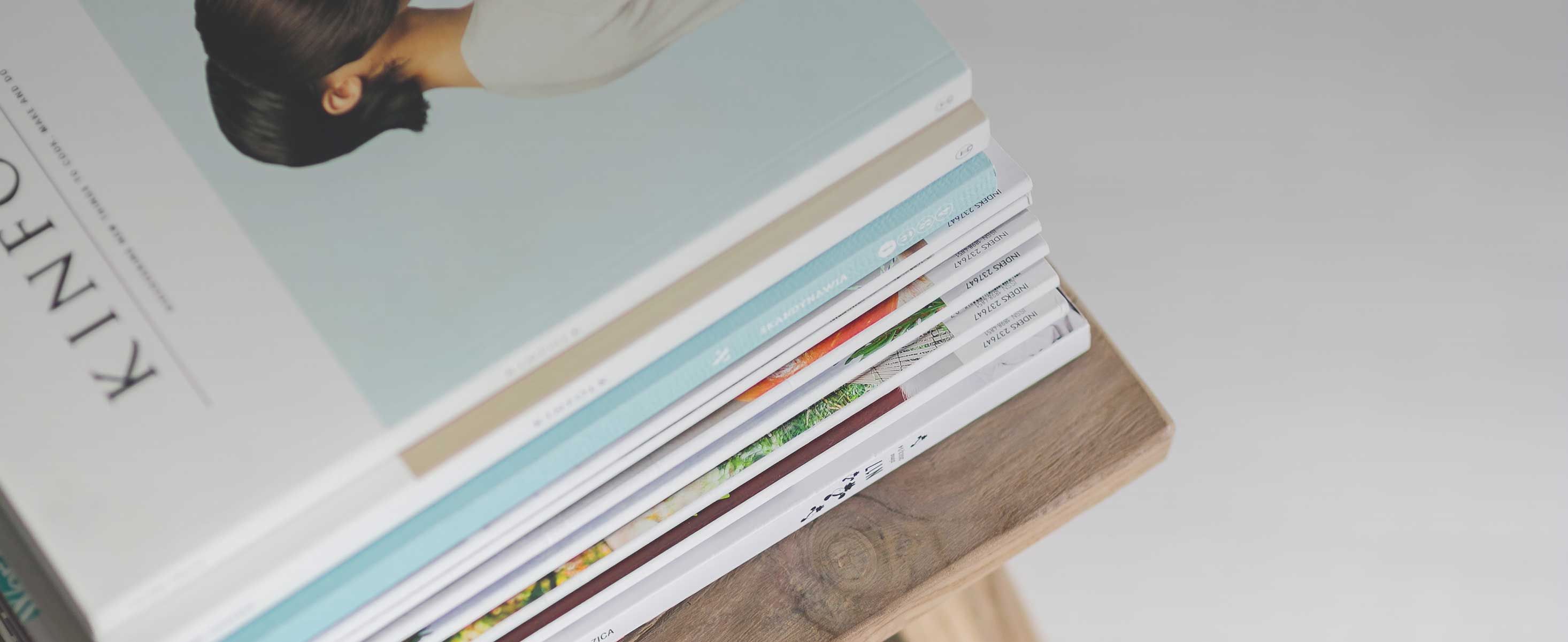
5 minute read
REPAIR YARDS KEEP BUSY and open to new opportunities
U.S. ship repair yards continue to keep busy with a variety of work of all kinds. And nowhere was that variety more in evidence than at Detyens Shipyards last month. The mix of government and commercial vessels in at the Charleston, S.C., yard included the Military Sealift Command fast combat support ship USNS Supply ; the ex-USS Robert G. Bradley (FFG-49), an
Oliver Hazard Perry-class frigate being refurbished prior to hand-over to the Kingdom of Bahrain as the Khalid Bin Ali ; the MSC Henry J. Kaiser -class fleet USNS Leroy Grumman (T-AO 195), the Ready Reserve Fleet (RRF) crane ship SS Cornhusker State (T-ACS-6); two American Queen Cruises coastal cruise ships, the Ocean Voyager and the Ocean Navigator ; the RRF RO/RO vehicle carrier Cape Ducato (T-AKR-5051), the
Advertisement
By Nick Blenkey, Senior Editorial Consultant
Netherlands-flag containership Bermuda Islander and the U.S.-flag cable lay ship Decisive , owned by Transoceanic Cable Company.
Also keeping busy at this time of year are Great Lakes shipyards. The Great Lakes are the largest freshwater system in the world. This is good news for steel hulls and explains the longevity of Great Lakes bulkers. Even so, when the Soo Locks close, it’s time for those ships to enter their annual winter layup and maintenance phase. This year alone, U.S. Great Lakes shipping companies will invest over $126 million in their vessels at shipyards and facilities across the Great Lakes, according to the Lake Carriers Association. That includes over $48 million in Wisconsin, $43.5 million in Ohio, $9 million in Michigan, and $26 million spread across Minnesota, Illinois, New York, and Pennsylvania.
Consolidation Continues
When MARAD last got round to publishing a “Report on Survey of U.S. Shipbuilding and Repair Facilities,” which, shockingly, was in 2004, it counted
Ships receiving attention at Detyens Shipyards in January included: USNS Supply, Khalid Bin Ali (ex-USS Robert G. Bradley ), USNS Grumman, Cornhusker State, Ocean Voyager in floating dry dock, Cape Ducato in dry dock #5, Ocean Navigator, Bermuda Islander in dry dock #1 and cable layer Decisive in dry dock #2.
27 shipyards with drydocking facilities and 34 topsides repair facilities. Those numbers may still be vaguely accurate, given that graving docks seldom get filled in and that floating docks can be towed to other places. But what has happened is that there has been considerable consolidation of ownership and the disappearance of some historic names. That’s still happening.
Last November, Bollinger Shipyards caught most of the market by surprise with its acquisition of Singapore Technologies Engineering’s two U.S. yards, VT Halter Marine Inc. and ST Engineering Halter Marine Offshore (STEHMO). While Halter Marine has been much in the news as the builder of the Coast
Guard’s Polar Security Cutter, operations at STEHMO have attracted far less attention and it’s interesting that its new name is Bollinger Mississippi Repair.
With deep-water access and no air draft restrictions, the shipyard has impressive repair capabilities, including a 546-foot dry dock with a 12,000-tonne lift capacity, and announced a $10 million upgrade program in 2020. Bollinger Shipyards is a major player in the ship repair market and Bollinger Mississippi Repair joins a roster of six Bollinger repair yards in Louisiana that includes facilities in Algiers, Amelia, Harvey (Bollinger Quick Repair), Larose, Lockport, and Port Fourchon.
Conversions and Modifications Ahead?
To get an idea of what’s going on at individual repair yards around the U.S., go to www.marinelog.com and type “ship repair” in the search box. Chances are that in the months ahead, that search will produce news of some interesting conversion projects.

When you need a new vessel in a hurry, particularly if it’s specialized, then a good way to go about it is by converting an existing one. This is dramatically illustrated by the U.K.’s decision to shelve plans to build a new royal yacht and instead speed up its acquisition of specialist offshore vessels to convert to subsea protection and mine countermeasures vessels.
In the U.S., a similar “we need it faster than we can get a newbuild” project has been picking up pace. With the U.S. Coast Guard’s single active heavy polar icebreaker, Polar Star , reaching the end of its useful service life there have long been proposals floating around that the Coast Guard acquire an interim vessel until the first of its new Polar Security cutters enter service. The most frequently mentioned candidate has been Edison Chouest Offshore’s M/V Aiviq and the Coast Guard’s FY2023 budget requested $125 million in procurement funding for the purchase of an existing commercially available polar icebreaker to augment the Coast Guard’s polar icebreaking capacity until the new PSCs enter service. When the Coast Guard’s FY2023 authorization got passed it included the wording “$150,000,000 is authorized for the acquisition or procurement of an available icebreaker.”
The only vessel meeting the requirements set by the Coast Guard in an RFI issued in May of last year is the
Aiviq . Built in 2012 by Chouest’s North American Shipbuilders for use on the Shell Alaska drilling campaign, it is the world’s most powerful, privately-owned icebreaker. With Polar Class 3, it is capable of operating in the harshest of environments and checks all the boxes in the RFI.
What remains to be seen is when the Coast Guard will pull the trigger and go ahead with the acquisition and conversion contracts.
A rather less high-profile project underscores the attractions of conversions for commercial operators. The Woods Hole, Martha’s Vineyard and Nantucket Steamship Authority is buying two offshore supply vessels (OSVs) from Hornbeck Offshore Services (HOS) of Covington, La., for conversion to freight ferries. The sister vessels—the 2009-built HOS Lode Star and 2008-built HOS Shooting Star —are 73 meter long 240 class OSVs.

They will replace the Steamship Authority’s aging open deck freight ferries, the 1981-buillt M/V Gay Head and 1982-built M/V Katama . Those, too, started off life as sister offshore service vessels. In 1988, the Steamship Authority converted the Katama to ferry service, adding a rounded stern to fit loading ramps and a small passenger area. Ten years later, the Katama received an additional upgrade as a 50-foot midsection was added along with more powerful EMD engines. Acquired a year after the Katama , the Gay Head also received a 50-foot midsection upgrade, as well as a new engine upgrade in the mid 1990s.
Both are now showing their age and a study commissioned by the Steamship Authority indicated they had an expected useful life of less than five years, while the two OSVs being acquired from HOS have an estimated remaining useful life of at least 25 years.
Initial cost estimates for the acquisition, conversion, and re-activation of the two OSVs is approximately $30 million. The Steamship Authority will finance the acquisition through the sale of bond anticipation notes within its $100 million bonding limit.

“The purchase and conversion of available OSVs is the most efficient, rapid and cost-effective path to upgrade our fleet and best serve the vehicle and freight transport needs of island residents and visitors,” said Steamship Authority General Manager Robert Davis. “The similar design of the vessels also promotes economies of scale through interchangeability of vessels for service needs, inventory of spare parts and crew training. Additionally, purchasing these used vessels will put the authority in a better financial transition to plan for investigate the possible inclusion of alternative fuel technologies into its next newly constructed vessel.”
While a growing number of Jones Act newbuildings are being ordered for the offshore wind area, there may be growing opportunities for repair yards to modify existing vessels for that market. A lot of eyes will be on how well the Otto Candies LLC Jones Act-compliant offshore IMR vessel, the Paul Candies , performs on a Siemens Gamesa Renewable Energy contract to support the construction phase of the South Fork Wind project, offshore New York.