
6 minute read
INDUSTRY NEWS: Australian Innovation Leads to Sustainable Alternative for Architectural Hardwoods
Source: By Dr. Cameron Chai
Researchers have long sought to recreate natural materials like spider’s silk and human bone with varying degrees of success. Australian company 3RT has gone one better, successfully manufacturing appearance-grade hardwoods using a process that takes just 1 day, where mother nature would take 100’s of years. What’s even more significant is that the products are sustainable and ecologically friendly.
While there are other products on the market such as plywood and MDF (medium density fibreboard), 3RT have commercialised a product that addresses the other end of the market, i.e. high-end architectural and designer timber products. What really makes their product stand apart are its environmentally friendly credentials. 3RT’s Designer Hardwood is based on wood waste materials. Furthermore, Designer Hardwood uses water-based adhesives unlike the phenolics and other resins used in other reconstituted wood products. In doing so, it also satisfies the company’s core values, reduce, reuse and recycle. Designer Hardwood, is the product of several years of development work by 3RT. It looks, feels and behaves just like naturally sourced tropical hardwood, retaining the texture and warmth of the natural material. In fact, it has growth rings to give it grain, but owing to the fact it is man-made, it doesn’t have cracks or splits that may render certain sections unusable. It can be cut, machined and coated just like any other hardwood and is probably easier to work with than the natural analogue as it doesn’t have any nots and is more consistent. 3RT formed in 2014 with the idea of creating a product from wood residues from trees that are not suitable for producing sawn quality timber. These trees may be sourced from councils who need to remove trees, many of which may be sick or dangerous, or excess trees from timber plantations which effectively makes them waste products. However, this is not a typical story of how an industry insider identifies a problem, finds a solution and commercialises it. Rather, 3RT had an idea and almost no relevant industry expertise. As a result, they had to form strategic partnerships with outsiders to turn the concept into a reality.
Solving The Materials Problem
Peter Torreele, Managing Director of 3RT explained, “after initially contacting wood experts, 3RT looked outside the box and began working with materials experts at Flinders University to solve the physical problem of how to turn wood waste
materials into attractive timber.” With the specific requirement to develop an environmentally friendly product, 3RT and Flinders set about developing a process using a water-based, formaldehyde-free “Nano-glue” that biomimics the structure of a natural tree in hours. They then tackled the next issue of designing an industrial process to create the final product. They achieved this by combining pressure and temperature to densify and the materials and cure the resin, in a process that takes merely minutes. 3RT also worked with TAFE SA, whom they supplied with materials to work with so they could see how the material behaved and performed. They used this feedback to further refine the material to make it as close to the Mother Nature’s own product.
Solving The Production Problem
Based on the process developed by 3RT, they built a pilot unit that is now located at their Innovation Centre in Adelaide. They then partnered with Bosch Manufacturing Solutions to design and optimise the future manufacturing facility. The fact that this had never been done before was probably a blessing in disguise. It allowed people with expertise form other fields such as automotive to offer fresh ideas on how the production process could be designed. Andrew Bartlett, Manager Strategic Projects at Bosch Manufacturing Solutions said, “we had never seen a project like this before as we normally operate in the advanced manufacturing and medtech space. The more we looked at it, the more we realised the project had merit and although the application was very different, the basic concepts were still the same and could benefit from our expertise in sensors, robotics, automation, materials handling and data processing.” The team from Bosch designed a highly sophisticated, automated production workflow that relies heavily on constantly processing data acquired from throughout the process dealing with over 100 process parameters. The process is so tightly monitored that it can take into account the variances in natural trees that act as the raw material and adjust the process accordingly to achieve greater than 99% product conformity in the finished product. It even has the intelligence to learn and take into account the changes that take place for future occurrences. Furthermore, the high levels of automation effectively eliminate operator error from the 2 people required to run a shift, contributing to product consistency. The process is able to produce hardwood slabs 500x270x2600mm. Hardwood slabs this size have not been available for a very long time. The plant itself is scalable with a production capacity of 6-10,000m 3 /year. “One of the beauties of our system is that the output is independent of the input material. The system is robust enough and smart enough to make adjustments to the process such that it can even convert softwoods into hardwoods”, said Peter Torreele.
Sustainability
As mentioned, the raw materials are primarily waste products and the other materials are non-toxic and recyclable. The development of Designer Hardwood is also somewhat timely with hardwoods getting scarcer due to protection of native forests . This will no doubt continue to drive prices up, while at the same time governments look to implement legislation to outlaw illegal logging. Sawmills that process naturally occurring hardwoods are like CNC machining stations which take large billets and machine them down to smaller, tailored size slabs. This results in a lot of waste. In the case of a hardwood sawmill, they typically run at 30-32% efficiency. 3RT’s process is the opposite. By using a bottom up manufacturing approach there is essentially no waste from the production process, while the tropical hardwood trees are allowed to flourish and the associated wildlife habitats can remain intact.
Commercialising the Technology
We all accept that buying sustainable alternatives is better for the environment, however, we also know that doing the right things for the environment often comes with a premium price. This is not the case for Designer Hardwood because 3RT does not want to charge an “ecopremium”. While Designer Hardwood is commercially available in limited quantities through a handful of select lighthouse customers, Peter explains this is more to see how to determine the optimum routes to market. Their aim is to work with international partners to set up production facilities around the world and to licence the technology. 3RT finished the demonstration plant in Adelaide in 2019. There are plans to build a larger commercial plant in the near future. The existing plant was built so that 3RT can work with customers to refine the manufacturing process, tailoring it to their own, locally sourced wood fibres. Once the proof of concept has been completed, the client can be provided with a fully functional production plant delivered to their site and pre-optimised with their own specific set of production parameters streamlining the path to commercial viability. There are a number of companies that have already expressed interest in Designer Hardwood and 3RT’s innovative process of turning a waste product into a sustainable, high-value product. Hopefully this will be the next chapter in another Australian success story with production plants and an excellent case study strategic partnerships can be used to marry different skillsets across industries and scientific fields for a common outcome.
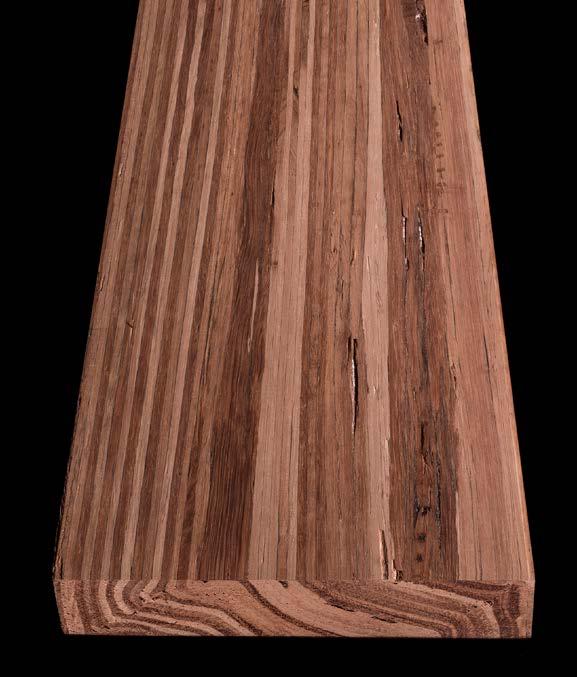
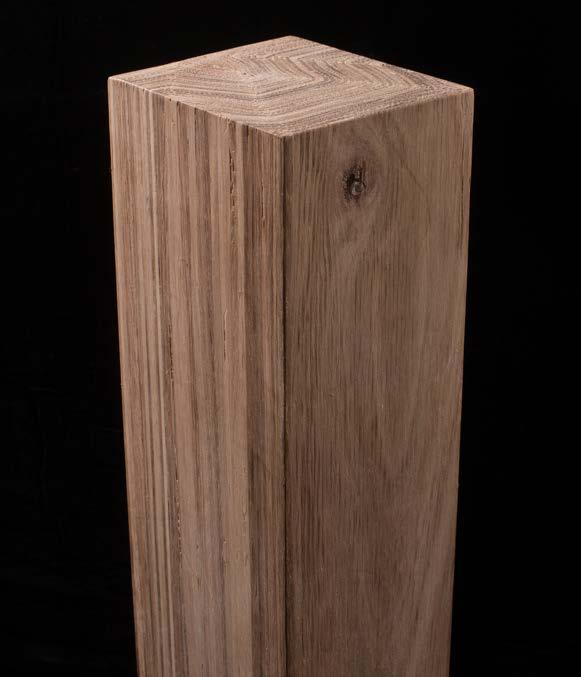