
8 minute read
I Poczuć wartość danych
ANDRZEJ SOLDATY
założyciel Inwicjatywy dla Polskiego Przemysłu 4.0, współtwórca Fundacji Platforma Przemysłu Przyszłości
Advertisement
POCZUĆ WARTOŚĆ DANYCH
– Jak doprowadzić do tego, by poczuć wartość danych i zrozumieć, że pomagają one tworzyć nową wartość produktu? Musimy uświadomić sobie, że jeśli produkt staje się inteligentny, umożliwia śledzenie jego wykorzystania, buduje dla mnie – jako producenta – wiedzę, którą mogę przekształcić w biznes – mówi Andrzej Soldaty, założyciel Inicjatywy dla Polskiego Przemysłu 4.0, współtwórca Fundacji Platforma Przemysłu Przyszłości, który większość swojej kariery zawodowej związał z obszarem automatyzacji przemysłu.
Joanna Jaśkowska: Czy polski przemysł jest już Przemysłem 4.0? Czy może wciąż 3.0? A może 3,5?
Andrzej Soldaty: Żeby odpowiedzieć na to pytanie trzeba wyjść od interpretacji pojęcia „Przemysł 4.0”. Termin ten został użyty po raz pierwszy 10 lat temu jako nazwa inicjatywy podejmowanej przez rząd niemiecki na rzecz transformacji krajowego przemysłu zgodnie z przełomowymi trendami nasilającymi się w branży wytwórczej na świecie. Chodziło o zachowanie konkurencyjności niemieckiego przemysłu, a szerzej gospodarki, w obliczu zmian w produkcji przemysłowej wprowadzanych w Stanach Zjednoczonych i krajach azjatyckich.
Nazwa Przemysł 4.0 stała się synonimem nowej generacji przemysłu, wykorzystującej innowacyjne rozwiązania techniczne i organizacyjne, a do upowszechnienia tej idei przyczyniły się targi hanowerskie, które pod hasłem „rozwiązania Przemysłu 4.0” zapraszają do prezentacji dostawców nowoczesnych rozwiązań.
Pod określeniem Przemysł 4.0. kryje się jednak znacznie więcej niż tylko rozwiązania techniczne.
To zmiana paradygmatów wytwarzania dotycząca zarówno systemów wytwórczych, jak i modeli biznesowych oraz architektury produktów. Zmiana całego sposobu tworzenia wartości jest tym, co określamy właśnie jako Przemysł 4.0.
A konkretniej?
Niewątpliwie mówiąc o Przemyśle 4.0, podświadomie kojarzymy go z transformacją cyfrową. Jednak nie są to pojęcia tożsame. Przemysł 4.0 to nowy sposób
fot. zasoby rozmówcy
funkcjonowania przedsiębiorstw, organizacji, nawet całej gospodarki, który z jednej strony bazuje na cyfryzacji, ale z drugiej – na datafikacji. Cyfryzacja to wykorzystanie technologii cyfrowej, natomiast datafikacja – zastosowanie danych w sposób efektywny. Połączenie tych dwóch elementów tworzy coś, co zmienia sposób funkcjonowania, paradygmaty wytwarzania i buduje Przemysł 4.0.
Technologie są jednym z komponentów tworzących ów Przemysł 4.0. Sama technologia, wprowadzenie zaawansowanej automatyzacji, robotyzacji, cyfryzacji to jeszcze bowiem nie Przemysł 4.0. Jest nim kompleksowe przedsięwzięcie pokazujące efekty, o których mówili twórcy tego pojęcia. To sieć wartości, gdzie przedsiębiorstwa – jako tzw. smart factories – połączone są ze sobą. Działają jako autonomiczne podmioty, które wymieniają informacje, dostosowują się do aktualnych potrzeb rynku, podejmują autonomiczne decyzje.
Nie jest to trochę futurystyczna, ale tylko wizja?
Z jednej strony – na pewno tak. Ale z drugiej widzimy, że konkretnie się urzeczywistnia. Widoczne jest to np. w raportach Światowego Forum Ekonomicznego, gdzie co roku prezentowani są liderzy Przemysłu 4.0. To obecnie 69 firm na świecie, które są „latarniami morskimi” pokazującymi, jak tę koncepcję można wdrażać i jakie korzyści z tego płyną. To jednak jest dopiero kilkadziesiąt przedsiębiorstw w skali świata. Pełne wdrożenie Przemysłu 4.0 to coś, co określić możemy jako perspektywa, wizja, do której dążymy. A stan przygotowania do tego wdrożenia to już druga sprawa. M.in. kwestie technologii mają tu kluczowe znaczenie, ale też kultura organizacyjna, regulacje prawne, przygotowanie ludzi do tych zmian.
Wracając do mojego pytania: jak można w tej chwili zdefiniować polski przemysł? Jaki jest stopień jego zaawansowania w kierunku tworzenia tej „nowej generacji”?
Kierując się założeniem, że czynnikiem umożliwiającym realizacje koncepcji Przemysłu 4.0 są rozwiązania techniczne, przyjrzyjmy się danym opublikowanym przez GUS dotyczącym wykorzystania technologii ICT, czyli informatyczno-telekomunikacyjnej w przemyśle przetwórczym. W tym obszarze, jak wynika z danych za rok 2020, funkcjonuje ponad 30 tys. przedsiębiorstw, różnej wielkości. Praktycznie prawie 100% jest podłączonych do Internetu szerokopasmowego. Jeśli chodzi o jego szybkość, ponad 40% firm dysponuje prędkością 100 Mb/s. Ponad 90% przedsiębiorstw wyposaża pracowników w mobilne urządzenia umożliwiające łączność z Internetem – średnio ¼ pracowników te urządzenia posiada.
Element łączności jest konieczny do wejścia w koncepcję Przemysłu 4.0. Ale teraz przyjrzyjmy się temu, jak Internet jest wykorzystywany, odwołując się do wspomnianego raportu GUS. Ponad 80% przedsiębiorców posiada własną stronę internetową, ale w zasadzie głównie wykorzystywana jest ona do prezentowania produktów czy usług. Natomiast inne działania interaktywne, jak np. prowadzenie czatu z klientem, to już margines – 6%. Wykorzystanie Internetu ma przede wszystkim charakter pasywny, a uczestniczenie w łańcuchach wartości w czasie rzeczywistym wymiany informacji to podstawa Przemysłu 4.0.
Jeśli chodzi o Internet Rzeczy, czyli podłączenie urządzeń do Internetu w celu zbierania, przesyłania i przetwarzania danych – 17% przedsiębiorstw krajowych deklaruje korzystanie z tego rozwiązania. W tym aspekcie pozytywnie prezentuje się sektor energetyczny i ciepłowniczy– 39 % przedsiębiorstw wykorzystuje rozwiązania IoT.
Inicjatywa dla Polskiego Przemysłu 4.0 powstała w 2016 roku. Co to za ruch? Na czym polegają jego działania?
Inicjatywa powstała jako potrzeba wewnętrzna, która narodziła się w wyniku mojego uczestnictwa w przedsięwzięciach i projektach, które można określić działaniami na rzecz Przemysłu 4.0 w Europie. Przez 35 lat miałem przyjemność działać w obszarze automatyzacji przemysłu, rozpoczynając swoją karierę w Ośrodku Badawczo-Rozwojowym Automatyzacji Przemysłu Chemicznego. Prowadziłem zespoły ds. robotyzacji i wykonywałem pierwsze aplikacje robotów w polskim przemyśle chemicznym. Potem związałem się z koncernem międzynarodowym, który jest jednym z liderów automatyzacji nie tylko w Europie, ale i na świecie. Podczas 25-letniej działalności miałem tam okazję z jednej strony uczestniczyć aktywnie we wdrażaniu rozwiązań, które można nazwać początkami Przemysłu 4.0, ale z drugiej strony tworzyć sieć partnerów, którzy z tą tematyką mieli do czynienia. W momencie, gdy działania w tym zakresie stawały się w Europie coraz bardziej powszechne, stwierdziliśmy, że należy o tym mówić, pokazywać, że jest konieczność pójścia tą drogą. Początkowo pod hasłem „Inicjatywa dla Polskiego Przemysłu 4.0” występowaliśmy na konferencjach, spotkaniach branżowych, gdzie przedstawialiśmy omawianą ideę. To szybko zostało dostrzeżone przez ówczesne Ministerstwo Rozwoju, które tworzyło zapisy na rzecz strategii zrównoważonego rozwoju, gdzie została określona konieczność reindustrializacji w kierunku Przemysłu 4.0. W ministerstwie powstał Zespół ds. Transformacji Przemysłowej, którego uczestnikami stali się członkowie Inicjatywy. Jednym z obszarów, jakimi się zajmował, było wypracowanie koncepcji czegoś, co nazwano Platforma Przemysłu Przyszłości – orkiestratora stymulującego wprowadzanie działań w kierunku Przemysłu 4.0 zarówno odgórnie, jak i w wyniku inicjatyw oddolnych. Miałem przyjemność ten projekt prowadzić. Platforma została powołana ustawą jako Fundacja, przejąłem jej prowadzenie w fazie tworzenia i przez pierwsze dwa lata pełniłem rolę prezesa, tworząc zespół i koncepcję. Następnie przekazałem prowadzenie osobom, które obecnie zajmują się rozwojem organizacyjnym, a sam uczestniczę w inicjatywach merytorycznych w kierunku rozwoju Przemysłu 4.0, m.in. organizując Centrum Przemysłu 4.0 na Politechnice Śląskiej.
CYFROWE ZMIANY
Postępujący proces starzenia społeczeństw zmniejsza podaż pracowników w wieku produkcyjnym. Następuje zmiana generacyjna, a kolejne pokolenia mają nowe, cyfrowe podejście do poznawania i rozumienia świata fot. 123rf
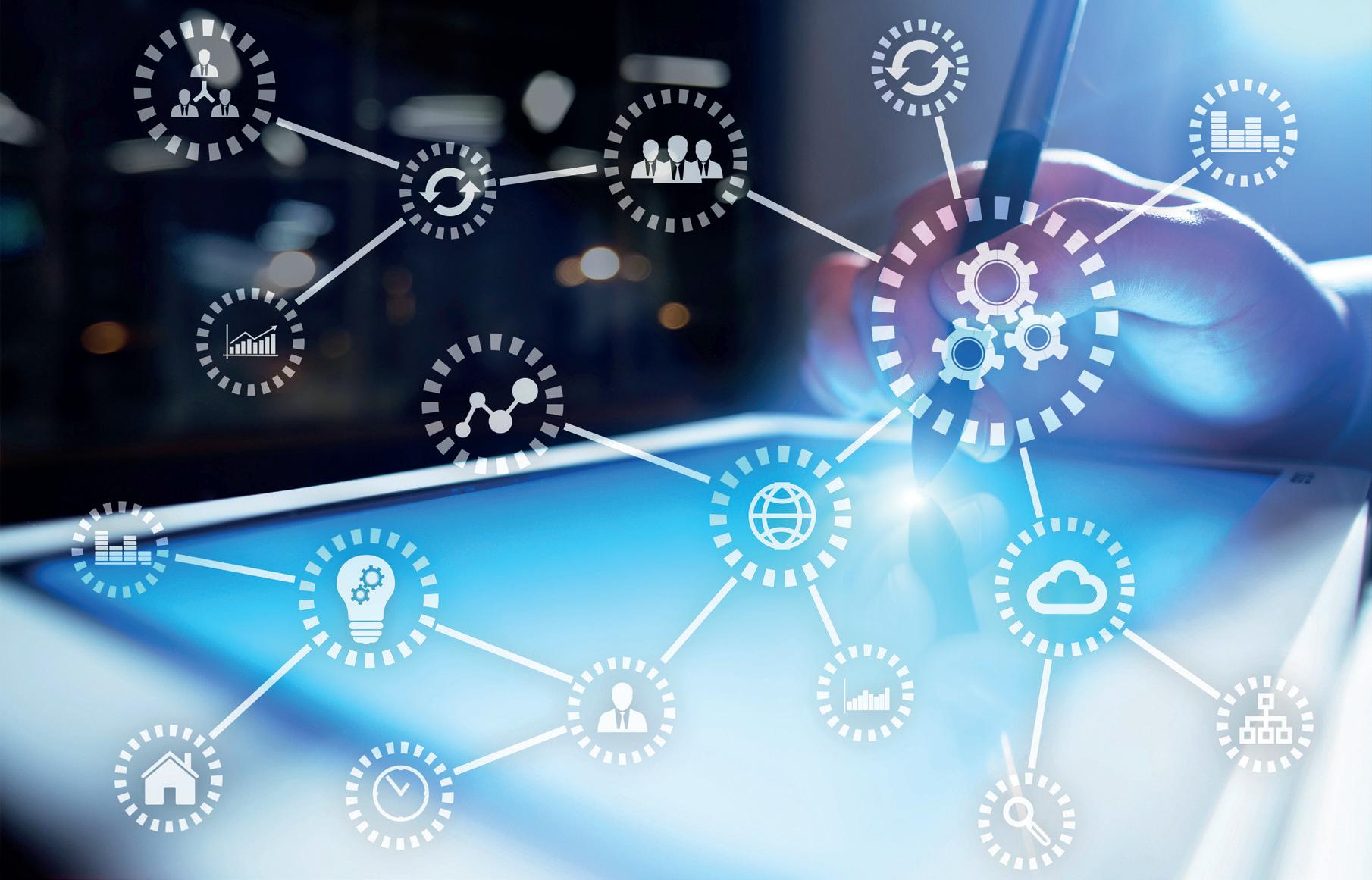
Kolejny element to wykorzystanie Big Data – tę technologię stosuje nieco ponad 8% firm. W przypadku sektora energetycznego i ciepłowniczego udział ten jest wyższy i wynosi blisko 13%, a prawie 9 % firm w tym sektorze stosuje Big Data w odniesieniu do danych z czujników i urządzeń inteligentnych.
Patrząc przez pryzmat tych liczb, nie odwołując się do subiektywnych ocen przedsiębiorców, czy są na etapie 3.0 czy 4.0 czy jeszcze innym, trudno powiedzieć, żebyśmy byli na poziomie 4.0.
Czyli Przemysł 4.0 to na razie cel, wizja dla polskiej gospodarki. A w jakich obszarach – w zakresie budowy nowoczesnego przemysłu – mamy najwięcej „do nadrobienia”? Czy pandemia wpłynęła tu na przyspieszenie zmian?
Pandemia jest bardzo silnym akceleratorem zmian, szczególnie w obszarze wykorzystania technologii cyfrowych w budowaniu interakcji pomiędzy uczestnikami łańcucha wartości.
W budowaniu wartości w procesach produkcyjnych dotychczas te interakcje miały charakter fizyczny: człowiek – człowiek. Obecnie, poprzez dystansowanie społeczne, wprowadza się elementy, które wirtualizują ten kontakt – choćby praca zdalna. Koronawirus bardzo przyspieszył rozwój obszaru związanego z komunikacją, przekazywaniem informacji na odległość.
Natomiast największym obecnie wyzwaniem jest to, w jaki sposób dane, które dzięki tej łączności przekazujemy, mogą być wykorzystywane, przetwarzane. Często zostają one wewnątrz maszyny albo używane są tylko do pewnego poziomu, np. wizualizacji stanu. Nie wchodzą w dalszy proces budowania wartości. Jak doprowadzić do tego, by poczuć wartość danych i zrozumieć, że pomagają one tworzyć nową wartość produktu? Musimy uświadomić sobie, że jeśli produkt staje się inteligentny, umożliwia śledzenie jego wykorzystania, buduje dla mnie – jako producenta – wiedzę, którą mogę przekształcić w biznes.
Spójrzmy na konkretną dziedzinę. Jak systemy informatyczne, sztuczna inteligencja są lub mogą być wykorzystywane w zakresie remontów i utrzymania ruchu?
Cały czas krążymy wokół danych, ich przetwarzania w informacje, a następnie przetwarzania informacji w wiedzę, a tej – w biznes. W UR to nabiera szczególnego znaczenia w związku ze zmianami demograficznymi. Następuje proces starzenia społeczeństw, zdecydowane zmniejszenie podaży pracowników w wieku produkcyjnym w odniesieniu do całości populacji. Mamy do czynienia ze zmianami pokoleniowymi. Nowe generacje: X, Y, Z mają zupełnie inne nawyki, podejście – dla nich smartfon jest nieodłącznym elementem poznawania i rozumienia świata.
W UR jedną z kluczowych kompetencji jest rozpoznawanie przyczyn dysfunkcji maszyny, urządzenia, prowadzenie nie tylko zadań prewencyjnych ale i predykcji – w miarę możliwości – np. w oparciu o charakterystyczne symptomy. To jest wiedza, która została zgromadzona przez specjalistów, którzy mają z tymi urządzeniami kontakt na co dzień, znają je. A co się dzieje, gdy ten pracownik „złota rączka” odchodzi, bo osiągnął wiek ponademerytalny? Okazuje się, że brak wiedzy, doświadczenia, kompetencji jest wyzwaniem dla właściciela. I nikt nie jest w stanie zapewnić poprawnej produkcji.
Dzięki cyfryzacji i przetwarzaniu danych możemy zgromadzić wiedzę poprzez skanowanie zachowań pracowników, zbieranie wszystkich raportów. Uzyskujemy w ten sposób bazę, która może być transferowana do następców dzięki rzeczywistości rozszerzonej. Obserwując cyfrowego bliźniaka maszyny, mogę odwołać się zarówno do wiedzy zgromadzonej w bazie w moim zakładzie, jak i do tej, którą gromadzi producent maszyny. Świat UR będzie mocno „ucyfrowiony” poprzez korzystanie z „cyfrowych bliźniaków” – w nich zaszyta będzie informacja pozwalająca dokonywać remontów, ale też prowadzić predykcję – wyprzedzająco analizować, co może się dziać. Co więcej: podejmować działania zapobiegające wystąpieniu awarii.
W obszarze UR kontakt na linii: człowiek – maszyna będzie wspierany zasobem zewnętrznym, który zbiera wszystkie informacje z maszyny, jak i doświadczenia związane z jej eksploatacją.
Jak – według pana – będą w związku z tym wyglądały w przyszłości służby UR? Czy muszą pojawić się nowe zawody? Nowe specjalności?
Kluczowa będzie umiejętność korzystania z technologii wspierających proces bezpośredniego interweniowania w obszarze maszyny czy utrzymania ruchu. Ale to jest domena nowych pokoleń, które urządzenia cyfrowe wykorzystują w sposób naturalny. Dla nich ta umiejętność jest wpisana niejako w geny – teraz trzeba tylko te umiejętności zasilić odpowiednią wiedzą, zbieraniem danych, informacji.
W UR będą tworzyć się dwie warstwy. Pierwsza to backoffice – tu będzie gromadzona wiedza związana z utrzymaniem ruchu. Druga to bezpośredni kontakt z maszyną. Osoby wyposażone w szereg technologii wspomagających będą nadzorcami rozwiązań wykonujących określone czynności.
Obok wyzwań związanych z Przemysłem 4.0 nie sposób nie zauważyć tych dotyczących celów klimatycznych, z Europejskim Zielonym Ładem. Czy i jak nowe technologie mogą dopomóc we wdrożeniu polityki green dealu?
W założeniach polityki przemysłowej opublikowanej przez Komisję Europejską w zeszłym roku cały czas się mówi o dwóch elementach: nowy przemysł to digital transiton i green transition. Są one ze sobą powiązane. W takim ujęciu cyfryzacja rozumiana jako wykorzystanie technologii cyfrowych, jak i datafikacja – czyli zarządzanie za pomocą tych technologii danymi i budowanie z nich informacji i wiedzy – pozwala w sposób konkretny zarządzać m.in. efektywnym wykorzystaniem energii, zasobów, środków produkcji. To oczywiście możliwość śledzenia produktu w całym cyklu jego życia, od powstania po recykling czy ponowne jego wykorzystanie. A więc niewątpliwie cyfryzacja staje się naturalnym czynnikiem pozwalającym w sposób konkretny realizować koncepcję Zielonego Ładu.
__________________________________________________________
Rozmawiała Joanna Jaśkowska, zastępca redaktora naczelnego Wydawnictwa BMP
Reklama
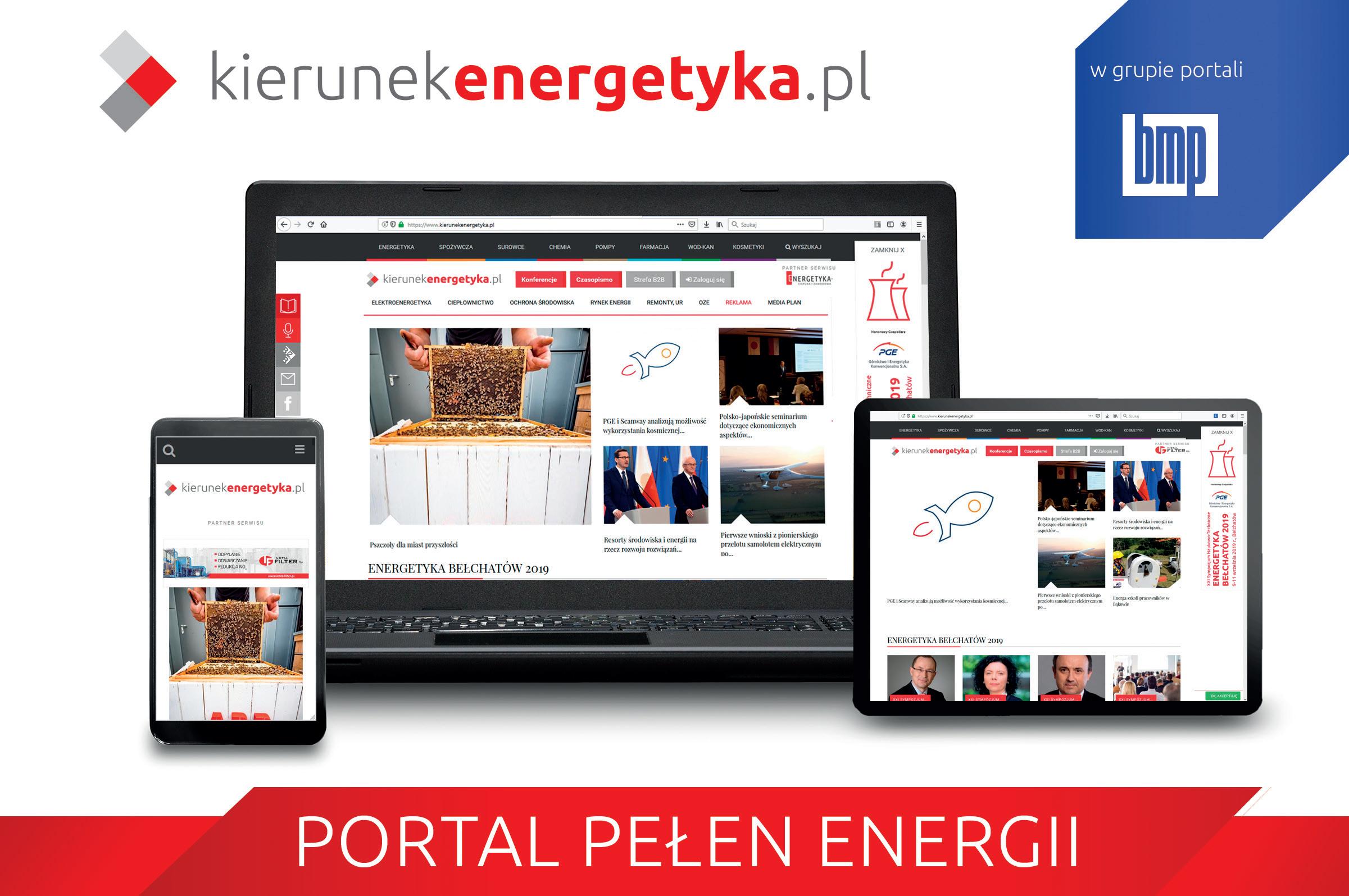