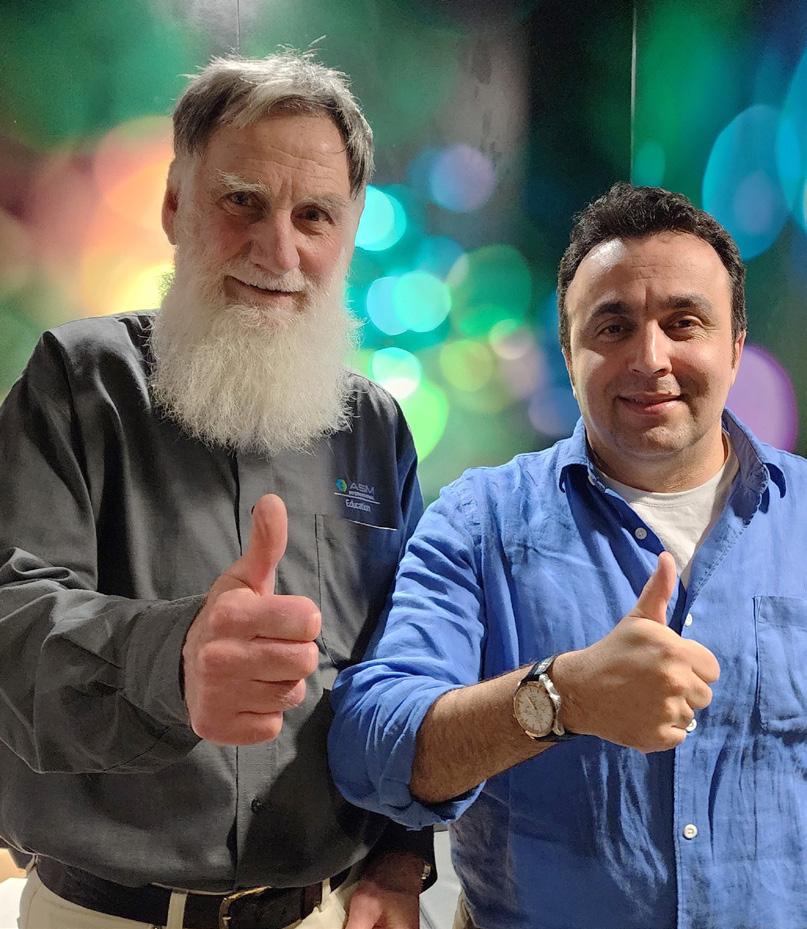
4 minute read
WA Branch Technical Meeting - 9 September 2024 Surface Engineering, the working face for industry
Source: Prof Chris Berndt, SEAM ARC Training Centre
Distinguished Professor Chris Berndt, from Swinburne University, is Director of the ARC Training Centre for Surface Engineering for Advanced Materials (SEAM). SEAM is now at the end of its five-year ARC funding period, and Chris’ presentation described some of its achievements, provided a snapshot view of several projects, and outlined potential future directions.
The Centre’s goal has been to develop postgraduate professional materials engineers, who through direct involvement with industry during their research studies, are available for “plug and play” employment after graduation. SEAM is a joint venture between Swinburne, RMIT and UniSA, with several industry partners. Together these participants have leveraged the $4.9m ARC grant to a total value of $9.3m in cash and in kind. Continued funding has depended on meeting quarterly targets and SEAM’s success led to an increase of $3.5m on the original planned funding.
Chris used the nine Technology Readiness Levels, from basic research (TRL-1) to full commercial deployment (TRL-9) in characterising SEAM’s research as TRL-6 to TRL-7 (verified protypes and demonstrated pilot systems).
SEAM has undertaken 15 projects working in teams of around ten people per project. It has attracted 25 PhD student researchers and eight postdoctoral fellows. From these, Chris only had time to refer briefly to just a few.
The first project he talked about was development of a coating to reduce slag deposition on the boiler tubes of coal-fired power stations. Because of the practical problems of working on operating boilers, this involved developing a simulated boiler environment in which to test various coatings. The approach taken in developing the coating was biomimetic, imitating the way the surface structures of leaves on some plants give hydrophobic properties allowing them to shed water. A sprayed coating was developed that had a similar surface topology, and this was shown to produce a significant improvement in the simulated boiler tubes.
Another project involved surface treatment for improved tungsten carbide cutting tool performance. This research was largely undertaken on-site in a production facility. The challenge in this project was dealing with the two-phase structure of tungsten carbide composites, and the approach taken involved grinding, electropolishing and applying multiple PVD coatings.
Another project is kinetic fusion coating, or cold spraying. This project, involving two PhD students and three postdoctoral fellows, characterised around 130 titanium powders and used artificial intelligence-guided modelling for process optimisation. Work is continuing the use of shot peening to reduce residual stress.
The last project Chris described concerned the ‘LaserBond’ process for applying thermal spray coating to novel substrates, notably to glass fibre composites. This involves metallisation of the composite surface with metallic flash coating, followed by application of the final coating by HVOF (high velocity oxygen fuel) spraying. Carbon dioxide colling is used to keep the temperature rise on the composite surface to less than 35 °C. The advantage is that the process can produce components with desired surface properties but with a weight saving of up to 80% compared to using a metallic substrate.
Looking ahead, the joint venture partners are seeking to establish an ARC Centre of Excellence, four times the size of SEAM. So far, six universities intend to participate, and industry partners are being sought to put together a competitive proposal to put to the ARC for $35m funding over seven years.
Funding will support around 80 postgraduate students and 20 postdoctoral fellows and will extend to sustainable materials more generally than just surface engineering. In terms of technology readiness levels, the aim will be TRL-4 (prototype validation), the level often associated with the ‘valley of death’ between proof of concept and commercial success.
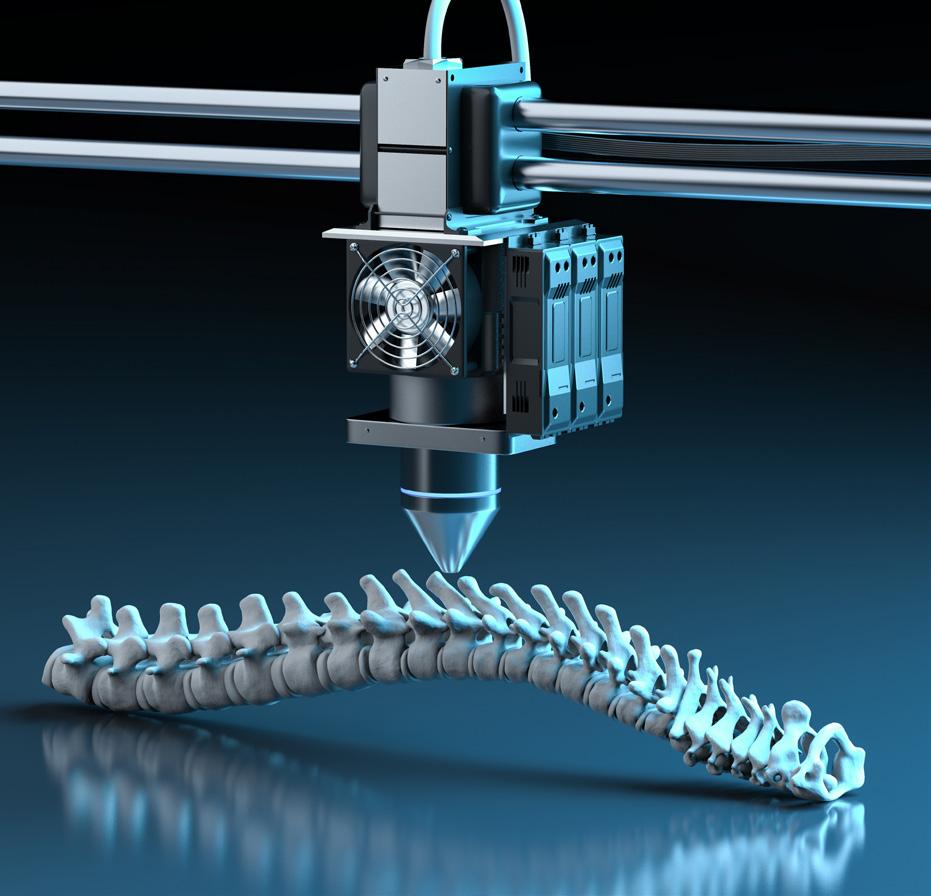
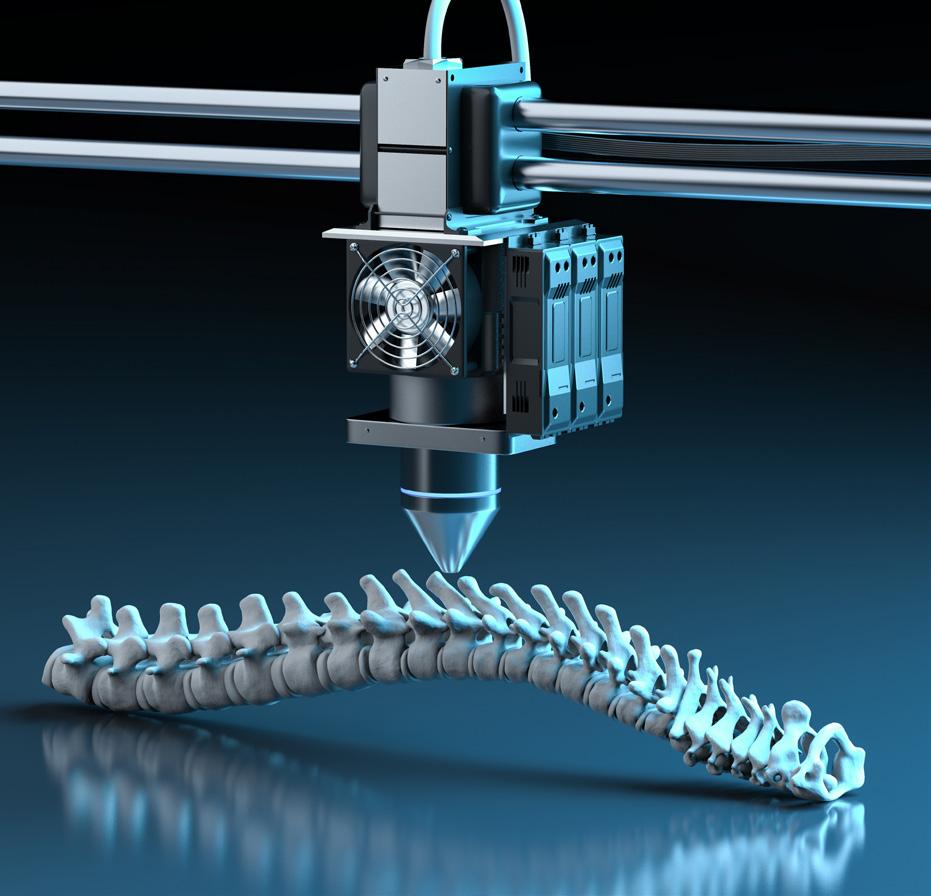
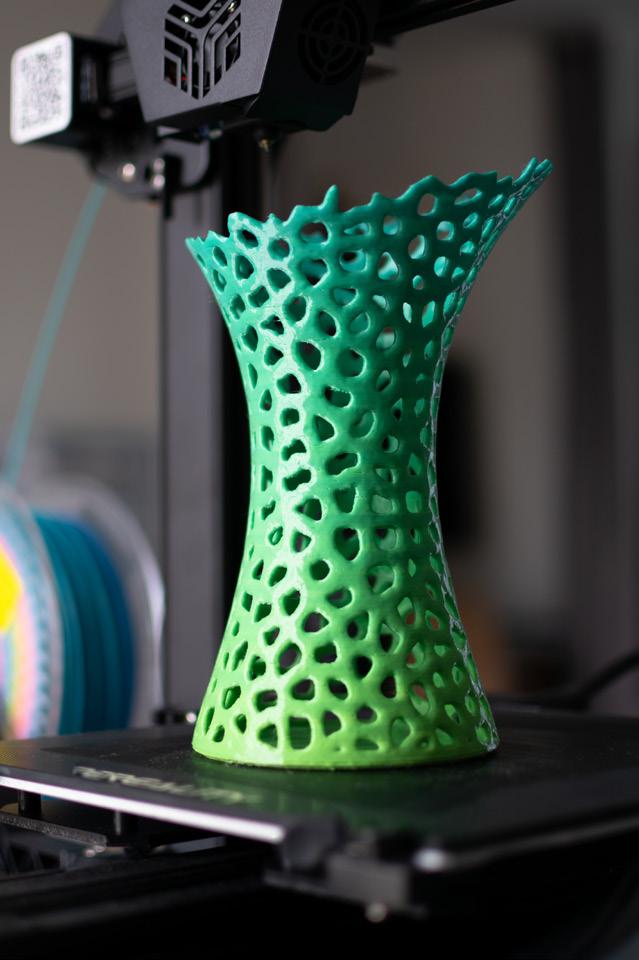
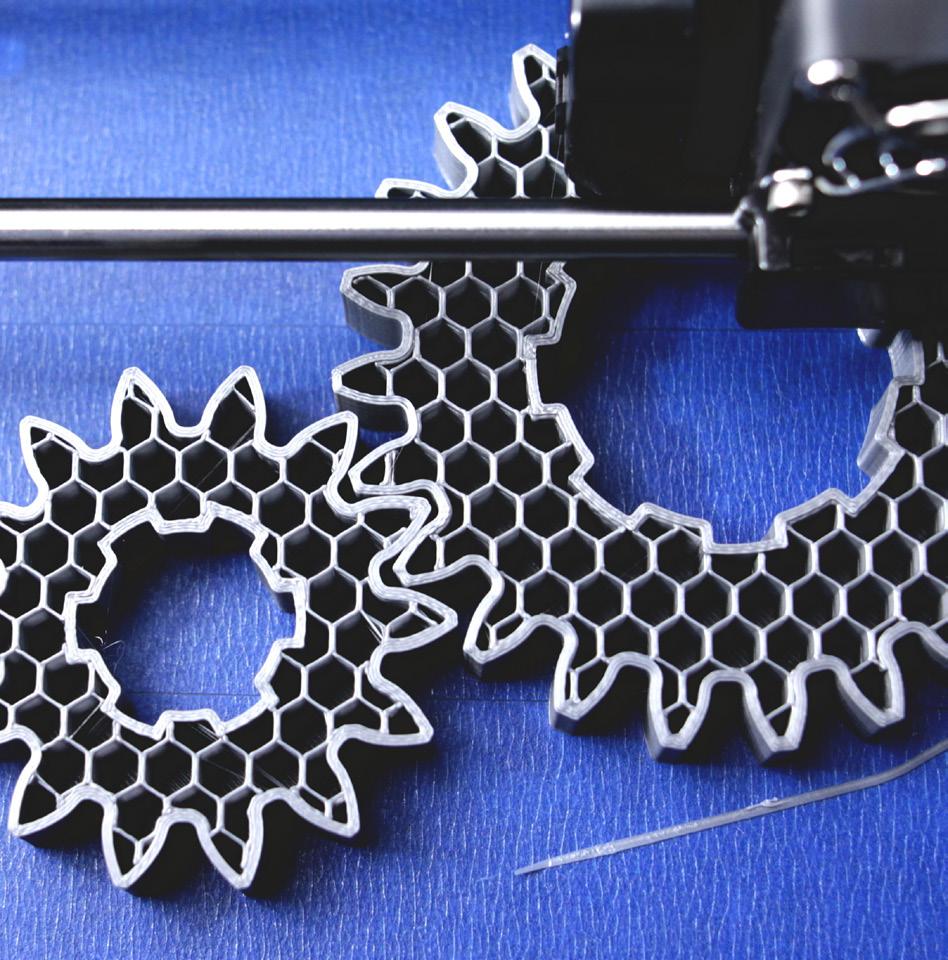
1 - 3 JU LY 2 025
RMIT UNIVERSITY, MELBOURNE
The 4th Asia-Pacific International Conference on Additive Manufacturing (APICAM) is the not-to-be-missed industry conference of 2025.
The 4th Asia-Pacific International Conference on Additive Manufacturing (APICAM) is the not-to-be-missed industry conference of 2025.
The 4th Asia-Pacific International Conference on Additive Manufacturing (APICAM) is the not-to-be-missed industry conference of 2025.
APICAM was created to provide an opportunity for industry professionals and thinkers to come together, share knowledge and engage in the type of networking that is vital to the furthering of the additive manufacturing industry.
APICAM was created to provide an opportunity for industry professionals and thinkers to come together, share knowledge and engage in the type of networking that is vital to the furthering of the additive manufacturing industry.
Some of the leading minds in the industry will give presentations on pressing issues and the ways in which innovations can navigate challenges. Important areas such as 3D printing and additive manufacturing in the automotive, biomedical, defence and aerospace industries will be covered by experts from each respective field.
Some of the leading minds in the industry will give presentations on pressing issues and the ways in which innovations can navigate challenges. Important areas such as 3D printing and additive manufacturing in the automotive, biomedical, defence and aerospace industries will be covered by experts from each respective field.
The purpose of this conference is to provide a focused forum for the presentation of advanced research and improved understanding of various aspects of additive manufacturing.
The purpose of this conference is to provide a focused forum for the presentation of advanced research and improved understanding of various aspects of additive manufacturing.
The APICAM2025 organizing committee is seeking abstracts for either an oral or poster presentation. .
The APICAM2025 organizing committee is seeking abstracts for either an oral or poster presentation. .
Enquiries:
Enquiries: Tanya Smith | Materials Australia +61 3 9326 7266 | imea@materialsaustralia.com.au
1 MARCH 2 02 5
Abstracts
Additive Manufacturing Defence Application
Additive Manufacturing of Electronic Devices
Additive Manufacturing Green/Clean Energy
Additive Manufacturing Space Application
Additive Manufacturing Post - Processing
Bioprinting and Biomaterials
Ceramic and Concrete Additive Manufacturing
Design, Qualification and Certification
Digital Manufacturing
Emerging Additive Manufacturing Technologies
Metal Additive Manufacturing
Modelling and Simulations
Polymer Additive Manufacturing
Sustainability