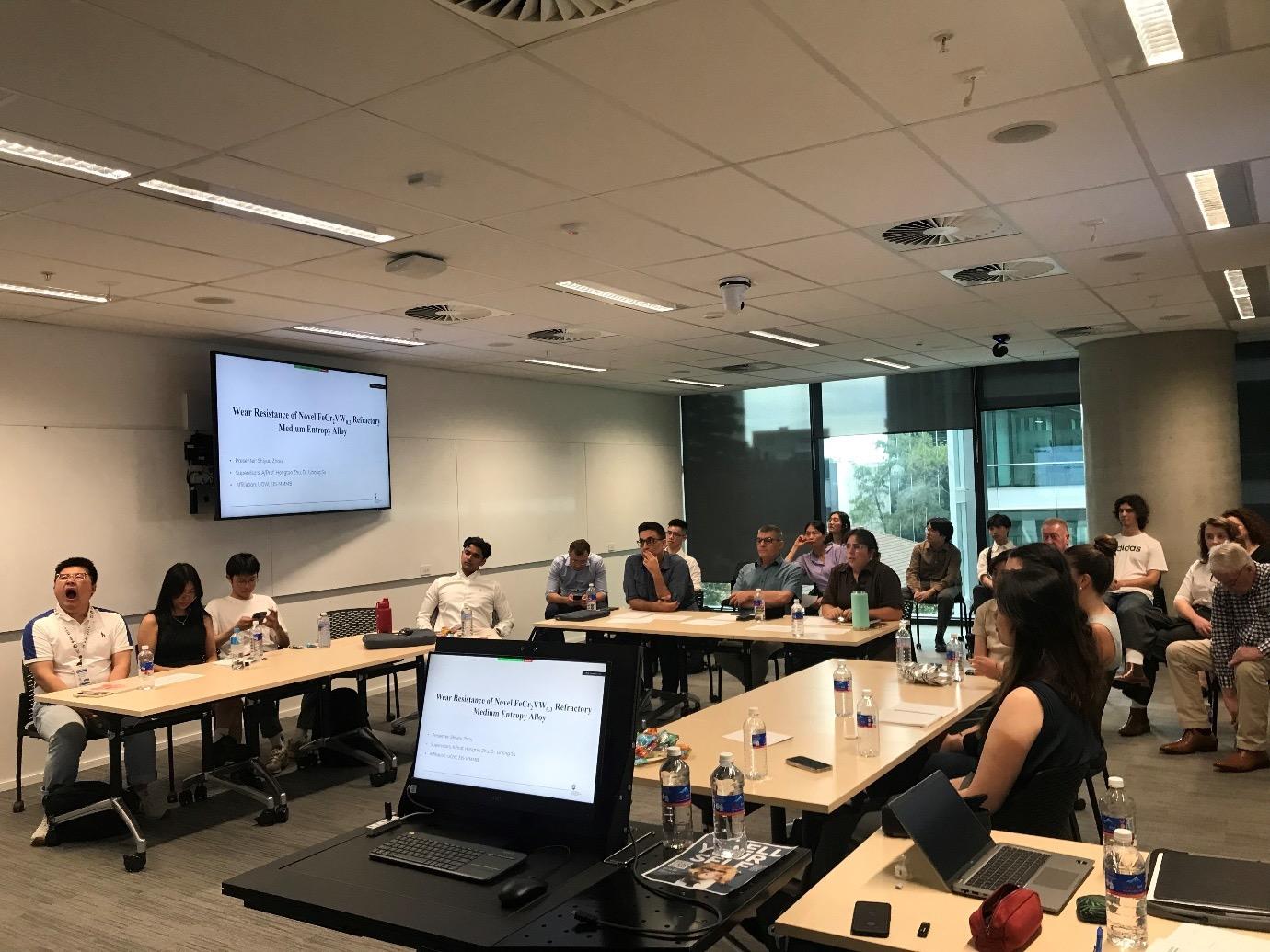
3 minute read
NSW Branch Report
Source: Alan Todhunter - NSW State President
ARC SEAM Roadshow
In late October, the ARC SEAM Roadshow was held in Parramatta and Wollongong. The event highlighted the facilities, achievements and successes of the Australian Research Council Industrial Transformation Training Centre on Surface Engineering for Advanced Materials.
The presentation provided information on the background for the establishment of SEAM, the professional model by which SEAM interacts with industry, universities and national labs, as well as case histories. Many thanks to Christopher Berndt and Robert McMahon for facilitating the event.
Recent Student Events
The New South Wales Branch also hosted two student-centred activities in recent months.
Following the success of the CMatP presentations, the NSW Branch held an online session for final year students working on a PhD in materials science. The diversity in research topics reflected the scope of their supervisor's interests and offered insight into the research areas by students. The students who presented were from UNSW, the University of Wollongong, University of Sydney, and Western Sydney University.
Plans are set to make this an annual event. The presentations offer multiple benefits: updating industry on the range of exciting projects being undertaken, as well as the opportunity to give students feedback.
The second recent student event was a hybrid face-to-face and online presentation by students in their honours year or first year of postgraduate study. Nine students presented their research and six other students presented posters. Students were from the University of Newcastle, UNSW, the University of Wollongong, the University of Sydney, and Western Sydney University.
The students all received one-year membership to Materials Australia and have been encouraged to continue a career in materials. Many thanks are extended to the judges and the sponsors.
Looking Ahead
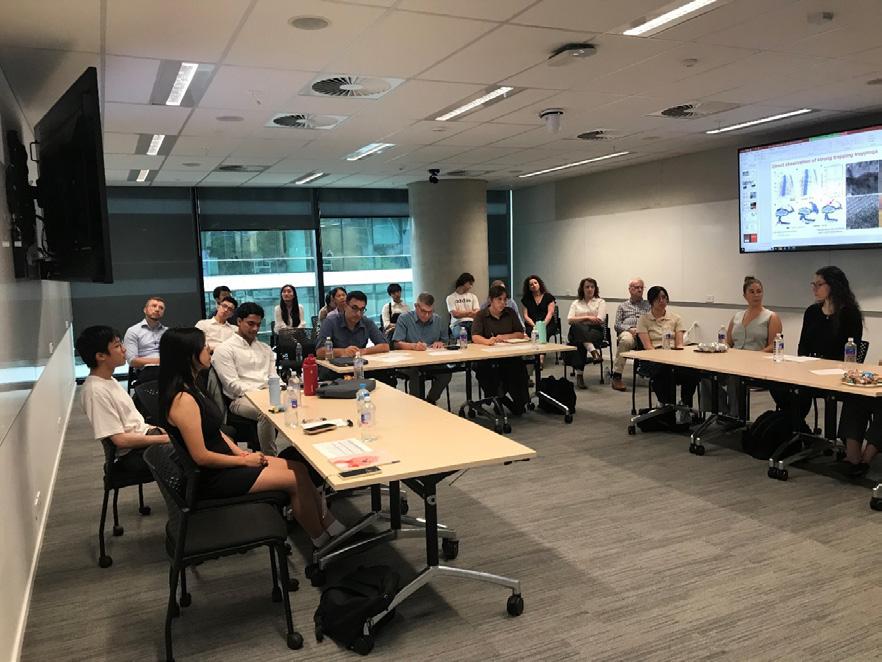
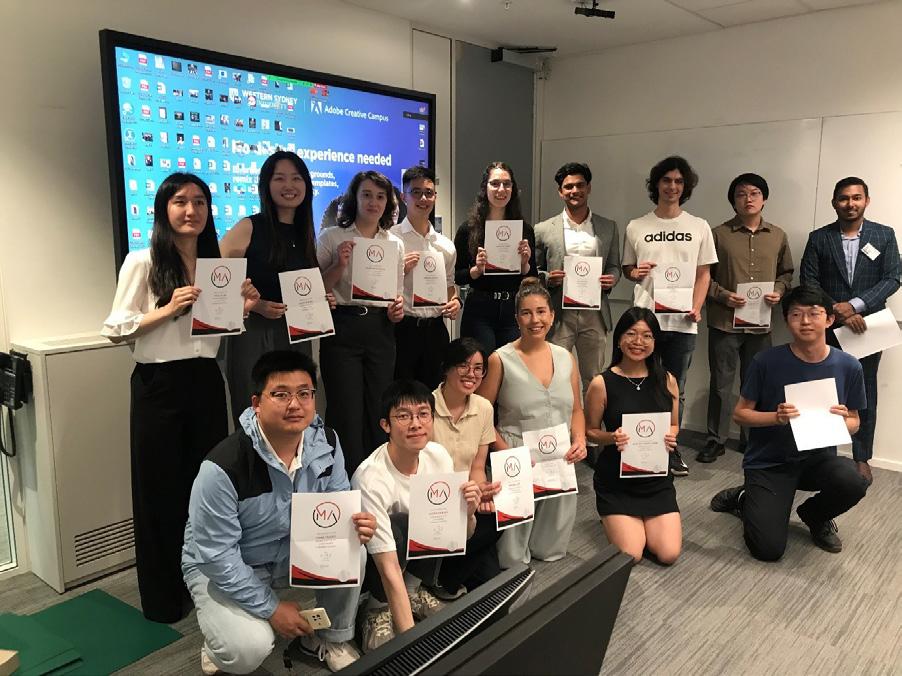
The New South Wales Branch is pleased to announce that it has three new committee members, comprising Andrew Gregory, Ali Hadigheh, and Robert Small. They will join our existing committee in planning a calendar of local activities for 2025.
The New South Wales Branch looks forward to a successful year ahead.
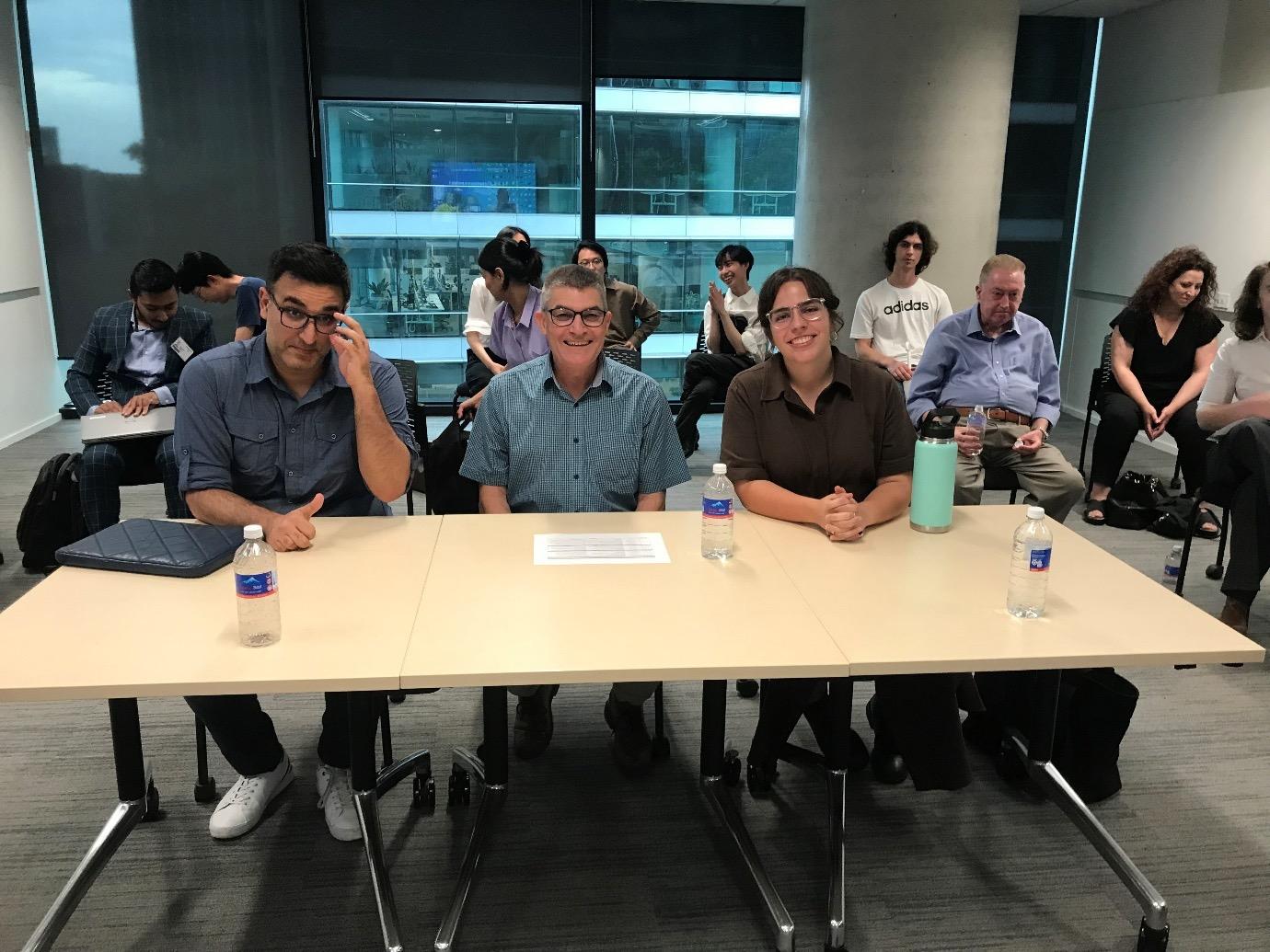



Founded in 2019 as a partnership between three universities, SEAM’s mission is to help solve critical surface engineering problems faced by industry, while training up talented industry-ready graduates for our future
Founded in 2019 as a partnership between three universities, SEAM’s mission is to help solve critical surface engineering problems faced by industry, while training up talented industry-ready graduates for our future.

Superhydrophobic Coatings Reducing Boiler Slag Deposition
Working with SCG Chemicals (SCGC) and taking advantage of Swinburne University’s suspension plasma spray (SPS) facility, (the leading facility available in the southern hemisphere) SEAM PhD Kritkasem (Kris) Khantisopon used a SPS process to mimic natural structures and create a superhydrophobic coating that greatly reduces slag deposition in a simulated biomass fired boiler. The undulating surface was created by the SPS process. Traditional slurry spray processes will have difficulties making this kind of structure During the fabrication process, the SPS coating deposition is instant, whereas slurry spray coatings can take days to complete Combined with the over 12% reduction in slag deposition weight demonstrated in this study, there is potential for significant savings in costs associated with cleaning of boilers and increased lifespan Now a PhD, Dr Kris Khantisopon is working at Swinburne as a Materials Characterisation Technician
Cracking the Code on Quality Coatings
A combined project with industry partner LaserBond conducted by SEAM PhD student Md Jonaet Ansari has allowed researchers to develop an optimized analytical approach utilizing an acoustic emission (AE) defect detection technique to identify process-induced cracks during the laser metal deposition (LMD, also known as Laser Cladding) process The developed signal processing algorithm analyses acoustic signals generated throughout the deposition process, enabling the immediate identification of cracking events as they occur To validate this method, components were longitudinally sectioned, allowing direct comparison between physical crack locations and their acoustic signals By pinpointing the specific locations and timings of cracks, manufacturers gained the capability to understand precisely when and where cracks occur in the manufactured components. The real-time detection of cracks enables manufacturers to adjust their processes as necessary, thereby reducing the likelihood of producing defective parts and potentially saving time and resources in post-production quality inspections.
Machine Learning for Manufacturing
Cold spray is an advanced additive manufacturing technology used for producing near-net shape parts, as well as for surface coating and repair. It is a layer-by-layer deposition process that can be applied to a wide range of metals without melting them during the process Titomic’s TKF AM System harnesses cold spray technology (together with software and robotics) to produce high-performance metals at unprecedented speed and scale – and with improved safety and sustainability . SEAM PhD student Martin Eberle teamed with SEAM industry partner Titomic to elevate their TKF cold-spray process to the next level - integrating advanced sensors to provide critical process insights in real-time, paired with a data analysis pipeline powered by machine learning, and all validated by testing and analytical capabilities at SEAM This collaboration has expedited development and fortified quality, unlocking high-value applications and access to global markets. After submitting his PhD at Swinburne University of Technology, Martin is now an Engineer at Titomic.
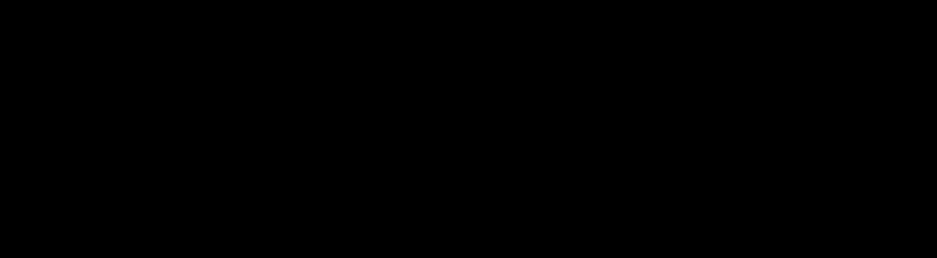
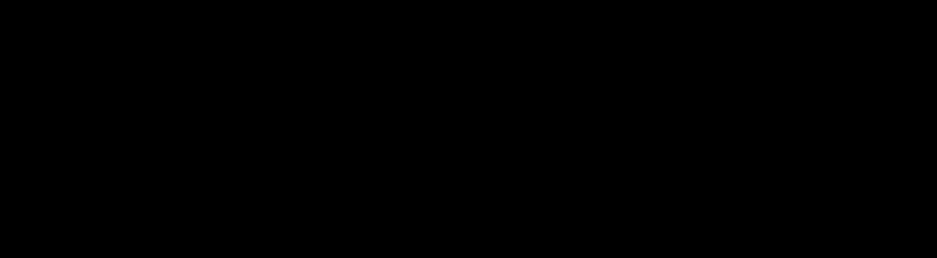
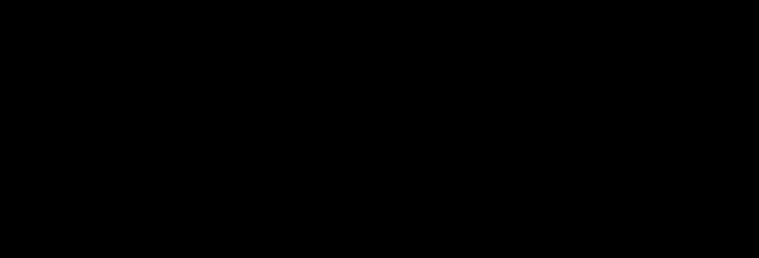
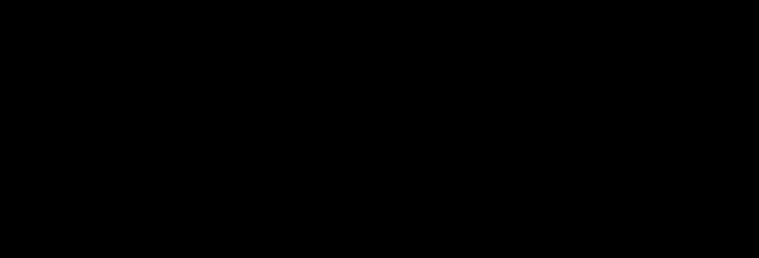

