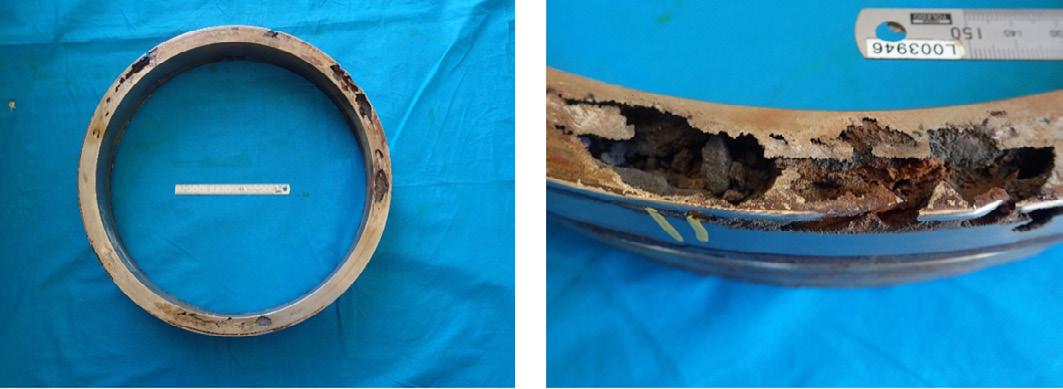
6 minute read
Super Duplex Can Corrode
Source: LMATS (Laboratories for Materials Advanced Testing Services)
This short investigation demonstrates how poor heattreatment during initial manufacture can still have detrimental effects years later.
Introduction
Leaking was found to be occurring from the ends of super duplex (UNS S32750) pipes. It was reported that the pipes had been in operation for 10 years and the pipework was connected together using mechanical pressure joints. The affected material was similar to material that had been in operation for two years longer under the same conditions, which showed none of these failures.
Two rings, which had been cut from the ends of two 425mm diameter pipes, were supplied for examination. The reported operating conditions for both rings were: • Pressure of60Ba • Temperature of 13-180oC • Approximate pH of 8.1 Ring 1 carried brine with a salinity of 51,200ppm. Ring 2 carried seawater with a salinity of 32,640 to 34,560ppm.
Ring 1 – Brine
Severe corrosion was found on the end face of the supplied ring in three positions around the circumference. The rest of the end face was relatively unaffected, but red rust staining was prevalent. The intensity of the metal loss showed that the metal of the ring had practically disintegrated.
The as received Ring 1 showing extensive corrosion on the end face.
The as received Ring 2 showing corrosion on the end face. Close up of Ring 1 showing extensive corrosion on the end face. The yellow paint marks the position of the microsection.
Close up of Ring 2 showing corrosion on the end face. Macrosections though the Rings showing the extensive internal corrosion.
Ring 2 - Seawater
Severe corrosion was also found on the end face of the Ring 2 at various positions around the circumference. The intensity of the metal loss was evident, with very deep pitting and severe loss of material.
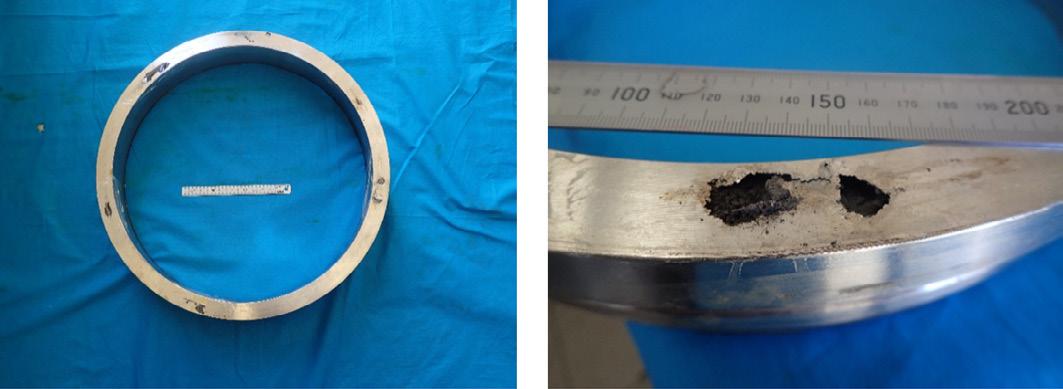
Macrosections were cut through some of the areas of corrosion, which revealed that extensive corrosion had propagated the whole depth of the sections.
Hardness, Chemical and % Ferrite
The chemical analysis for both samples met the requirements of UNS S32750, a superduplex stainless steel except for the slightly lower Nitrogen values. Both meet the requirements of NORSOK M-630 (MDS D51/D52(5)) for a PREN > 40.
PREN = CR% + (3.3 x Mo%) + (16 x N%)
2251/01 = 24.4 + (3.3 x 4.1) + (16 x 0.15) = 40.33
2251/02 = 24.7 + (3.3 x 4.2) + (16 x 0.21) = 41.93
The percentage ferrite was measured using a Ficher Ferritscope. The percentage ferrite met the requirements of DNV-OS-F101 with ferrite content of 35 – 55%.
The hardness values of 255Hv (Ring 1) and 258Hv (Ring 2) met the requirements for UNS 32750 of < 326Hv in the solution annealed condition.
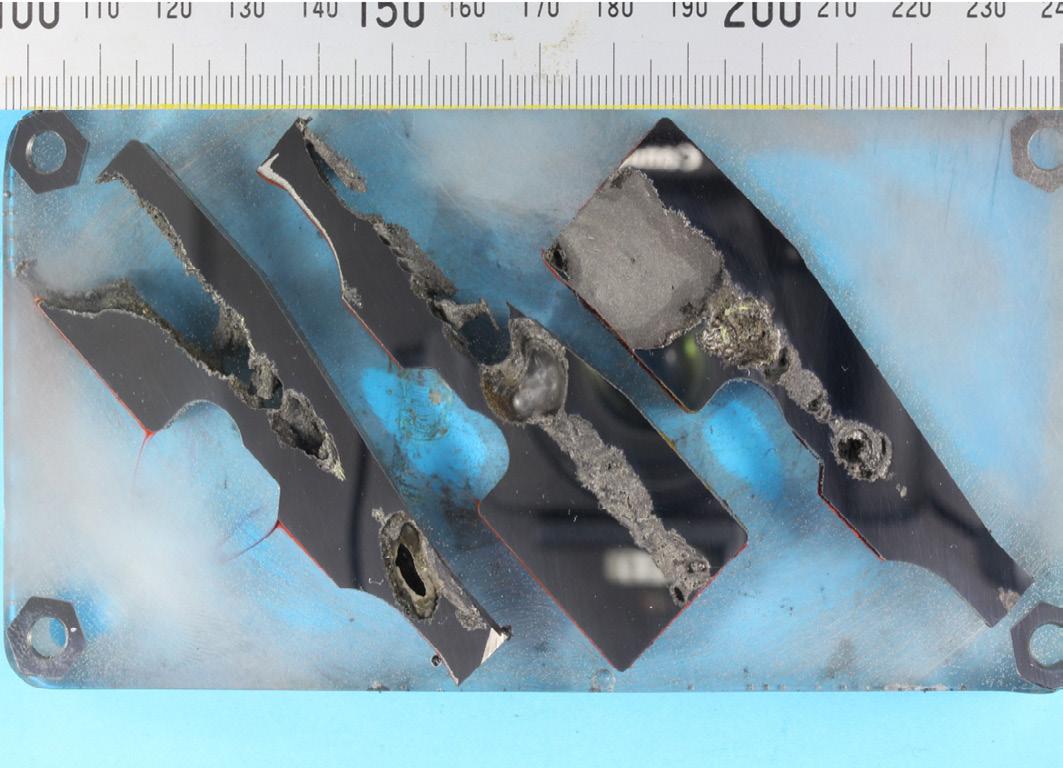
ASTM G48 Corrosion Test
The corrosion test, ASTM G48 Method A, was conducted at 500oC for 24 hours. An acceptance criteria of a maximum weight loss of 4g/m2 is specified in DNV-OS -F101 for superduplex stainless steels. Pitting was observed in both samples after testing with weight losses of 867g/m2 for Ring 1, and 670g/m2 for Ring 2.
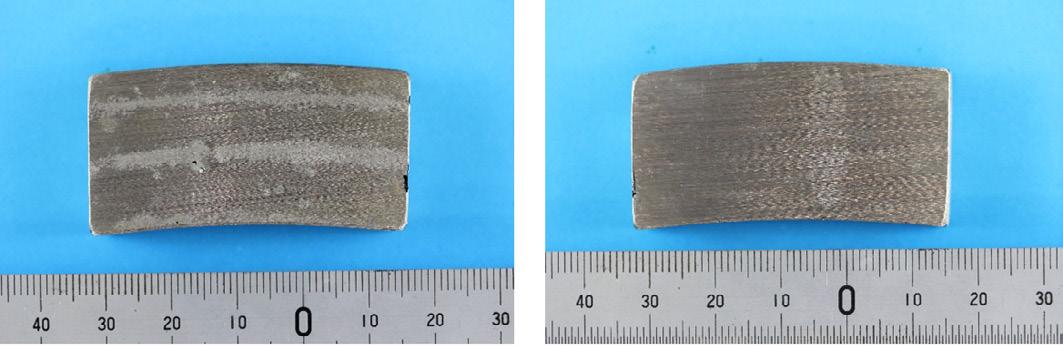
Sample from Ring 1 after testing showing pitting.
Microstructural Examination
Sample from Ring 2 after testing showing pitting.
Examination of the metallographic structures followed the procedure given in ASTM A923 and was etched using electrolytic 40% sodium hydroxide. Structures from both Ring 1 and Ring 2 showed evidence of intermetallic precipitation at the grain-boundaries.
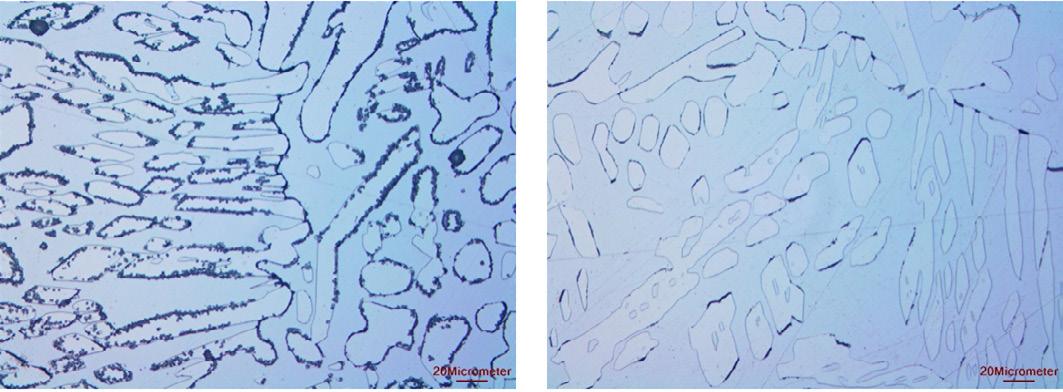
High magnification of Ring 1 showing the intermetallic precipitation at the grain boundaries. High magnification Ring 2 showing the intermetallic precipitation at the grain boundaries.
Discussion
The chemical analysis for both samples met the requirements of UNS S32750, a superduplex stainless steel except for the slightly lower nitrogen values but both samples had a PREN > 40. The ferrite / austenite phase balance was measured to be 48.4% which met the requirements of DNV-OS-F101 and Norsok M-603 D51.
PREN >40 is typically specified for seawater service[1][2][3]. Both stub rings had a PREN greater than 40. Although, Ring 2 was slightly higher that Ring 1. This lower PREN of Ring 1, and hence lower corrosion resistance, could also be seen in the G48 test where it suffered more corrosion than Ring 2. However, both samples failed the G48 test with pitting and weight losses far greater than the industry standard of 4g/ m2(4,5). The critical pitting temperature of UNS 32750 should be >70 C for a fully solution annealed structure (6). The metallographic structure of the stub rings was found to consist of austenite and ferrite. However, precipitation of intermetallic phases at the grain boundaries was observed. The precipitation in Ring 1 was higher than in Ring 2, which could also account for the greater attack. Also, the higher salinity of the brine that Ring 1 was exposed to would also increase the corrosivity. Sigma phase precipitation and the precipitation of other intermetallic phases increases the susceptibility to corrosion(7). Sigma phase is a chromium-molybdenum rich phase that can render stainless steels susceptible to intergranular corrosion, pitting and crevice corrosion. Third phases and precipitates can lower the alloy content locally in adjacent areas, consequently the PREN is effectively reduced in these areas making them very susceptible to pitting corrosion. Sigma phase forms when an alloy is cooled slowly through the range from around 1,000oC to 5,500oC. The formation of sigma phase can be avoided during initial production by solution annealing at a temperature above the formation range, followed by a rapid quench with minimal delay. Careful control of heat treatment and quenching conditions should be an important part of purchasing specifications, and also forms the basis for industry approvals such as Norsok M-650. Achieving a fast enough cooling rate can become more challenging at larger diameters, and for thicker section castings. The corrosion seen in the rings was concentrated on the end faces. This is where a crevice would have been formed due to the joining of the rings by the mechanical connectors. Crevice corrosion can be considered a severe form of pitting. Any crevice, whether the result of a metal-to-metal, a gasket, fouling or deposits, tends to restrict oxygen access, concentrate the chloride ion and reduce the pH resulting in attack. It is considered at under normal circumstances, with the material not having reduced corrosion resistance due the precipitation of intermetallic phases, that the material would not have suffered from crevice corrosion.
Conclusion
The corrosion is considered to have been caused due to the formation of crevices, which then propagated by an autocatalytic mechanism into the material which had reduced corrosion resistance due to the precipitation of intermetallic phases. The precipitation of the intermetallic phases would have been due to ineffective heat treatment during the manufacture of the pipes 10 years previously.
References
1. Gerhard Schiroky, Anibal Dam, Akinyemi Okeremi, Charlie Speed (2013). "Pitting and crevice corrosion of offshore stainless-steel tubing". Offshore Magazine. 2. Kathy Riggs Larsen (2016). "Selecting Stainless Steels for
Seawater Pumps". Materials Performance. 3. Dirk Aberle and Dinesh C. Agarwal (2008). 08085 High
Performance Corrosion Resistant Stainless Steels and Nickel
Alloys for Oil & Gas Applications. NACE. Product Number: 5130008085-SG, 4. DNV-OS-F101 – Submarine Pipeline Systems 5. NORSOK M-630 D51 6. Practical guidelines for the fabrication of Duplex Stainless Steel, 2nd ed, IMOA 2009 7. ASM Metals handbook Vol 13B, 2005.