
6 minute read
WOMEN IN THE INDUSTRY: Professor Nikki Stanford
Source: Sally Wood
Professor Nikki Stanford is a Research Leader in University of South Australia’s Future Industries Institute (FII). The FII was established with a new research culture in mind - one deeply engaged with industry, with the end goal of building economic growth through relevant innovation and industry partnership.
The Institute reflects the University’s strategic ambition to be Australia’s University of Enterprise which engages fully with the professions and industry globally, whose research is informed, leading edge and relevant. FII continues to forge national and international research partnerships, in new industries and technologies, that address real world issues. Their goal is to support a creative and engaged culture, and to help develop a sustainable ecosystem in which innovative, complex, growth-focused industries thrive. Professor Stanford’s niche in the materials research field has been focused on bridging the gap between engineering and science, by applying a broad range of advanced characterisation techniques to ‘real world’ problems, such as fatigue, light-weighting and casting. Before joining FII, Professor Stanford held research positions with Imperial College London, the University of Manchester, Deakin University and Monash University. She has studied a broad range of materials research topics, including casting defects in nickel single crystal turbine blades, shape memory steels, phase transformation phenomena in titanium, and magnesium texture development. Professor Stanford is particularly well known for her light metals research portfolio, and in 2015 was awarded the Helmholtz-Zentrum Geesthacht’s Magnesium Award for international magnesium researcher of the year.
Q&A with Professor Stanford
Professor Stanfordtook time out of her busy schedule to answer a few questions for Materials Australia magazine.
Why (and how) did you decide to embark on a career in Materials Science?
Materials science is the perfect mix of science and engineering. I get to use expensive microscopes and do some really exciting science, and it all ends up being useful to someone. Although I started out doing mostly hard materials such as steels, I’m increasingly getting involved in collaborative research looking into polymers, surface science, energy storage, medical devices and computational science.
Can you describe the projects you’re currently working on?
Outside of my research, I also teach in the undergraduate course on materials science, which is a compulsory for all engineers. I’m pretty passionate about it. We get one opportunity to instil the most important principles of materials into our future engineers. This is to ensure that they understand the true nature of the materials that they are using. I’m also the chair of the Microscopy Australia Education Committee. Our main focus at the moment is the expansion of our online training tool called MyScope https://myscope.training. It’s the largest online microscopy training tool, and we get about 100,000 unique visitors every year, from all over the world. It’s a great project to be part of—I really enjoy it.
What do you enjoy most about your research?
I enjoy the small amount of lab time I get. I’ve enjoyed doing 3D printing and working with my digital technologies colleagues on Industry 4.0 projects, but ultimately, what I enjoy most is being on an expensive instrument taking beautiful micrographs. I wish I could be in the lab all the time.
Coating and Repair of Additive Manufactured Components
Professor Stanford is part of a research project that is investigating the development of laser clad and 3D printed structures, as well as other potential application technologies, for use in the mining and oil and gas industries. The structures will be designed to resist abrasion, erosion, impact and corrosion (both chemical and microbially induced). The projects will include design, investigation of process parameters,
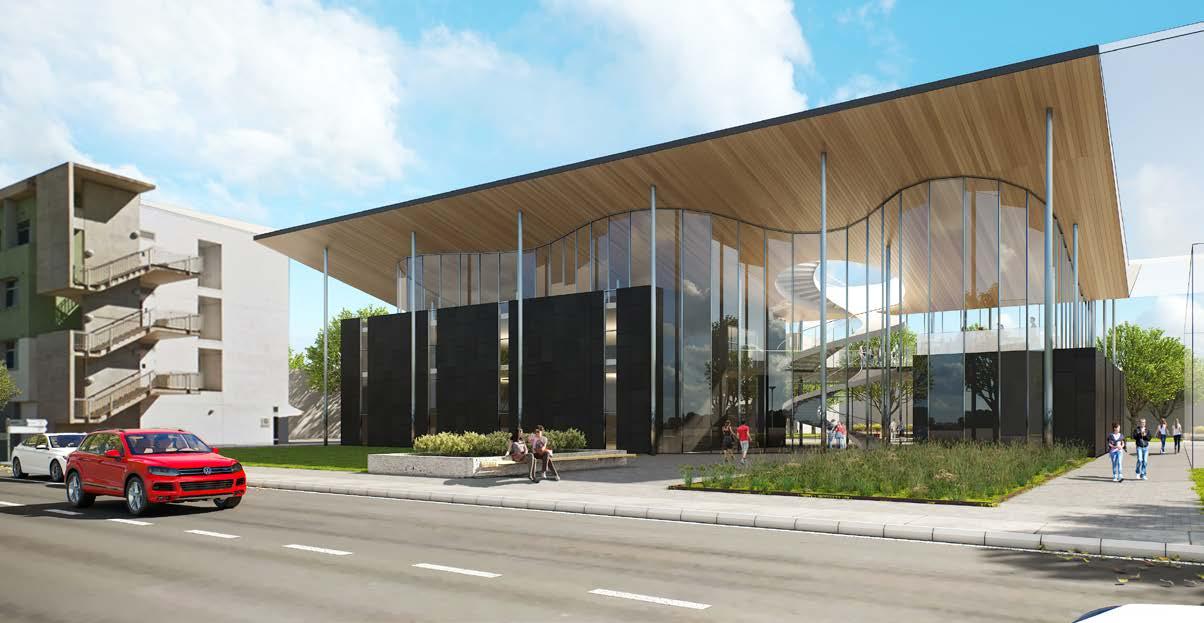
Professor Nikki Stanford addresses a group of researchers at Industry 4.0 Testlab. Image courtesy of the University of South Australia.
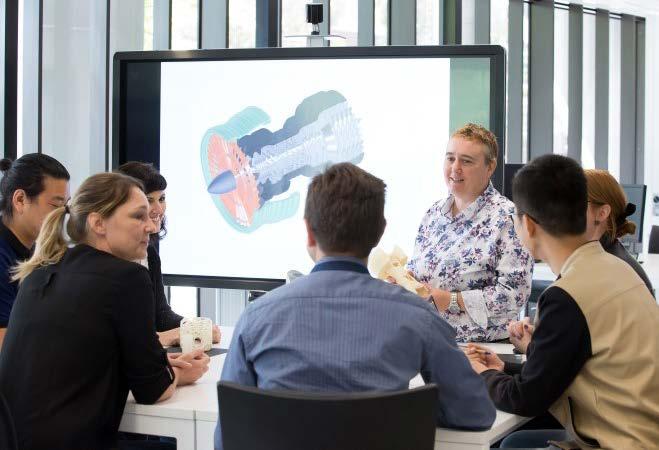
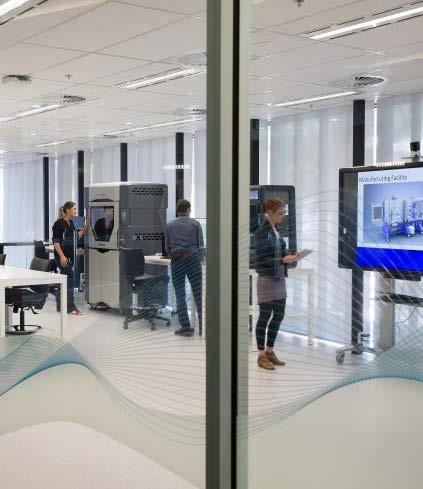
Inside the University of South Australia’s Industry 4.0 Testlab. Image courtesy of the University of South Australia.
advanced feedback mechanisms and control, measurement of properties, as well as the study of interface behaviour by advanced electron microscopy. Along with the University of South Australia’s industry partners, LaserBond and Santos, the project also includes hands-on training experience for several PhD students.
Surface Engineering for Advanced Materials
Professor Stanford is one of the chief investigators for the Surface Engineering for Advanced Materials (SEAM) ARC Training Centre. SEAM targets the training of early career researchers in an industrial context. The proposed area of surface engineering for advanced materials is a core need in all manufacturing sectors that control the efficiency, productivity and sustainability of Australian industry. This project aspires to be the model centre that integrates industry-university cooperation for applied training within an industrial setting. This Centre desires to be the nexus for an international collaborative network. The Centre pursues ambitious outcomes that are reflected in terms of industry-fit researchers and commercial benefits for industry. The spectrum of applications being addressed ranges from thin films to thick coatings and additive layered materials. This is the first Training Centre of its kind, with a specific focus on surface engineering across (i) very thin films less than 10 μm, (ii) coatings less than 250 μm, and (iii) thick overlays up to tens of millimetres thick. The third category encompasses additive manufacturing (AM) since this is, fundamentally, a layerby-layer material deposition process. Application fields include: biomaterials, corrosion, graphene layering, machining, cutting, grinding, thick coatings for heavy industries such as mining, high temperature coatings, laser metal deposition for materials repair, additive manufacturing for aerospace, and Industry 4.0 manufacturing processes. For further information, visit: https://arcseam.com.au
Industry 4.0 Testlab
Professor Stanford is the Director of the University of South Australia’s Industry 4.0 Testlab. The Testlab has established to demonstrate Industry 4.0 methodologies and practices, and includes practical laboratory-based capabilities and a pilot scale manufacturing demonstration. The Testlab has a particular focus on the defence sector, and is also highly relevant to the space, mining, electronics, food and agriculture, and automotive industries. A key objective of the Testlab is engagement with small and medium enterprises (SMEs), introducing them to a broad range of Industry 4.0 strategies, methodologies and approaches. This includes demonstrating how these methods can be adopted by industry to enhance productivity, competitiveness and profitability. The Testlab provides local SMEs, and high-tech start-ups, with otherwise unattainable access to these smart factory technologies. For further information, visit: https:// www.unisa.edu.au/research/testlab/
Other Projects
Cluster Hardening of Metastable Steel Alloys Produced by Thin Strip Casting
The goal of this project is to generate sufficient knowledge to apply strip casting to a wider range of steel grades. Direct strip casting is an emerging green technology that reduces the energy required to process liquid steel into thin sheet product by up to 90%.
Development of Novel High Performance Aluminium Alloys Containing Scandium
Over 30 million tonnes of high performance aluminium alloys are produced per annum. This project aims to develop a new generation of alloys that contain scandium. SScandium is beneficial in the improvement of the bulk properties of aluminium, but its high cost has restricted research. Australia has the largest deposit of scandium in the world, and the Australian mining company, Clean TeQ, has developed a sustainable extraction technology to capitalise on this resource. A fundamental understanding of the beneficial effects of scandium will expedite rapid developments in these new alloys.