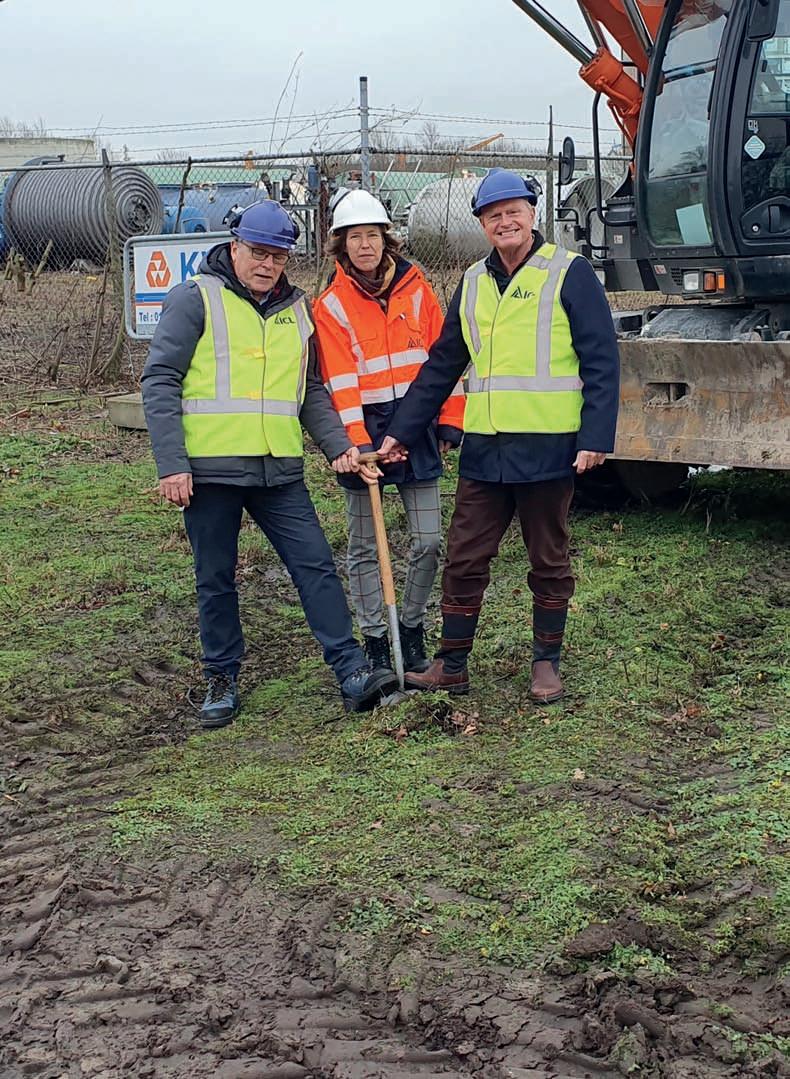
3 minute read
First spade in the ground
FIrSt SPAde In the ground. From LeFt to rIght, toIne JAnSSen, PoLyStyreneLooP PLAnt mAnAger, SASkIA gooLe, SIte-mAnAger ICL – IP terneuzen And LeIn tAnge, dIreCtor PoLyStyreneLooP CooPerAtIve.
A start was made with the new common entrance road for PolyStyreneLoop and ICL-IP.
PolyStyreneLoop Cooperative will build the plant as PolyStyreneLoop in Terneuzen, Netherlands. The company aims to set up a demonstration plant for recycling polystyrene foam construction waste (both EPS and XPS) containing the legacy chemical HBCD and (H)CFC’s. It will separate and destruct the obtained HBCD and will recycle and sell polystyrene beads (PS) compliant to the POP regulation described in the Basel Convention. The separated HBCD, will be destroyed and the bromine recovered in the Bromine recovery unit (BRU) based at ICL, Terneuzen. This phase 1 initiative is about demonstrating the viability of recycling this construction waste and when successful, a roll-out to different locations in Europe is foreseen.
Upcycling The flame retardant HBCD, used in foam insulation boards for decades, is now considered a contaminant. This means that millions of tons of PS foam waste can no longer be regularly recycled. A best practice for the handling of this waste is needed. With the CreaSolv Process used by PolyStyreneLoop, an industry-scale recycling process for PS foam demolition waste containing HBCD will be developed. This technology has been accepted by the UNEP Basel Convention as a best available recycling technology to handle HBCD waste.
The PolyStyreneLoop Cooperative now has more than 70 members and supporters from 18 EU countries, representing the entire polystyrene foam value chain. It is a new model for value chain cooperation in recycling. EPS and XPS demolition waste coming from buildings that were insulated with EPS/XPS before August 2015 all contain a now banned POP substance, rendering all this EPS unrecyclable. Members of the cooperative from the recycling and demolition sector collect and pre-treat the material before it is treated by PolyStyreneLoop, while members from the raw material supply branch will take the 100% recycled PS and will use it again in construction applications, as feedstock for extrusion of EPS beads, or via continuous XPS foaming. It is the first time in Europe that a two-step solvent upcycling factory is realised. The process is a solvent-based purification and therefore physical recycling.
Pre-treatment technology Plastic wastes are selectively dissolved using a specific proprietary solvent formulation. This dissolution is a physical
uPCyLIng to hAndLe wASte.
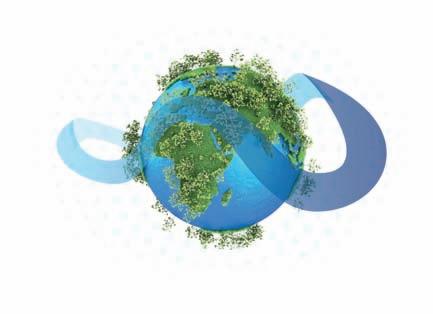
separation process. It is a pre-treatment technology, which has the potential to recover polystyrene and separate them from legislated additives (like HBCD). The process consists of three steps. Steps 1 and 2 are pre-treatment for step 3. First, the PS foam waste is dissolved in tanks containing a PS-specific liquid. The solid impurities (like adhesives, dirt and cement) are separated through filtration and then incinerated. Next, another liquid is added, which transforms the PS into a gel, while the additive (HBCD) stays in the remaining liquid. The PS gel is then separated from the process liquids. Once cleaned, this gel is transferred via a devolatiser and extruder into granulated polymer polystyrene. The liquid, still containing the additive, is distilled and re-used in a closed loop while the additive (HBCD) remains as sludge. This process is followed by the destruction of the HBCD additive within the sludge in a high temperature waste incineration at 1,100 ˚C. During the last step, the elemental bromine, used for modern flame retardants, is recovered and can be reused to produce new products, thus closing the bromine loop. The applied technology turns PS foam waste into new highquality raw material. During the recycling process, all impurities, such as cement or other construction residues, as well as the flame retardant HBCD are safely removed and destroyed, while the valuable polystyrene and bromine are recovered.
i. polystyreneloop.org
