
4 minute read
Fast-tracking with FASTAR
Nippon Paint Marine expects more vessels in KSS Line’s 31 strong feet to adopt a FASTAR system later this year.
Nippon Paint Marine Coatings supplies customers around the world with high-quality products, technical services and know-how by making use of Nippon Paint Group’s global bases in manufacturing, sales, service, and logistics networks.
ALL PHOTOS COURTESY OF NIPPON PAINT MARINE.
Nippon Paint Marine has been at the forefront of technical innovation in marine paint for 140 years. Since being the frst marine paint company to produce tin-free selfpolishing antifouling in 1991, and now being the only company to have a true biocide free self-polishing antifouling, innovation and dedicated research have been the keys to stay ahead and keep the environment safe. The company has shown its ability to innovate fast and efectively, which makes Nippon Paint Marine one of the industry’s most valuable players. Let’s take a look at where the company is today and dive deeper into some of their latest successes.
JOSCO believes in FASTAR
Nippon Paint Marine’s ground-breaking nano-based antifouling FASTAR I® has been recently selected for the trio of energy-efcient box ships the Tsuneishi Group is building for China’s Jiangsu Ocean Shipping Co (JOSCO). The frst 1091TEU ship in the series, Hull No SS297, is nearing completion at the shipbuilder’s facility in Zhoushan City, Zhejiang Province, China, and scheduled to join the JOSCO feet last month (April). The second and third vessels in the series will be followed in August and September retrospectively. With an overall length of 146m and a 23.25m beam, each vessel in the series is based on Tsuneishi’s innovative low-resistance hull form and includes an array of energy-saving technologies.
Commenting on the decision to apply the FASTAR coating, Lian Jian Guo, General Manager, Technical Division, JOSCO, says, “We have very good experience with Nippon Paint Marine
systems on our vessels, so were keen to add to the overall energy efciency of these next generation vessels with the new FASTAR system. With the installation of advanced technologies designed to reduce energy consumption and emissions, these vessels will be the greenest in the JOSCO feet.”
The advanced technologies to which Lian Jian Guo refers include Tsuneishi’s TOP-GR and MT-FAST systems, of which the former optimises the number, diameter, shape and geometric distribution of propeller blades to achieve greater propulsive efciency. Further efciency gains are achieved with MT-FAST, which adds a wing-like device to the front of the propeller to alter water fows.
Introduced to the market early last year, Nippon Paint Marine’s fourth generation antifouling uses completely new hydrophilic and hydrophobic nano-sized silyl acrylate components to more precisely control the release of biocides.
Tsuneishi group (Zhoushan) Shipbuilding, one of Japan’s Tsuneishi Shipbuilding’s overseas shipyards, is also building three similar 1091TEU vessels for Taicang Container Lines Co., a subsidiary of China’s Jiangsu Port Group. These vessels, designed for the intraregional trade, will also beneft from the FASTAR coating. KSS Line has applied Nippon Paint Marine’s FASTAR® coating to the hulls of a pair of LPG (liquefed petroleum gas) carriers, becoming the frst South Korean shipowner to apply the novel nano-type antifouling paint to existing tonnage. The gas and chemical carrier operator applied a FASTAR I system to the 78,000m3 capacity VLGC Gas Power during a scheduled drydocking in February at Sembcorp Marine’s 87ha Admiralty shipyard in Singapore’s Sembawang district.

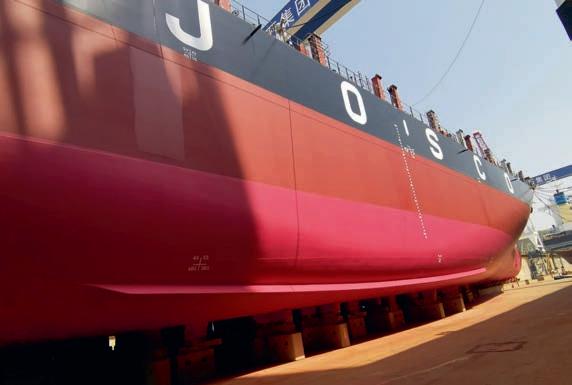
The application followed the success of the coating on KSS Line’s 84,000m3 capacity Gas Star, which was applied in December 2021 at the Yeosu Ocean shipyard in Gwangyang Bay, South Korea. In both cases, FASTAR I replaced Nippon Paint Marine’s popular A-LFSea® 150 product on the vessels’ fat bottom and vertical sides, representing the frst commercial reference for the new coating not only on a Koreanowned ship but also an LPG carrier. With a 20% to 30% increase in drydockings worldwide over the past twelve months, largely due to shipowners installing systems capable of meeting new environmental regulations, the coatings company says FASTAR can support shipowners’ sustainability goals. FASTAR is a twocoat, self-polishing copolymer antifouling paint that uses hydrophilic and hydrophobic nano-sized silyl acrylate components to precisely control the release of biocides – the active agents that target marine biofouling.
Nippon Paint Marine expects more vessels in KSS Line’s 31 strong feet to adopt a FASTAR system at scheduled drydockings later this year. Excluding these new applications, the marine coatings pioneer has to date supplied antifouling systems to the petrochemical carriers Duke Chemist, E Chemist, Falcon Chemist, and the gas carriers Gas Quantum, Gas Utopia and Gas Venus.
i. nipponpaint-marine.com
BOOTH NO. B5-204 SMM 2022