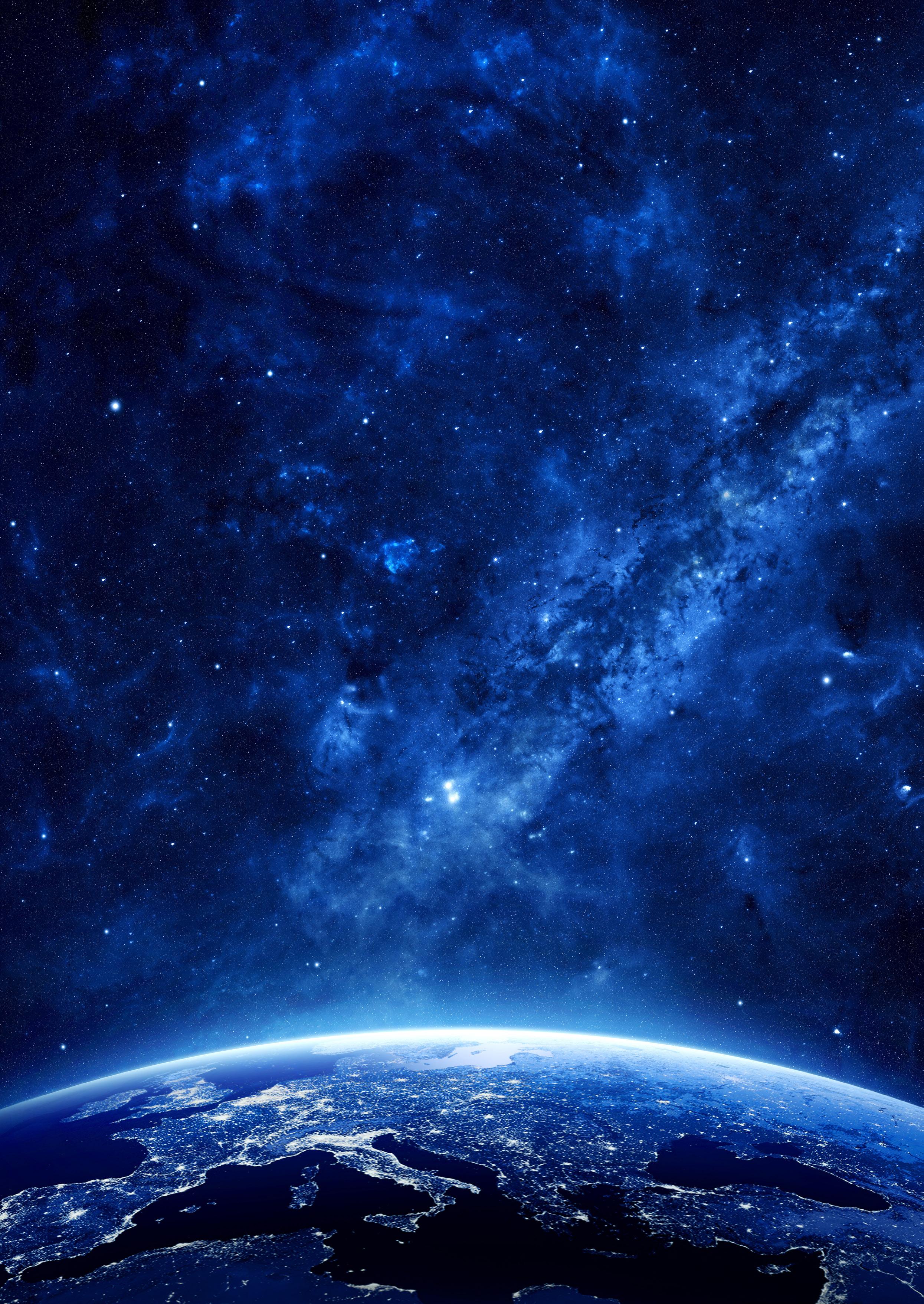
29 minute read
Feature - Australia’s Aeronautical and Space Materials Market Takes Full Flight
Australia’s Aeronautical and Space Materials Market Takes Full Flight
Since the Wright brothers took their inaugural 12-second flight in 1903, air travel has taken to new heights. From the fuel-efficient Boeing 787 Dreamliner to the double-decker Airbus A380, materials science plays a critical role in the development and maintenance of these widebody jets. Today’s modern aircraft are transforming the way in which people travel and connect with each other. Aerospace materials are also getting smarter, greener, and lighter, which is paving the way for longer non-stop commercial flights, and travel that is out of this world entirely. As the private sector accelerates the journey into space, manufacturers rely on materials that boast outstanding properties. They need to endure immense stress, ionising radiation, and withstand extreme environmental factors.
There are also some missions— like low earth and geostationary orbits—that offer a range of other obstacles around safety and longevity. To overcome these challenges, researchers connect with industry representatives to bring theory into practice. Aerospace materials are typically made up of metal alloys, and polymeric based materials. These materials are tested and analysed for their performance, temperature-control, and ability to survive hostile environments.
For example, researchers have found that polymers can shield against the impacts of severe radiation because of their high hydrogen properties and light weight. Similarly, nanotubes can increase the strength of polymers to enhance their electrical and thermal conductivity. According to Dr Larry Marshall (Chief Executive, CSIRO), “Science becomes real in the hands of visionary partners like Boeing who are willing to embrace science to support the development of a whole new sustainable and resilient industry that supports a green recovery.” For example, CSIRO researchers and end-users are investigating the use of hydrogen in commercial air travel to increase sustainability, which in turn, will reduce costs. By 2035, hydrogen may provide deeper decarbonisation when used alongside existing airport and aircraft infrastructure.
Dr Marshall believes it could then support a complete transition from conventional jet fuel around 2050. "As we see travel resume, hydrogen presents a key solution to enable a sustainable recovery for the industry using liquid renewable fuel, and to grow future resilience from threats like oil shocks.”
CSIRO swung into action as the COVID-19 pandemic brought the international and domestic travel industry to a grinding halt, with a suite of new research offerings. Likewise, the industry itself was forced to reconsider their paradigm and recover to a different ‘normal’.
The Chief Executive Officer at Qantas Domestic and International Andrew David said the aviation sector was heavily impacted by the spread of COVID-19.
“Early in the pandemic we were 11 weeks from bankruptcy and have since posted $6 billion in losses and over $24 billion in lost revenue.”
“But because Qantas came into the pandemic in a strong position, and as a result of making some very difficult decisions, we’ve been able to weather the storm,” he said.
As the sector emerges from the depths of global lockdowns, carriers are demanding low weight, yet stronger aircraft that boast a high strength-toweight ratio.
The global aerospace materials market is expected to reach US$57.9 billion by 2026, according to the research and advisory firm, MarketsandMarkets. The market will also to grow by 8.8% year-on-year from 2021 to 2026, and offer new opportunities for highperformance materials, sustainability, and cost-effective travel.
The Age-Old Problem of Fatigue
Fatigue is the most common way in which aircraft structures and engine components are damaged. In fact, aircraft fatigue causes over 50% of all metal component failures. Researchers have found the most common type of damage on a Boeing 747 jet was fatigue cracking (58%), corrosion (29%) and then impact damage from events like bird strikes (13%). The study examined 71 Boeing 747s with an average of around 30,000 flying hours. Aerospace materials are subject to a range of fatigue: • Cyclic stress fatigue occurs by the repeated application of loads to the material • Corrosion fatigue: occurs by the combined effects of corrosion and cyclic stress loading • Fretting fatigue is the progressive deterioration of materials by smallscale rubbing movements that cause abrasion of mating components • Acoustic fatigue is caused by highfrequency fluctuations in stress caused by noise • Thermal fatigue is caused by fluctuating stresses induced by the thermal expansion and contraction of materials owing to thermal cycling Aerospace engineers are tasked with selecting and development materials with a high tolerance to these types of fatigue. Increasingly, there are other challenges like cost, longevity, and sustainability.
How are Manufacturers Overcoming Challenges in theSector?
Aeronautical and space components need exceptional strength and resistance to a range of extreme conditions. As such, the aviation industry is making deliberate efforts to crack down on sustainable practices. Boeing and Airbus—the world’s biggest aviation manufacturers—are using their slick designs to reduce payload and fuel on long-haul flights. The two manufacturers are placing materials and process science at the core of their business to drive their change. Boeing has used carbon-fibrereinforced polymer composites in its Boeing 787 Dreamliner, which has made lighter airframe components a reality. This has led to a 15% reduction in fuel and makes the Dreamliner up to 25% more efficient than other similar aircraft.
Boeing is also a participant in the United Nations’ (UN) ‘Decade of Delivery’, which supports a global push to protect the planet. The program runs in line with the Sustainable Development Goals (SDGs). “Boeing’s support for the UN SDGs shows that every single day our employees lead with purpose and are part of something bigger,” said Boeing’s Chief Sustainability Officer Chris Raymond. “These goals ensure that the world is moving in the right direction together toward a more sustainable future and it illustrates that Boeing is working hard to earn trust among our stakeholders,” he added.
Like aeronautical and space components themselves, the environmental impact of fuel is also an important consideration for scientists and engineers. As such, Qantas and Airbus recently signed a landmark agreement to fasttrack Australia’s sustainable aviation fuel (SAF) industry. The US$200 million agreement will bring SAF production to Australia and cut greenhouse gas emissions by around 80%. This fuel can be used in contemporary aircraft, with no modifications to engines. Qantas has committed to using 10% of SAF in its mix by the end of the decade. “Aviation is an irreplaceable industry, especially for a country the size of Australia, and one that’s located so far away from so much of the world. Future generations are relying on us to get this right so they too can benefit from air travel,” said Qantas Chief Executive Alan Joyce. “The aviation industry also needs the right policy settings in place to ensure the price of SAF comes down over time so that the cost of air travel doesn’t rise,” he added.
SAF can reduce carbon dioxide emissions by up to 80% over their life cycle when compared to conventional jet fuel.
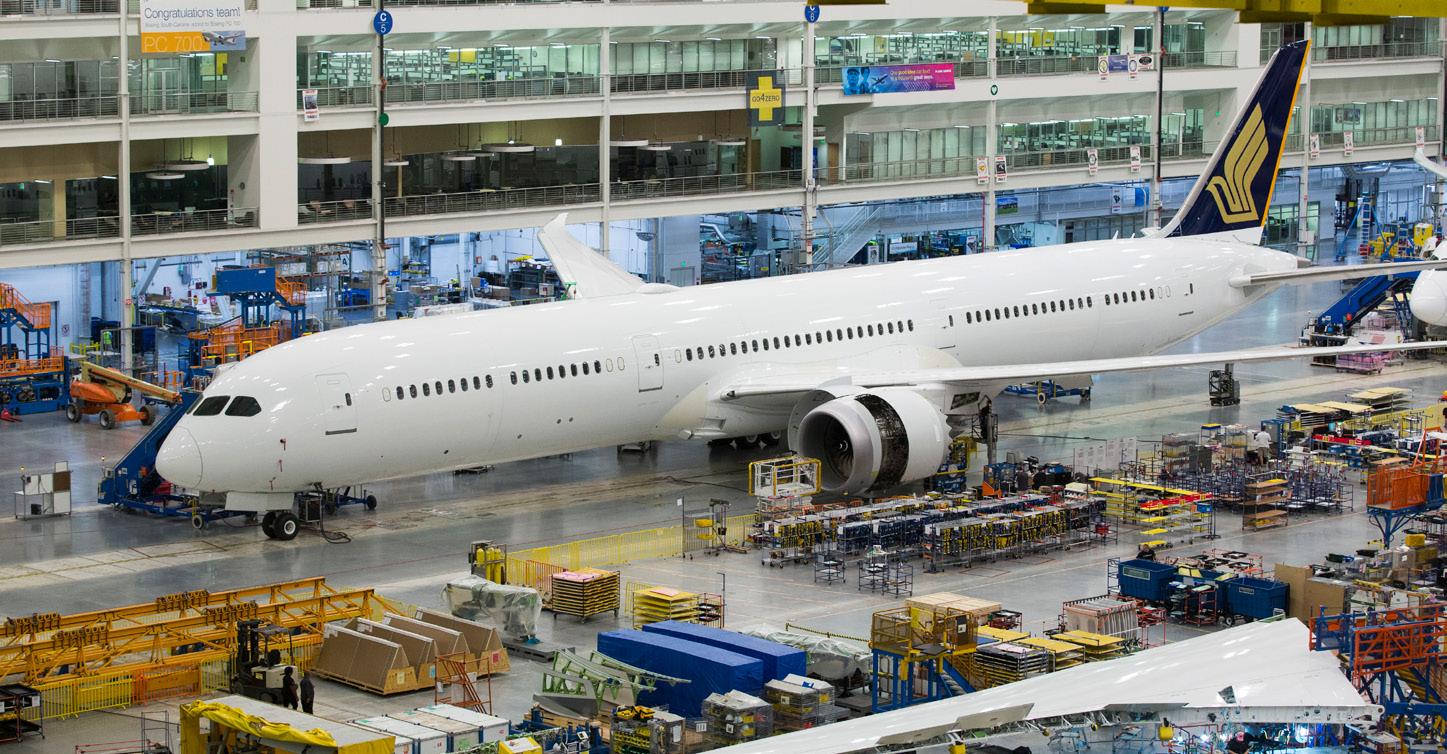
Boeing rolls out the first 787-10 Dreamliner built for Singapore Airlines at its Final Assembly facility in North Charleston, South Carolina. (Josh Drake photo). Photo courtesy of Boeing.
Industry Partnerships are TakingOff
Aerospace components and materials rely on a swift research-into-practice loop, where end-user driven challenges are met with a suite of opportunities. The Institute of Frontier Materials, which is based at Deakin University’s Melbourne campus, has a growing body of researchers who are working on carbon fibres to bring tailored functionality to industry partners. These fibres can change colour, as well as absorb and store energy.
“Our focus is the development and implementation of surface modification techniques that allows us to install a chemistry on the fibre surface that is for a specific application. At the moment it’s a ‘one-size-fits-all’ approach,” said Professor Luke Henderson, who is the research team leader.
The surface of carbon fibres is typically inert, and little will respond or react with it. This is a challenge for the final material.
“We have given carbon fibres new and previously-thought-impossible functionality,” Professor Henderson said. The research team has been funded and supported by a range of high-level partners, including: Boeing, SABIC, Solvay, Fortescue Metals group, Rolls Royce, Ford USA, Gen2Carbon and CASS Foundation. In addition, the Australian Research Council have supported the group. Carbon graphite is black and, in the past, there were only two ways to change the colour of carbon fibres— either painting the surface or weaving the fibres with a dyed fabric. However, Deakin researchers made modifications to the fibre that turned the carbon fibres into an electric blue colour.
According to Deakin University Materials Chemistry Professor Luke Henderson, “The real kick is that it works by the same mechanism as nature’s way to generate blue colours. Blue in nature is very hard to generate with a pigment—what it does is use the wavelengths of light to interact with each other.”
“It’s the same way that butterflies and peacocks generate their iridescent blue. So we went with a bio-inspired colour generation theme rather than a pigment approach,” Professor Henderson said.
Likewise, leading researchers at the Australian Nuclear Science and Technology Organisation (ANSTO), are deep into addressing the challenges that extreme environments have on aerospace components. ANSTO is looking at the role that novel nuclear-based energy-generation systems can have on a range of settings, like corrosion, oxidisation, high temperatures, and radiation. The research covers how nickelbased superalloys can be included in aerospace materials to withstand temperatures above 500°C. Meanwhile, reinforced carbon—carbon composites can used for thermal and thermal-shock shielding, which is a gamechanger for the space shuttle’s nose. Lastly, ultra-High Temperature Ceramics are being considered for their strong covalent bonds, which can endure a melting temperature above 2,500°C and boast a good oxidation resistance.
This research is translating into practice, as private technology developers begin reaching for the stars. For example, Gilmour Space Technologies is developing new capabilities for launching small satellites into space. The Queenslandbased startup is one of Australia’s leading space companies, as they pioneer innovative hybrid propulsion technologies with the goal of providing lower cost access to space. “We are designing, developing and building a launch vehicle to take small satellites into space, and we are doing this in Australia,” said Adam Gilmour (Founder and Chief Executive Officer, Gilmour Space Technologies). “It has always been incredibly difficult and expensive to send anything into space, but thanks to the last decade of technology advancements, satellites that used to be the size of a fridge can now be made in the size of a microwave, with perhaps the same or better capability.” “This rapid technology advancement caught the industry by surprise. Many of the major aerospace companies have been building bigger and bigger rockets, and we saw the opportunity to provide smaller launch vehicles to transport this new generation of smaller satellites to space,” Gilmour said.

Gilmour Space Technologies.
Opportunities to Reach New Heights
The Australian aerospace sector relies on a strong pipeline of next generation thinkers who can drive change and develop Australia’s interest in this emerging area. As global space supply chains bounce back from the height of COVID-19 lockdowns, they are becoming more gloablised. Meanwhile, innovation is accelerating at an unprecedented pace. As such, there has never been a more exciting time to jump on board the space bandwagon and launch into a new stratosphere of opportunity. CSIRO is at the forefront of aeronautical and space innovation in Australia through the National Space Mission for Earth Observation, which is a $1.2 billion program to design, construct, launch and operate four new Earth observation satellites.
“The recent launch of our CSIRO Centre for Earth Observation provides a dedicated facility for satellite-derived
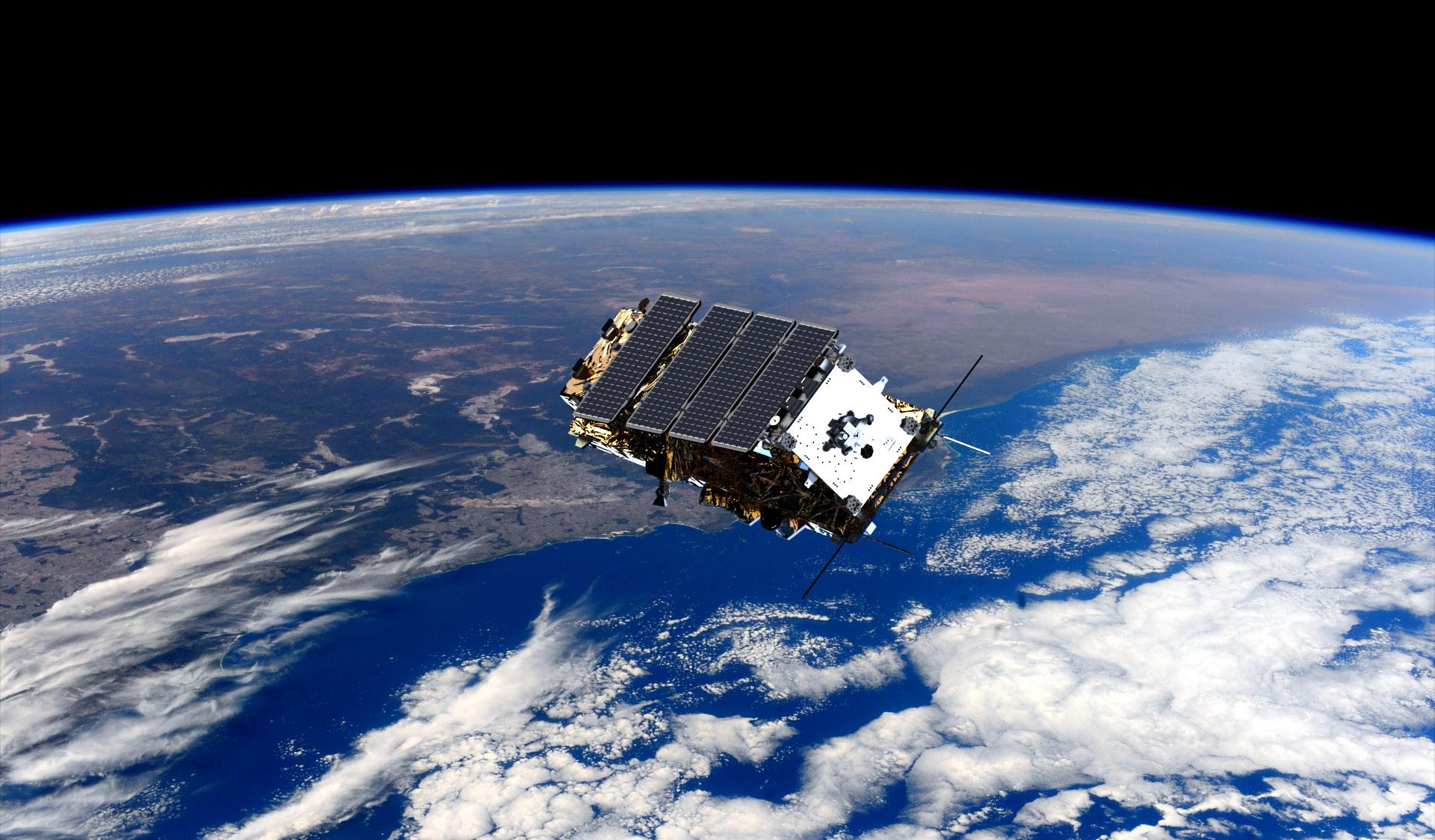
Ground communications for our share of the NovaSAR-1 satellite will be managed by the Centre for Appropriate Technology (CfAT), Australia’s first and only Aboriginal owned-and-operated ground station provider. Image: Surrey Satellite Technology. Image courtesy of CSIRO.
CfAT technicians put the finishing touches on the satellite dish for the earth ground station in Alice Springs. Image: Ekistica Ltd. Image courtesy of CSIRO.
data, including data gathered from our tasking and acquisition time on the NovaSAR satellite, the first time Australian scientists have ever been able to drive an imaging satellite,” said Dr Larry Marshall (Chief Executive, CSIRO). “We are committed to continuing to grow a diverse and robust space industry in Australia, including bringing our world-class science, technical solutions, and partners to the table.”
The Australian Government is also supporting 20,000 new jobs by 2030, which will triple the nation’s space industry to $12 billion. As part of this ambitious target, there are opportunities in: • The commercialisation of rocket technology • Nano and small satellites • Launch vehicles and facilities • Propellants and fuels • Position, navigation, and timing tools • Communication technologies • Aerospace medicine There are already several aeronautical and space projects in the works, including a $150 million Moon to Mars initiative, which is linking Australian researchers with NASA to go back to the Moon, and beyond, to Mars. There is also the $65.7 million Fast Tracking Access to Space initiative, which will get Australian technologies into space sooner. It also seeks to position Australia as a leading nation for space launches. The International Space Investment initiative will unlock new space opportunities by working with India’s space industry. It is supported by a $3 million boost for broader international partnerships. Finally, the Australian Taxation Office is helping businesses secure investments in the sector by sharing guidance and support.
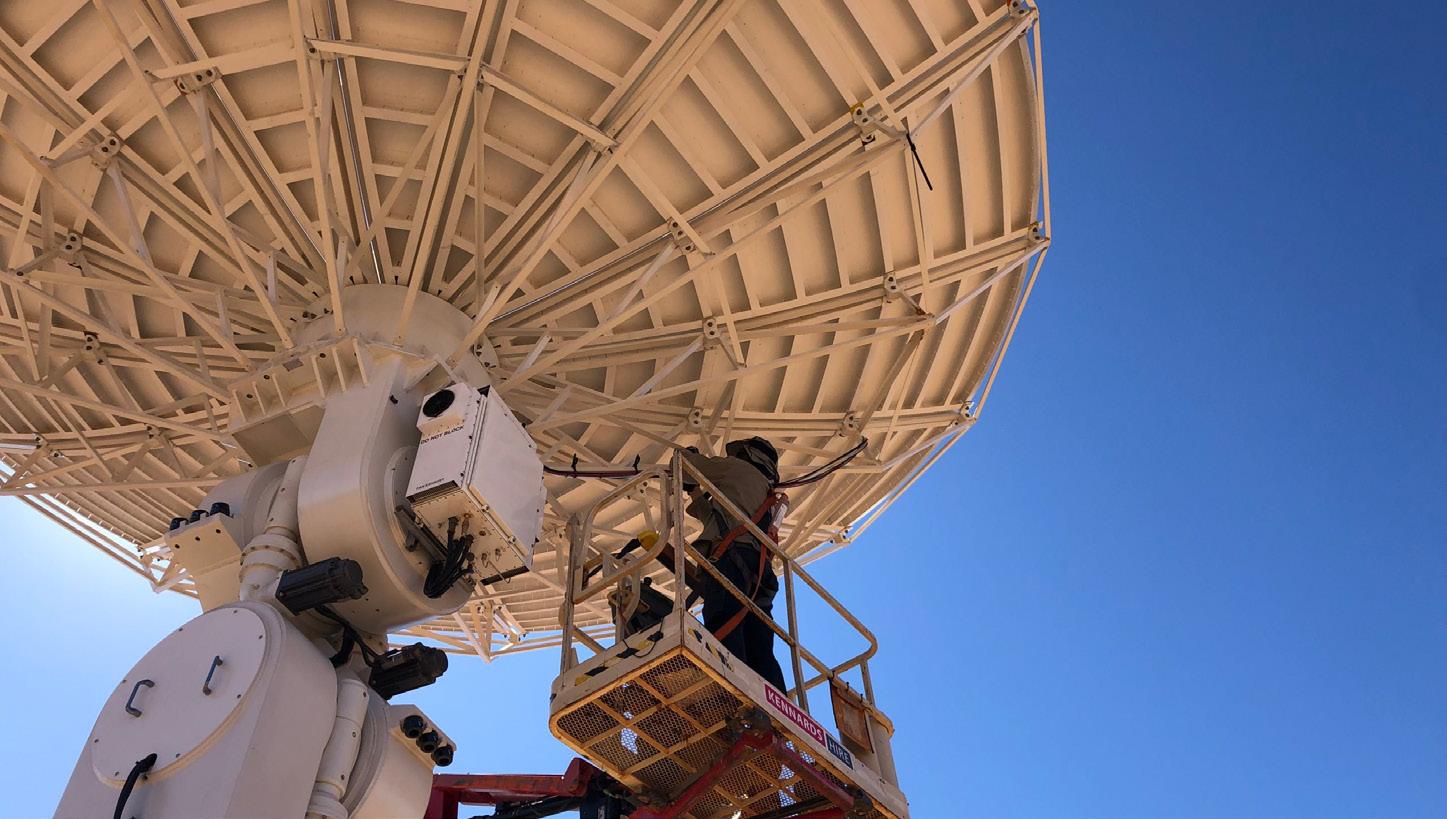
Australia Shoots for the Stars
Source: Sally Wood
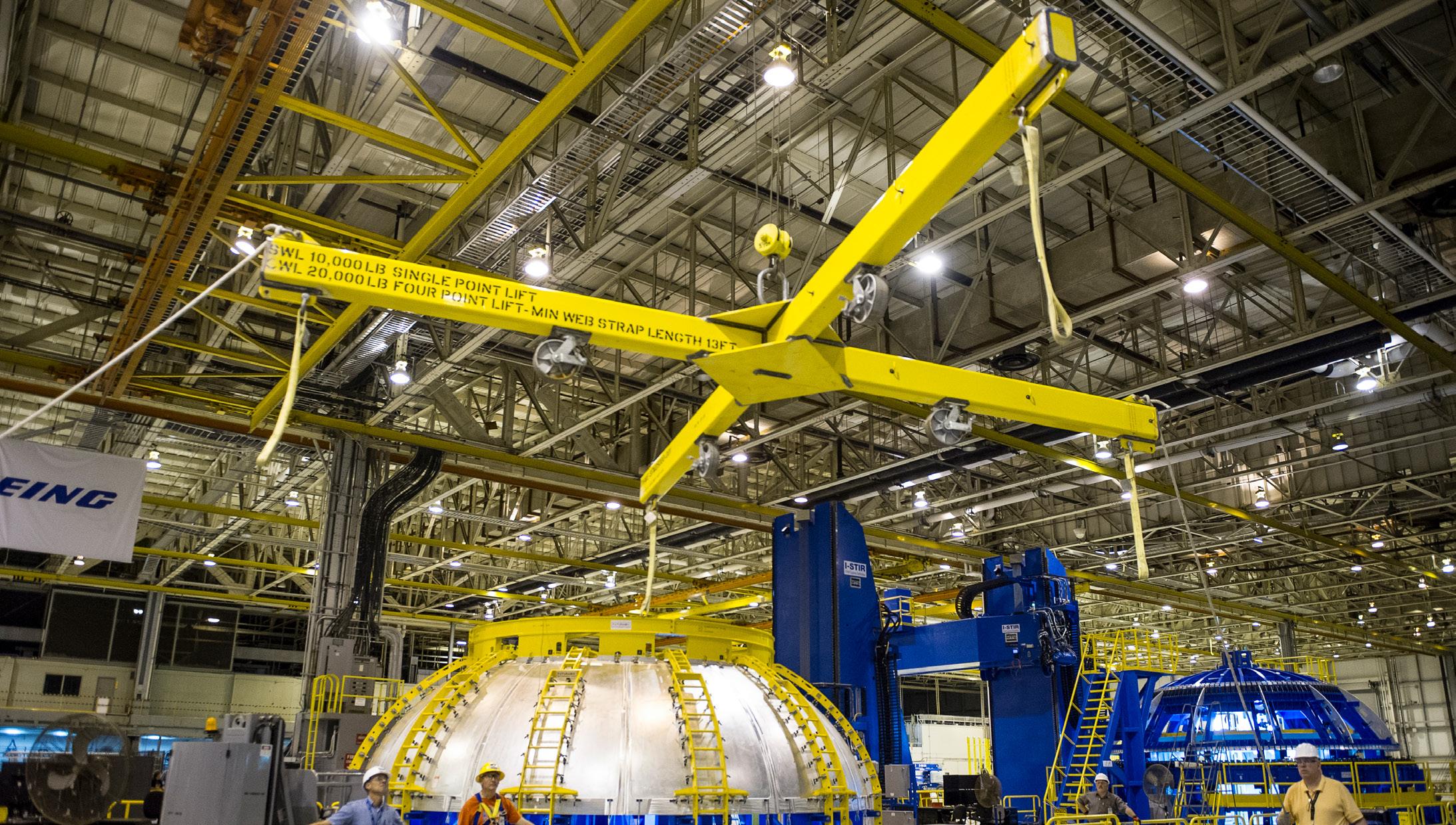
Space launch system manufacturing. Photo courtesy of Boeing.
The aeronautics and space sector constantly develops new tools like additive manufacturing, or novel components to take to new heights. The Innovative Launch, Automation, Novel Materials, Communications, and Hypersonics (iLAuNCH) program is bringing 23 industry organisations and three universities under the same roof to develop Australia’s space program. This sovereign capability will grow Australia’s commercially viable civil rockets; rocket manufacturing; and in-space hardware like satellites and communications.
The University of Southern Queensland, Australian National University and University of South Australia will lead the charge. Professor Peter Schubel from the University of Southern Queensland’s Institute for Advanced Engineering and Space Science said iLAuNCH will operate as a national space commercialisation hub. $3.65 billion in economic benefits associated with the 18 core iLAuNCH commercialisation projects, which will accelerate Australian IP to market, and the development of a Space Engineering Degree that will create a pipeline of skilled, job ready engineers into this exciting high-value, highgrowth sector,” he said. The University of Southern Queensland is the nation’s only institution with end-to-end rocket manufacturing capacities. This includes everything from design to launch capabilities. Meanwhile, the Director of the ANU Institute for Space Professor, Anna Moore said the three universities have valuable space research specialties. “This opportunity is an amazing first step toward ensuring Australia's sovereign space capability grows well into the future, and we're delighted to be partnering with the University of Southern Queensland,” she said. It is expected to generate over $3.65 billion in economic benefits across the region and Australia.
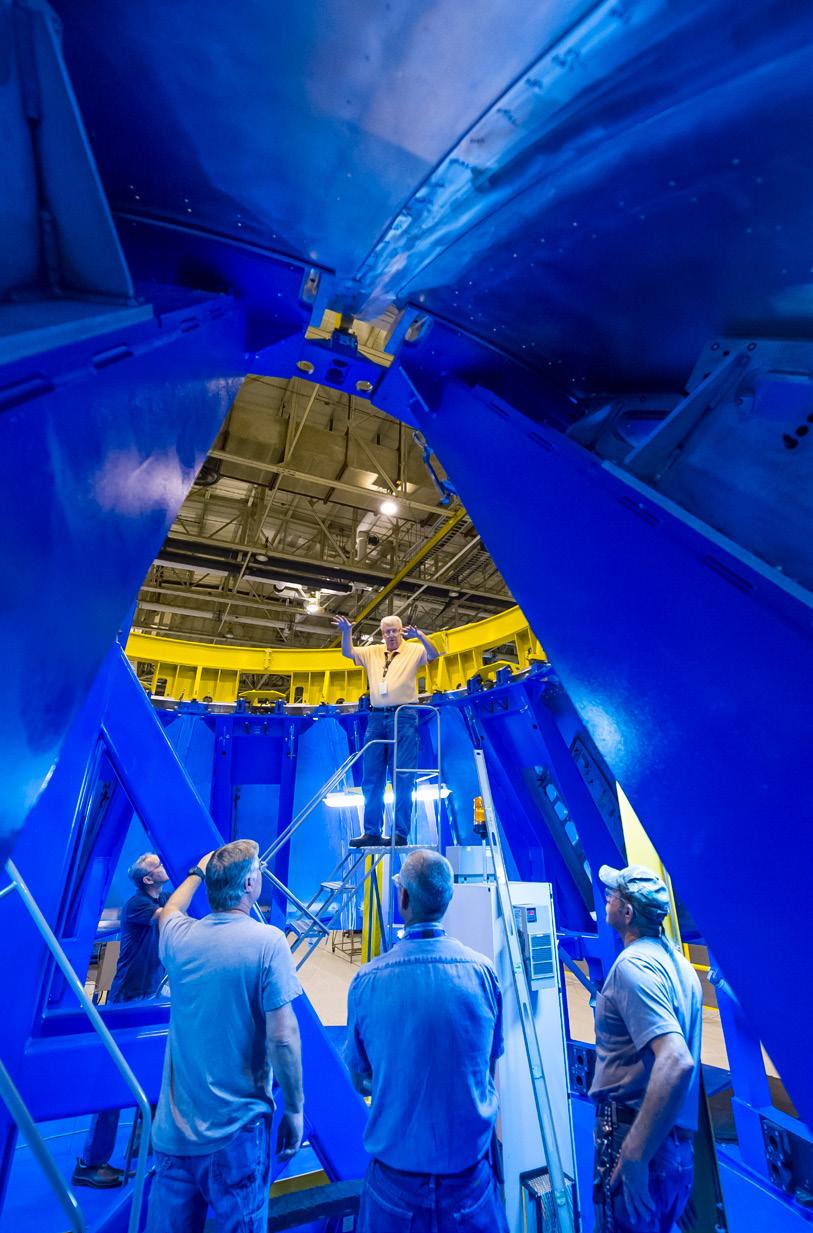
Space launch system manufacturing. Photo courtesy of Boeing.
AML3D to Develop 3D Printed Components for Boeing
Source: Sally Wood
AML3D Limited recently received an additional purchase agreement to develop and produce 3D printed components for aviation powerhouse, Boeing. The key components involve extensive printing of high-strength aluminium, and an intensive testing program. This is comparative to the testing of structural components and aligned with the requirements of AS9100D quality assurance for ‘fly’ parts. As a global aerospace company, Boeing develops, manufactures, and services commercial airplanes, defence products and space systems for customers in more than 150 countries. The company uses the talents of a global supplier base to advance economic opportunity, sustainability, and community impacts. The AML3D purchase agreement for $140,000 will be received from Boeing on standard commercial terms. These parts will be manufactured using AML3D’s proprietary Wire Additive Manufacturing (WAM) process. AML3D’s Managing Director, Andrew Sales said the components will be tested and validated for the basis of near-term future work. “AML3D is excited to continue working with Boeing, and cementing our relationship with one of the world’s largest aerospace companies through our proprietary WAM® process.” “This purchase contract is a major step in our journey and will provide the Company further opportunity to now validate and produce parts on time and to specification for a high-quality Tier 1 customer, which is further endorsement of the adoption of our proprietary WAM® 3D printed solutions and core to our Strategy for the Company in the coming years,” he added.
The agreement follows a visit and technical discussions with Boeing’s Director of Global Additive Manufacturing in March. The agreement is a sign of Boeing’s commitment to innovating for the future. It also aligns with the company’s core values of safety, quality, and integrity.
AS9100D:2016 Certification for Aerospace Parts
AML3D has also recently implemented the Aerospace Quality Management System AS9100D:2016 Accreditation. This accreditation is essential and unlocks the potential for the company to manufacture ‘fly’ parts for use in aircraft. This makes AML3D the second 3D wire feedstock additive manufacturing company to achieve the Standard, which offers significant competitive advantage when bidding for contracts.
“Implementation of AS9100D certification will further demonstrate AML3D’s commitment to delivering the highest quality components into the aviation, space and defence industry,” Sales said.
The AS9100D:2016 Standard provides the framework for world-class business growth through a risk and opportunity-based process approach to managing the business. “This is an important step in our growth strategy for the company as we pursue high-value contracts for aerospace,” Sales explained. The accreditation process is expected to be completed in the second half of the 2023 financial year, at a cost of approximately $25,000, with funding sourced from the company’s recent ‘growth initiative’ capital raise. The process neatly aligns with AML3D’s focus on enhancing the quality of its products and service, and enhancing customer satisfaction. “We are excited to further progress into the aerospace industry with our technology, further validated by this certification,” Sales said. AML3D hopes the accreditation will expand its potential customer base, support decisions for existing clients, procure more components, and refer more customers to the company.
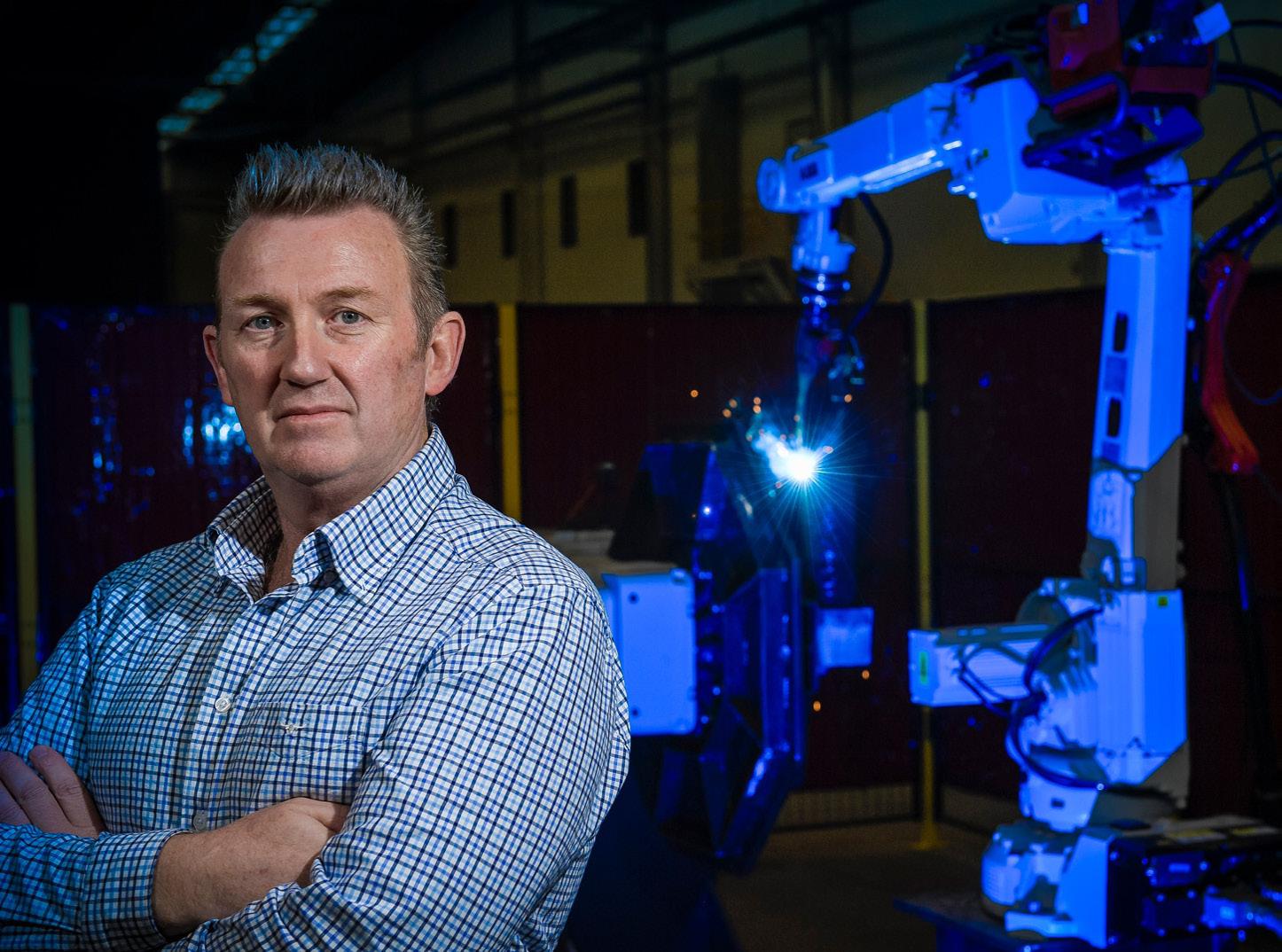
Andy Sales, Founder and Managing Director of AML3D.
Global Aerospace Company Partners with Australian Manufacturer of Composite Tanks
A collaborative partnership between Lockheed Martin, Omni Tanker, and the University of New South Wales (UNSW) will commercialise world-first composite tank technologies. This innovative research program seeks to solve the challenges of using composites for the transportation and storage of liquid hydrogen. It has a range of applications on the ground, in the air, underwater and in space. The project was recently announced as part of the Federal Government’s Advanced Manufacturing Growth Centre (AMGC). The co-funded initiative is worth $1.4 million and will put a range of local technologies to the test. Christopher Hess is the Head of Industrial Development at Lockheed Martin Australia, who said the AMGC’s support will go hand-in-hand with the ongoing collaboration between UNSW and Omni Tanker.
“We have had a long-standing research collaboration with UNSW and Omni Tanker, and we are grateful for the support of the AMGC as we now look to commercialise these cutting edge, Australian-developed composite tank technologies for a number of Lockheed Martin and NASA applications,” Hess added. The project will combine nanoengineering technology developed by UNSW in partnership with Lockheed Martin and Omni Tanker.
Together, the team will develop two new operational scale propellant tanks for storing cryogenic liquid fuels for commercial and civil satellite programs. • A ‘Type IV’ fluoropolymer-lined carbon fibre composite tank • A ‘Type V’ linerless carbon fibre composite tank These tanks will draw on Omni Tanker’s patented OmniBIND™ technology and be equipped for a range of environments. David Ball is Lockheed Martin Space’s Regional Director Australia and New Zealand, who said the tanks are lightweight, cost-effective, and resistant to microcracking. “As the world increasingly looks to hydrogen for emission-free energy, containing and transporting it in a safe, cost-effective and economic manner remains extremely challenging.” “The space industry is particularly interested in the development of linerless composite tanks for their weight efficiency and durability, which represent the cutting edge of composite pressure vessel manufacturing,” he added. In all, this research has the potential to support Australia’s sovereign space capabilities, strengthen space-faring allies and partner nations, and make important technological contributions to future space missions. The project builds on the recent work of UNSW researchers, who discovered carbon fibre composites that can withstand liquid hydrogen temperatures without matrix cracks. The research was led by Professor Chun Wang, who said this is a challenge that has, up until now, prevented mass-market adoption of these materials for such applications. “This new technology is the result of an outstanding collaboration and partnership between UNSW, Lockheed Martin and Omni Tanker over the past four years. It is wonderful seeing our research achievement is now moving closer towards commercial success and generating social and economic impact in Australia and beyond,” Professor Wang said.
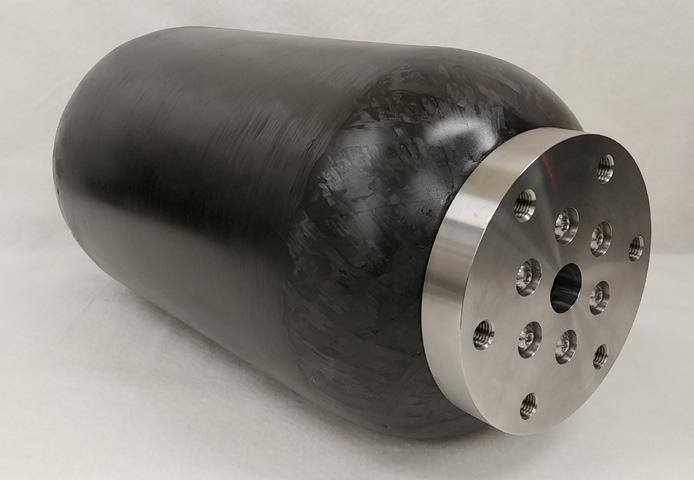
Linerless liquid hydrogen tank
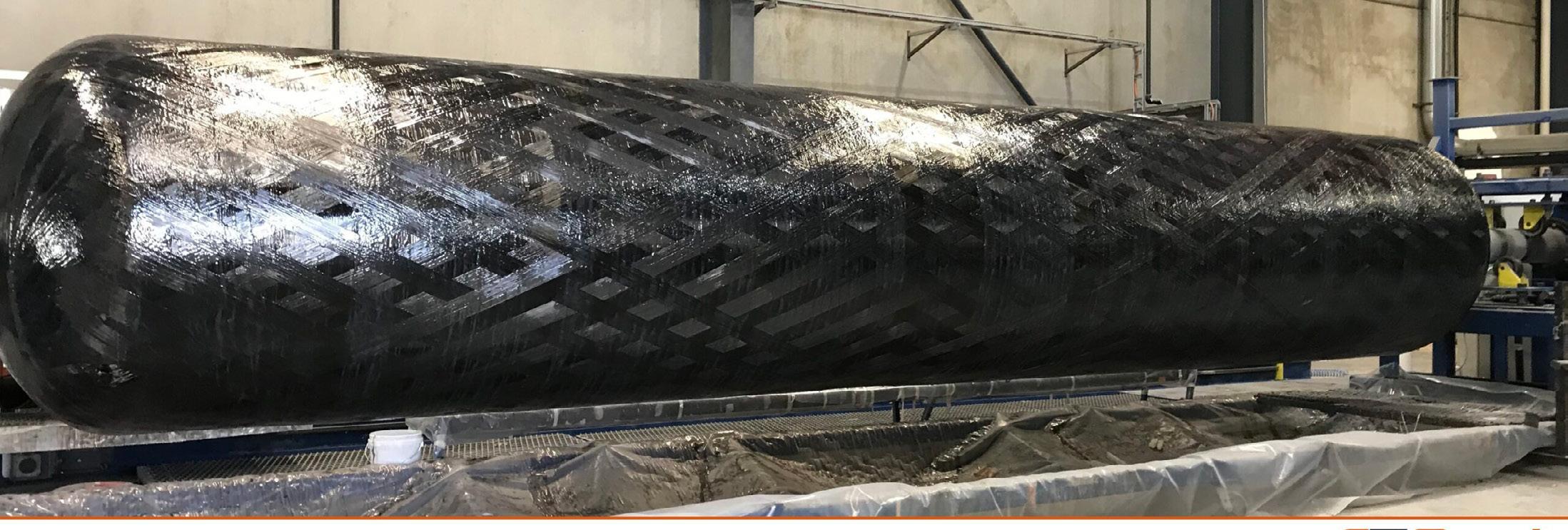
Source: Sally Wood
The Melbourne based additive manufacturing company, Titomic has been awarded $2.325 million as part of the Federal Government's Modern Manufacturing Initiative (MMI). This funding will enable Titomic to create a range of new material blends and offer high-performance coatings for Australia’s growing space sector. The company will primarily focus on environmentally sustainable components, and how they can be incorporated into practice. Herbert Koeck is the Chief Executive at Titomic, who said the collaboration allows his company to offer the custom Cold Spray Additive Manufacturing (CSAM) technology systems into partner supply chains. “This project allows us to show our unique capability to use industrial scale additive manufacturing to create world leading ‘low carbon footprint’ green titanium and high-performance coatings for satellites and space vehicles,” he said. The company specialises in the creation of large-scale additive manufacturing techniques, and hopes to use its CSAM technology to fabricate complex material blends for radiation shielding and hypersonic protection. The MMI grant is one part of a planned project expenditure of $4.65 million, which allows Titomic to build and commercialise space vehicle parts using green titanium, and a range of other high-performance coatings. Titomic will work with Swinburne University of Technology, and the Australian Nuclear Science and Technology Organisation (ANSTO) to conduct a series of tests to prove that its demonstrator parts can be used within its Titomic Kinetic Fusion technology. “This MMI space-based applications grant is a huge step forward for Australia’s manufacturing sector,” said Professor Alan Duffy, who is the Director of the Institute for Space Technology and Industry at the Swinburne University of Technology. “This takes the longstanding collaboration between Titomic and Swinburne University of Technology to a new level, building Australia’s reputation as an innovative and highvalue space manufacturing nation and we welcome companies and researchers to access this national space manufacturing facility in Victoria,” he added. Swinburne will receive the TKF1000 additive manufacturing system from with an Industry 4.0 additive manufacturing platform embedded within its Kinetic Fusion Technology (KET). “Our supply of a TKF1000 System to Swinburne University of Technology with its Industry 4.0 additive manufacturing platform to drive high-value technological and material developments, will also accelerate space and manufacturing sector growth in Australia, creating highvalue jobs, and attracting local investment,” said Herbert Koeck from Titomic.
Together, this unlocks the potential for researchers and students to grow Australia’s advanced manufacturing and space sector capabilities. This industrial-sized, metal 3D printer will pave the way for new avenues for specialist additive manufacturing processes. “We can build lighter, stronger and more capable structures of incredible complexity that will allow Australian companies to leapfrog ahead of the competition in building for space,” Professor Duffy said. The TKF1000 machine will be one of two in the world. The British research and technology institution, TWI currently houses the other. Professor Pascale Quester is the ViceChancellor and President Swinburne University of Technology, who said the MMI grant offers educational and economic benefits to Australia.
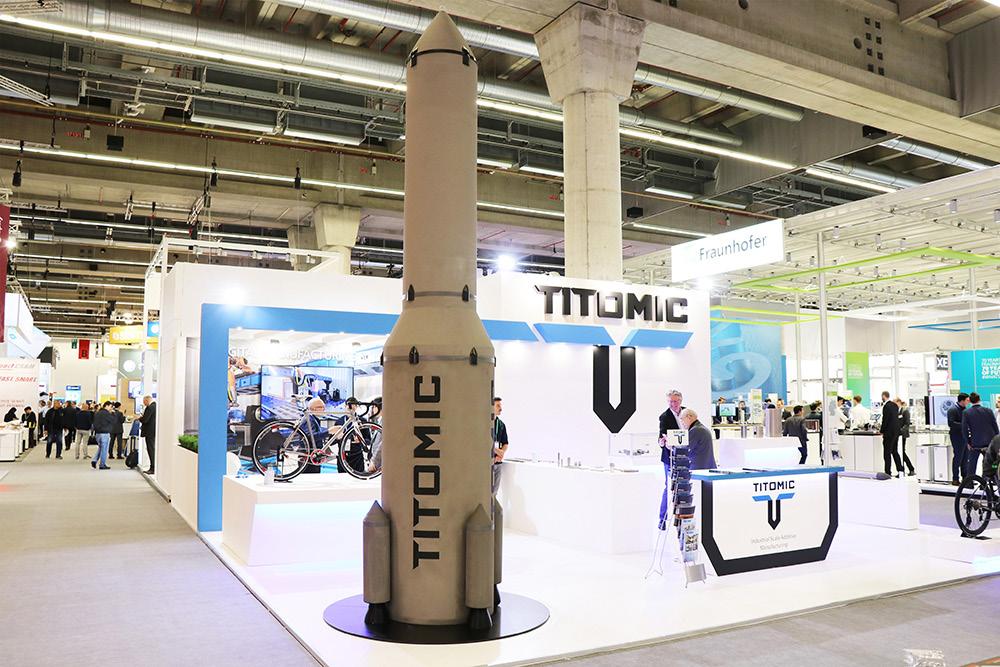
Titomic's 5.5 meter 3D printed titanium rocket. Image courtesy of Titomic.
Boeing and RMIT to Research Space Manufacturing Capability
Boeing and RMIT University recently signed an agreement to scope the future of materials research and process innovation capabilities, alongside Australia’s growing space sector.
Boeing is a trailblazer in the aviation space and is seeking to expand its relationship with research institutions like RMIT.
Boeing Defence Australia Director of Aerospace Engineering and Production, Paul Watson, said Australia’s burgeoning space sector requires the ongoing production of complex, low volume, bespoke components not suited to conventional manufacturing techniques. “This partnership will develop new knowledge in advanced manufacturing technologies which will not only stimulate the development of a local fabrication capability but will also expose Australian industry to space export markets as part of Boeing’s global supply chain,” he said. The research undertaking positions Boeing—one of the first companies to venture into the commercial aviation market—at the forefront of the next frontier to build a strong sovereign space manufacturing capability. Boeing already has a longstanding relationship with RMIT, which offers a launchpad into industrial solutions dedicated to growing Australia’s space sector.
RMIT’s Deputy Vice Chancellor for Research and Innovation, Professor Calum Drummond AO, said the research and development will be undertaken at RMIT’s Space Industry Hub. “Our ultimate goal is to maximise opportunities for commercialisation of the products that we co-develop with Boeing,” he said. The Hub, which was launched in 2021, offers a tangible pathway for local businesses to grow their skills and export globally. “Leveraging Boeing and RMIT’s joint expertise and facilities, we believe we can unlock boundless future opportunities for Australian industry,” Professor Drummond said.
In 2019, Boeing signed a statement of intent to invest in research and development activities with the Australian Space Agency. The agreement focussed on the several key areas: • Space situational awareness • Space manufacturing and materials • On-orbit image processing • Space launch and hypersonics • Remote spacecraft operations • Antimicrobial surfaces for space systems • Virtual reality and augmented reality in space Boeing also offers a number of scholarships to Australian university students, where they can sharpen their skills and become part of the next generation of aerospace innovation. In 2021, four Boeing-funded grants were awarded to local students in a strong sign that the sector is gaining pace and momentum. Aaron Johan was one of the first to receive a Boeing scholarship after knocking on the door of the aviation sector for many years. “I’ve had a fascination with aircraft— fixed and rotary wing—since I was about 10 years old,” he said. “When I left high school I didn’t have the financial means to pursue an aeronautical engineering degree so I moved to Victoria to be a commercial aircraft mechanic but wasn’t successful in getting a position.” “I returned to Queensland to study at Aviation Australia but the financial support I had secured fell through before I could start. It was then I met with Boeing and they offered me a scholarship,” he explained. Boeing is on the hunt to leverage the knowledge it has fostered through this program, and other research partnerships, as it casts its efforts towards a growing role in the sector.
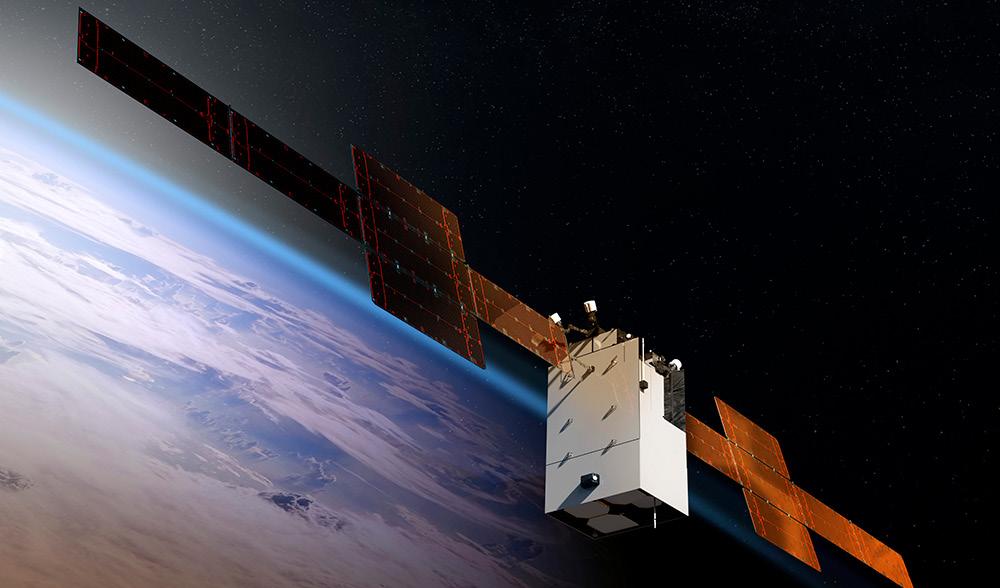
Above: The WSG-11+, will be added to the US military WSG network in 2024. It is hoped that collaborations with Australian industry will lead to support opportunities within Boeing’s global supply chain. Image courtesy of: Boeing
Left: RMIT University is a world leader in the development of advanced manufacturing technologies for aerospace. Image courtesy of: RMIT
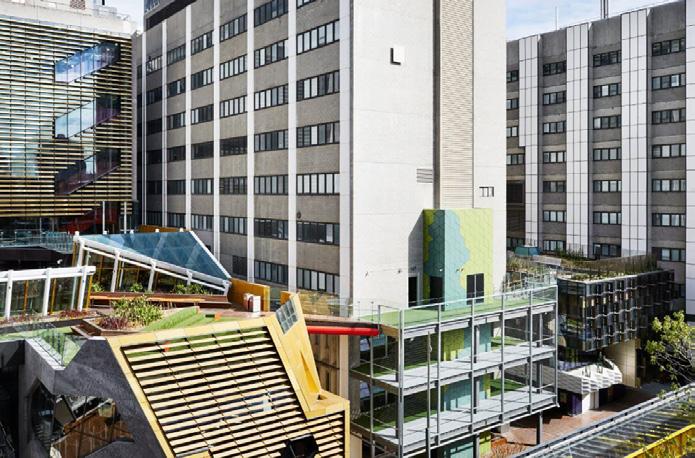
Testing Time for Australian Space Hardware Manufacturers
Source: Sally Wood
A new funding round has been provided to the Australian Nuclear Science and Technology Organisation (ANSTO), which will grant local manufacturers with access to onshore facilities that are currently only available in Europe and the United States.
While Richard Branson and Jeff Bezos have leaped out of this world, travelling in space remains a risk for the masses.
Space infrastructure, like satellites need to withstand the extremities of space, where they are exposed to conditions quite unlike anything on Earth. This latest ANSTO grant of $665,000 will propel Australia into a worldleading space centre with facilities to test payload, components, and hardware prior to their deployment into space. It forms part of the Federal Government’s $2.5 million investment towards the National Space Qualification Network (NSQN), which brings industry and academia under the same roof to provide certification for satellites and other space-bound technologies. The Head of Research Infrastructure at ANSTO, Dr Miles Apperley said the NSQN partnership will tap into local talent. “It’s incredibly exciting to see this collaboration in our space industry and this partnership will put Australia firmly on the global stage,” he said. “It will bring together all the experience and knowledge from each organisation to offer a well-oiled mechanism for space companies to conduct product testing on Australian shores. The space industry has created a rapidly growing need for innovation in Australia. It has the potential to create new jobs and businesses for the next generation and I can’t wait to see how the industry continues to grow over the coming years,” Dr Apperley explained. ANSTO boasts a range of ion beam, x-ray, and gamma-ray irradiation capabilities, which allows researchers to test materials used in space components. This latest round of upgrades will maximise the efficiency of prepping electronics for the extreme environment of space. Dr Ceri Brenner is ANSTO’s recently appointed Leader of the Centre for Accelerator Science. She said the new funding would enable ANSTO to apply its considerable knowledge to the area of space testing and qualification of electronic devices.
“Nearly all products that go into space, like rocket ships and satellites, are operated by technology.” “If the technology malfunctions, that product is in real trouble. For all the obvious safety and financial reasons, manufacturers want to be certain that when they launch a product into space, it can withstand the harsh climate it’s entering,” she explained. For example, ANSTO recently commissioned a new beamline to support space research relating to the impact of galactic cosmic radiation on astronauts.
This places ANSTO in a unique position, where they have the expertise, the equipment, and the knowledge for this much-needed program to be a success. Dr Brenner believes Australia’s young but enthusiastic space industry is counting on these initiatives to thrive. “And that is where ANSTO and its partners can step in with our testing capabilities. We can help provide that certainty with our instruments and techniques. Rigorous testing sees the product exposed to radiation, vibrations, extreme temperatures and vacuums, to ensure it is space-ready.”
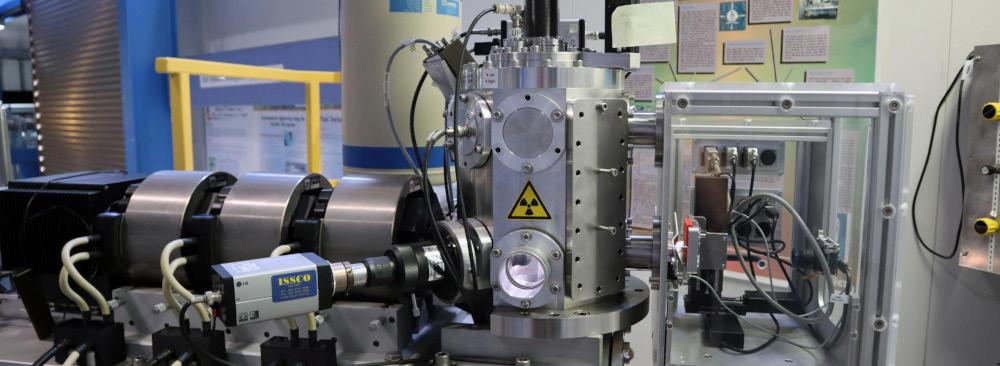
The high energy heavy ion microprobe at ANSTO. Coupled with an accelerator system, this unique scientific instrument is capable of producing a highly focused beam of accelerated ions with a spot size down to sub-micrometre dimensions. Image courtesy of: ANSTO.
Jetting Off with 3D Printing
Source: Sally Wood
3D Printed Jet Engine © Monash University, Centre for Additive Manufacturing.
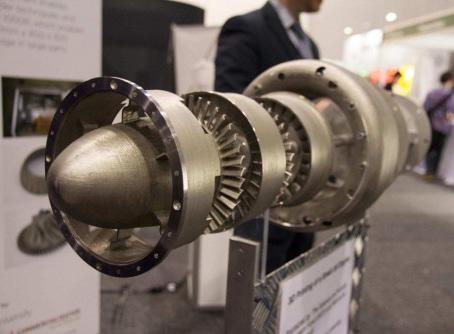
Jet engine components can take anywhere from six months to two years to complete. This is a significant challenge, particularly because of the rapid development of technology and designs in the aviation industry. However, Australia’s national science agency CSIRO, have created the world's first 3D printed jet engines. These devices were created by using different additive manufacturing technologies and were then successfully combined into a finished product. “I have worked with the aerospace industry for about 25 years with companies such as Rolls-Royce and Airbus,” said Xinhua Wu, who is the Director of the Monash Centre for Additive Manufacturing. The Arcam Electron Beam Melting printer was used to print the engines, alongside cold spray technology, which printed a variety of jet engine components. The device allows materials to be 3D printed at a relatively high rate. “Arcam is one of the world’s leading places for 3D printing of aerospace components. Data put us at the forefront of the international arena for 3D printing,” Professor Wu said. The jet engine is part of a successful list of other additive manufacturing success stories like mouthguards, horseshoes, and bikes. In fact, the metal 3D printing market is expected to be worth $10 billion by the end of the decade. Researchers and industry trailblazers connected at the Lab 22 manufacturing facility in Melbourne to prove that these parts can be made in a matter of days. The Lab 22 facilities offers a range of important services, including: • Metallic 3D printing • Advanced machining for improved profitability • Surface engineering for enhanced performance • Laser assisted additive deposition
Laser heat treatments “It was our chance to prove what we could do,” Professor Wu said. “But when we reviewed the plans we realised that the engine had evolved over years of manufacture. So we took the engine to pieces and scanned the components. Then we printed two copies.” The research initiative was supported by additional funding from the Science Industry Endowment Fund (SIEF). This fund invests in scientific research that is in Australia’s long-term national interests. The fund specifically seeks to support collaborative links between science, research and tertiary organisations. Knowledge and ideas for the next generation of thinkers and leaders is at the core of SIEF. In addition, Amaero Engineering— one of Monash University’s partner organisations—has made the technology available to Australian industry representatives. “The project is a spectacular proof of concept that’s leading to significant contracts with aerospace companies. It was a challenge for the team and pushed the technology to new heights of success—no one has printed an entire engine commercially yet,” said Ben Batagol from Amaero Engineering. Australia’s manufacturing sector relies on strong research partnerships to bring the latest technology to life and remain competitive on a global scale. The research is part is part of a larger integrated group of facilities that are used for Australian research. Researchers are encouraged to share their ideas and connect with other industry thinkers to bring out-of-thisworld ideas to life.