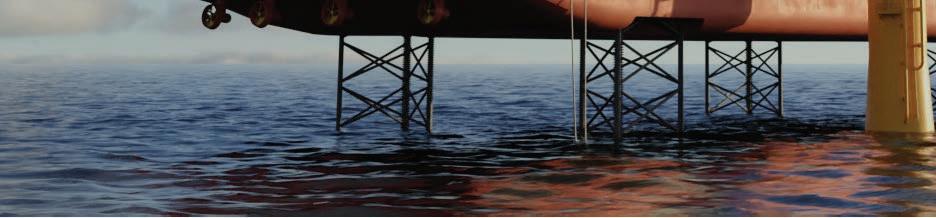
8 minute read
UPDATES
The NP20000X ULAM design is intended to be Jones Act compliant.
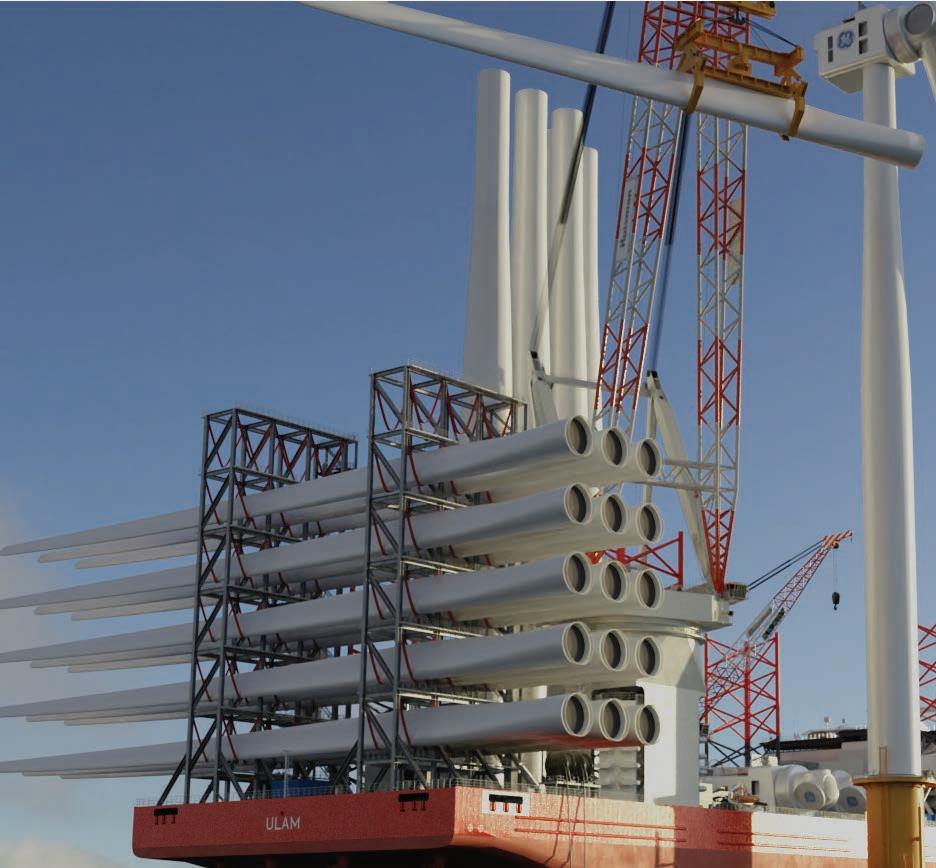
Advertisement
Jones Act Compliant WTIV Design is Hydrogen Ready
ABS HAS AWARDED ITS APPROVAL IN PRINCIPLE (AIP) for a hydrogen-ready wind turbine installation vessel (WTIV) design to Ned Project Inc., which is working with GPZ Energy to develop WTIV projects for the U.S. market.
The NP20000X ULAM design is intended to be Jones Act compliant. It is also designed to be able to meet future offshore wind market demands, specifically operations involving 15-20 MW wind turbine installations. Its innovative approach loads monopiles vertically on the 8,000-square-meter deck, eliminating the need to rotate monopiles to the vertical position at sea, increasing efficiency and safety.
The design is equipped with a leg encircling heavy cargo crane with a working load of 3,500 metric tons capable of handling turbines of 240-meter rotor diameter and 150-meter tower height.
The enginerooms of the hydrogen-ready WTIV are designed to be able to be converted into fuel cell compartments accommodating polymer electrolyte membrane fuel cells, making it possible to rely solely on liquefied hydrogen (LH2) to meet its energy demands.
“There is significant potential for growth in the U.S. offshore wind market and we are confident our WTIV design has the attributes required to deliver this,” said Peter Novinsky, spokesperson for GPZ Energy. “The scale, power and handling capacity as well as the innovative way it handles the monopiles means this is perfectly adapted to serve the U.S. industry.”
“ABS is the ideal partner for a highly specialized wind turbine installation vessel such as this, both for the U.S. market and internationally,” said Greg Lennon, ABS vice president, offshore wind. “Our extensive knowledge of U.S. regulations combined with our global offshore industry leadership means we are uniquely equipped to support this project and a range of other innovative vessels now being commissioned to support the growing international demand for renewable energy. ABS is committed to playing a significant role in the safe development of the U.S. offshore wind industry.”
Burger Boat Books Order for Ferry Designed for Tough Winters
BURGER BOAT COMPANY’S MANITOWOC, WIS., shipyard has started construction of a new 92-foot vehicle/ passenger ferry, the Neebish Islander III. Ordered by the Eastern Upper Peninsula Transportation Authority (EUPTA), located in Sault Ste. Marie, Mich., the ferry will operate year-round on the St. Mary’s River in Michigan’s Upper Peninsula between Barbeau, Mich., and Neebish Island. It has been designed to operate in the harsh winter environment and through the solid ice conditions it will encounter on its route.
Based on the experience of four previous commercial vessel designs built by this shipyard, we know that EUPTA will receive a first-class product from Burger Boat Company, and we look forward to collaborating once again,” said Mark Pudlo, president, Seacraft Design LLC, which designed the vessel.
The Eastern Upper Peninsula Transportation Authority, established in 1975, operates three local vehicle and passenger ferries to the nearby islands of Sugar, Neebish, and Drummond.
“We’re grateful to be selected by the Eastern Upper Peninsula Transportation Authority to build their new vessel,” said Jim Ruffolo, president and CEO, Burger Boat Company. “At Burger, our team prizes collaboration, among each other and with our clients, to deliver vessels people can look upon with pride, year after year. Whether it’s a luxury yacht or a hard-working ferry for demanding conditions like those the Neebish Islander III will face, we are committed to delivering tailored, quality vessels that meet and exceed the owner’s vision.”
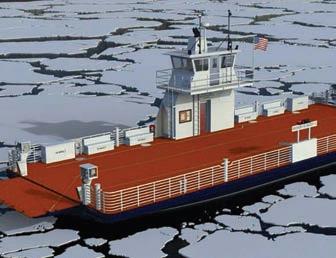
Bunkerings in Two Countries Show Trend to Greener Versions of Gas Fuels

RLNG bunkering was carried out by bunker vessel Clean Jacksonville
WHILE LNG OFFERS drastically reduced CO2 emissions compared to other fossil fuels, it’s seen as a bridge to zero emissions such as ammonia or hydrogen. As shipowners face progressively tighter IMO CII and EEXI standards, the search is on for greener liquefied gas fuels that promise to extend the time that IMO standards can be met by LNG-fueled ships.
Last month saw two pioneering bunkering involving these cleaner fuels. In one, carried out in the Port of Jacksonville, Fla., America’s first LNG bunkering vessel, Clean Jacksonville, bunkered the world’s first LNG-fueled containership, TOTE Maritime Puerto Rico’s Isla Bella, with a blend of LNG and renewable liquefied natural gas (RLNG) supplied by JAX LNG, a small-scale LNG facility located along the St. John’s River in Jacksonville.
Element Markets supplied the renewable natural gas (RNG) used to produce the RLNG. Produced from the decomposition of organic waste, RNG is compatible with existing natural gas infrastructure, providing a practical and replicable source of energy that mitigates and repurposes carbon emissions. For this bunkering event, RTCs were matched to the physical LNG loaded into the Clean Jacksonville to create the RLNG/LNG blended product.
JAX LNG is the long-term supplier to the two LNG-fueled container vessels—the Isla Bella and the Perla del Caribe—that TOTE Maritime Puerto Rico operates between Jacksonville and Puerto Rico.
“We’re proud to partner with JAX LNG, which has continued to solidify its position as the industry leader in the clean fuel revolution,” said Mike Noone, president of TOTE Maritime Puerto Rico. “RNG is a clean, drop-in fuel source that
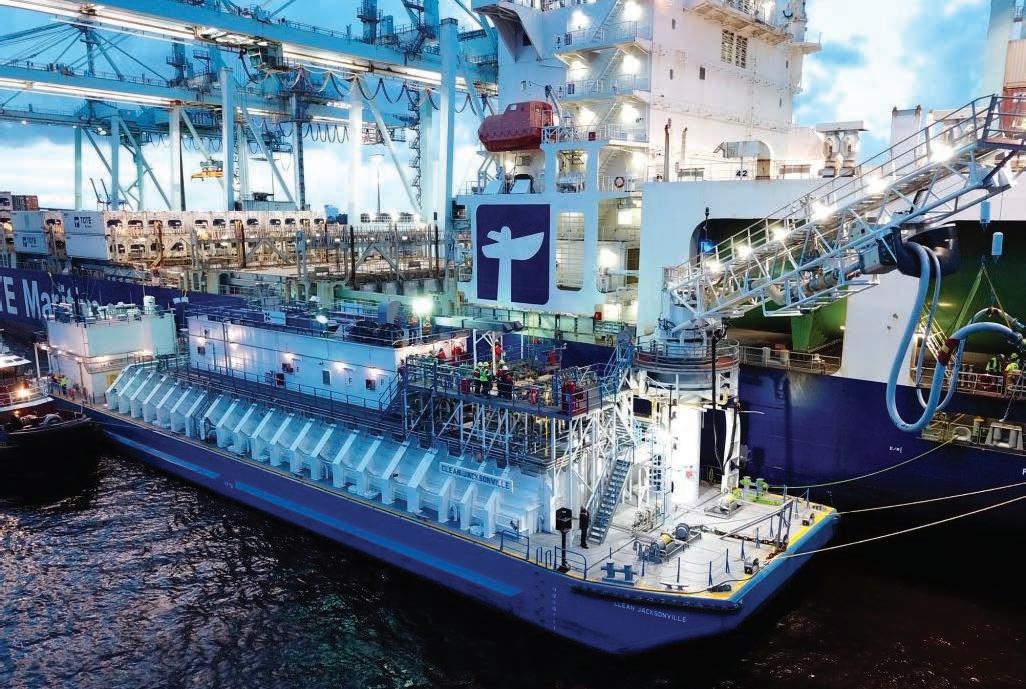
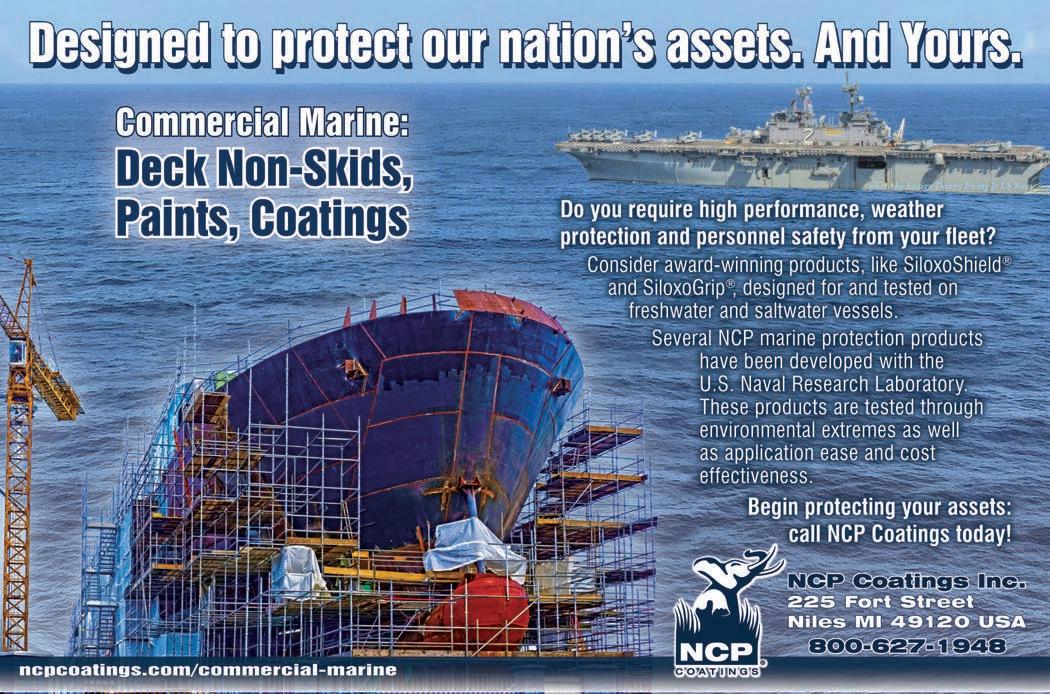
can be readily deployed for use today, since it needs no new equipment to capture or transport it.”
On the other side of the Atlantic, at the Elbe port in Brunsbüttel, Germany, a containership that first made the headlines when its main engines were converted to dual-fuel operation was in the news again. In a world-first for the maritime sector, the ship, the ElbBLUE, was bunkered by LNG supplier Liquind Marine with some 20 tons of green SNG (synthetic natural gas). The liquefied SNG was produced in a power-to-gas facility in Werlte, Germany, owned by kiwi AG. It was generated using 100% renewable energy, one of a number of Power-to-X electricity conversion, energy storage, and reconversion pathways that make use of surplus electric power, typically during periods where fluctuating, renewable-energy generation exceeds load.
The ElbBLUE is the former Wes Amelie. In 2017, its MAN 8L48/60B main engine was retrofitted to its current, four-stroke MAN 51/60DF unit to enable dual-fuel operation. The first such conversion of its type globally, it showed that existing engines could be converted to LNG operation. Following the SNG monitoring, the ElbBLUE continued its journey under the supervision of engineers from MAN PrimeServ, MAN Energy Solutions’ after-sales division. The vessel’s direct CO2 emissions are expected to decline by 56 tons for this coming trip.
Owned by German shipowner Elbdeich Reederei and operated by charterer Unifeeder, the 1,036 TEU feeder containership operates on the North Sea and the Baltic.

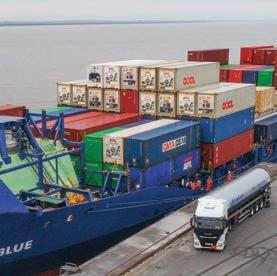
ElbBLUE was bunkered with SNG by Liquid Marine truck.
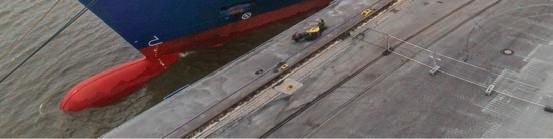
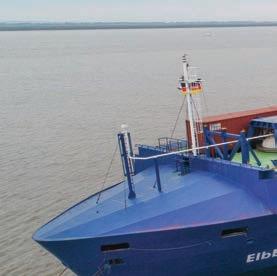

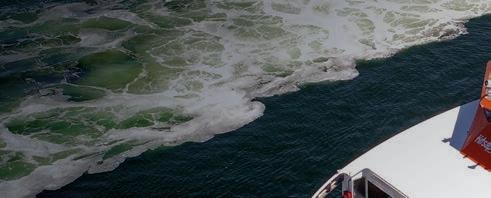
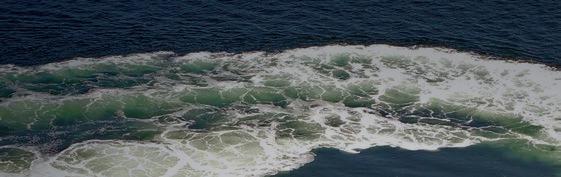

World-leading ship design for passenger vessels
Get in touch
703-920-7070
140FT
High-Speed Subchapter K Passenger Vessel

inquiries@bmtdp.com www.bmt.org

Austal USA Sees Booming Ship Repair Business at New West Campus
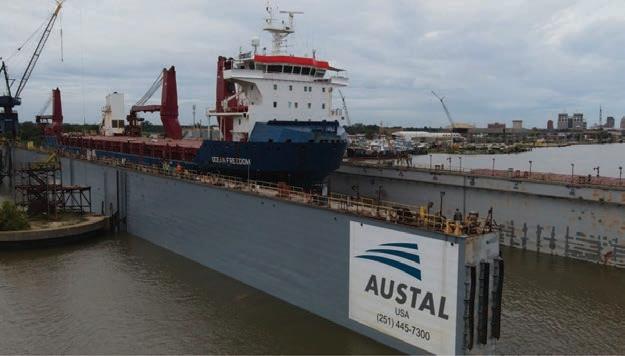
FOLLOWING ITS SEPTEMBER 2020 acquisition of additional waterfront along the Mobile River in Mobile, Ala., Austal USA was quick to establish a ship repair facility that, it reports, has had a booming response.
“Almost immediately after word got out Austal USA had purchased the additional waterfront property, we were inundated with calls from commercial captains looking to return to Mobile to have their ships serviced,” Austal USA’s senior vice president of operations Mike Bell said. “We are pleased with all of the positive feedback we have received from our ship repair customers thus far.”
Austal’s acquisition included 15 acres of waterfront property spanning almost 3,000 linear feet of waterfront pier space, a 20,000ton certified Panamax-class floating dry dock, a 300,000 square foot outside fabrication area, and 100,000 square feet of covered fabrication facilities all just 30 miles from the Gulf of Mexico.
While Austal USA is best known for advanced manufacturing of high tech Navy ships, word is rapidly getting out that the company also has a highly capable ship repair operation.
The Austal West Campus repair facility is located across the river from Austal USA’s 165-acre corporate headquarters providing access to deep water berthing for vessels up to 1,000 feet, advanced manufacturing capabilities, including a friction stir welder, CNC machines, CNC cutting tables, and a carpenter shop, machine shop and electrical and pipe shops. The repair facility also offers heavy-lifting capability with mobile cranes, overhead cranes and wing wall cranes that travel the length of the 668-foot dry dock.
Services provided by Austal’s Mobile ship repair operation range from conversions and upgrades to advanced ship repair.
The machine shop and fabrication areas are fully equipped with overhead cranes, lathes, and CNC plasma cutters. Other technical services offered to the company’s service clients include full-service detail design capability, 3D modeling, field engineering support and dimensional accuracy control.
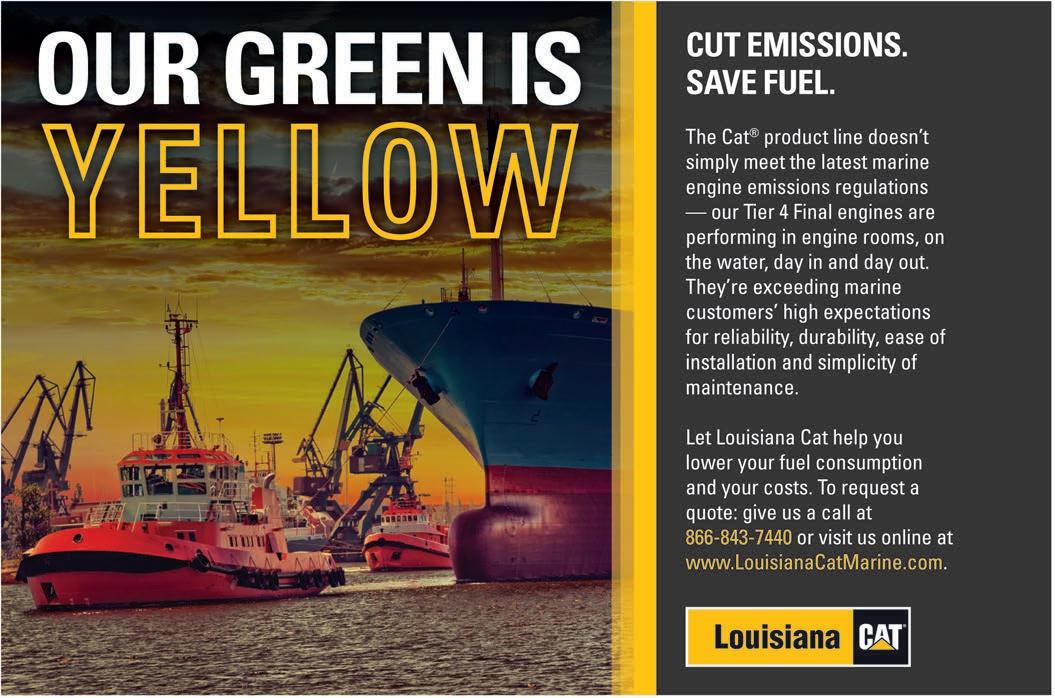