to a stand-still if the ROV’s task is a critical function. The cost of this downtime for vessel and crew can be hundreds of thousands of euros, which may be billed back to the ROV operations company if they are liable for interruptions in service. Additionally, the extremely limited availability of spare parts in the middle of the ocean makes it clear that reliability is a paramount concern.
Reliable control Proportional spool valves with low hysteresis are most commonly used to control the precise movements of the ROV’s manipulators (robotic arms). The manipulators are very powerful – able to lift in excess of 225kg in air – but must have very precise control to allow the ROV to turn the delicate handles on subsea equipment. Wandfluh’s proportional directional control valves offer the ROV pilot reliable, delicate control with low hysteresis. The compact WDPFA03 or the NG6 proportional directional control valves WDPFA06 are most used for manipulator control and auxiliary tooling functions. Thrusters propel the ROV vertically and horizontally through the water. Up to eight thrusters, driven by individual hydraulic motors, are each controlled by a pair of proportional pressure reducing and relieving valves MVPPM33.
Ten million cycles The critical hydraulic equipment is not limited to the subsea vehicle. The host >>
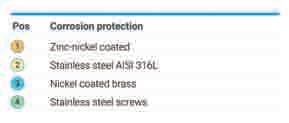
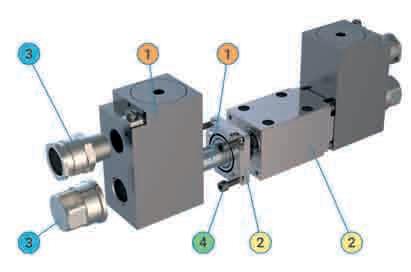
vessel must also have a Launch and Recovery System (LARS), high-tension winch and deck HPU. In addition to the reliability requirements, these components may also be located in corrosive and explosive environments. Wandfluh solenoids are rated for ten million cycles of service life. Wandfluh solenoids for ROV applications are wound in-house and modified according to the subsea specification standards. The solenoid tube assembly is constructed of the highest quality, magnetic materials. This construction offers the strongest, evenly distributed magnetic field at lower power levels, resulting in reduced hysteresis. Special modifications are made to the solenoid and housing to withstand the ambient pressure at depth, which can be in excess of 6,000psi. The electronics are also tested to ensure the ability to withstand pressure cycling, as the ROV repeatedly descends and returns to the surface.
Spool valves with special fluids The inherent design of a spool valve allows leakage around the spool to reduce friction, improving response time and performance. Due to tighter tolerances and precision machining, Wandfluh spool valves have lower leakage rates. Hence, lower leakage rates result in greater efficiency and fluid availability for other system functions. In turn, a smaller pump can be used providing additional cost savings. In recent years, industries are using more environmentally friendly hydraulic fluids. These fluids pose new challenges due to lower lubricity, reduced corrosion inhibitors and lower viscosity. Some of these fluids have very high water content, making the use of standard valves undesirable. To meet the new requirements, Wandfluh engineers researched new material options and developed new construction techniques. The result of their efforts is the Z595 series of valves. The internal components of Z595 valves utilise the highest grades of stainless steel and are compatible with fire resistant HFC and HFA fluids, as well as water-glycol based fluids with water contents as high as 95%. Additionally, the engineers optimised the spool design to offer higher resistance to cavitation.
Corrosion protected valves The solenoid valves aboard an ROV are typically housed in an oil-filled housing on top of the valve pack to prevent direct contact between the valves and water, however sometimes a design requires valves be directly exposed to the subsea environment. The ROV support equipment mounted to the deck of the surface vessel is also exposed directly to the harsh marine conditions. For valves directly in contact with these hostile conditions, Wandfluh offers special external coatings and stainless materials. These offerings are referred to as K8, K9 and K10, with an increasing level of protection respectively. K8 valves utilise a zinc-nickel coating on the valve and solenoid zinc-nickel coating on the valve and solenoid housing exterior and zinc coated fasteners. housing exterior and zinc coated fasteners. K8 valves rate very highly (>500 hours) in the K8 valves rate very highly (>500 hours) in the ISO 9227 salt spray test. This test creates a ISO 9227 salt spray test. This test creates a harsh corrosive environment to accelerate harsh corrosive environment to accelerate the formation of corrosion to help the formation of corrosion to help determine a material’s resistance determine a material’s resistance to corrosion. K9 valves use high-grade AISI 316L, acidresistant, stainless steel for all external components except the solenoid housing which Ks zinc-nickel coated. K9 valves have a superior rating n>1,000
K9 corrosion protection standard.
hours) in the ISO salt spray test. K10 valves offer the highest level of corrosion protection. All external elements of K10 valves, including the solenoid housing, are made of stainless materials. K10 valves share the superior rating in excess of 1,000 hours in the salt spray test.
Electronics Wandflu ‘s range of optionss extends into the electrical and electronics design as well. Many electrical connection styles are offered on the solenoid, including DIN/ISO 4400, Deutsch, AMP Jr. Timer, Phoenix connectors as well as flying leads. The broad range allows to select the best match for the specific requirements, whether it be minimising space, power saving options or full digital control. Electronics with LEDs are also available to allow rapid troubleshooting. In summary, Wandfluh offers a wide selectioe of products designed specifically for environments requiring high precision, durability, reliability and safety. The company offers a number of field-proven options that can be used as building blocks to create the perfect solution to any to create the perfect solution to any customer’s challenging application. customer’s challenging application.
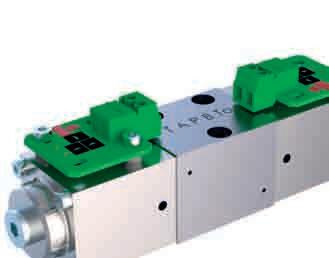
i. wandfluh.com wandfluh.com
NG3-MINI proportional spool valve WDPFA03 with connectors.
