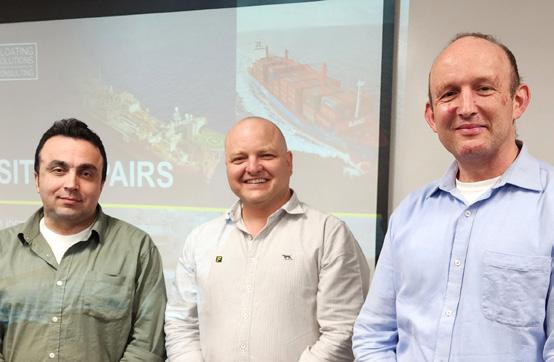
4 minute read
WA Branch Technical Meeting - 7 October 2024 Composite Repairs in a Marine Environment
Source: Jason LeCoultre and Matthew Williamson
Jason LeCoultre is the founder and Managing Director of FUZE Solutions, a composite technology focussed business that provides solutions to the oil & gas, mining and defence industries. Matthew Williamson is Principal Naval Architect with Floating Solutions Consulting in Perth.
Jason has worked for more than twenty years in structural composites, servicing the mining industry and oil & gas industry floating assets. Mathhew’s focus is on reducing in-service structural risk on ships, including naval vessels. Their joint presentation addressed the question of why composites are not used more often for ship repairs, and what might be done to change this situation. In doing so, they drew on a paper that they, together with Peter Butt, Chief Technology Officer at FUZE Solutions, had recently presented at a defence industries conference.
As an overview, Jason pointed out that the use of composites for structures and in structural repair is well proven in multiple industries and is extensively documented. They started as a hightech option for aircraft and spacecraft in the 1970s and were then widely adopted in lower tech uses, especially for repairs, in oil & gas and mining industries. However, while composite repairs in ships were well established in the 1990s, they currently aren’t much used. What had happened to cause this?
Jason and Matt used role play to demonstrate the difficulty of getting approval for a composite repair to a ship. Jason took the part of an engineer who was trying to convince Matt to approve a composite repair to a cracked steel structure, pointing out the advantages of a repair that could be made in three days, with no hot work. The standard welding repair would take three weeks, and would be much more disruptive, but Matt pointed out since it was standard it could be approved at a relatively low level. Because composite repairs are not standard, it was likely that the weld repair would be completed before the necessary special approval could be obtained for the composite option.
From a project management viewpoint, the standard repair was much more attractive as the schedule was predictable and approvals were easy to get, even though it would take longer and the repair would be more expensive.
In short, the barriers to the use of composites are not essentially technical but arise because they are not included in standards and guidelines. Composites are not part of the ‘tool kit’ for structural repair in ships. The impact on schedules of the need for, and uncertainty of, individual approval is a strong disincentive to their use.
Basically, in ship repair there is a vicious circle of ignorance, with general lack of experience, limited knowledge, few suppliers, no standard applications, and no approved processes. Ways of breaking this circle could include changes to contract structures, bringing in outside experience, and having to deal with situations where there is no other option, other than to use composites. Matt described how the ‘no other option’ situation had arisen in the UK in the 1990s with a particularly complex repair that affected a class of naval vessels. However, unlike the case with aircraft repair where the use of composites has become embedded in repair manuals, once the pressing need had been resolved, interest in composites for ship repair waned. Faced with lack of demand, suppliers moved to other customers, notably in the emerging wind turbine industry. The supporting infrastructure for composite ship repairs was lost, and the circle of ignorance was reestablished.
What is needed is route to certification for composite repairs to remove the need for specific approval for every proposed use. This would ensure that approval requires the same level of authority as the equivalent steel repair. Matt explained that a key requirement is demonstrating that there is no baseline configuration change because of the repair. That is, that it doesn’t change asset capability, and can be documented without having to change fleet-wide design drawings. Jason and Matt foresee a path towards this through linking composite repairs to strategy and language used in the Australian Government Sovereign Defence Industry Priorities (SDIP).
Questions from the audience brought out some interesting background on ship design, maintenance and repair. Matt pointed out that ship design is not necessarily aimed at the lightest possible structure and general corrosion of plates that were originally thicker than necessary can even be looked on as ‘post-construction lightening’. In repairing a forty-year-old ship it is not necessary to replace every part with the original thickness of steel.
The role of shipping classification societies, such as Lloyd’s Register and DNV, was also raised. Compared with steel and welding, there is relatively little open discussion and knowledgesharing regarding composite repairs. Even in the oil & gas industry clients tend not to talk about these repairs, although they are extensively used. Various possible for reasons for this include respect for supplier’s intellectual property, and sensitivity to disclosing situations where there were no other repair options.
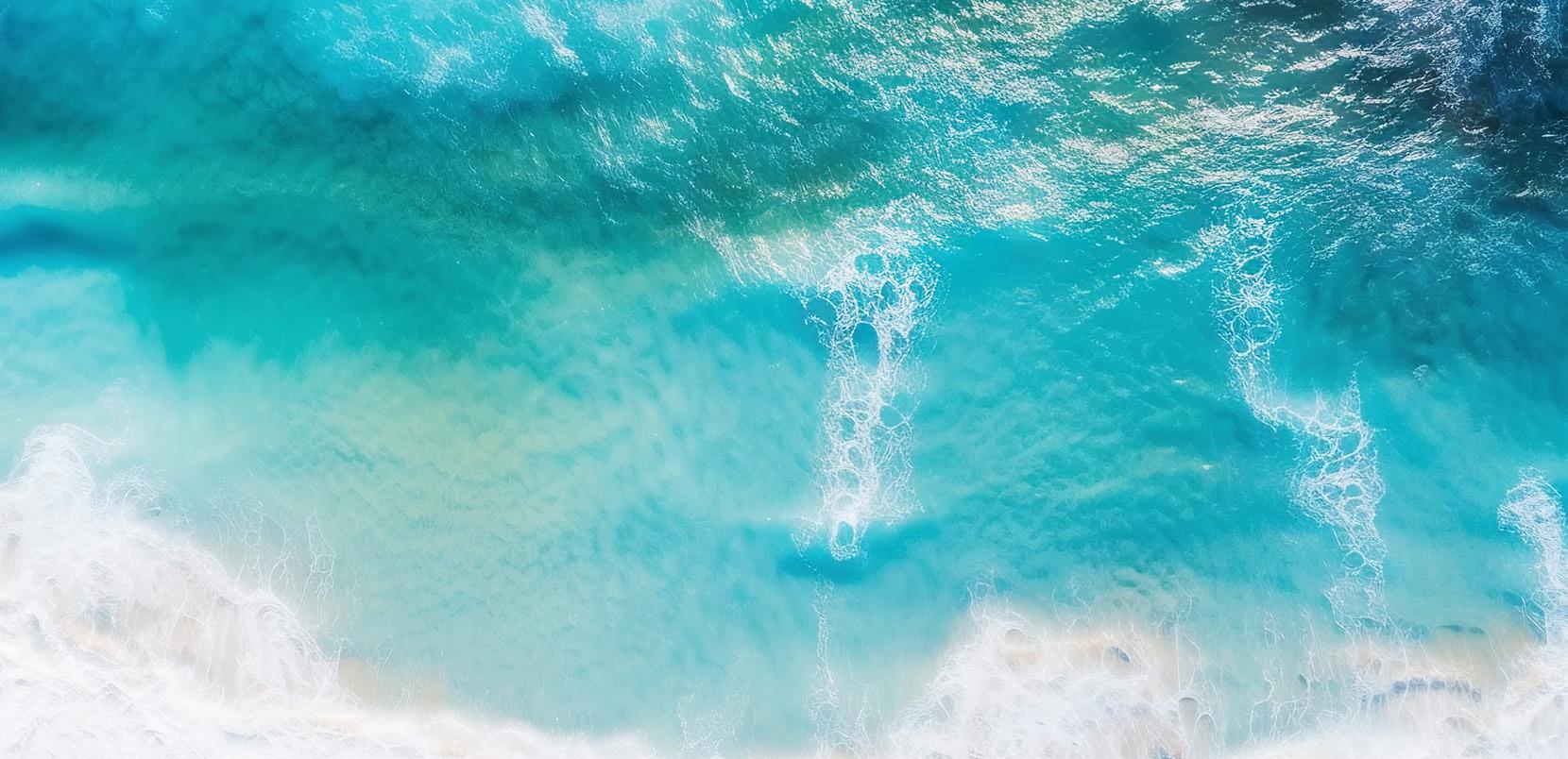
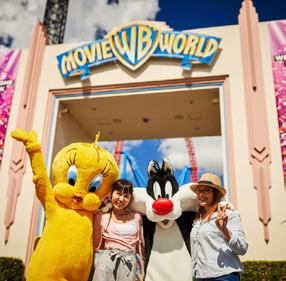
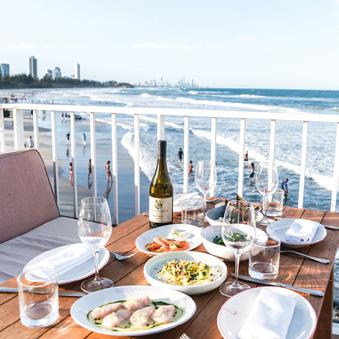
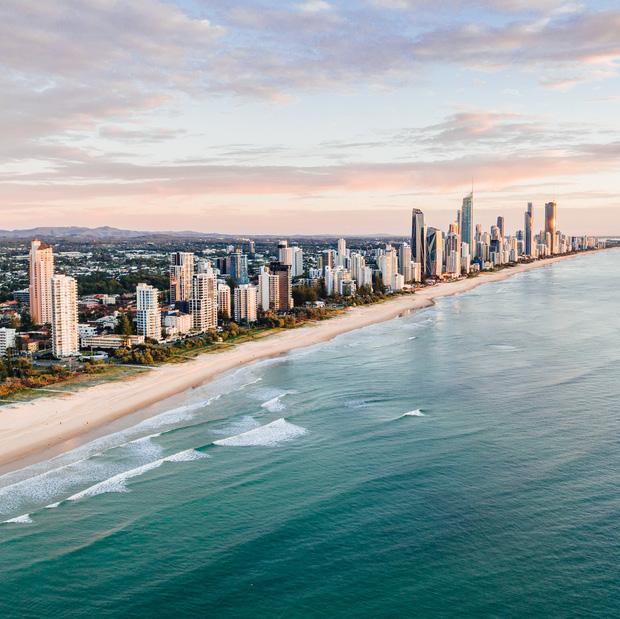
The Pacific Rim International Conference on Advanced Materials and Processing is held every three years, jointly sponsored by the Chinese Society for Metals (CSM), The Japan Institute of Metals and Materials (JIMM), The Korean Institute of Metals and Materials (KIM), Materials Australia (MA), and The Minerals, Metals and Materials Society (TMS).
The purpose of PRICM is to provide an attractive forum for the exchange of scientific and technological information on materials and processing. PRICM-12 will be held in Gold Coast on August 9-13, 2026, hosted by Materials Australia.
PRICM-12 aims to bring together leading scientists, technologists and engineers from the Asia-Pacific region and around the world to discuss contemporary discoveries and innovations in the rapidly evolving field of materials and processing. This event is also intended to foster stronger and closer interactions between materials practitioners and their international counterparts.
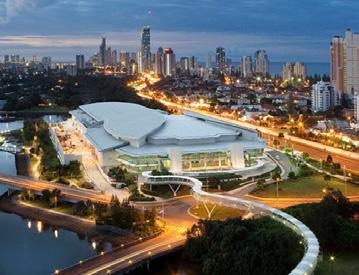

9-13 AUGUST 2026
Gold Coast Convention & Exhibition Centre
ORGANIZING SOCIETY
Materials Australia
Tanya Smith +61 3 9326 7266 pricm12@materialsaustralia.com.au
This conference will cover most aspects of advanced materials and their manufacturing processes. It has 15 symposia:
Symposium A: Advanced Steels and Properties
Symposium B: Advanced Processing of Materials
Symposium C: Structural Materials for High Temperature
Symposium D: Light Metals and Alloys
Symposium E: Additive Manufacturing
Symposium F: Thin Films and Surface Engineering
Symposium G: Materials for Energy Storage and Generation
Symposium H: Electronic and Magnetic Materials
Symposium I: Biomaterials and Soft Materials and their Application
Symposium J: Materials Characterization and in situ/3D/4D Analysis
Symposium K: High-Entropy Materials and Amorphous Materials
Symposium L: Composite, Coating and HeteroMaterials
Symposium M: Nano Materials and Nano Severe Plastic Deformation
Symposium N: Computational Materials and Artificial Intelligence
Symposium O: Materials for Sustainability (Green Steel, Recycling, and Corrosion)
On behalf of the organising committee, it is our great pleasure to cordially invite you to PRICM-12.
Professor Jianfeng Nie
Organizing Chair of PRICM12