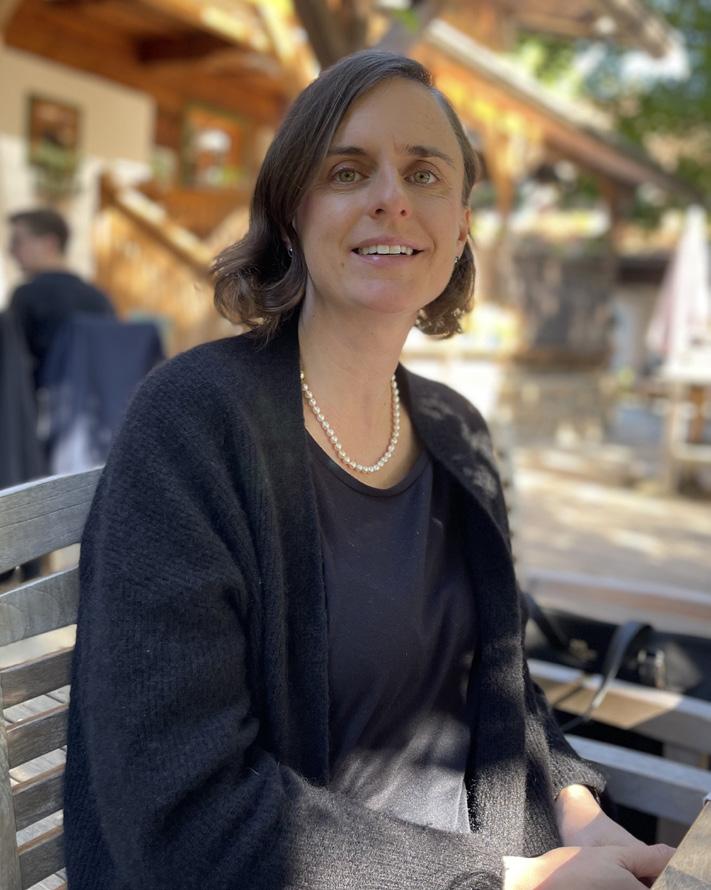
5 minute read
Sophie Primig, Alcoa Distinguished Professor at UNSW Sydney
Sophie Primig is currently an Alcoa Distinguished Professor at the University of New South Wales (UNSW) Sydney. Her research contributions are in processing-structureproperty relationships of structural alloys. Sophie combines state-of-the-art experimental techniques such as multiscale correlative microscopy with mechanical testing and contemporary modelling approaches. Her research philosophy is to achieve a balance between fundamental discovery and industrial application.
She was awarded her PhD from Montanuniversität Leoben (Austria) in 2012. After a short period of postdoctoral research and a role as leader of a group with strong industry linkages at the same university, she moved to UNSW in 2015. She holds two UNSW Graduate Certificates in Education and Management. She is a passionate student-focused teacher, editor of the Journal of Materials Science, current TMS Phase Transformation Committee Chair and active Materials Australia member.
Sophie recently received a $1,205,600 Australian Research Council (ARC) Future Fellowships to investigate built-in 3D microstructural gradients into high-performance alloys. Commercially, this could lead to opportunities for domestic production of engineering parts, reducing reliance on international trade. Environmentally and socially, the project promises lower emissions through improved mechanical design and workforce training opportunities.
Describe your current job and how to do juggle your time?
I describe myself as a metallurgist and engineer who is passionate about building teams that can tackle current global challenges using materials science & engineering skills. I am currently an Alcoa Distinguished Professor in the School of Materials Science & Engineering at UNSW Sydney.
The mission of my research group (www.engineeringmicrosturctures.com) is the design and discovery of next generation structural metallic materials. We aim to achieve better properties than currently available by engineering of the microstructure of alloys, via conventional thermo-mechanical such as forging or advanced processing such additive manufacturing (AM) routes. Our research philosophy is to achieve a balance between fundamental discovery and industrial application. We are most well-known for our research on Ni-based superalloys, stainless steels, and Ti-alloys for aerospace, energy, tooling, and defence.
I am a passionate university lecturer although my current teaching load is low. I have recently been awarded a research-focused Future Fellowship by the Australian Research Council that I will start in early 2025. My Fellowship is on a current hot-topic in AM, aiming to engineer gradient microstructures for unlocking superior and site-specific materials properties. This was partly inspired by the unusual site-specific microstructure evolution my group encountered in a stainless steel that was 3D printed using a concentric laser powder bed fusion scan (see Figure 1).
I am equally passionate about leadership and mentorship. Some of my current roles include editor of Journal of Materials Science and chair of the TMS Phase Transformations committee. I also lead the Transport and Infrastructure theme group in my School. I used to be active in Materials Australia (more on that later), although I am currently taking a break from that. One of my strategies to juggle my time is to avoid wearing too many different hats at the same time.
I would describe my job as diverse and occasionally challenging. However, leading with a diverse research group, traveling the world to collaborate with international leaders in my field, and tackling materials engineering challenges together with my industrial partners are some of the main reasons why I love my job.
How did you end up in your current job?
My first degree is a Master’s in Materials Science & Engineering with strong physical metallurgy focus from back in Austria where I grew up. The portrait photo (Figure 2) is from one of my many recent visits back home. I think enrolled into this program mainly because I was unable to make a choice between Physics, Chemistry and Maths. I went to Montanuniversität Leoben, a small but prestigious mining and materials focused university. I was impressed by their low student-to-academic-ratio and high employability. I ended up staying in Leoben for fourteen years, as student assistant, then as MEng and PhD student, PostDoc, and finally in an academic role working closely with various local companies. c)
In 2015, I felt ready for new challenges in a much bigger university and moved to UNSW Sydney, initially as a Lecturer.
What has been the most productive period in your research career and why?
Although I was grateful for the new opportunity at UNSW, the following years were probably the hardest of my career. It seemed like that whatever I tried would fail, somehow. This is not unusual for a junior academic; especially given I had to start from scratch in a new country and university without any existing networks.
I tried hard to start new collaborations with industry and experienced my various first and unsuccessful attempts at getting funding for fundamental research. It seemed to take ages until my small new group started to produce anything publishable.
The hard groundwork paid off. Starting with the award of a DECRA Fellowship by the Australian Research Council in 2018, I was soon awarded several grants and fellowships, including a major five-year program on AM via the socalled AUSMURI program together with the University of Sydney and six great US-based universities. My next and more enjoyable challenge was to build a bigger and more diverse research group capable of achieving great outcomes in all those projects. I believe I have accomplished this.
What do you think are your most significant research accomplishments?
In my applied research, I have helped several national and international manufacturers of aerospace materials to tackle processability challenges such as cracking during forging, leading to poor yield and/or poor mechanical properties. Advancements in the understanding of processing-structure- property relationships, often underpinned by through-process modelling, has enabled my industry partners to make superior products at lower cost, and their customers to design and build more fuelefficient aeroengines.
In my fundamental research, my group and I have explored the poorly understood physical metallurgy of AM processes that are highly non-equilibrium in nature. Our findings have usually been enabled by advanced multiscale characterisation and modelling. We started this research stream at the right time and place, roughly six years ago in Sydney where amazing characterisation facilities are available via Microscopy Australia. My leadership in AM has recently been recognised by the invitation to contribute a major chapter on the physical metallurgy of AM to the next edition of Hono & Laughlin ‘Physical Metallurgy’, a leading textbook in my discipline.
What are the big issues in your research area?
The perhaps biggest future challenge in my field is how we will continue to make progress in a world with increasingly limited resources but ever-growing demands for more and better engineering materials. If I had to pick my undergrad specialisation today, I believe I would go for process rather than physical metallurgy. A couple of decades ago, this meant learning about crushing and refining ores and understanding dirty blast furnaces. However, today it is time for the brightest minds of the next generation to reinvent these often >100 years old dirty and energyintensive metallurgical processes to make them net-zero.
How would you go about motivating an early career researcher who is going through a low point?
I was fortunate to have many great mentors at UNSW and beyond. One of the perhaps most useful tips in my early days in Australia was to get involved in a local professional organisation. I attended the annual NSW Materials Australia CMatP conference at UNSW in 2015, where I was recruited to join the NSW council. I later became a CMatP myself and was the NSW branch president from 2020-2022. An article about my research on Ni-based superalloys with a European partner company in the Materials Australia magazine in 2017 ended up being the basis for my first ARC Linkage grant with a local manufacturer.
Hence, my message to a struggling ECR would be around trying to pursue many different avenues that could potentially lead to success. If you are cut-out for a challenging but ultimately rewarding career in academia, good things will eventually start to happen as long as you keep trying hard.
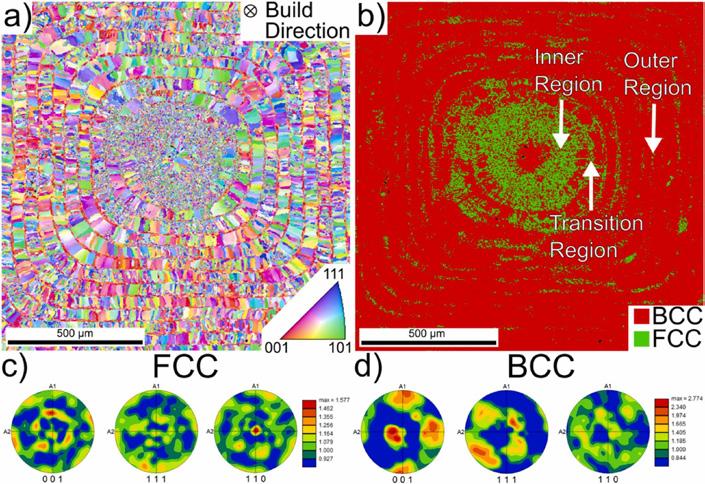
Figure 1: Laser-powder bed fusion of 17-4 PH stainless steel leading to site-specific formation of (a) coarse versus fine grains and (b) austenite (FCC) versus ferrite (BCC) due to the thermal signature of (c) a concentric scan pattern. For more information and detailed discussion of the underlying phase transformation pathways, please refer to the original open access paper by M. Haines et al. in Additive Manufacturing (https://doi. org/10.1016/j.addma.2023.103686).