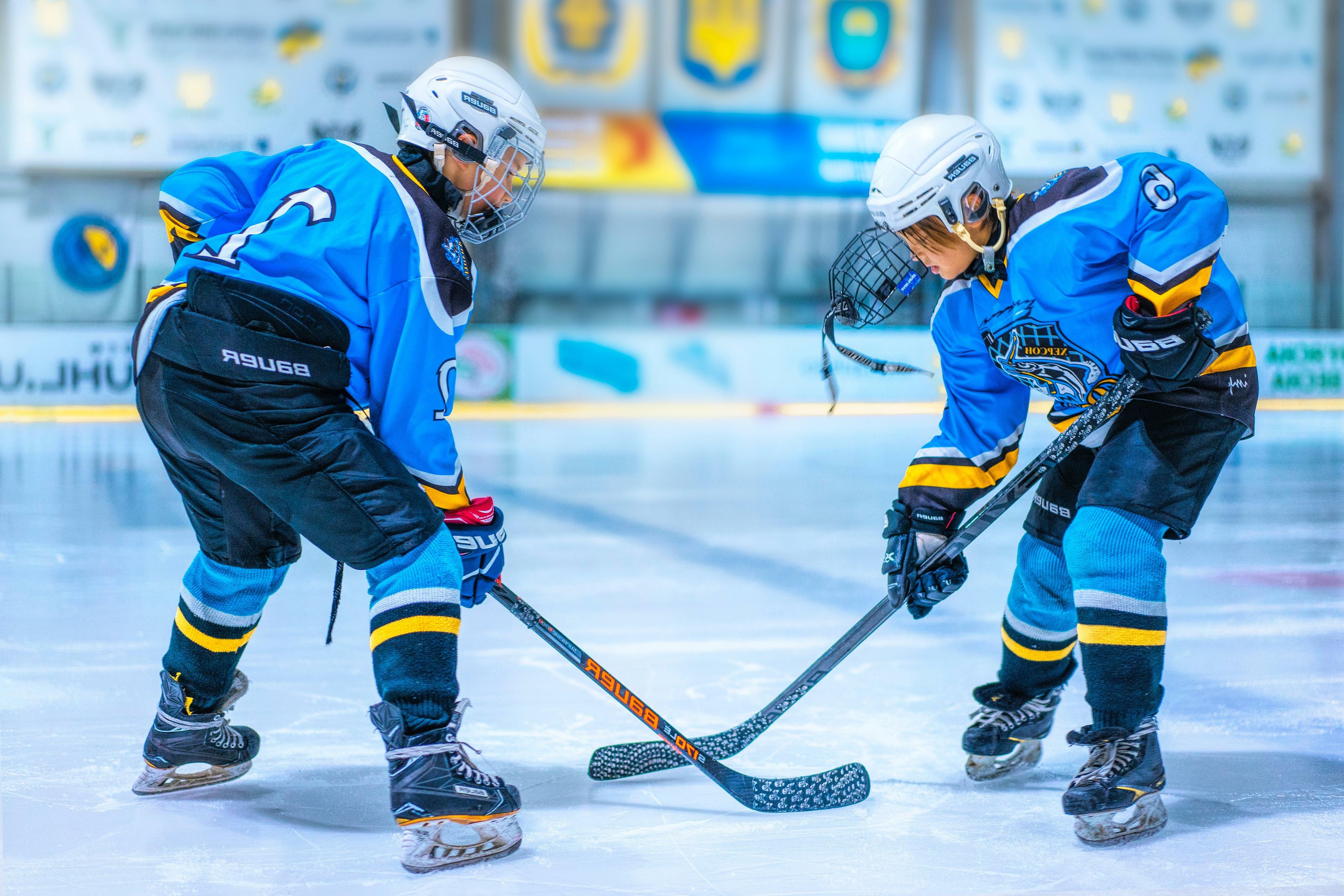

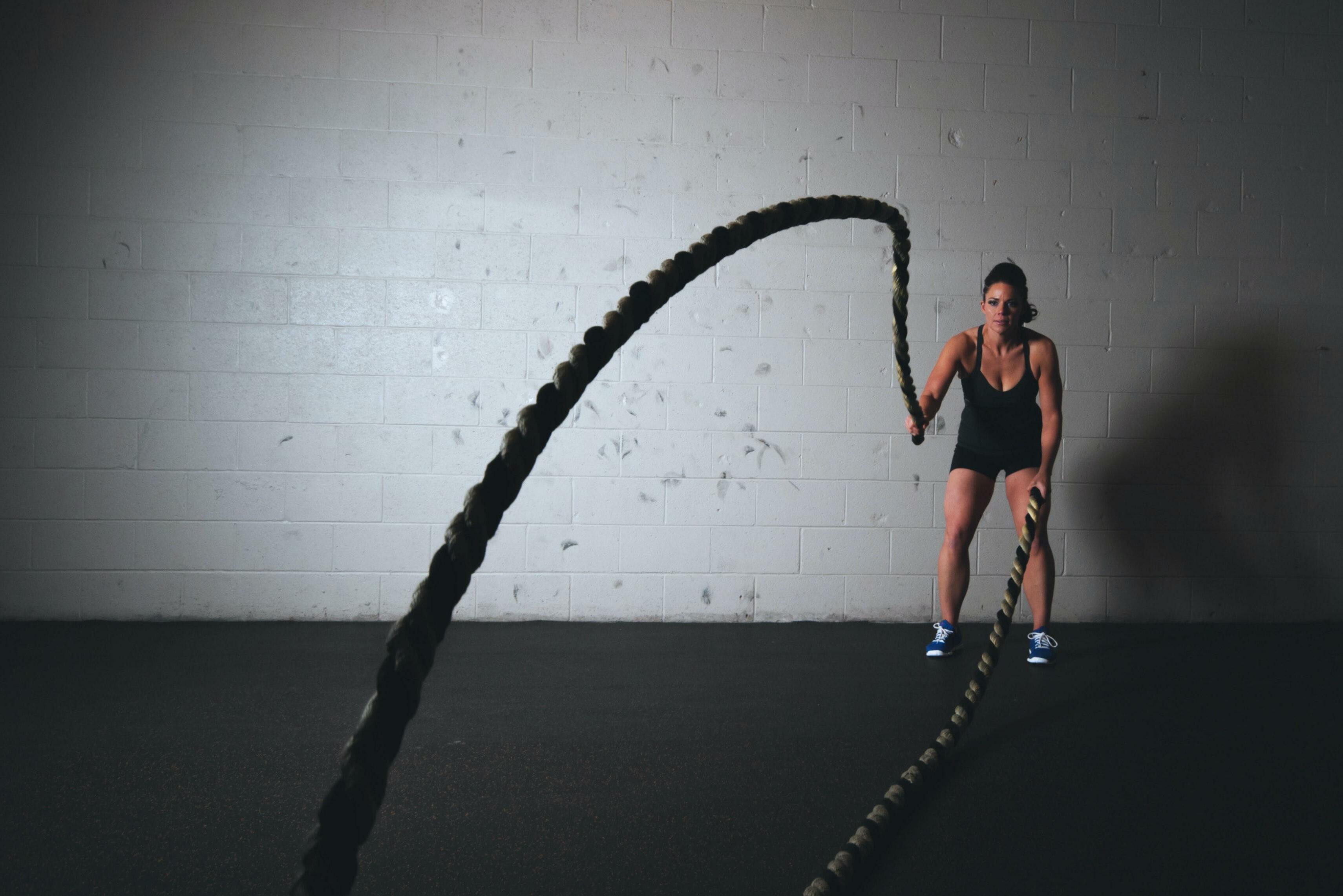
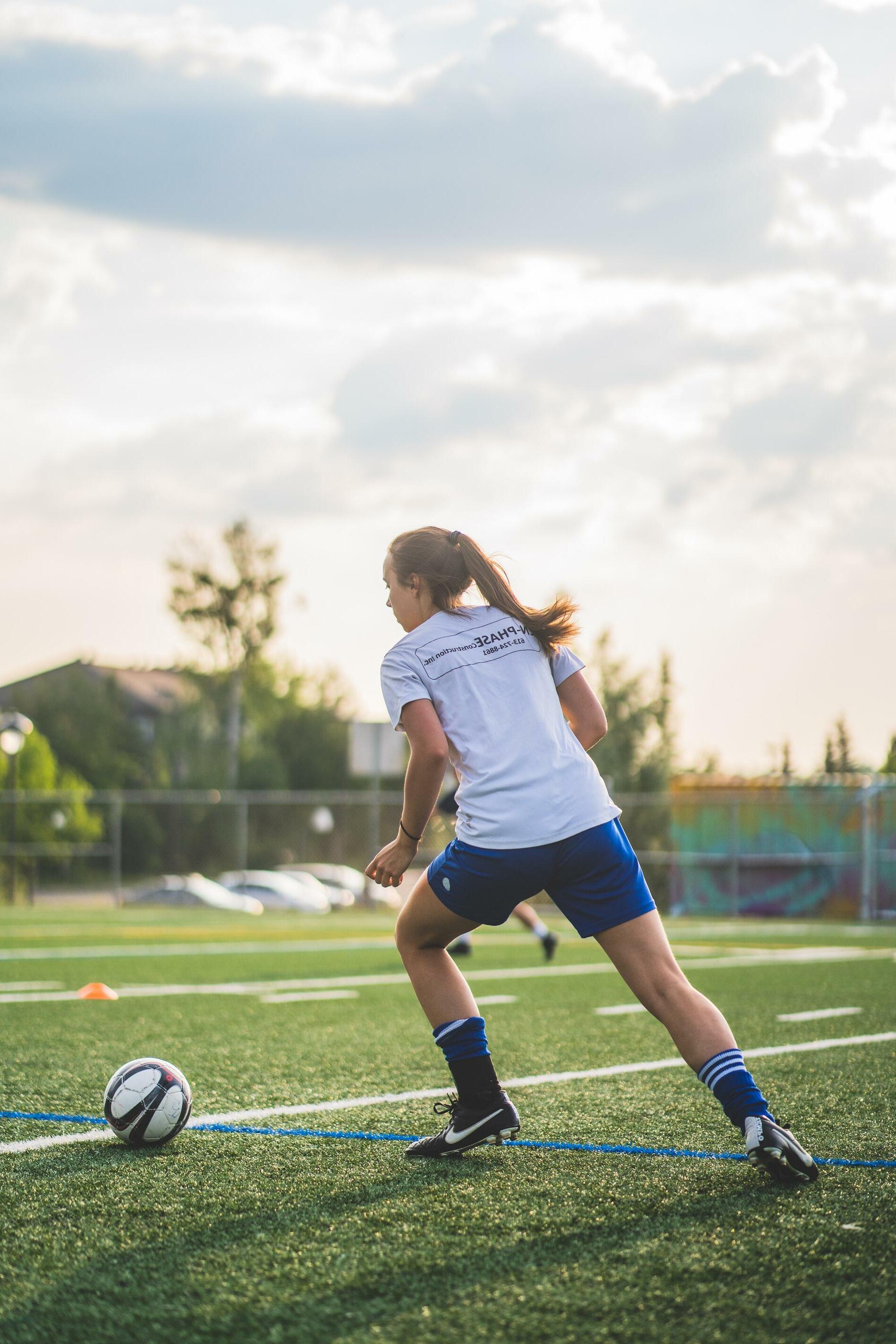

Since its founding in Industries continues Canadian owned and by its principals. The Companies strives to expectations while c becoming the most r cost effective munici
In 1999, Marmak est Municipal Partnershi municipalities implem management solutio Partnership compris whose participation development of vario Marmak continues to offerings and garner for delivering cost ef edge municipal solut
The Ontario Recreation Facilities Association (ORFA) partnered with Marmak in 2016 to develop the RFAM (Recreation Facility Asset Management) solution as a tool to aid recreation staff in the appropriation of their assets by storing inventory, facilitating regular inspections and handling work orders. Once built, the solution was then promoted and marketed as a member service benefit.
In recent years, RFAM has grown to be the solution of choice across North America for the management of recreation assets.
Not only has the number of users grown but also the number of features. These additional features are all based on user suggestion and feedback.
If you want to examine the first artificial indoor ice rink in North America, you’ll have to go back quite a bit—to Feb. 12, 1879, to be exact. That date designates the opening of a rink within New York’s famed Madison Square Garden. This was made possible by more than a mile of wrought-iron pipes carried ammonia brine through a layered floor, cooling it to the freezing point. The floor was then sprayed with 4 inches of water, generating several tons of ice. Today, there are more than 4,500 ice rinks of all shapes, sizes, and purposes in Canada and the U.S. Certainly, the equipment and refrigerant technology below and above the ice has evolved substantially since 1879. However, the adoption of newer cooling technology typically isn’t as fast or widespread in ice arenas as it is in some other industries. In fact, in 2020 it was estimated that one-third of the approximate 4,800 indoor ice rinks in North America were using ammonia to create ice even with safer solutions available for some time.
The Chemours Company, the inventors of Freon™ and Opteon™ refrigerants, has been immersed in refrigeration and air conditioning for nearly a century. Through that time and many partnerships in the ice sports space, we’ve come to understand that many ice facilities—from the smallest community rinks to national league arenas—face unique challenges to transitioning at the pace or to the extent of upgrades they may like. We’ve also come to appreciate the value these rinks have in building communities, inspiring athleticism, and supporting local economies. Lastly, as a company dedicated to taking on the planet’s biggest challenges and creating a better world through the power of our chemistry, we recognize that, with the right support, ice rink facilities can make a significant impact on improving the health and sustainability of our planet—as well as the health and safety of the athletes, spectators and facility staff Inspired by all of this knowledge and background, five years ago Chemours launched an initiative to support ice rink facility operators and managers in navigating the complex regulatory landscapes while improving the efficiency, performance, safety, and sustainability of their venues.
Our initiative is built on the pillars of education, customized solutions, and continual support helping to ensure that the solutions a facility puts in place offers long term sustainability that can transition with the arena as well as the world surrounding it. When we work with a facility manager, we start by understanding their challenges, needs, budget, businesses goals, and visions for the short and long term. We assess their facility, purpose, and the people they serve. In turn, we provide education about everything from current requirements and upcoming regulatory changes to the immediate and long term benefits of retrofits or new equipment, for example From here, we begin to determine the best solution from equipment to the refrigerant that charges it.
Today, Chemours’ Opteon™ XP10 (R 513A) and Opteon™ XP40 (R 449A) are two of the most popular solutions for ice arenas. These HFO blends have environmental advantages over legacy refrigerants—such as R-22 and R-507— offering zero ozone depletion potential (ODP) and lower global warming potential (GWP) Opteon™ XP10 and XP40 also offer excellent energy efficiency from both a fluid perspective and as a critical component to make the most advanced ice building refrigeration systems perform at their peak They are versatile enough to be used in new and retrofitted systems and offer the optimal balance of properties for many facilities potentially resulting in lower total cost of ownership, enhanced performance, decreased overall system energy consumption, improved safety for workers, players and fans.
upgrade their systems in the most responsible and results driven ways stem from strong partnerships we have built throughout the industry. Chemours is proud to have recently entered into a partnership with Marmak, which offers tremendous opportunity for us to extend our commitment to supporting the growth and sustainability of ice venues throughout the U.S. and Canada. Through Marmak and its RFAM platform, facility operators and managers will have enhanced access to Chemours Opteon™ refrigerants. Moreover, we, as a company, will enjoy valuable opportunities to continue providing the education and technical support that ensure facilities remain compliant while providing the quality athletic experiences that support thriving communities. Chemours applauds Marmak for becoming the powerful asset management resource it is, and for advancing its mission to help facilities implement cost effective infrastructure solutions and establish best practices leading to long term success every day.
We are honored to now be part of the Marmak family of resources and encourage facilities to contact Chemours or Marmak to learn more.
supporting more than a hundred ice rink facilities in North America in their refrigeration system transition and we’re just getting started. We remain committed to ensuring thousands more travel the path to environmentally strong and safe solutions that also deliver operational reliability, efficiency, stellar ice performance, venue comfort, and safety for spectators and staff. Recently, we’ve enjoyed “headline” projects that brought our Opteon™ refrigerants to the global stage at three ice sport arenas during the 2022 Winter Games, as well as several well known rinks in the U.S.. With that being said, we have just as much pride and take just as much care in our support of venues like Ontario’s Markham Village Community Centre as it transitions to newer generation refrigerants. To us, these local facilities are the centers of athleticism and communities they serve, and we look forward to continuing to leverage our resources to support their growth.
To learn more about Chemours’ initiative in support of ice venues, other partners we’re collaborating with in this effort, and the Opteon™ portfolio of refrigerants, or to inquire about solutions for your facility, visit Opteon.com, or call 1.866.433.TECH.
The world is now full of acronyms, as depicted in the title of this article. Some of these acronyms have multiple (and unfortunate) meanings, but our population has become very used to dealing with acronyms. Using acronyms is easier and quicker, and that’s why people do it Take a moment to think about the underlying reason why we use acronyms Most people are busy with either work or self induced digital connection overload, which creates a tendency towards needing simple or easy or fast. In the recreation industry in particular, this tendency becomes engrained into the working culture due to continually being asked to “do more with less.” Appling Innovation is the enabler to enhanced viability of our recreation facilities. Over the last decade, there has been increasing pressure on our recreation facilities while social awareness (and in some cases, demands) are more pronounced when it comes to lowering our environmental footprint. A textbook “do more with less” scenario emerges and voila: the very viability of the operation is in question. During this time, the National Hockey League has been collecting community rink industry feedback and evaluating best practices The NHL® is committed to ensuring and enhancing the viability of community rinks in North America Acknowledging that this pursuit requires a big picture and not a singular one size fits all approach, major themes that the League has learned from the industry over the past years are modelled into the Viability Framework developed in partnership with I.B. Storey Inc, the Official Rink Engineering Consultant of the NHL®.
The Viability Framework, (See “Focus on Community Rinks” Facility Forum Summer 2022), is an evaluation tool to ensure we are not missing out on leveraging our full potential. The considerations include safety (patrons, staff & surrounding environment), operating costs (both utility AND external maintenance), internal labor (internal intervention required), regulatory (ex. Technical Safety BC requirements), and optimization (fine tuning / leveraging of equipment for maximum benefit).
The convergence in the recreation industry of Information Technology (IT) with Operational Technology (OT) has yielding an abundance of data to manage and disseminate. In relation to the Viability Framework, this data can be leveraged to enhance or improve safety, reduce operating costs and associated carbon footprint, align regulatory requirements and streamline reporting, reduce internal intervention (internal service) needs and optimize the performance of the facility. Implemented effectively, this IoT turning data to information allows for informed actions.
One of the most under-leveraged approaches is the utilization of asset management tools. Asset management is historically viewed as a financial budget-forecasting tool and, also historically, a lifecycle upgrade with a same-for-same configuration. Step two is the appearance an approved spending list of “upgrades” and the modernization of a conventional approach would be undertaken. The conventional approach, a same-for-same, isn’t ideal in almost all cases. Even our floor mops have become more advanced. There is the belief on underlying recreation facility infrastructure that if something new is purchased to replace “the old one,” it will be “better.” Better (within the eye of the beholder) might mean more efficient or effective but that may not be the case. This situation falls into “the new one will be more efficient” bucket, which is more accurately translated as “the new one will be new.” This could be more efficient or it could be new 1950’s technology. When viewed through the lens of the viability struggle for recreation facilities, the challenge with this conventional way of thinking becomes self-evident.
Recreation facilities are operational intensive due to the very nature of the delivered services. That means that the needs of these facilities are greater. Compounding the financial planning activity is the burden that many organizations are faced with aging infrastructure, leading to prioritization and deferrals, leading to increased “do more with less” mandates.
Leveraging the market convergence, an effective asset management plan can, and perhaps should, contain active monitoring of asset usage and streamlined internal service (ex. work orders) to allow for better and informed decisions regarding asset replacement and true escalating costs of ineffective and inefficient equipment.
But that’s only part of the story. Using an asset management plan, there is effectively a plan for money to be spent. But applying a big-picture review, the opportunity exists to maximize the value of that intended spend, enhancing the viability of the facility leveraging information (converted from data).
Let’s look at a common example in the ice arena industry: the refrigeration plant upgrade. Some asset plans upgrade a component or two of a broader system each year which is a way to “spread out the pain” financially. But this leaves us with a car that has one new tire, one slightly used tire, and a couple of old ones. This makes a technology pivot challenging to implement and traps ownership with the conventional approach. However, combining the asset management information and forecasting tools allows for a big-picture evaluation of the application of new technology and deriving all of the associated benefits that come with that decision.
Considering an entirely new refrigeration plant, which is very heart of any ice arena, is typically viewed as unnecessary since we have that new and slightly used tire. The secondary objection tends to pertain to the single-number sound-bite analysis which results in a disservice to our informed decision making. The example most common to occur is an upgrade from a conventional ice making system to a state-ofthe-art oil-less compressor package. Without getting too far into the weeds, oilless compressors have been operating in the marketplace for nearly 20 years. One leading manufacturer has over 80,000 units installed worldwide – so it’s not exactly new, but it is new to the artificial ice operation. Removing the need for oil brings many layers of simplification and benefit; no oil to purchase, check, drain, or dispose of are only the starters. There’s also the simplification of the system and that yields reliability. There’s less to go wrong and less to maintain. There’s also less to purchase from an equipment standpoint, so these units are highly cost effective. Considering the viability analysis, these units operate with a non-toxic and non-flammable refrigerant which enhances safety for patrons, staff and the surrounding community. Leveraging the new technology unlocks a highly efficient compressor system and reduces operating costs.
Coupled with a new-technology adiabatic cooler, we eliminate water treatment and dramatically reduce water usage. So, the viability summary becomes:
Safety: Enhanced with non-toxic / non-flammable refrigerant.
Service: (Internal intervention) Less operator requirements allowing staff to focus on other tasks.
Regulatory: Reduced requirements for specialized plant rooms.
Operating Costs: Reduced due to leveraged technology, simplicity and external service needs.
Optimization: Highly advanced optimized equipment allowing for better operational information and footprint.
While no situation is ever the same, typical results of this plant approach have yielded 80% reduction in maintenance costs, elimination of water treatment costs, 20% reduction in electricity, and 60% reduction in water usage. The information to get started is often available in the existing asset management plan or system.
The combination of asset management information, budget forecasting, and the implications of new technology results in a Reconfigured Asset Renewal Plan. This achieves the underlying objectives of an asset management plan as well as leveraging viability enhancements impacting the financial, social, and environmental aspects of our recreational facilities, which are the very fabric of our communities.
Everyone is talking about it, so let's talk about it now. Energy Efficiency How about a step further, Building (Automation)Efficiency NewconstructionprojectsareveryefficientwithsomebuildsratedLEEDcertifiedandeven some stating being net zero ready. But what about existing buildings with a limited budget and little to no Automation?Doesthatsoundlikeyourfacility?Let'sstepfurtheragain
Simple Building Automation Systems controlling HVAC only is a great start and will, yes, still provide savings but limited. EvensettingbackthescheduleandsetpointsinasimplefurnaceorRoofTopUnitwillhelp!Thisworkcan be completed in a phased approach Advanced Building Automation Systems are larger and more complex, howeverbycontrollingallHVAC,mechanicalandelectricalsystemswillprovideincreasedsavings
In recreational facilities that have rinks, we typically find that the HVAC Automation and the Ice Plant Automation are separate This causes mechanical and electrical equipment and systems to potentially 'fight' one another Let's say the Ice/slab is higher than normal above setpoint, so why is the Dehumidifier or Bleacher heaters running when the Ice Plant needs to pull the Ice/slab down? Or what potential Heat Recovery in the Ice Plant is any of that waste heat being recovered or are we just rejecting it outside? Having your facilities systems integrated and working together really is key
I've mentioned the Ice Plant and phased approach Not all customers can afford to Automate all or even the majority of mechanical, electrical, refrigeration systems in one phase, but there should be a focus of first, taking control of the biggest consumer in a hockey or curling rink the Ice Plant Done properly, there can be between 15 40% savings by Automating the Ice Plant alone
Advanced Building Automation Systems can also produce significant energy savings from utility meters and Intelligent logic Peak demand limiting, Load shifting and Demand Response Curtailment to name a few, have proven to dramatically lower energy usage while, intelligently, not affecting the user conditions (customer comfort and ice quality) Recent projects have been operating at 16 ekW/ft2 while projects starting up this fall (for the first time) are engineered to operate at ~ 10 ekW/ft2. Impressive.
So, the next time you think about Energy Efficiency, look closely, you might be closer to your goal then you realize.
Integrationissoimportantandisquietfranklythekeythesuccess. Thefloorplangraphicandtheenergyflowof thesystem,theRontheleftstandsforrefrigerationandtherefrigerationplantitself,fromhereHeating,Coolingand Dehumidification to the rink space. Continuing to move to the right, heat to the Common Areas, offices, meeting rooms,andcommunityrooms Stillpassing100%recoveredheattotheturffield,whichisextremelyefficient! Ifthe iceisout(likeitistoday)wehavesmart,integratedwaterheaterstoheatonlyloadsthatactuallyrequireitfromthe Thermal Management System We’ve all heard of the IoT, or the internet of things This facility is completely integratedwithseveraldifferentmanufacture’sequipmentworkingandcommunicatingtogetheronasingleplatform, with complete mobility and access from any smart device, no plug ins or applications are required Just simply securelylogintoyoursystem,fromanybrowser,fromanywhere,tomonitorandcontrolyourfacility Thefloorplan graphicalsoshowsallspacetemperatures,humidityandairqualitylevelswithaspectrumgraphicquicklyindicatingif temperaturesareat,aboveorbelowsetpoint. OthergraphicsshowstheHotWaterSystemandtheintelligentwater heaters Main Air Handling Unit graphic with a (Heated from the Ice Plant) Glycol heating coil instead of the traditionalnaturalgasfiredappliance
Not only can you integrate Building Equipment, but also BuildingSystems GuestAutomationisproudtopartnerwith Marmak/RFAM on integrating our two systems to holistically work together to provide facilities with energy costing information, providing lifecycle planning, asset performance/efficiencyandhiddenenergycost.
As facility managers, it is your responsibility to manage the assets in your charge to ensure they are effectively operational for as long as budgets allow and certainly for the expected life of the asset itself. Regular scheduled maintenance of structures and components within facilities helps to extend the life of your assets and for budgeting purposes, that is critical. Managing your assets however, from the point of view of risk, provides a different viewpoint from which to fashion your maintenance tasks and inspection schedules. This perspective still serves the purpose of protecting your assets from deterioration and harm but also against costly liability claims. If an asset, be it an ice rink, a community centre, even an outdoor trail or track is not managed properly, it poses a potential loss for the municipality or owner of the asset, either by the complete loss of the asset itself through gradual or catastrophic destruction, or by a third-party visitor injuring themselves in, or on, the asset. The resulting lawsuit can be equally devastating to the bottom line of a facility or municipality.
In order to assess exposures, facility managers must first recognize and inventory all of the assets they are responsible for. In a multi-rink arena, that will include separate components of the structure; from the coffee shop or restaurant, the skate-sharpening store, to the sprinkler system, or the chiller plant. Utilizing your pre-existing asset inspection schedule is a good place to start, but don’t let that be your only guide. Each time a new component to a facility is added, inspections of that particular element should be added as per the manufacturer’s recommendations. A holistic assessment should be undertaken to determine how that component can or will affect the entire facility. A workflow should be in place to insert the component into the inspection schedule. Some inspections are governed by legislation and regulations (TSSA, TSBC etc.) for ice plants or aquatics. These legislated inspection requirements should be fully understood and considered a bare minimum for the purposes of risk management. Washrooms, entrances and exits may not have a legislated requirement, but this work must still be carried out to ensure that the facility is in good repair and to illustrate that public safety is front-of-mind.
When considering liability exposures, we must look to not only hazards and exposures inside the structure but to those found outside as well. Slip and fall and trip and fall accidents are undoubtedly the most common incidents that plague facilities and arenas and municipalities in general. There is an argument to be made that the only way to eliminate slip, trip and falls is to shutter the facility entirely so that no one can enter. Appealing as this might seem some days, especially in this time of staff shortages and pandemics, closing the facility may serve to reduce the incidents inside the facility but will do nothing to reduce exposure on the tracks, fields and trails outside the facility. Because delivering recreational services to the community is the prime directive, we suggest instead that the areas need to be de risked as much as possible.
Deep in the thick of the pandemic, the importance of public outdoor spaces and trails became a priority for those that were searching for sanctuary outdoors in nature. This caused the ORFA Board of Directors to reiterate the industry definition of a recreation facility: “any land, premises, location or thing at or upon which offers a recreation or leisure experience for all” The definition affirmed a more expansive responsibility of care and control over recreational compliance in order to meet the obligations of Covid regulations. British Columbia has similar guidelines in place. Given that the definition of facility includes those outdoor spaces, we need to look to how we can be made to be responsible for them and to what degree.
Each Province and Territory has Occupiers Liability legislation which details responsibilities and requirements and also details who is an Occupier for the purposes of that legislation. In general terms an Occupier controls access and egress to a facility and when we are dealing with a facility, that can be straightforward. But who is the Occupier of a sports field? Who is the Occupier of a bike park or a trail? If someone is hurt while on those outdoor premises, the facility or municipality could very well be exposed to damages, especially if they have not taken the requisite care and maintenance of these important outdoor areas. Now that we know there will be responsibility as well as risk exposures, how do we start assessing those exposures so we can begin to manage them? Using the existing asset management process you presently use is a good place to start, but should always be subject to review. In order to start the process, you must begin with a thorough inventory of all the assets you are responsible for.
You must inventory all areas of responsibility (both indoors and out), and again, using your existing schedules and checklists in a structured way can help grapple with what at times can be an overwhelming task. Pay special attention to “border” areas; places that may indeed fall outside the scope of your responsibilities but by their proximity to your space could cause for concern. If there is an adjacent school yard for instance, that borders your park or sports field and you share a common trail, you need to be certain where your responsibility ends and where the other “Occupier’s” begins. The way that claims come in, it may be determined that though the victim thought they were on school property when they fell with further investigation, it was in fact part of your recreational facility area. Outdoor areas that include boundary spaces can be problematic when establishing responsibility. Typically, responsibility will be determined by a pre-existing agreement which will map out the specific areas of accountability.
Once the areas of responsibility are established, a customized and dynamic checklist should apply to them Checklists are used to ensure that proper work has been carried out and that nothing was missed The process of checking for hazards should start with the checklist, but front line staff should be encouraged to not only be limited to the template provided The form should act as merely a starting point to inspections. Consequently checklists, either physical or automated, should have ample space for notations and observations. The action plan behind a checklist is equally important: If the inspection fails, or if a notation is made, your Standard Operating Procedure (SOP) should contain an action plan escalating the matter, where necessary to management, and that action plan should be tracked This cannot be overstated; having a series of checklists that continually shows a fail, or a deficiency, with no discernible action taken, is not only inadequate asset management but also really bad risk management Again, checklists should be customized to a particular scenario: different checklists unique to stairways, vacant buildings, washrooms, shower rooms, and changing rooms should be tailored to each area and each hazard. The checklists should be dynamic; if a new condition exists that requires a change (perhaps a pandemic which requires enhanced cleaning, hand sanitizer, disconnection of air dryers) the list must be able to include and respond to these new circumstances. We use these checklists to confirm that the work has been done but more importantly these properly completed checklists also act as evidence of that good work The most common complaint around job logs and checklists is the difficulty in compelling staff to complete the process as part of their workflow From a worker perspective, the task itself seems fruitless, a make work project that just enables “big brother” to watch them and to make sure they are doing their work. Why would anyone want to do it? Certainly, we have all seen sweep records and job logs that have been “filled out” with nothing more than an illegible signature and a tick mark.
That mindset oftentimes correlates with a disconnect between management and front-line staff. If indeed these work logs are being used to incentivize or punish staff for being late or not doing their job properly, management runs the risk that not only will staff be demoralized but that they may not even do the task, let alone complete the checklist. Luckily, automated asset management systems are enabling staff to complete real-time inspection logs which create a documented action plan when a problem is discovered. Staff member can see this as an efficient way to actually complete their tasks rather than “ticking a box” to make the boss happy. We do often see facility managers who have taken the time to create a fully fleshed-out Standard Operating Procedure, but then there is no real connection between the prescribed work of the front-line workers and that SOP. Educating staff of the importance of documentation and the work that they do will serve to illustrate why the sweep records and consistent procedures are a necessity. Making staff aware of the action that is taken by management when a deficiency or hazard is discovered shows them the importance of the checklist and the work they do.
When a lawsuit is initiated by a Plaintiff, allegations will typically state some form of negligence on the part of the operator of the facility: The Plaintiff alleges that the arena operator neglected to address water on the floor causing a slippery surface. The Plaintiff alleges that this area had been neglected for some time, though the fall occurred in an area where visitors would enter the facility in inclement weather. The Plaintiff will show that there had been substantial snow the evening in question. The Plaintiff alleges that they did slip on that wet area. The Plaintiff further alleges that due to the negligence of the facility operator, they suffered catastrophic injuries when they fell, breaking their hip, their shoulder, and suffering a concussion.
If the facility can illustrate clearly that the area was kept clean and dry, they will be able to dispute the allegations of negligence that the plaintiff is making. They can show that staff took extra care when the snow was forecast to ensure there were mats placed at the door and there are job logs and checklists to illustrate the work was done. Then, not only can the claim be properly defended, but it is more than probable the claim itself will be shut down prior to expensive litigation commencing because plaintiff counsel can assess that their allegations will likely not be provable against a wall of good solid evidence to the contrary.
Pertinent inspection documentation paints a picture: it illustrates, often to a court, that management and workers are consistent in their approach to risk management and facility maintenance: We check the weather every day and note it. If inclement weather is expected staff are notified to take extra care at all entry ways and ensure that the mats are changed more regularly. See? Here are emails to staff for three months this Winter. Here are the sweep records to show that the staff changed the mats at twice the rate and enhanced mopping and erected “wet floor” signage. We even get our staff to take photos and attach them to the sweep records – here is that evidence. Even if a loss happens at a different time, this type of regimen shows that the arena always takes proper care to ensure safety as well as the continued longevity of the facility, its equipment and systems. It demonstrates a culture of best practice.
Courts consistently uphold the idea that if it cannot be proven, it was not done. If rink managers cannot show that the floor was kept dry, the plaintiff’s assertion that the floor was wet, will in all likelihood, be believed. Because no evidence was provided to demonstrate that the work was done, it shows instead that in all likelihood the facility is lackadaisical about document-keeping and potentially, about safety altogether. As a result, the lack of overall documentation helps to bolster the Plaintiff’s allegations: it paints a negative picture. Though the extra work of tracking front-line tasks can seem daunting and some days it might feel like there is not enough staff and not enough time to coordinate the required record-keeping and implement those required processes, the work is integral to all that you do as a facility manager.
There are many other sources of evidence that should be included in your assessments: invoices illustrate particular parts were purchased that facilitate regular repairs (think floor mat contracts or gaskets for chillers or new fire extinguishers); work orders, if repairs are required on a bleacher or on a dripping water fountain; incident or near-miss reports can speak to root-cause of losses and occurrences which may not constitute a loss or a claim but nevertheless should be noted and acted upon. The power of good recordkeeping and consistent practices when presenting evidence cannot be overstated. There are ample examples of claims in which checklists and job logs were used effectively to defend against claims. An excellent example of evidence “painting a picture” of good housekeeping and consistent practices Corbin v. Halifax (Regional Municipality), exemplifies the importance of documentation coupled with consistent procedures. The Plaintiff suffered a fall at an aquatics facility in the shower room and sued the facility for her injuries claiming that the tile used was not appropriate for a shower room. The facility had a set a procedure in place when incidents occurred and called the injured patron after the incident occurred to ensure she was okay and to follow up the manager fully documented the exchange. They were able to show that precisely because there were no other incident reports pertaining to the shower room, that this person was the only one to have ever fallen in there. Consequently, the shower room tiles were not inappropriate.
The judge found against the Plaintiff because the defendant was able to show that their cleaning and monitoring procedures met a reasonable standard of care. The facility provided sufficient evidence to illustrate staff conscientiously fulfilled their obligations. Remember that though it may not seem like it, courts do not expect perfection. Rather, the expectation is one of reasonableness.
By using checklists and job logs that consider hazards as well as asset management, you can be assured that the prescribed maintenance is being completed in order keep the facility and grounds in top running shape and ensure it is compliant and safe. When caring for your outdoor assets, fields and trails, be sure to include thorough hazard inspections in your Asset Management plan. These valuable documents should provide more than just ticked boxes rather, the checklist should denote an action plan for management to act when front-line workers become aware of a problem. That action plan should be documented. Frontline staff need to be aware of the importance of these documents; they are not just make-work projects. Lastly, remember Asset Management is a team effort: If managers simply overwhelm front-line staff with a list of to-do inspections they run the risk that nothing will get done – checklist exhaustion is real – there has to be a dynamic feedback loop and action plan.
This article is a collaborative project together with Intact Public Entities (IPE) and Marmak. Marmak and IPE have partnered together to create meaningful articles and presentations and educational content to help keep recreational spaces safe and operational. If you are interested in learning more about the importance of risk management to your organization, please feel free to contact Marmak at: info@marmak.ca.
Warrior Ice Arena will now automate their facility management, ice operations and preventative maintenance by using RFAM.
RFAM is used by 250+ Rinks across North America to streamline and improve their Asset Management practices.
"We are excited to start using RFAM and all it has to offer a facility like ours This will help streamline and digitize our logs and spreadsheets to all live in one place, making day to day operations easier for our operations team, and easier to oversee by our management team "