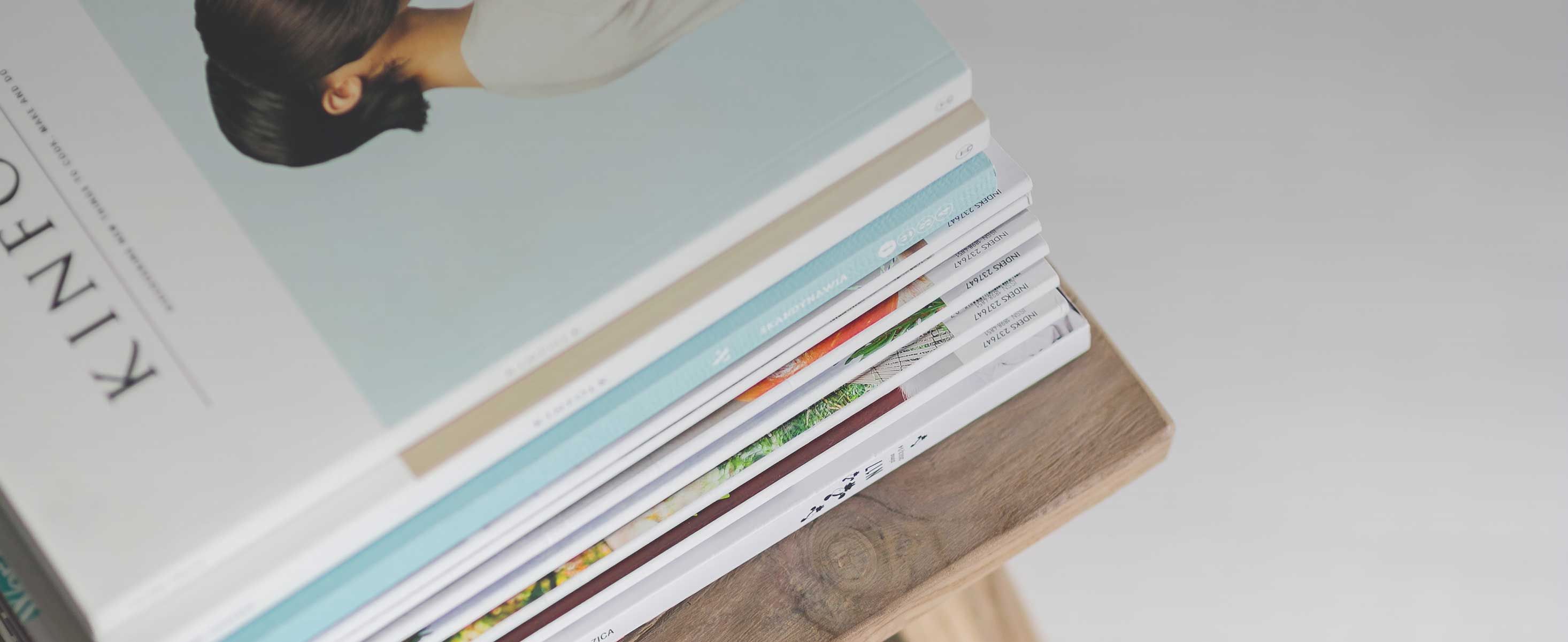
2 minute read
Essential Resource - Money Well Spent
TOOLBOX SAFETY MEETING
BY KIM HODNE SAFETY CONSULTANT
A common denominator for all business is cost. Is their value in conducting a Toolbox Safety meeting? The meeting has merit and is an opportunity to strengthen a company’s workplace safety program, but it has to make sense and more importantly be effective. It must not be viewed by management as a waste of time and money and employees need to embrace and participate in the effort. At the end of the day, it’s about safety communication, not just checking a box to fulfill a policy. It’s a time to reinforce our commitment to a safe and healthy workplace. To introduce new gear that improves safety, review existing policy or simply discuss relevant hazards on the jobsite and how to address those hazards.
For new employees toolbox safety meetings are a chance to learn and ask questions, for veteran employees it provides an opportunity to teach, to share their experience in safe work practices which usually start with, “we had this guy working one time…” or, “I remember this job we were doing three years ago and…”. Sharing knowledge on a topic that’s relatable and relevant goes along way in not only safety, but team building and trust.
The problem I most often hear out in the field on toolbox talks is there are no new topics and nobody wants to lead the talk. Let’s face it, not every leader in the field is comfortable speaking/teaching to a crowd, even if its small and well known to them. So, let us first address the issue of safety topics. I realize there are only so many times we can talk ladder safety, slip trips and falls or PPE, but I also know there are a great many relevant “other” safety issues to discuss. When was the last time we talked about compressed gas cylinders, housekeeping, eyewash stations, pneumatic nail gun safety or hearing protection? Options and variety are key to a good program. MBI & CSSI have over 150 topics to choose from, all easily delivered in under thirty minutes which includes time for Q&A. The task of conducting the talk can be shared between crew members, if someone is good with handling compressed gas cylinders. The one who is well versed in use/safety of nail guns can teach it. Utilize the talent on your team. It’s not an hour-long power point training class. It’s a 10-15-minute conversation that is important to the safe operation of the jobsite everyone's a part of. Professionally speaking, I believe it is money well spent when done genuinely with purpose and buy-in by all levels. Resource and moral support from the front office through delivery in the field without it perceived as burdensome or time wasted. Consistency is key, planned by leadership and expected by the crew. And just as important are topics or issues that resonate/matter to the team, gets their attention and allows for input. Over the years I’ve seen the good and the bad, the successful and not so successful and the ones that work are the programs that engage the crew in a meaningful way. It has to be relevant. If it’s not, well then it’s not money well spent.