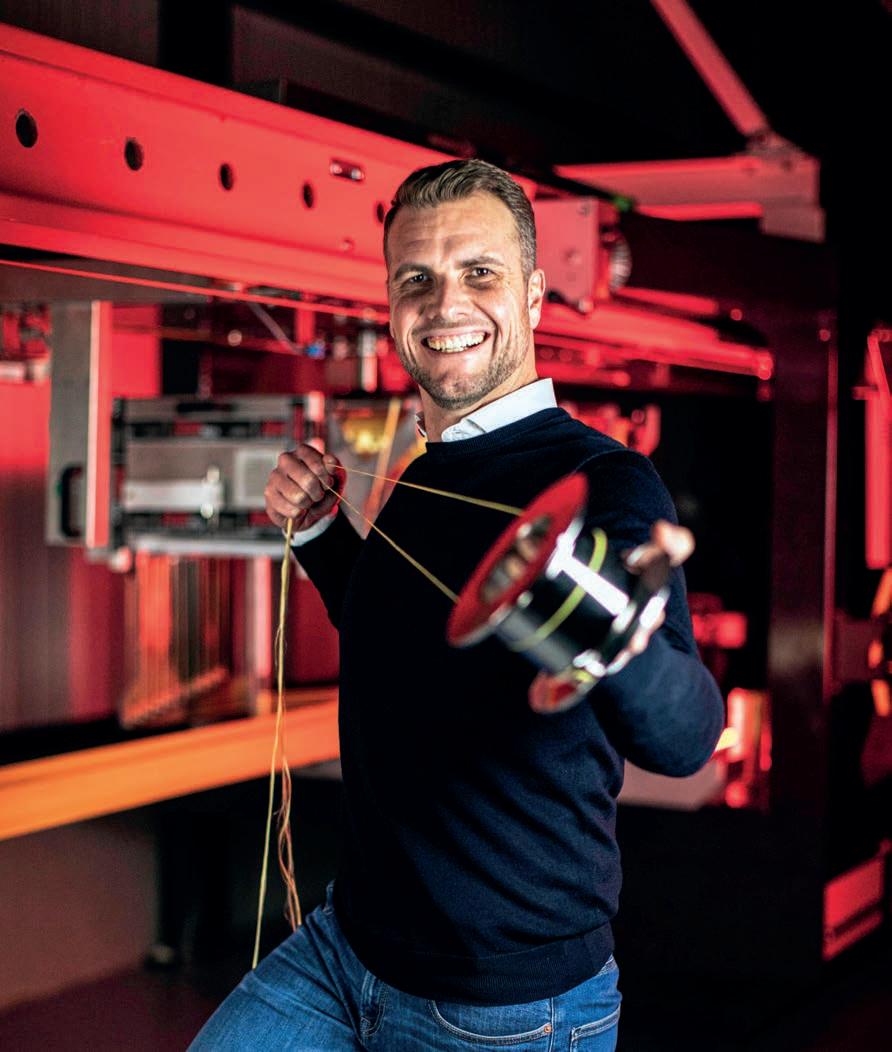
7 minute read
The strongest alternatve
The strongest alternative
CABLES ARE USED FOR MANY DIFFERENT THINGS IN THE OFFSHORE INDUSTRY. TODAY, STEEL IS USED IN MOST SITUATIONS. STEEL OBVIOUSLY HAS LOTS OF ADVANTAGES, THOUGH COMPANIES ARE NOW SHOWING GROWING INTEREST IN CABLES MADE FROM SYNTHETIC FIBRES.
ALL PHOTOS COURTESY OF FIBREMAX.
Duco Handgraaf, Sales & Marketing Manager at FibreMax: “Our cables are among the strongest alternatives for steel.”
Fibremax is a fast-growing company that produces fbre cables via the patented endless winding technology. These cables compete successfully with steel cables. Fibremax cables are 85% lower in weight, maintenance-free, and have a lifecycle that is at least fve tmes longer than cables with the same break load produced from steel. One can fnd the company’s cables, for instance in cranes, mining operatons, aerospace, and ofshore energy projects.
Endless winding
FibreMax originates from Smart Rigging, a company that fabricates and supplies lightweight yacht rigging. With the increasing size of yachts, the company was forced to produce thicker rigging products, also useful for industrial use. For this purpose, it was decided to establish the new brand FibreMax. For the producton of cables, FibreMax uses the endless winding method. “Endless winding,” explains Duco Handgraaf, Sales and Marketng Manager of FibreMax, “is a totally automated process of contnuous winding of parallel strands of fbres around two end ftngs untl the right cable strength or required cable stretch has been reached. Afer the required length has been programmed, the EWR (Endless Winding Robot) computer calculates the number of fbres and loops required for the specifed cable.”
All kinds of fbres
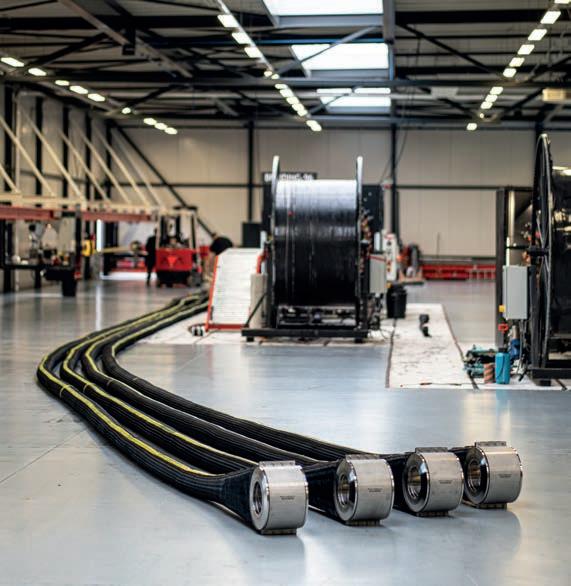
He contnues, “All fbres lie parallel in one line of equal length and the EWR during the winding process maintains the same tension in all fbres with an accuracy of 0,1%. This results in the highest break load, lowest stretch and diameter, with the use of less fbre and a smaller safety margin. It also ensures that cables are produced with high repeatability. When producing multple cables, we can guarantee that each of them will have exactly the same specifcatons.” According to Mr Handgraaf, the endless winding process yields yet another valuable advantage for customers. “The endless winding method can be applied to all kinds of fbres, so we produce cables from aramid, HMPE, PBO, and carbon. We can hence meet all the requirements from our customers, as they do not have to look for various suppliers for diferent types of cables. They come to us with a challenge, and we look for the best product to solve this.”
Heavy lift equipment
“Our frst customers in the industry were producers of on and ofshore cranes such as Liebherr, TTS-NMF, and Huisman. Our cables are among the strongest alternatves for steel,” Mr Handgraaf says, “making them partcularly useful for implementaton in heavy lif equipment. We can replace all current steel versions with an alternatve that is up to 85% lighter, lasts up to seven tmes longer, and requires no maintenance. Cranes are usually equipped with heavy steel plate or steel wire rope pendants and steel connectors. By using light-weight crane
FibreMax demonstrated in 2019 that their aramid cable is the strongest cable in the world.
pendants made from aramid, signifcant weight reducton over steel can be achieved with almost the same rigidity. It is important to realise that this weight reducton has advantages that go much further than just adding weight capacity. Booms can be made longer, constructon details can be downsized, the counterweight can be made lighter, service life is extended, and transport and installaton are easier and quicker, resultng in faster operatons. The reduced weight of the machinery furthermore enables the electrifcaton of cranes.”
Offshore mooring
FibreMax products are also found in mooring ofshore oil & gas assets, and the transiton towards renewable energy has >>
By using light-weight crane pendants made from aramid, a signifcant weight reduction over steel can be achieved with almost the same rigidity.
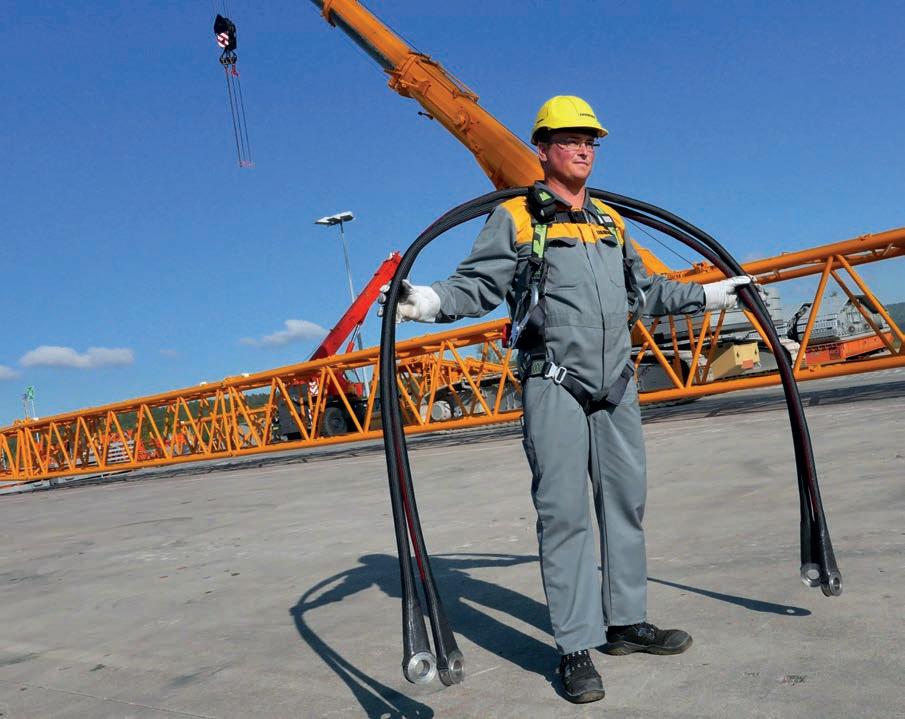
now opened up various interestng markets for the company. “For subsea use, we have our cables made of Dyneema DM20”, states Mr Handgraaf. “Dyneema DM20 is light, strong, and it can foat. Ofshore wind and wave energy are examples of green energy sources where we stand at the forefront of developments. Afer the development of windfarms in shallow water, the focus is at present shifing towards deeper water and foatng windfarms. We are currently involved in several TLP designs. Our lightweight Dyneema DM20 fbre mooring tendons ofer signifcant benefts compared with conventonal steel wire rope. Our Dyneema DM20 cables also play a role in marine energy power generators, with customers such as Minesto. Compared to steel ropes with the same break load, we achieve a 90% weight loss, while the diameter is 10% smaller. Compared with braided ropes, we stll ofer a 30% lower weight and a 30% smaller diameter. Due to the reduced weight, transport and handling are much easier and more cost-efectve as smaller vessels and cranes can be used. A higher payload for the TLP or a smaller/ lighter TLP constructon are yet other possibilites. Thanks to Dyneema DM20’s strength, maintenance is limited which is of course very useful for subsea purposes, along with the product’s longer lifespan.”
Closer to price of steel
The FibreMax cables are perhaps initally more expensive compared with steel ones but according to Mr Handgraaf, money can be saved when considering the entre product lifespan. “Although our product is more expensive compared to steel alternatves, our customers ultmately save money as lighter and smaller cranes can be used and the costs of cable maintenance decrease, as well as those of logistcs and handling. The longer cable life should also be considered.” Stll, the company contnuously searches for cost reducton. “Our goal is to get closer to the price of steel products and for this, we believe in

All fbres lie parallel in one line of equal length. The EWR during the winding process maintains an equal tension in all fbres with an accuracy of 0,1%. The offces and factories are fully powered by rooftop PV panels.
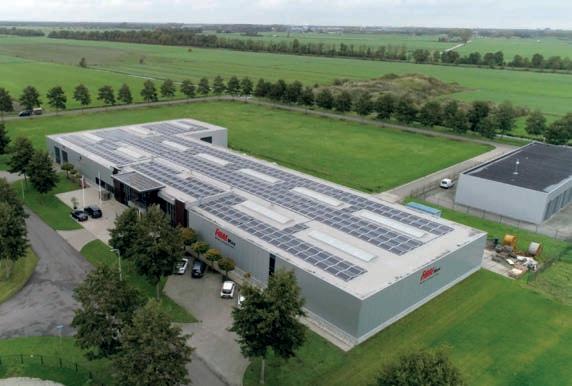
automatng our producton process. With our EWR, we can produce at a high speed with a constant high quality, which in the end results in a higher cost efciency.” Apart from extending the producton facilites with an additonal 2,400m2 (an expansion of 300%), the company recently also invested in a second upgraded EWR and a laser cutng robot. “Our new laser cutng robot is one of a kind”, comments Mr Handgraaf. “It will be used for the producton of end ftngs to replace the manual cutng, which can be a prety boring and tedious job.”
Bright future
The company’s expansion is a prelude to a bright looking future for FibreMax. “When I joined the company about four years ago,” Mr Handgraaf elaborates, “I notced a very positve vibe within the organisaton. With NPM Capital as one of our shareholders, we have a sound fnancial backbone. NPM Capital is also shareholder in heavy lif specialist Mammoet, so they are well aware of what is going on in the market. Their trust in us and in our products sparks confdence.” When speaking of a bright future, the company furthermore wants to contribute to a more sustainable environment. “As a supplier to the renewables industry, we indirectly promote energy transiton yet directly also put ample efort into reducing our ecological footprint”, Mr Handgraaf states. “All our products can be recycled. Our ofces and factories are fully powered by our own roofop PV panels. We prefer to make use of regional suppliers, which shortens our supply chain. Our aramid named Twaron, for example, comes from the Dutch Teijin producton facility, and Dyneema DM20 is supplied by Dutch company DSM.”
Lifespan of 35 years or more
One of the short-term challenges of FibreMax relates to the lifespan of their Dyneema DM20 cables. “We demonstrated in 2019 that our aramid cable really is the strongest cable in the world. We set a world record that year with a destructve test at DNV GL. The aramid cables were intended for a gigantc fy-jib for installing, among other things, ofshore wind turbines. The cables had to be as light and durable as possible, with a minimum strength of 16,500kN.A world record of 17.020kN was achieved at the very frst atempt.” For subsea cables, the lifespan of our products is essental and we are convinced that our Dyneema DM20 cables will last at least 35 years. This means that they do not have to be replaced during the technical lifetme of TLP ofshore turbines. Testng is currently ongoing to get this lifespan of 35 years ofcially proved and certfed. We hope this project will be ready mid-2021. This would really boost the acceptance of our products”, Mr Handgraaf concludes.