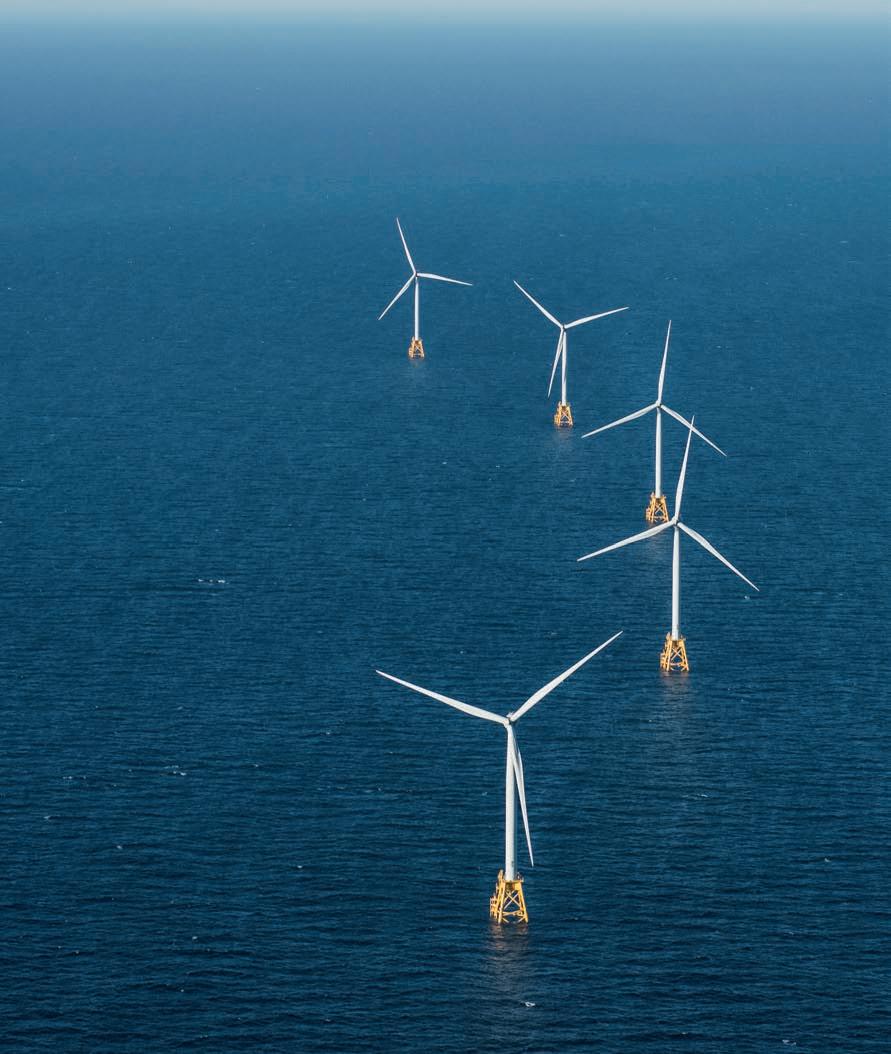
8 minute read
Inspired by nature
Composite joint for ofshore jackets
Monopiles and jackets are used for the foundation of bottom fxed ofshore wind turbines. The steel welded TKY joints used for the assembly of jackets form a weak spot in the strength and durability of this type of construction. Start-up company Tree Composites has developed a joint made of composites that eliminates this weakness.
ALL PHOTOS COURTESY OF TREE COMPOSITES, UNLESS STATED OTHERWISE.
Maxim Segeren is Managing Director and Co-founder of the young company, and we talk with him about their innovative solution. He became involved in the ofshore industry during his study at Delft University of Technology (TUD), where he earned his MSc degree in ofshore engineering with a focus on ofshore wind jackets, and a PhD degree in civil engineering with the slip joint connection for ofshore wind turbines. After his PhD, he remained involved with the TUD. “After promoting,” he explains, “I stayed at the university where I became involved in forming consortia between the industry and science aiming at the development of innovations within ofshore wind. One of those innovations was a wrapped composite joint that today is referred to as the TC Joint.”
TC Joints versus steel welded joints
According to Mr Segeren, a jacket has an excellent weight/rigidity ratio and this is why they are technically the best foundation for ofshore wind turbines. “Despite jackets being the better solution, monopiles are dominating the market, even when they are much heavier than jackets”, he states. “One of the reasons for this is the higher price of jackets and the longer production time caused by the complex welding of the multi-membered joints. The weld also causes local stress concentrations that can reduce the fatigue resistance by 10 to 100 times. To guarantee a lifespan of these complex welds of 25
To guarantee a lifespan of jackets of 25 years or longer, the thickness of steel used in TKY joints is increased locally in the order of 300%.
years or longer, the thickness of steel is increased locally in the order of 300%, which means extra use of steel.” Mr Segeren continues, “The improvement of our composite joint compared to welding steel joints is that the load is transferred through the surface of a dedicated composite wrap, and not through the smaller surface of the welds which is limited to the wall thickness. The composite also protects the steel against corrosion. Our wrapped composite joint is made by the lamination of glass fbres on the individual steel tubes. The brace members (diagonals) are bonded to the chord members (legs) through a coupling formed by composite wrapping. This provides outstanding bonding strength and fawless quality. The composite wrap is tailored in length and thickness to deal with static and dynamic loads transferred by the joint. The optimised, nature-like shape of the composite wrap with increasing thickness towards the root of the joint reduces the stress concentration in the composite material and bonded interface, thereby solving issues in fatigue prone/driven design. As the lifespan of a jacket highly depends on that of the joints, the TC Joint makes the entire construction of the jacket longer lasting. Wrapped composite joints can also acquire higher dimensional tolerances than welds due to omission of distortions by welding heat input. Another advantage of the TC Joint is that it reduces the amount of steel used by 30% to 60% as a result of the increased fatigue resistance. The composite joint itself is lighter than steel ones and as no welding is needed, there is no need for thick local cans and overdesigned global thicknesses of the tubes. This steel reduction also helps to reduce CO2 emissions. Finally, the acceleration of jackets production by prefabrication of the joints is feasible by factor two to three, as the joint omits complex welding activities onsite and does not require the application of an additional coating to protect the steel against corrosion.”
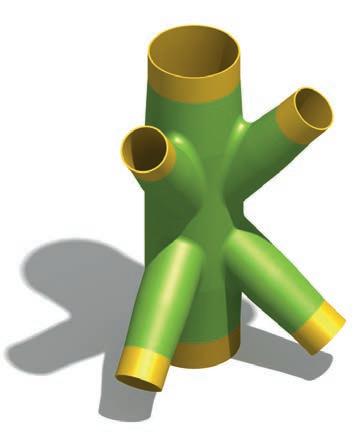
Old tree
With the frst prototype built in 2017 at Versteden, a close collaboration with them followed with over 100 tests executed at TU Delft to perfect the technique. “When I heard about the composite joint, I was sceptical about the concept of a structural joint made by wrapping material around individual tubes, as I had tried to wrap a broken pencil myself in my younger years,” Mr Segeren admits, “however, seeing is believing. The successful laboratory tests created enthusiasm and a drive to further develop this innovative concept and its many advantages compared with steel joints into a commercial product. Parties that could incorporate this innovation in their core business were non-existing, as this unique disruptive technique combines the two separate worlds of composites and steel structures. In other products such as aircraft wings and turbine blades, a combination of composite and steel is not uncommon, however the specifc application and creation of a load transfer in a structural joint of ofshore jackets by replacing traditional complex welds is a completely new concept.” In 2020, a dedicated company focussing on design and manufacturing of composite joints called Tree Composites was founded to develop the technique further. “We named the company Tree Composites after the inspiration by nature”, Mr Segeren elaborates. The inventor of the concept, Assistant Professor at TU Delft Marko Pavlovic, became inspired by an old tree in his hometown near Belgrade. The local community placed steel rods on branches of the tree to >>

Maxim Segeren is Managing Director of Tree Composites.
The optimised, nature-like shape of the composite wrap with increasing thickness towards the root of joint reduces the stress concentration in the composite material and bonded interface, thereby solving issues in fatigue prone/driven design.
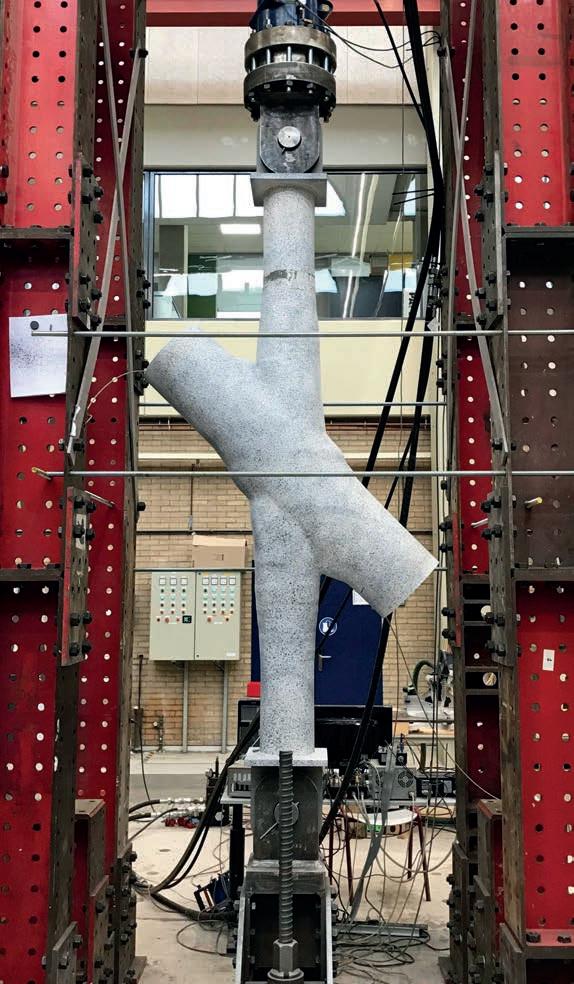
In the combination of steel and composite, it is always the steel that shows failure or behaviour outside design limits during testing. Assistant Professor at TU Delft, Marko Pavlovic became inspired by an old tree in his hometown near Belgrade.
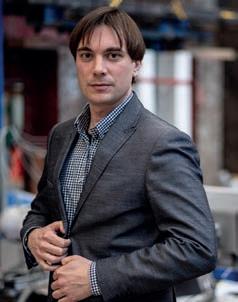
Maxim Segeren – Managing Director of Tree Composites.
extend its lifetime. A tree reacts to the loads it is subjected to, and this tree can grow additional fbres at locations where they are needed. Mr Pavlovic noticed that the tree grew over and around the steel tubulars, creating a structural connection. Based on this observation, he came up with the idea of the wrapped composite joint. At the end of 2020, just a few months after founding the company, DNV provided the statement of feasibility for the composite joints, marking an important milestone.”
WrapNode-I
In May 2021, the project WrapNode-I started with TU Delft as research partner and large parties joined the consortium such as HSM Ofshore, Smulders, Siemens Gamesa, Shell, AOC, BuFA, Salzgitter Renewables, and Enersea. “The WrapNode-I project is part of GROW”, Mr Segeren voices. “GROW stands for Growth through Research, development & demonstration in Ofshore Wind. It is a joint research programme in ofshore wind that initiates research and accelerates innovations. The Netherland Enterprise Agency (RVO) fnancially backs the project through a subsidy. Aim of WrapNode-I is to test the efects of
According to Mr Segeren, despite jackets being the better solution, monopiles are dominating the market, even when they are much heavier than jackets.
scale and other infuences such as the ofshore environment. So far with success, as in the combination of steel and composite it is always the steel that shows failure or behaviour outside design limits. Next to this R&D project, we are preparing pilot projects and we hope that this will result in a full-scale ofshore project soon. WrapNode-I will run until 2023 and will be followed by the next phase, WrapNode-II, in which a full-scale onshore demonstration jacket will be realised. After this, we aim to have a full-scale jacket ofshore in 2025 as the frst pilot project for ofshore wind. The major challenge we face with the composite joint is not developing the technique, but introducing this gamechanger in the conservative ofshore wind industry.”
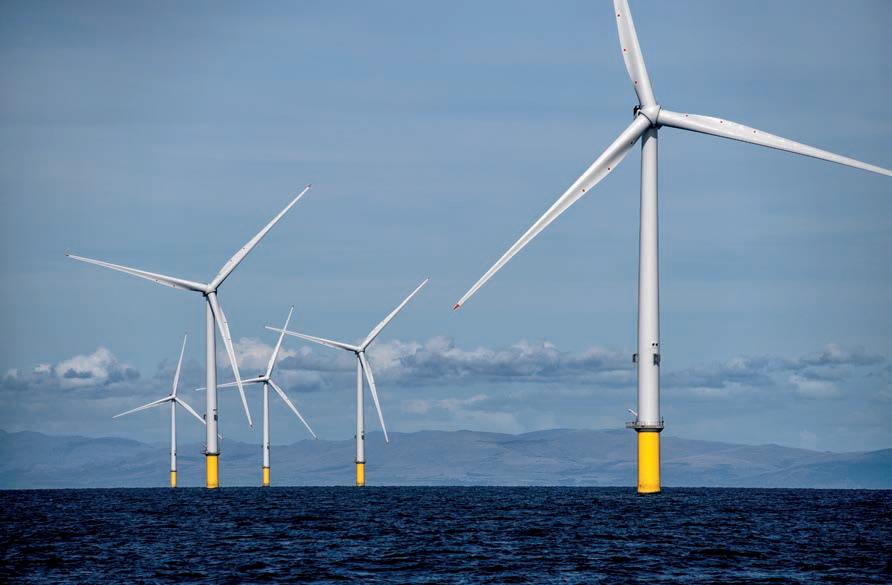
Standardisation
“Today, the construction of jackets without using our TC Joints is still more expensive compared to that of steel monopiles,” Mr Segeren explains, “however, the construction of jackets using TC Joints will go much faster, and with the Dutch 2030 goals in mind for the realisation of ofshore windfarms we need to speed things up. Time and production capacity will become an important item in realising these goals. What drives us is that we strongly believe we contribute to the acceleration of the energy transition with our joints. Our aim is to accelerate the production of the jacket by the introduction of the TC Joint from 1 to 2/3 jackets a week. Achieving this will make it feasible to reach the renewable energy goals. In the Dutch wind industry, there are initiatives that are in favour of a restriction in size of the turbines and with a focus on standardisation and industrialisation. If that happens, an interesting idea arises to extend permits to 60 years and having a jacket foundation of a lifetime of 60 years that is feasible when using TC joints for a similar price. With lifetimes of current wind turbines of 25 to 30 years, a new turbine could replace the frst after its lifetime without having to install a new foundation.” For Mr Segeren, the Tree Composites story has only just begun. According to him, once the concept has reached full adoption in the market, it can expand globally in dedicated production yards for jackets assembled with TCJs produced on the spot or prefabricated ones. “This sounds ambitious indeed and it will be challenging, but we believe in our solution. We are a motivated, passionate, and thorough team. We are eager to listen, learn, and improve, and hope to attract potential partners with our enthusiasm about the many pros of our solution”, Mr Segeren concludes.
Photo courtesy of Ørsted.