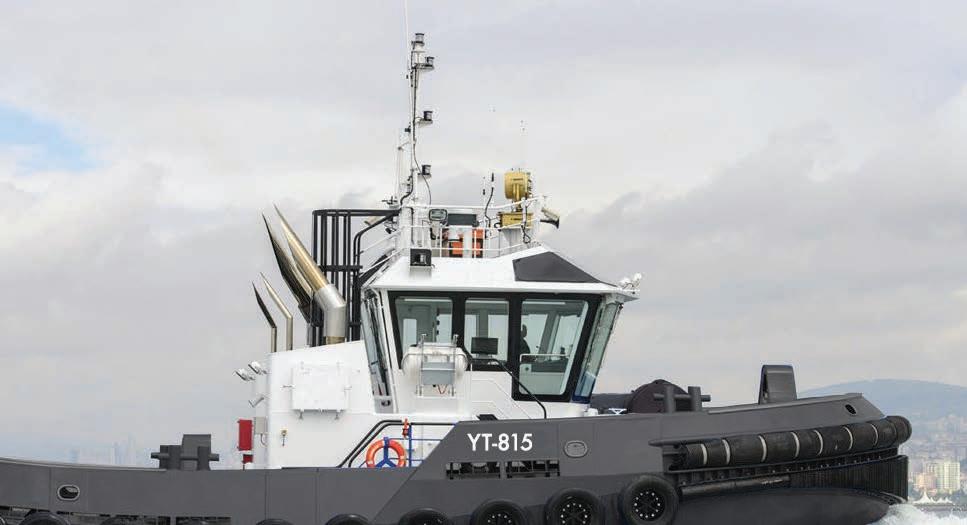
7 minute read
DECK MACHINERY Rugged, Tough and High Performing?
by Marine Log
Deck machinery is wide and varied, from articulating cranes to constant tension winches and capstans, all aimed at helping floatin gvessels perform their missions in all conditions.
Advertisement
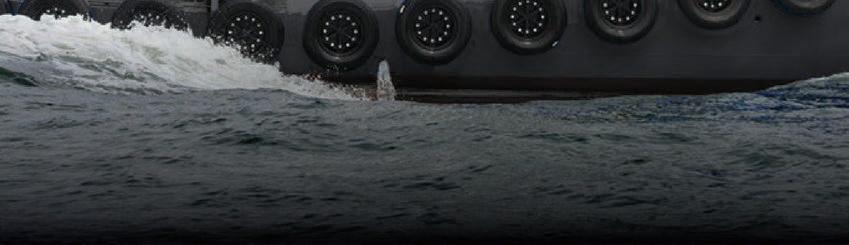
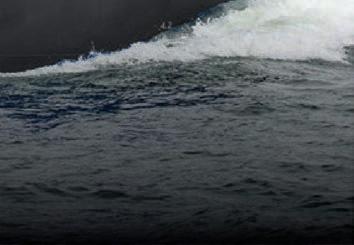

Deck machinery manufacturers continue to innovate with advanced and energy efficient technology.
From inside a control booth of an offshore platform, operators view a screen and a logic controller as a high-performing winch lowers their wet bell down into the ocean depths, helping the vessel complete its hydrographic mission.
The IHC Hytech Gantry wet bell system, built in cooperation with Romanian-headquartered DMT Marine Equipment, allows two divers and equipment operators to carefully work at a depth of nearly 270 feet below the ocean’s surface. The winch equipment’s containerized double hydraulic, 25 kW power units power a covered gantry handling system along with the DMT winch system that is installed onboard the vessel as a skid and requires no extra deck stiffening.
Marine deck machinery is wide and varied, from articulating cranes to constant tension winches and capstans, all performing
By Jim Romeo
delicate operations aimed at helping floating vessels perform their missions in the most severe conditions. Designs are rugged, endurable, environmentally compliant and high performing.
They must be designed to meet strong payloads and support very complex operations. This is particularly true for salvage and dive operations and towing and tug operations for commercial and government settings.
Outfitting New Naval Platforms For example, the Navy’s new T-ATSX class of ships being built at Gulf Island Fabrication’s shipyard in Houma, La., for the Military Sealift Command, will have a MacGregor deck machinery package that includes a main towing and traction winch, offshore crane, triplex shark jaws, towing and pop-up pins, and a stern roller.
The T-ATSX is a towing, salvage and rescue vessel class designed for worldwide naval service deployments, including openocean towing, submarine rescue and salvage support operations. The class’s design is based on those of commercial offshore towing vessels, and it will replace the T-ATF and T-ARS 50-class vessels that U.S. Military Sealift Command currently operates.
West Creek, N.J.-based JonRie will supply equipment for six Navy YT-808-class tugs built by Dakota Creek Industries, Anacortes, Wash. The agile capability of tugs requires deck machinery that’s not only reliable and fully environmentally compliant, but also durable and works well in tight scenarios where versatility and high performance are required. The 90-foot tugs will have a total power of 2,690 kW and will be used to dock and undock naval ships into berths and docking areas.
On the bow of each tug will be a JonRie Series 210 heavy duty hawser winch
complete with JonRie’s standard render block with a spool capacity of 600 feet of 18-centimeter hawser, a line pull of nearly 10 tons, a line speed of 174 feet per minute and a brake capacity of 150 tons.
On the stern, the tugs will have a JonRie Series 421 heavy-duty capstan with 50 tons of bollard capacity. The capstan will have a line pull of almost 78 tons and a line speed of 30 feet per minute.
“The trend in the industry in deck equipment is to return to hydraulic systems for reliability,” says Brandon Durar, president JonRie InterTech, who supplies the Navy tugs and other deck machinery throughout the Navy fleet. “The U.S. Navy took the first stance and went back to what they call legacy equipment (stuff that works). They have so much equipment in service not working it was time to fall back and regroup. JonRie just won the contracts for the Navy tugs YT-808 class and the project started out with electric winches. To make it similar to the YT-802 class, the Navy went back to hydraulic JonRie winches—A series 210 Hawser winch on the bow and a series 421 at Capstan back aft.”
Durar adds that JonRie has also just won the contract for the U.S. Navy tugs YT-815 class, supplying an all-hydraulic winch package, with a Series 220 Double Drum winch on the bow for submarine docking and a series 421 aft capstans. According to Durar, the Navy LPD-17 class vessels’ all-electric windlasses, an effort that the Navy is abandoning, will return to an all-hydraulic drive for its reliability and dependability.
Rugged and Green Commercial tugs are turning to innovative advancements in deck machinery to aid in their operations. This is especially true for new vessel construction where the intent its to construct energy efficient vessels that will be rugged, durable and high performing.
This is well demonstrated with Seattlebased Foss Maritime’s new ASD-90 tugs. The EPA Tier IV compliant Z-drive Tractor tugs will be equipped with a Markey escort winch on the bow and a Markey double drum offshore towing and rescue winch or an optional barge-handling winch. The bow winch, the
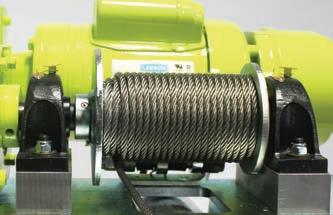
Foss Maritime’s EPA Tier IV compliant Z-drive tractor tugs will be equipped with a Markey escort winch on the bow and other options.
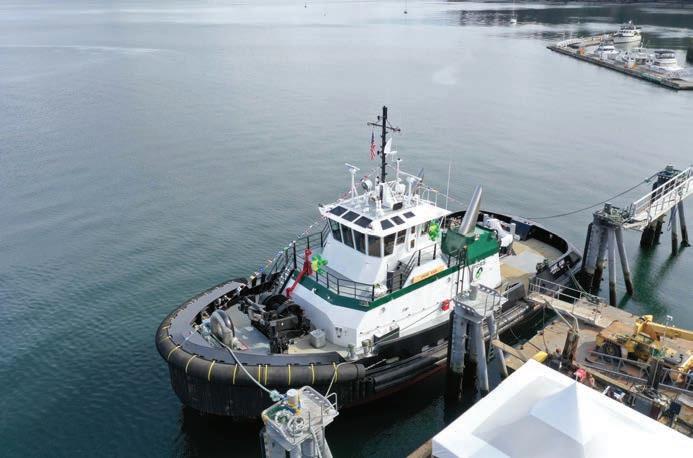
Markey DEPCF-52R, have a bow line of 750 feet of 10-inch circumference synthetic and the tow winch, the Markey DEPC-32 (escort) or TESS-34AS (emergency towing) has a 2,500-foot tow wire, with a 2 ¼-inch diameter wire. The barge line is 450 feet of 6 ½-inch circumference polyline.
The 100- by 40-foot ASD-90 tugs are multi-functional to include ship assist and escort capabilities, as well as towing.
Will Roberts, the chief operating officer for Foss Maritime, says safety for the crew and customers drives its demand and focus.
Focus on Compliant According to Roberts, the trends in deck machinery focus on power and safety of the crew on deck.
“Anytime a crew member is on deck, he or she is more at risk than when in the interior of the vessel,” he says. “Deck machinery also presents a risk of pollution, such as from a hydraulic oil spill. Then, there is just ensuring that the deck equipment, like our winches, can meet the ever-increasing power requirements of customers. To ensure we meet all these criteria, the [Foss tug] Jamie Ann’s winches are powered by an electric drive, significantly reducing, if not eliminating, any chance of hydraulic oil spilling on or over the deck.”
Roberts says the electric drive also creates efficiency throughout the system and ensures the company meets the power demands of customers. This is in contrast to the direction the U.S. Navy is taking for its new tug class vessels where they are steering away from all-electric windlasses.
“The new winch on the tug Jamie Ann, as well as new winches on our vessels are electric drive in order to eliminate risk of a hydraulic oil spill on deck,” adds Roberts. “Tighter specifications increase efficiency of the system by allowing for greater tension monitoring and control, especially for render and recover capabilities for our assist and escort tugs. Finally, the new winch on the Jamie Ann means that our crew does not have to be on deck monitoring the winch visually thereby decreasing lost time incidents and more generally potential injuries.”
Patterson’s New Davit Cranes Also focused on customer safety is Patterson Manufacturing, Pittsburgh, Pa., with its recently released line of davit cranes (see bottom-left photo).
Patterson Manufacturing, Pittsburgh, Pa., is a supplier of winches, rigging and fittings. From inventing the first river ratchet in 1871 to patenting the revolutionary YoYo winch in 2009, Patterson has been innovating and solving problems for industry leaders for over a century.
According to Patterson’s President Taylor Grapes, the davit crane line was a natural extension to their existing catalog as they have proven experience making custom products for lifting applications.
“Patterson rigorously tests all new designs, both digitally and physically,” says Grapes. “Using ANSYS for digital finite element analysis, we can see where problems may surface due to focused stress-in a part or assembly before we ever physically build something. Once a prototype had been made, we perform thousands of loaded cycle tests at various loads and positions, and other conditions depending on the product. Lastly, all products are tested to yield and to failure, either in-house on a hydraulic test bed, or by a certified third party.”