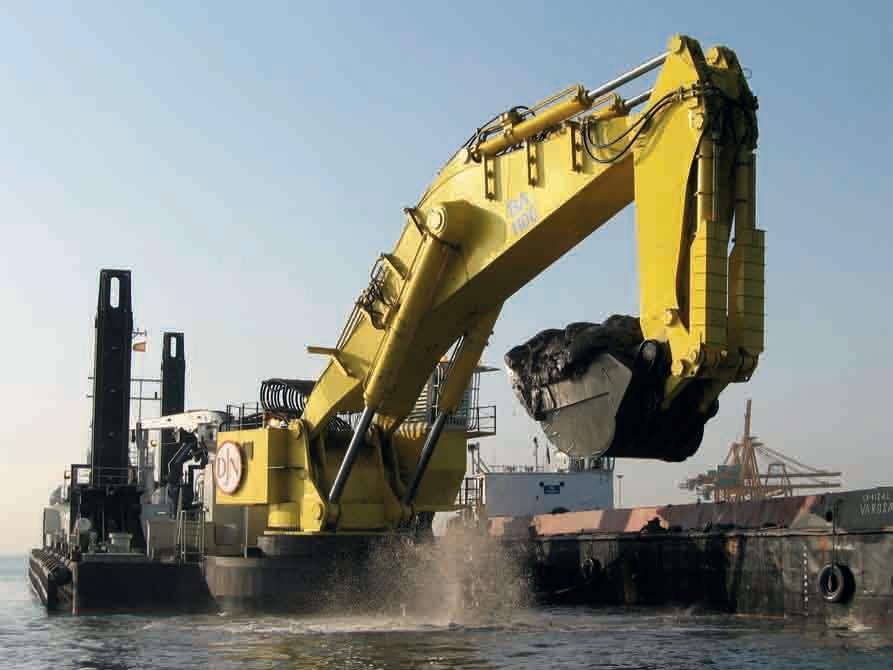
8 minute read
Haptics and automation in subsea industries – Bachmann
The remote control of sub-sea robots is very difficult for the human operator, due to the unpredictable environments, limited visual and haptic feedback, and slow vehicle dynamics.
Haptics and automation in subsea industries
“HAPTIC FEEDBACK CREATES AWARENESS OF WHAT A MACHINE IS DOING, GIVING THE HUMAN OPERATOR INSIGHT INTO HOW THE MACHINE IS BEHAVING.” ROEL KUIPER – RESEARCH & Development Engineer at Dutch subsea specialist Seatools – is talking about the potential benefits to be gained from haptic feedback in the challenging environment of the subsea world.
Mr kuiper goes on to state that the sense of touch is engrained into the very foundation of how we interact with our surroundings. “We touch and feel everything”, he says. “By picking up a coffee cup, for example, we know if it is full or empty. And then we can move that cup without spilling the coffee.” This tactile ability is so innately wired into our behaviour that we go through our daily lives not giving it a second thought.
However, in a modern world where (automated) machines are playing an evermore important role in our lives, haptic feedback is most definitely a subject that we need to be paying more attention to. “As soon as machines perform operations, we are eliminating haptic feedback. But, in doing this, we are making it more difficult for ourselves to control these machines.” Mr Kuiper’s point here is that, haptic feedback gives us the possibility to regain the control of machine operations; the outcome of this will have major effects on productivity, training and safety of operations.
Muddy or rocky? Turning our attention back to Mr Kuiper’s involvement in this fascinating subject, he has spent his entire academic career studying haptics in the maritime subsea industry. His first contact with Seatools was in 2009, as an intern during his Offshore Engineering company internship while studying at the University of Technology Delft. This focused on developing a simulator for a backhoe dredger. “My work included creating software protection for the simulator and building haptic feedback into the joystick controls, allowing the human operator to actually feel what was happening. First, when the machine makes contact with the seabed. Second, the amount of force required to move through the seabed – for example, is it muddy or is it rocky? And third, if the excavator bucket is stuck, on a boulder, for instance.”
Rare earth minerals After graduating, Mr Kuiper continued his study with a double Master’s between 2010 and 2012, also at University of Technology Delft and also in association with Seatools. The first of these Master’s followed the subsea track of offshore engineering by investigating the rock yielded from subsea mining, and the amount of energy required to mine and process it. The second Master’s, in mechanical engineering on the biorobotics track, focused more on the automation of the human subsea robot interface. Once again this required the construction of a haptic feedback simulator.
Straight off the back of his double Master’s, Mr Kuiper continued his work with haptic feedback in the subsea mining industry by taking on a PhD in 2012. “This is definitely an interesting new market with a lot of potential – in particular for rare earth mineral mining – but it’s still on the edge of economic and technical feasibility. The idea for this PhD was to use haptic feedback to assist the human operator even further with more advanced automation”, he says, highlighting the fact that it is possible to generate haptic feedback on a joystick to generate force feedback where the controller gives suggestions about what sort of input the operator has to provide.
Linking research with industry A continual presence running throughout Mr Kuiper’s academic studies has been Bachmann equipment within the simulator controllers forming a link between the two worlds of research and industry. “The Bachmann controller is powerful enough to enable the full dynamic model to run in real time, in addition to the haptic feedback algorithm based on the position and forces >>
Controller
Hoisting force
Cutting force
The TriaR is a 3-DoF force-reflecting joystick, designed by Roel Kuiper to explore control possibilities for subsea telemanipulation.
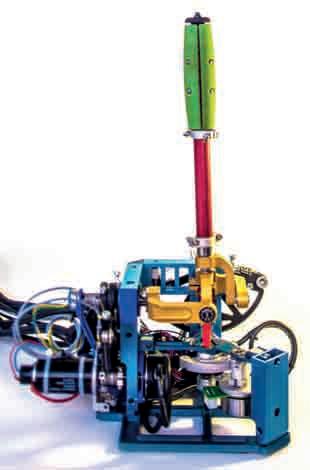
of the excavator.” The high frequencies used by the Bachmann controller are of particular benefit, he explains. “This is very helpful because the haptic feedback going back to the human operator needs to be at least 1,000Hz to ensure that the force algorithm is stable.”
The subject of increasing automation is another of the common themes in Mr Kuiper’s academic career. Moreover, it is perhaps one of the biggest industrial trends to take place in recent decades. So how does Mr Kuiper see the future role of haptic feedback in automated subsea operations? “You have to remember that this is an extremely harsh environment with no visibility and – due to costs – with limited sensors. You only have the sensors that you definitely need to do the task; never a side view or a 3D scanning camera to give you general feedback. The speed of the machine is also a challenge – the human operator has to predict what the machine will be doing in a matter of seconds ahead. Furthermore, the difficulty in controlling these machines is how to deal with the unexpected. There are no sensors for that.”
“As soon as machines perform operations, we are eliminating haptic feedback. But, in doing this, we are making it more difficult for ourselves to control these machines.”

Towards full automation Despite the challenges posed by the unpredictability of the subsea environment, automation by haptic feedback might be a solution for full automation in the future, he continues. “But we are not there yet. This is because, at the moment, a human is better at making the key decisions rather than the machine.” In others words, although a computer always pays attention and is never tired, it can still make mistakes. The reason for this difference between human and machine is best described by the German term fingerspitzengefuhl, which is a form of instinctive situational awareness. “It will take a lot of effort to be fully automated, but by incorporating more of this feeling into operations, we are taking small steps towards the point of full automation.” The advantages of using haptic feedback simulators in the subsea industry are numerous, as Mr Kuiper’s academic studies, and now professional career at Seatools, is showing. Existing markets can be made more productive and more effective through simulator training and semi-automated operations. And, most notably, this development goes hand-in-hand with an increase in safety awareness. Looking further into the future, this subject will play a significant role in the exploration and profitability of new and exciting markets, too.
i. www.bachmann.info
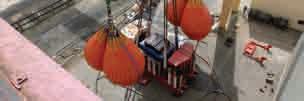
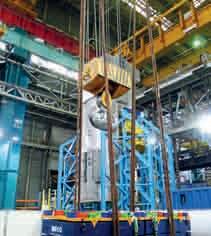
Diesel and gas engine components 39.000 di erent parts available from stock! Diesel and gas engine components 39.000 di erent parts available from stock!
39.000 di erent parts available from stock! 39.000 di erent parts available from stock! Diesel and gas engine components Diesel and gas engine components Diesel and gas engine components > hoisting equipment > wire ropes > cranes > rigging > fall arrest equipment > hydraulic jacks > chains and accesoiries > inspection > certification > dynamic loadtesting
39.000 di erent Vlissingen-Oost (NL) parts available 39.000 di erent Temse (Belgium)Rilland (NL)
for the Best Performance for the Best Performance from stock! parts available from stock! P.O. box 80 NL - 4450 AB Heinkenszand Groenlandweg 4, Harbor nr. 4056 4455 SN Vlissingen-Oost - NL Liftal NV Industriezone TTS Duitslandstraat 4 B - 9140 Temse De Poort 15 NL - 4411 PB Rilland
Phone: +31 (0)118 488 450 E-mail: vlissingen@liftal.com Phone: +31 (0)113 571 523 E-mail: rilland@liftal.com Phone: +32 (0)3 710 1182 E-mail: temse@liftal.com
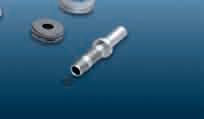
CYLINDER HEADS (COMPONENTS) | INDUSTRIAL SPRINGS | FUEL EQUIPMENT | CYLINDER HEADS (COMPONENTS) | INDUSTRIAL SPRINGS | FUEL EQUIPMENT | for the Best Performance PISTONS (PINS,RINGS) | LINERS & ANTI-POLISHING RINGS | BEARINGS | STUDS, NUTS & BOLTS | GASKETS, O-RINGS & SEALINGSETS | ELECTRICAL PARTS for the Best Performance PISTONS (PINS,RINGS) | LINERS & ANTI-POLISHING RINGS | BEARINGS | STUDS, NUTS & BOLTS | GASKETS, O-RINGS & SEALINGSETS | ELECTRICAL PARTS
CYLINDER HEADS (COMPONENTS) the Best Performance | CYLINDER HEADS (COMPONENTS) | INDUSTRIAL SPRINGS INDUSTRIAL SPRINGS | FUEL EQUIPMENT | for the Best Performance PISTONS (PINS,RINGS) | LINERS & ANTI-POLISHING RINGS STUDS, NUTS & BOLTS | GASKETS, O-RINGS & SEALINGSETS Daltonstraat 4 | 3335 LR Zwijndrecht | The Netherlands | +31 (0)180 412 133 | sales@thbverhoef.com PISTONS (PINS,RINGS) | LINERS & ANTI-POLISHING RINGS | BEARINGS | STUDS, NUTS & BOLTS | GASKETS, O-RINGS & SEALINGSETS | ELECTRICAL PARTS Daltonstraat 4 | 3335 LR Zwijndrecht | The Netherlands | +31 (0)180 412 133 for the Best Performance CYLINDER HEADS (COMPONENTS) | INDUSTRIAL SPRINGS | FUEL EQUIPMENT | CYLINDER HEADS (COMPONENTS) | INDUSTRIAL SPRINGS | LINERS & ANTI-POLISHING RINGS | BEARINGS | PISTONS (PINS,RINGS) | LINERS & ANTI-POLISHING RINGS | GASKETS, O-RINGS & SEALINGSETS | STUDS, NUTS & BOLTS | GASKETS, O-RINGS & SEALINGSETS CYLINDER HEADS (COMPONENTS) | INDUSTRIAL SPRINGS | FUEL EQUIPMENT ELECTRICAL PARTS PISTONS (PINS,RINGS) | LINERS & ANTI-POLISHING RINGS | BEARINGS Daltonstraat 4 Daltonstraat 4 | 3335 LR Zwijndrecht | The Netherlands | +31 (0)180 412 133 STUDS, NUTS & BOLTS | GASKETS, O-RINGS & SEALINGSETS |
Daltonstraat 4 | 3335 LR Zwijndrecht | The Netherlands | +31 (0)180 412 133 | sales@thbverhoef.com Daltonstraat 4 | 3335 LR Zwijndrecht