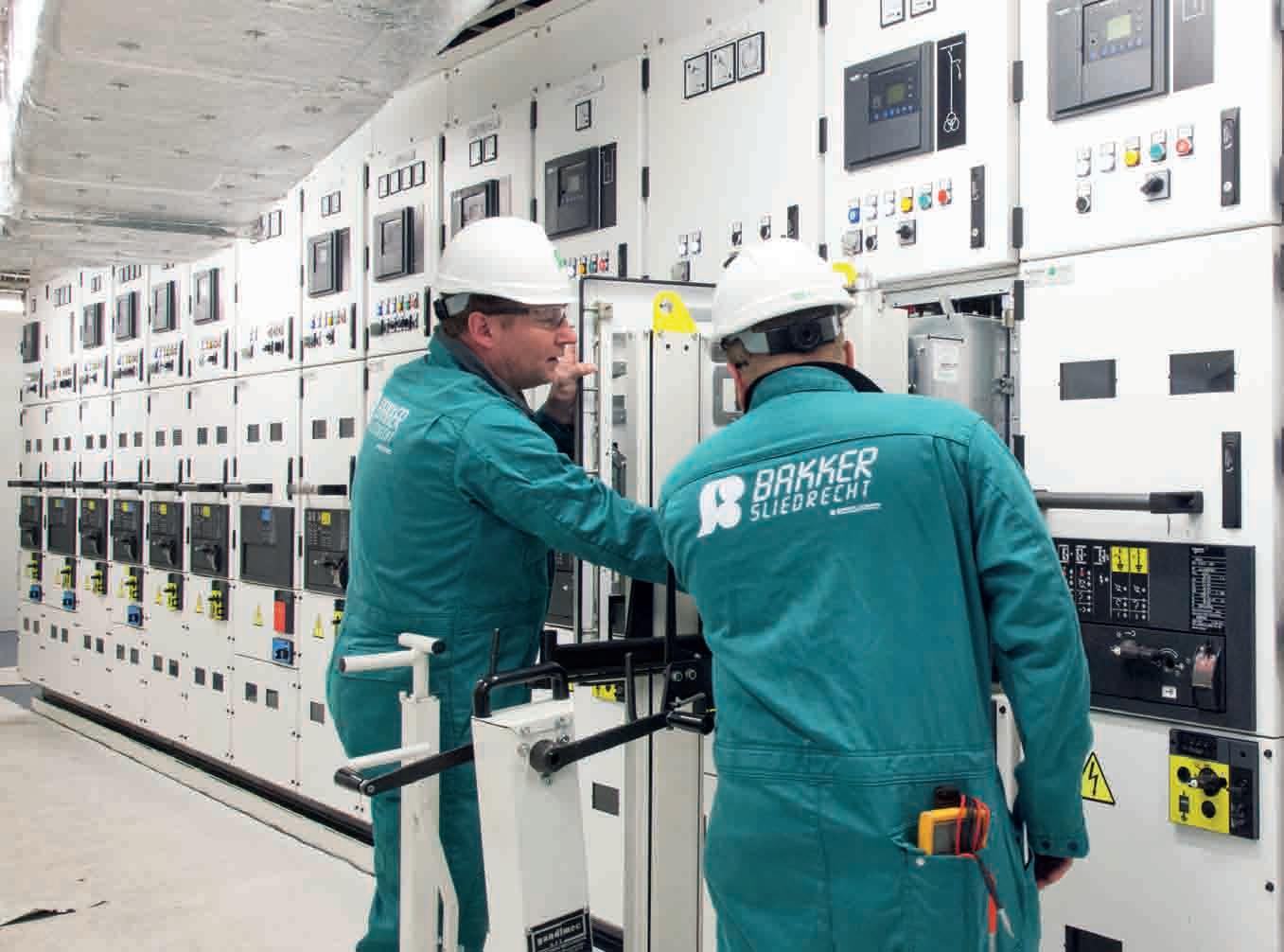
4 minute read
innovation Bakker Sliedrecht offers a new approach to maintenance
Bakker Sliedrecht is converting from time-based maintenance to condition-based maintenance.
New approach to maintenance
BAKKER SLIEDRECHT IS SWITCHING FROM TIME-BASED TO CONDITIONBASED MAINTENANCE OF MODULAR FREQUENCY CONVERTERS.
ALL PHOTOS COURTESY OF BAKKER SLIEDRECHT. I t is not the age, but the actual ageing that should be leading when replacing modular frequency converters, according to dredging and offshore system integrator Bakker Sliedrecht. The company is changing its approach from time-based to conditionbased maintenance, and the first offshore crane ship is already being successfully maintained in this way. Vessels with electrically-driven motors, but also cranes, terminals, pumps, and rollers use modular frequency converters to control their speed and power. Each frequency converter contains a capacitor bank in which the capacitors are subject to ageing. Replacing them is a time-consuming job. It can take between seven and eight hours to replace the capacitors of a single module
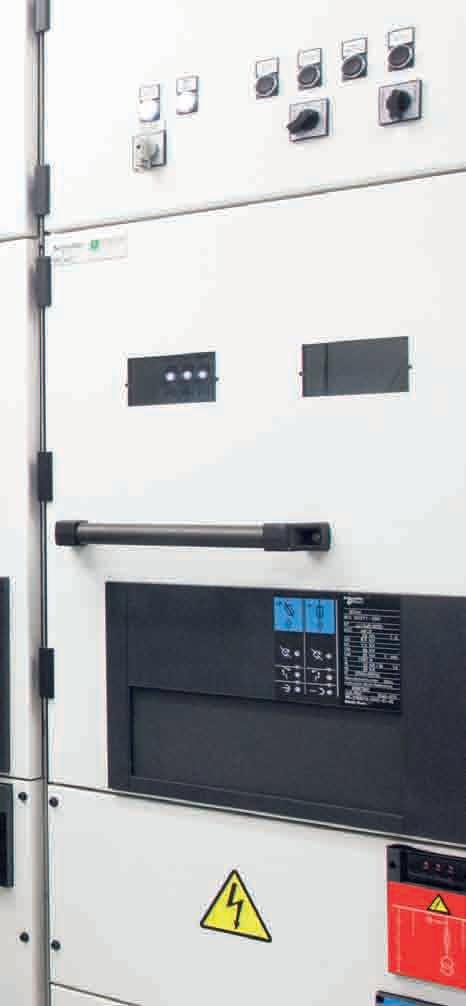
Replacing modular frequency converters is a time-consuming job. Condition monitoring allows shipowners to schedule maintenance.
and the average vessel has dozens of modules on board. By monitoring their condition, shipowners are able to schedule maintenance for a time most suitable to them. This results in significant cost-savings compared to ad hoc repairs. Most companies currently use time-based maintenance in which maintenance is based on the manufacturer’s prescribed replacement period, for instance nine years. This replacement period is based on the most severe conditions imaginable, not on the actual ageing of the capacitors. And to be on the safe side, maintenance is usually carried out in advance of the replacement period deadline, usually coinciding with other maintenance on board to limit the amount of down-time for the vessel.
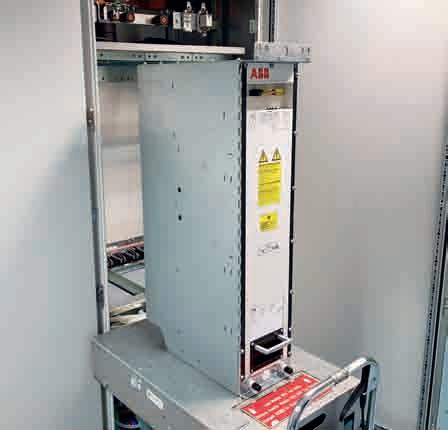
Preventing potential faults Bakker Sliedrecht specialises in preventive maintenance. Preventive maintenance consists of condition-based inspections. Service engineers can survey the condition of the installations during inspection. “Together with our clients, we draw up a detailed and tailored preventive maintenance plan based upon their requested availability and reliability”, states Arend van der Velde, Head of Technology at Bakker Sliedrecht. “Our wide-ranging knowledge of systems combined with specific product knowledge ensures that our technicians are able to eliminate the causes of potential faults. Preventive maintenance results in lower risks, lower costs, and higher returns for our clients.” The company has recently started condition monitoring of modular frequency converters. The capacitor bank of one module per cabinet is measured for inspection. By doing this periodically, it is possible to determine the progression of ageing and to plan a replacement moment based on the actual condition of the capacitors. “Depending on different parameters such as current load, temperature, and voltage, capacitors might not last much longer than the prescribed replacement period, while others could last years longer”, explains Mr Van der Velde. “Condition-based maintenance can offer significant savings in terms of postponement of recommended maintenance and replacement of components. Shipowners can limit downtime and its associated costs , and execute corrective maintenance.”
Predicted ageing Bakker Sliedrecht is collecting data that shows how the ageing curve proceeds. By projecting this on the measured data, the ageing over time can be predicted. Furthermore, prolonged downtime of the frequency converters also causes the ageing of the capacitor bank, which is not taken into account in time-based maintenance schedules. The condition monitoring of the frequency converters takes place at the same time as the maintenance intervals recommended by the manufacturer. The client can exchange one of the modules with a spare one and send it off to Bakker Sliedrecht. “We prefer to carry out the inspection of the module in our workshop”, comments Mr Van der Velde. This is because we have available all equipment for testing both before and after the inspection. Once the inspection is done, the module is returned and can be replaced by the customer at a later date.” Depending on the module’s condition, Bakker Sliedrecht can advise on the inspection frequency.
Replacing when suitable The advantages of condition-based maintenance over time-based maintenance are clear. Actual ageing is taken into account, so replacement is in most cases delayed in comparison to the estimate of the manufacturer’s prescribed replacement period used in time-based maintenance. As a result, replacements can be scheduled at a more convenient time. “We have decided to inspect more components inside the frequency converter modules. We have to open the module for inspection anyway, so it makes sense to test other components at the same time”, reveals Mr Van der Velde. “We have started using condition-based maintenance of frequency converters on an offshore crane vessel and it is being satisfactorily applied. We are already seeing a lot of interest in this initiative of condition-based maintenance from within the maritime sector.”