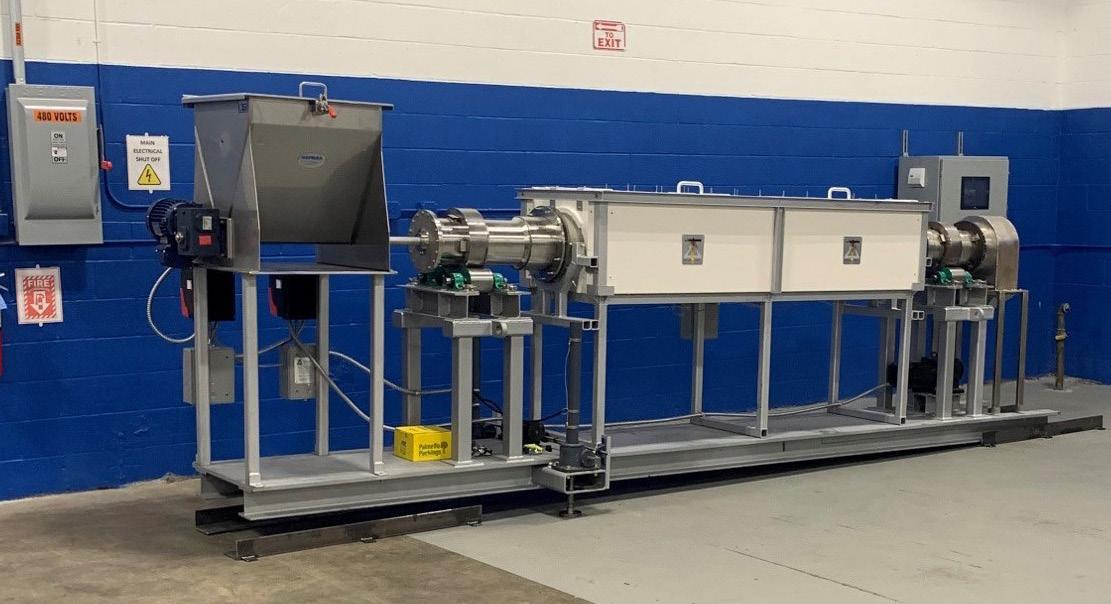
1 minute read
Deltech Furnaces Unveils Custom Rotary Kiln Systems for Hazardous Environments
By Mary F. Stevenson, Ph.D. – Deltech Furnaces
Deltech Furnaces has successfully completed the design, manufacturing, and installation of two advanced rotary kiln systems tailored for hazardous locations.
These bespoke systems incorporate cutting-edge features such as HMI (Human-Machine Interface) controls for precise multi-zone management and data acquisition, along with volumetric feeders mounted on precision linear drives for exact material distribution. The systems have undergone rigorous NRTL testing and meet stringent NFPA 86, UL 1203, and Class 1, Division 2 (Groups D and G) standards.
Rotary tube furnaces are a cornerstone in applications like calcining, continuous material processing, and oxidation, especially for materials such as alumina and iron ore pellets. Designed to operate under extreme temperatures, these furnaces provide unparalleled process control, ensuring superior product quality.
Deltech’s rotary tube furnaces stand out for their bespoke design, allowing for custom configurations and features tailored to specific operational needs, including compliance with hazardous environment standards. The company also adheres to ASME NQA-1:2008 standards, ensuring safety and reliability in demanding industries.
Key features of Deltech rotary tube furnaces include:
• Resistance heating with silicon carbide or molybdenum disilicide elements for temperatures up to 1,700°C.
• Single or multi-zone configurations.
• Customizable rotation speeds and gradients.
• Fully integrated, programmable control panels.
• Capability for processing in air, oxygen, or inert atmospheres.
• Optional gas mixing, detection, and alarm systems.
• Integrated exhaust scrubbers and gas control systems.
This latest project exemplifies Deltech’s commitment to delivering innovative, high-performance solutions for specialized industrial processes. Learn more about Deltech’s custom rotary kilns and furnaces: https:// www.deltechfurnaces.com/