
39 minute read
News
GCC AGRI-NUTRIENTS FEED 5% OF WORLD’S POPULATION, FINDS NEW GPCA REPORT
The GCC agri-nutrients industry supports the food supply of 5% of the world’s population, or 350 million people across the globe, according to a new report published by the Gulf Petrochemicals and Chemicals Association (GPCA). This figure marks the rising importance of agri-nutrients in enhancing global food security in a rapidly changing world, where we will need to produce 70% to 100% more food by 2050 to feed our growing population.
Advertisement
The findings were highlighted in a new report entitled ‘Role of Agri-Nutrients in Food Security’ released on the occasion of World Food Day organized by the UN. The report further reveals that over the last five decades, a portion of the global population supported by agri-nutrients manufactured by GCC producers has increased 33 times, from about 9 million in 1970 to 350 million currently.
The GCC agri-nutrient industry supports about 12,100 direct jobs in the region, and almost three times as many indirect and induced jobs, which means that every person working in the sector supports enough food production to feed about 30,000 people worldwide, including people in the GCC. Additionally, every person employed by the regional industry supports 17.7 tons of three main crops production per year (rice, wheat and maize), underlying the significance of the Arabian Gulf region in supporting global food security.
The COVID-19 pandemic has put food security and the nutrition of millions of people under threat, with many of the affected populations already suffering from malnutrition. According to the Food and Agriculture Organization (FAO) of the United Nations, the number of people joining the ranks of those suffering from malnutrition post the pandemic may range from 14.4 million to 38.2, or even 80.3 million depending on the GDP contraction.
The role of agri-nutrients during the pandemic has been essential in meeting the needs of billions of people across the globe and ensuring the uninterrupted supply of nutrition to the world’s population.
In the midst of the coronavirus crisis, production of agricultural chemicals
including fertilizers and crop protection chemicals declined by 5% between January and May 2020 globally. Furthermore, capacity utilization reduced from 81.5% in January to 75.1% in May 2020. Comparatively, in the GCC, fertilizer producers continued to produce essential fertilizers and supply their global customers without significant production and supply chain disruptions.
ABU DHABI’S AGTECH ECOSYSTEM EXPANDS ACROSS LAND, SEA AND SPACE
Three innovative agriculture companies will develop cutting-edge projects in Abu Dhabi to boost the emirate’s agriculture technology (AgTech) capabilities across land, sea and space. The Abu Dhabi Investment Office (ADIO) announced individual partnerships with Pure Harvest Smart Farms (Pure Harvest), FreshToHome and Nanoracks that will see the companies receive financial and non-financial incentives totalling AED 152 million (USD 41 million). The research and technologies developed by these companies will expand existing capabilities in Abu Dhabi’s AgTech ecosystem and promote innovation in the sector to address global food security challenges.
The new partnerships are a continuation of ADIO’s efforts to accelerate the growth of Abu Dhabi’s AgTech ecosystem through the AgTech Incentive Programme, which was established under Ghadan 21, Abu Dhabi’s accelerator programme. The Programme is open to both local and international AgTech companies. The partnerships follow ADIO’s AED 367 million (USD 100 million) investment earlier this year to bring four AgTech pioneers – AeroFarms, Madar Farms, RNZ and Responsive Drip Irrigation (RDI) – to the emirate to develop next generation agriculture solutions in arid and desert climates.
H.E. Dr. Tariq Bin Hendi, Director General of ADIO, said: “Abu Dhabi is pressing ahead at full steam with our mission to ‘turn the desert green’ and solve longterm global food security issues. We have created an environment where innovative ideas can flourish and this has enabled the rapid expansion of our AgTech sector. Innovations from the companies we partnered with earlier this year are already propelling the growth of Abu Dhabi’s 24,000 farms. Partnering with Pure Harvest, FreshToHome and Nanoracks adds a realm of new capabilities to the ecosystem across land, sea and space.”
Bin Hendi continued: “We are driving innovation across the entire agriculture value chain and this is producing a compounding effect that is benefiting farmers, innovators and companies in our region and beyond.” Pure Harvest, FreshToHome and Nanoracks have been awarded financial and nonGuiding theme 2021: ”Farming in the food chain“
The world’s leading trade fair
> Almost 155.000 highly qualified visitors, interested in new technologies for dairy, poultry and aquaculture
> 2,600 international exhibitors on more than 260,000 m² exhibition floor space
> The complete programme for animal production – breeding, feeding, housing, processing and marketing
> Leading technologies for renewable energies and decentralized energy supply
9 – 12 February 2021 Hanover, Germany
Hotline: +49 69 24788-265 | expo@DLG.org www.eurotier.com | facebook.com/eurotier
including
financial incentives to expand operations in Abu Dhabi. The competitive incentive packages include rebates on innovation-linked high-skilled payroll, high-tech CAPEX, as well as land, utility and intellectual property support. Since the beginning of 2020, ADIO has attracted seven AgTech companies to Abu Dhabi, each bringing a complementary skill to expand the ecosystem. ADIO’s new partnerships with Pure Harvest, FreshToHome and Nanoracks will build on the achievements made by AeroFarms, Madar Farms, RNZ and RDI, the AgTech pioneers ADIO partnered with earlier this year to establish R&D and production facilities in Abu Dhabi.
LOUIS DREYFUS COMPANY TO ENTER INTO STRATEGIC PARTNERSHIP WITH ADQ
Louis Dreyfus Company Holdings B.V. (LDCH) announced that the Group has signed an agreement to sell an indirect 45% equity stake in Louis Dreyfus Company B.V. (LDC) to ADQ, a large holding company based in Abu Dhabi. As part of this transaction, LDC has also signed a longterm commercial supply agreement with ADQ for the sale of agri-commodities to the United Arab Emirates (UAE).
“The transaction announced constitutes a milestone in a decade-long strategy envisioned by the Supervisory Board, which started with the consolidation of LDC’s parent company’s shareholding,” said Margarita Louis-Dreyfus, Chairperson of the Supervisory Board of LDCH. “We are delighted to welcome ADQ to our shareholder group as longterm partners and investors, with a common vision for LDC’s future, and experience that will bring further value to the business and support the Group’s ambitions.”
ADQ’s broad portfolio of major enterprises spans multiple sectors, among them food and agriculture. As part of its strategy for the sector, the company seeks to generate financial returns and strengthen the economic cluster in the UAE.
“As one of the world’s leading agri-commodities and food companies, LDC represents a strategic investment opportunity for ADQ, in line with our long-term food and agriculture investment strategy. We share LDC’s vision for future growth of the business, and look forward to partnering with LDC’s existing shareholders and management team to capitalize on the sector’s emerging opportunities, by accelerating LDC’s transformative growth strategy to move towards greater value chain integration - from producers to consumers,” said H.E. Mohamed Hassan Alsuwaidi, ADQ’s CEO.
Upon completion of the transaction, a portion of the proceeds of the sale amounting to a minimum of US$800 million will be invested into LDC to support the pursuit of the company’s long-term business plan and strategy, including the acceleration of strategic investments.
“Our strategy aims to
EGGSCARGOSYSTEM® INTRODUCES NEW PALLET
GI-OVO is expanding its EggsCargoSystem® with a new pallet. This concerns the EC Pallet Closed Deck which GI-OVO sees as a logical addition to the existing pallets with an open top deck. Especially in situations where eggs with a bad shell are transported, this new pallet can be of excellent service. After all, the closed top deck prevents contamination of the truck and the floors. The EC Pallet Closed Deck can be provided with a so-called logo print on both sides. The pallet can also be placed in racks without having to be provided with steel reinforcement.
For more information, visit www.gi-ovo.com

leverage global consumption trends through investments in new business opportunities, as the company embraces more of the agricultural value chain to become an increasingly integrated food, feed, fibers and ingredients company,” said Michael Gelchie, LDC’s Group CEO. “With a shared ambition for investment in innovations and technologies that can transform food and agricultural production, the investment potential created by the long-term partnership with ADQ brings additional strength to the pursuit of LDC’s strategic growth plans, building on the strong performance delivered in the first half of 2020.”
LDC remains focused on putting its strategy into action, while fulfilling its key role to keep essential food and feed supply chains moving, helping to ensure global access to food.
“LDC will continue to leverage its core historic capabilities to efficiently analyze and capture opportunities in a rapidly changing context, while pursuing our vision to shape resilient food supply chains, guided by our purpose to create fair and sustainable value for the benefit of current and future generations,” added Margarita Louis-Dreyfus. “As we embark on the next stage of LDC’s development, we look forward to working with ADQ toward the realization of that shared vision.”
MOSCOW STUDENTS DEVELOP A ROBOT TO DIAGNOSE PLANT DISEASES
Students from Moscow universities have presented a mobile robotic platform at Robofest, which identifies plant disease hotspots at an early stage and reduces the risk of crop loss. Robofest is Europe’s largest technology competition and festival. This year it is held online between 26 October and 1 November.
The robotic platform, developed by a team of Robofest participants aged 18 to 20, analyses the condition of plants by taking photographs of them. The photos are then uploaded to a special server, where the neural network processes the images of plants and classifies them by disease. Farmers then receive information from a chat room bot about the location of the disease hotspot and the problems’ cause as well as recommendations on how to treat infected plants.
The platform presented at Robofest identifies fungal diseases and microelement deficiency in plants. Diseases can be eliminated locally, so farmers will not have to cultivate the entire field, but only 10-15% of it. This will reduce costs for medicines, herbicides and fertilisers.
The robot's size is 172 by 172 centimetres. It can work for up to 16 hours without recharging. The device has already passed field tests in pilot fields at the Timiryazev Academy and has shown good results. The project won prizes in the Engineering Project and the Agroindustrial
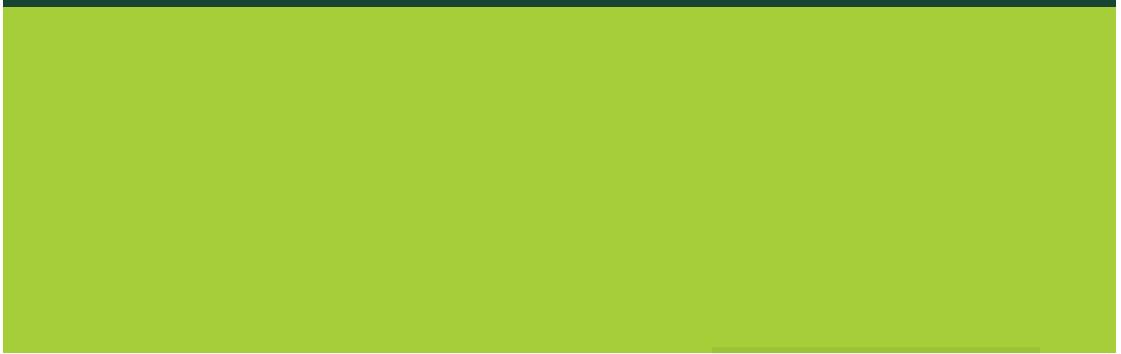

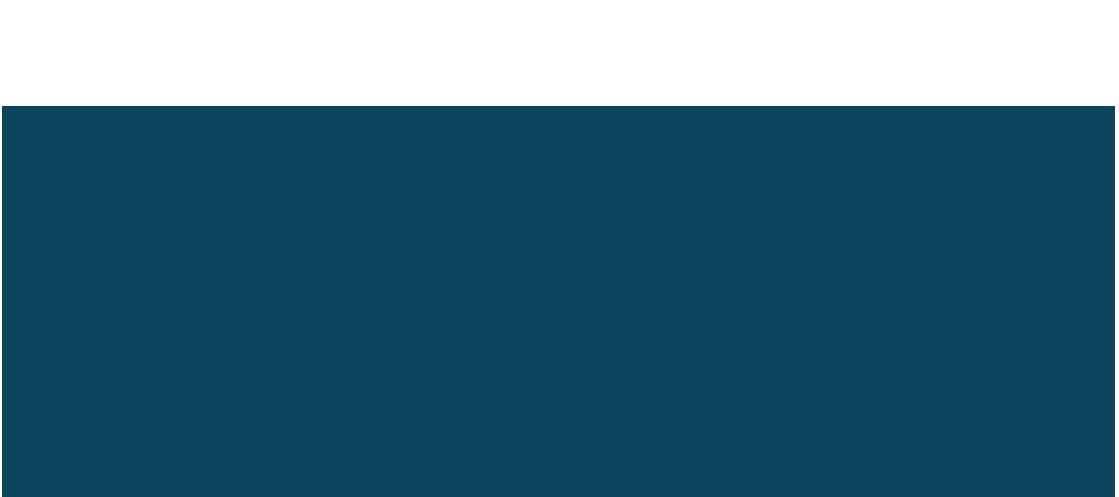
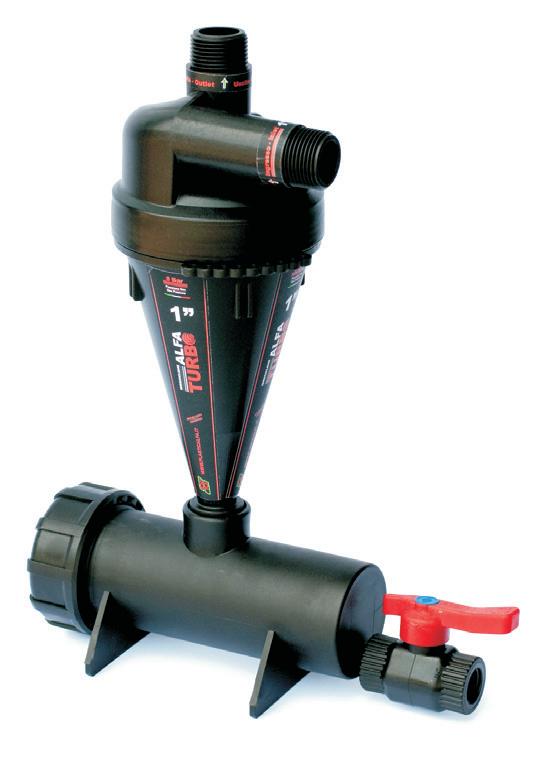

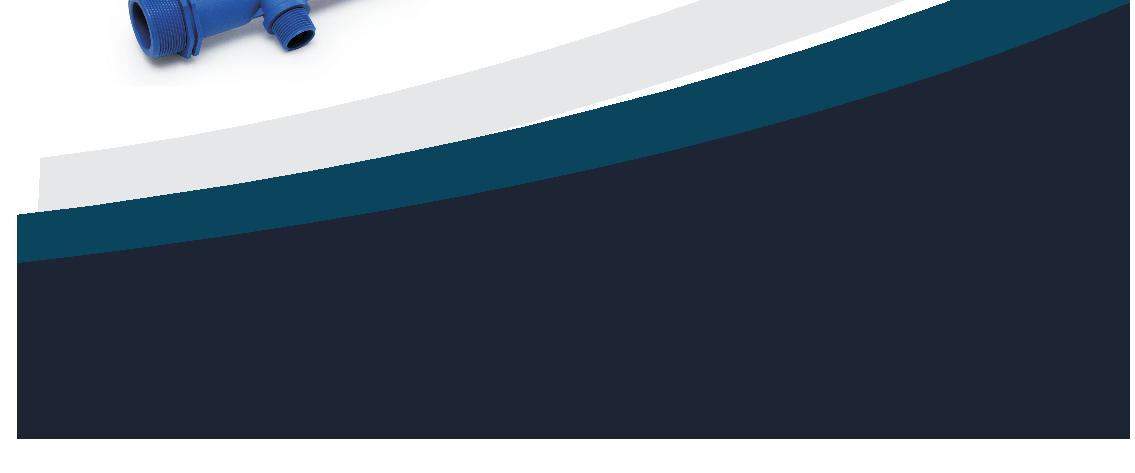

Complex divisions of the Robofest.
The robot received the highest accolade from the jury and experts of the Robofest. Among experts were representatives of Progress Agro – an agricultural holding based in the South of Russia – who expressed interest in testing the technology.
The world loses USD 75 billion worth of harvest each year due to late processing. Wide-scale use of the robot presented at the Robofest could significantly improve the situation, cut costs for farmers and increase crop yield.
Robofest is the largest technology festival for young people in Europe and one of the biggest in the world. This year Robofest is held online for the first time. A competition area has been set up in Moscow, with participants from all over Russia connecting to take part remotely. Challenges for the competition are developed by the largest industrial enterprises based on real needs.
You can follow the online broadcast of XII Robofest and communicate with participants and guests of the festival, as well as view the programme at http://online.robofest.ru/.
FARMLANDFINDER LAUNCHES OFFERS PLATFORM
FarmlandFinder Inc, a technology provider that helps farmland companies and lending institutions digitize farmland transactions, launches the first online marketplace for farmland.
Now at FarmlandFinder.com landowners are able to buy and sell farmland, entirely online. “Farmland is a highly fragmented and opaque market,” says Steven Brockshus, Founder and CEO of FarmlandFinder. “There are more absentee landowners today than ever before, farmers are looking for optionality when it comes to expanding their land base and getting access to reliable information about the farmland market is difficult. We’ve seen books, cars and houses start to transact online… why not farmland?”
Through the FarmlandFinder Offers Platform, a landowner can request an offer on their land and receive offers from a private network of verified buyers in as little as a week. Once an offer is accepted, FarmlandFinder helps to navigate the rest of the process to ensure a seamless and stress-free transaction.
“Farmland is the foundation for 5% of America’s annual GDP,” says Amanda DonohueHansen, Managing Director at Cultivian Sandbox and FarmlandFinder Board Member. “Farmland is valued in excess of $2.5 trillion with a staggering 10% -- $250 billion - transferring hands in the past 5 years, most of it offline and private. Even more of America’s farmland is projected to change hands in the coming years with generational turnover and growing interest in farmland as a financial and environmental investment.”
By digitizing the farmland transaction process, FarmlandFinder Offers can provide unique optionality to expanding farmers. Not only can they privately buy farms through the platform, but they can also expand their land base without taking on additional debt by partnering with an investor through the FarmlandFinder buyer network. This decreases the barrier of entry for beginning farmers and creates optionality for seasoned growers who are looking for unique ways to strengthen their balance sheets.
“At Cultivian Sandbox, we believe that if there was ever a time for a digital revolution in farmland, the time is now and FarmlandFinder is its pioneer platform,” says DonohueHansen. “We align with FarmlandFinder’s values to make farmland real estate transparent and accessible to all. We’re proud to support its launch of the Offers Platform to make farmland sales simple, instant and online.”
COVENTRY UNIVERSITY RESEARCH IDENTIFIES WHAT’S HOLDING THE UK BACK IN THE MOVE TO PEAT-FREE HORTICULTURE
A new report from Coventry University has assessed the UK’s progress towards peatfree horticulture and identified what factors are holding back further progression.
Protecting peat bogs is not just a matter of protecting wild habitats, peatlands are also key to the prevention of global warming as they store a lot of carbon. By harvesting peat and disturbing or destroying this land, harmful gasses are released into the atmosphere.
However, because of its water-retaining properties and consistency, peat is a popular growing media for professional horticulturists and casual gardeners alike.
In line with global targets of the United Nations (UN) Paris Agreement and UN Sustainable Development Goals, the UK government is pressing for significant reductions in the amount of peat used for
commercial and domestic horticultural purposes. However, Coventry University researchers have been investigating exactly what has changed in the last decade, in terms of the availability and usage of alternatives to peat, to identify the opportunities and barriers to further increases in the uptake of peat-free products.
The report illustrates how progress towards the government’s targets has fallen short, with peat currently constituting around 50 per cent of all growing media by volume, down from 70 per cent in 2009.
Dr David Bek, Co-Lead for the Sustainable Production and Consumption research theme in the Centre for Business in Society, said: “Early efforts to promote peatfree alternatives were hindered by the inconsistency and poor quality of products, which had long term impacts on consumer perceptions. However, considerable research and trialling has transformed the quality of alternative mixes to the extent that these can successfully match the performance of peat-based products.”
The report concludes with a set of recommendations for continuing the drive towards meeting the targets set by the UK government and ensuring that all growing media can be justifiably labelled as ‘responsibly sourced’, including: • Continuing the research and development of peat free

Agritentech_131X182.qxp_Mise en page 1 25/11/2020 12:21 Page1 alternatives. • Continued technology and knowledge transfer with commercial growers to increase confidence in, and use of, peat-free media. • The development of clear messaging around the environmental impacts to communicate with the public how they can make positive choices concerning growing media.

POULTRY INDUSTRY ACCESSES COBB RESOURCES MORE THAN 30,000 TIMES GLOBALLY
Cobb continues its tradition of providing tools and expertise to help the poultry industry succeed. In only

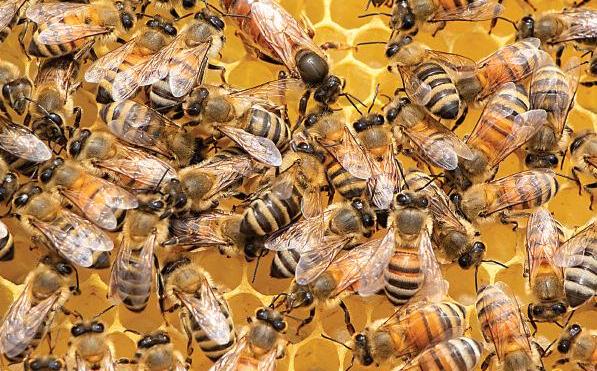
100% ORGANIC
To the attention of all farmers and breeders! Are you looking for both yields and security of natural and organic production?

AGRITENTECH is at your disposal to offer you its international expertise. Present throughout Africa and the Middle East, we have forged fruitful partnerships with leading companies in the field of technology to offer you the natural solutions of tomorrow. Our Italian partner, TENCOM, has developed a range of 100% organic soil care fertilisers that will enable you to optimise your production while respecting market constraints. As well as a range of essential oils that advantageously replace antibiotics on farms: poultry, cattle, sheep, bees...

Contact us to find out more: contact@agritentech.com
www.agritentech.com
one year, professionals world-wide accessed Cobb’s online resources more than 30,000 times. This impressive milestone includes just a snapshot of page views and downloads of topic-driven guides, videos, technical articles, white papers and more.
“At Cobb, we work hard every day to give customers the support they deserve and the guidance they need to help support the best outcomes for every single flock,” said Cody Polley, director of world tech support at Cobb-Vantress. “This impressive snapshot demonstrates the value our technical experts bring and the quality of resources Cobb shares with the industry.”
Of note, industry professionals downloaded or viewed Cobb’s management guides nearly 25,000 times within the year. The guides cover a wide-range of topics including hatchery, vaccination, brooding fundamentals, grandparent management, processing procedures, and more. They provide the latest u pdates to help deliver on Cobb’s commitment to provide customers with tools to help make quality protein accessible, healthy, and affordable worldwide.
“Customers know they can depend on us,” said Polley. “We will continue to provide them with the relevant technical expertise they deserve with these easily accessible resources available on our website and mobile application, Cobb Connection.”
LA NIÑA BEHIND UPWARD PRESSURE ON PERUVIAN MANGO PRICES
Peruvian mango exports this year are expected to drop by at least 15% compared to the previous year, even with an early start to the harvest season. The harvest season for the Mid-Year (MY) 2020-2021
NEW HOLLAND AGRICULTURE WIDENS EXTENSIVE T6 TRACTOR RANGE WITH UNIQUE 6-CYLINDER T6.160 DYNAMIC COMMAND
New Holland Agriculture extends its acclaimed all-purpose T6 tractor range with a new 6-cylinder model, the T6.160 Dynamic Command™. This unique tractor combines the high performance of the proven NEF 6-cylinder engine with New Holland’s exclusive Dual Clutch and CVT technology to deliver high efficiency and productivity. This comes in a compact package with a 2.6-metre wheelbase and 10.5 tonnes Gross Vehicle Weight.
Benjamin Davies, T6 Series Global Product Marketing Manager, explains: “New Holland has a proud legacy in this segment that started more than 30 years ago, when we launched the first compact 6-cylinder tractor on the market, the 7810. It was a true game changer, and the new T6.160 Dynamic Command builds on this rich heritage to offer farmers a compact low power Stage V 6-cylinder tractor with embedded technology for operator efficiency.”
The T6 range now offers two six-cylinder models with Dynamic Command: the existing 145-hp T6.180 and the new 135-hp T6.160 – the only compact 6-cylinder tractor on the market with rated power below 140 hp.
Christel Diebolt, Product Marketing Manager, Europe, adds: “The T6.160 Dynamic Command delivers all the benefits of the exclusive Dual Clutch technology, which made its debut in motorsports in 1980, winning races thanks to the fastest gear changes on the track. Customers will enjoy a full drive without loss of torque during the gear change at the lowest fuel consumption rate.”
The T6.160 Dynamic Command will be available in the second half of 2021.


campaign started at the end of October, which is two weeks earlier compared to the previous two seasons and expected to last until March 2021. Yet, reduced rainfalls associated with the La Niña phenomenon is causing the reservoirs not to reach the levels necessary to irrigate the plantations, especially in these key months. This is when mango plants in the area require continuous irrigation so that the fruit reaches the size demanded in the international market.
According to a Peru-based Tridge engagement manager, some companies have decided to advance harvests and shipments of the product as early as September. Additionally, Peruvian companies are allegedly trying to cope with the lack of rain and capitalise on the good prices in the international market.
A similar situation was observed just two years ago, during the 2018/19 season, when the exported volume of mango suffered a 10% drop. During this time, the lower volume caused a price increase, which reached USD 1.30 per kilogram, the highest in the five previous years. Faced with a similar scenario, Peruvian exporters expect a similar performance in prices during 2020/21.
ADM, INNOVAFEED ANNOUNCE CONSTRUCTION OF WORLD’S LARGEST INSECT PROTEIN FACILITY
ADM, one of the world’s leading human and animal nutrition providers, and InnovaFeed, the world leader in producing premium insect ingredients for animal feed, announced plans to collaborate on the construction and operation of the world’s largest insect protein production site, in Decatur, Illinois. The facility will be owned and operated by InnovaFeed and will co-locate with ADM’s Decatur corn processing complex, with ADM supplying feedstocks, waste heat and more. Together, these investments will bolster economic growth and job creation in Decatur and central Illinois while continuing to strengthen the state’s position as a center of innovative, sustainable agriculture.
“We are very pleased to launch this ambitious project, working alongside ADM and Illinois state partners as InnovaFeed expands to provide sustainable solutions to meet the fast growing demand for insect feed in the US and worldwide,” said Clement Ray, CEO and co-founder of InnovaFeed. “Around the world, InnovaFeed is contributing to the emergence of sustainable food systems by developing a pioneering and sustainable industry. Our new operations in Illinois, a global leader and destination for agriculture, will allow us to take the next steps to innovate and grow our business.”
“At a time when the demand for animal feed protein is steadily increasing, insect farming stands out as a true solution for the future,” said Chris Cuddy, ADM senior vice president and president of the company’s Carbohydrate Solutions business. “We’re excited to work with InnovaFeed on this ambitious project, which further expands our participation in the growing market for animal food and feed that comes from responsible, sustainable sources. It’s a great demonstration of how ADM is expanding its value chain by offering opportunities for collaboration to leading, innovative startups. It’s yet another example of how we’re constantly identifying new ways to create value from corn, oilseeds and more. And of course, we’re extremely proud that we can help bring this new, job-creating project to Decatur, the home of our North American headquarters.”
Insect feed has become an increasingly popular protein ingredient for the agriculture and aquaculture industries, as demand for animal feed has now reached an all-time high and consumers look for food that is sustainably and responsibly grown. InnovaFeed already operates two insect production facilities in France, including what is today the world’s largest. The Decatur facility represents InnovaFeed’s first international project.
DIGITAL AG GIVES FARM MANAGERS A COMPETITIVE EDGE
Farmers Edge™, a global leader in digital agriculture, and Farmers National Company (FNC), the nation's largest landowner services company, announced a partnership to help boost crop production and establish longterm land value across leased acres. The partnership equips landowners and operators with access to a wealth of digital and agronomic resources designed to support daily operations, improve sustainability, and create a seamless digital connection between stakeholders.
In October, FNC reported
land is selling at near-record levels; the company and its agents actively marketed and sold farmland worth US$2 billion over the last five years. This increase in prices and competition has put more pressure on landowners, operators, and investors to ensure quality conservation and management for current income and future economic value. Farmers Edge solutions bridge the gap between stakeholders to establish more transparency and trust. The company’s high-tech tools are powered by robust, field-centric data sets and Artificial Intelligence to help collect, curate, and execute on farm data quickly, resulting in better control of disease, improved soil fertility, and increased yields. Stakeholders gain an acute view of field activities, crop performance, and management practices verifying sustainability commitments and conservation measures on the farm. "Leasing land is a highstakes investment for everyone involved," says Wade Barnes, Farmers Edge CEO and co-founder. "Landowners want to ensure their assets are protected for generations to come, and operators need to be able to demonstrate their commitment to the land while also turning a profit. By working together with FNC, we're equipping their clients with innovative solutions that improve land value while also bringing a new level of connectivity and decisionsupport for sustainable crop production. Digital agriculture is reshaping the industry, and farm real estate is no exception; I predict we will see a significant shift in the importance it plays in operator selection, conservation requirements, and land prices in years to come." "At Farmers National Company, we're committed to providing landowners and their operators with the highest level of service and support to get the most value from farmland," says David Englund, AFM, FNC President and CEO. "It's a competitive market, and this partnership provides our farm managers with the tools they need to ensure they're making the best possible decisions for each client's land in the most sustainable, cost-effective way. With direct connectivity to the farm, we can provide our clients with a clear understanding of productivity, yield potential, management practices, and operational challenges to support real estate and rental decisions."
CARGILL PARTNERS WITH BINSENTRY TO HELP ANIMAL PRODUCERS AND FEED MILLS ACCURATELY AND SAFELY TRACK FEED INVENTORY
Hitting the side of a feed bin with a mallet, using load scales or installing vibration sensors to guestimate feed levels is a thing of the past. To make feed bin monitoring safer and more efficient for animal producers and feed mills, Cargill is now an exclusive distributor of BinSentry, an easy-to-install feed management solution that accurately tracks feed inventory.
Sensors from BinSentry use LiDAR sensors, the same advanced technology used in self-driving cars, to read bins every four hours. BinSentry installs in 10 minutes or less, requires no bin modification and is solar/battery powered. It also has self-cleaning sensors that wipe dust before each reading to ensure better accuracy. Users can confirm the correct feed is in their bins with an easy to use dashboard that they can view on any mobile device or computer.
“Integrating BinSentry sensors with our Cargill Nutrition Cloud Platform helps animal producers, feed mills and their customers get the right feed for specific animal groupings in their operations,” said Scott Ainslie, Cargill’s regional managing director of animal nutrition. “This also opens up opportunities for truck route optimization and better production scheduling in feed mills.”
BinSentry leverages lowpower, long-range networks such as NB-IoT and LTE-M, so even remotely located feed bins can be monitored, regardless of whether internet connectivity is available. Feed mills can plan delivery routes more efficiently and can ensure that farmers have the right amount of feed when they need it. Other benefits include fewer costly ordering errors, reduction in late or unexpected feed orders and increased safety by eliminating the need for producers or feed mill employees to climb into a bin to check inventory levels. With BinSentry, Cargill customers get intuitive software that provides powerful on-farm insights.
“BinSentry is proud to partner with Cargill to eliminate costly inefficiencies and enhance operational sustainability for those working hard to feed the world,” said BinSentry CEO Randall Schwartzentruber. “Together, our relentless
pursuit of agricultural innovation combined with Cargill’s feed expertise and extensive supply chain footprint will allow us to scale our solution quickly, helping producers and feed mill operators be more successful.”
UAE’S 20BY2020 INITIATIVE BRINGS LIFE-CHANGING WATER SOLUTION TO THOUSANDS IN CAMBODIAN VILLAGES
Thousands of people across three Cambodian villages can now live safer, healthier lives following the deployment of new water purifying technology as part of the Zayed Sustainability Prize’s UAE-driven humanitarian initiative, 20by2020.
After the most recent installation of solar powered light systems in vulnerable communities in Egypt and Jordan, the initiative has progressed with five water fountains, benefiting the 4,400 residents of the Chhnok Trou, Kampong Phrah and Ses Salab villages.
Due to the instalment of the water ultra-filtration solution, organised by the 20by2020 initiative, the village communities, along with the Chhnok Trou school and clinic, have access to clean and safe water for the first time. Not only does this gives residents an option for avoiding many of the waterborne diseases and other health issues stemming from dirty water, it will offer new opportunities for better hygiene, an essential requirement given the importance of handwashing in preventing the spread of coronavirus.
Over time it is intended that
BOSCH AND BASF ESTABLISH JOINT VENTURE FOR DIGITAL TECHNOLOGIES IN THE AGRICULTURAL SECTOR
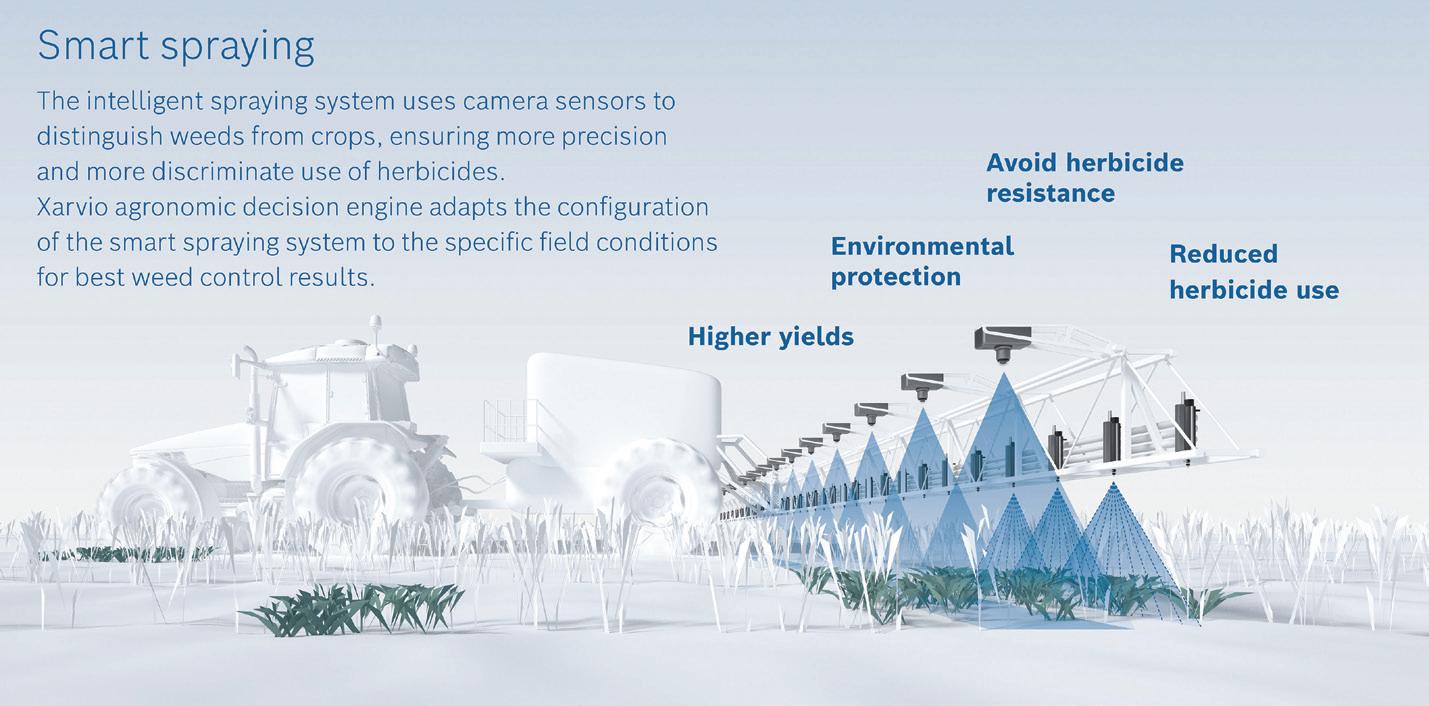
Bosch and BASF Digital Farming have signed a 50:50 joint venture (JV) agreement to globally market and sell smart farming solutions from a single source in the future. The JV agreement was signed on November 10, 2020 and will be followed by the founding of a new company based in Cologne, which will be established in the first quarter of 2021. The foundation is subject to the approval of the relevant antitrust authorities. Both parties have agreed not to disclose financial details.
Bosch brings to the JV significant capability in hardware and software, as well as digital services for planning and decision making in field crops. BASF Digital Farming with its xarvio™ Digital Farming Solutions provides an automated, real-time, field specific agronomic decisionmaking engine for weed management that is powered by the digital xarvio platform for crop optimization. It provides farmers with field zone specific advice on how to produce crops in the most sustainable way. Combining the expertise of both companies, with state-of-the-art hardware and software solutions, will make it easier and more convenient for farmers to benefit from digital solutions.
The first two products to be launched will be a version of the Intelligent Planting Solution (IPS) system, with enhanced digital intelligence for seeding and fertilizer prescriptions, and Smart Spraying. The Smart Spraying solution combines Bosch’s camera sensor technology and software with xarvio’ s crop optimization platform. Both products have been tested extensively in real growing conditions. Such innovative precision farming practices enable resource efficiencies supporting farmers and the environment.
Depending on the local conditions this may lead to a reduced need for crop protection products in specific applications. Smart Spraying shows up to 70 % herbicide volumes reduction in experimental stage. The solution is expected to be launched with a limited number of machines in 2021.
this access will improve the outlooks for residents through better hydration and the prevention of illness, which has been statistically proven to have significant, positive effects on the overall health and wellbeing of communities alongside individual growth and development.
20by2020’s support has seen yet another community benefit from life-saving technology. In Cambodia, the solution deployed has been developed by Safe Water Cube, a French company that was a Zayed Sustainability Prize finalist in 2019 under the Water Category. The technology deployment in Cambodia makes surface water drinkable (river, pond) by removing viruses and bacteria that cause diarrhoea, dysentery, cholera and hepatitis, from up to 1,000 litres of water per hour with no energy or maintenance required, and no chemicals used.
SYNGENTA GROUP ACQUIRES LEADING BIOLOGICALS COMPANY, VALAGRO
Syngenta Group announces the acquisition of Valagro, a leading Biologicals company, by its business unit Syngenta Crop Protection. The investment
BAYER HELPING TRANSFORM THE FOOD SYSTEM THROUGH INNOVATION IN AGRICULTURE
As part of the company’s Future of Farming Dialogue virtual event series, Liam Condon, President of the Crop Science division of Bayer, emphasized the importance of the company’s sustainability commitments it set in 2019. Condon addressed how the impact of COVID-19 and the resulting economic instability reinforced the need to intensify the focus on agricultural innovation and help make agriculture part of the solution to climate change, while continuing to ensure food security for all.
“The agricultural industry is no stranger to adversity – from flooding to drought to pest infestations – and COVID-19 is yet another stark reminder of the need to create a more sustainable and resilient food system to ensure food security,” said Condon. “Innovation, science and collaboration are key to not only solving the pandemic but also necessary in agriculture to solve the present and future challenges facing farmers.”
The Future of Farming Dialogue features a variety of internationally renowned speakers and stakeholders from academia, industry and media. The focus of discussion is how to build more resilient food systems, accelerate sustainable-driven innovations and develop new business models that can reward farmers for their services to the ecosystem.
Condon commented on Bayer’s sustainability commitments: “Especially in challenging times, it’s our responsibility to help ensure food security and reduce our environmental footprint. We also need to help farmers do the same by providing the products, services and technologies needed to produce enough food while using less resources and caring for the environment. The key to this is innovation and this is what we continue to drive forward.”
To underscore this, the company recently launched products and initiatives that highlight its commitment to agricultural innovation and digitalization, critical levers in driving a more sustainable food system. This includes: • An industry-first, externally developed model that can measure the environmental impact of any crop protection product in any crop around the world. So far, the company has used this model to screen its entire portfolio and its uses around the world to understand the sustainability implications. • The launch of the Bayer Carbon Initiative to help growers generate revenue for adopting specific climate-smart practices. Bayer is paving the way towards a carbonzero future for agriculture through this innovative, science-based and collaborative pilot program with the potential to deliver unmatched value to many more farmers through expansion in the U.S. and Brazil and other world regions. • The recent introduction of a new short stature corn product in Mexico, known as VITALA. The VITALA system consists of a new hybrid maize and best practices in agronomy to help farmers in Mexico grow more using less resources. Bayer is continuing to research and conduct trials with the goal of introducing region-specific varieties in other markets that will allow farmers around the world to experience the same benefits. • The ‘Better Life Farming Alliance’, an initiative led by Bayer to empower smallholder farming communities. Together with partners, this alliance provides, know-how, inputs, financial solutions and market access to them.

positions Syngenta Crop Protection as one of the key global companies poised to shape the rapidly growing Biologicals market, which is set to nearly double in size over the next five years. Valagro will continue to operate as an independent brand in the market within the Syngenta Crop Protection business.
Valagro is a market-leading producer of innovative Biologicals, with a ~10% CAGR from 2009-2019 and an approximate revenue of $175m in 2019. The company has excelled by harnessing the power of nature to provide innovative and effective solutions for plant nutrition and care. With 40 years of experience, it offers its customers a comprehensive crop portfolio in Biologicals with a market-leading position in biostimulants and speciality nutrients. Headquartered in Atessa, Italy, Valagro serves customers around the world with a strong presence in Europe and North America, as well as a growing footprint in Asia, including China, and LATAM. Valagro has over 700 employees, 13 subsidiaries and 8 production sites around the world, with a portfolio backed by best-in-class biological R&D, production and commercialization capabilities.
This strategic acquisition enables Syngenta Crop Protection to build a worldleading Biologicals business. Valagro has a strong commercial and production standing, as well as an industry-leading technology and research capacity. Valagro's well-established portfolio in biostimulants and specialty nutrients will complement both Syngenta Crop Protection's current range of biostimulants and biocontrols, as well as its future pipeline of biological solutions. Biocontrols and biostimulants, natural solutions for pest, disease control and crop improvement, are increasingly important for farmers worldwide in their efforts for sustainable agricultural production. This acquisition is fully in-line with Syngenta Crop Protection’s strategy to provide growers with additional complementary choices of products and technologies in order to effectively and sustainably care for their crops by managing resistance, enhancing soil health, reducing residues in crops, and addressing consumer demands.
Erik Fyrwald, CEO of Syngenta Group stated: “We are looking forward to welcoming the Valagro team to Syngenta Group. This acquisition underlines our growth ambitions in this area and positions us as one of the strongest players in the global biologicals market. The investment also forms part of our $2 billion commitment to help farmers address the effects of climate change and improve agricultural sustainability as part of our Good Growth Plan.”
TOP QUALITY LISIANTHUS WITH HYBRID LIGHTING INSTALLATION FROM SIGNIFY AT LUGT LISIANTHUS
Lugt Lisianthus achieves the best quality and a longer shelf life for its lisianthus using a hybrid light installation with LED grow lights from Signify the world leader in lighting (Euronext: LIGHT). With a combination of HPS and 25% LED lights with a light level of 364 µmol/m2/s on 5.8 hectares in Monster, the Netherlands, Lugt Lisianthus is able to grow more flowers and firmer stems with a shelf life of 14 days.
“We chose Signify because of the quality and reliability they provide. In addition, we believe that the Philips GreenPower LED is the most beautiful fixture. It is compact and also offers a long service life," says Marcel van der Lugt of Lugt Lisianthus.
Lugt Lisianthus is a family business that is celebrating its 100th anniversary this year. Originally producing vegetables and later freesias, the company has been growing lisianthus since 1992. In recent years, Lugt Lisianthus has successfully worked to improve the image and quality of the lisianthus. “Where we used to be able to grow 5 flowers per branch, we are now at 15 flowers per branch. We have also been able to shorten the cultivation period to 8 weeks and have almost doubled the shelf life to 14 days,” says Van der Lugt.
Lugt Lisianthus represents the best that ornamental floriculture has to offer. The most beautiful flowers, the strongest stems, and the highest number of buds per stem. The company is the first to cultivate Lisianthus according to Next Generation Growing (Dutch: "Het Nieuwe Telen"). In winter, the air in the greenhouse is refreshed and brought up to temperature with outside air, reducing humidity and keeping the crop more active. As a result, the climate in the greenhouse remains the same all year round. Growing Lisianthus
requires a lot of energy, but with Next Generation Growing, Lugt Lisianthus tries to be as sustainable as possible. Lugt Lisiantus chose the Philips GreenPower LEDs, which give less radiant heat, use 40% less energy and have a payback time of 5 years.
PRIVA’S OPEN PLATFORM TAKES CROP CONTROL TO THE NEXT LEVEL
Priva is going to change the way growers manage their crops. The company’s new open platform, based on new and exciting technologies such as cloud technology, seamlessly connects every aspect of the growing process. A suite of online applications and services makes it easier to grow a profitable crop, even autonomously.
NEW SEASON OF ‘COMMUNITY FARM’ AT DUBAI SILICON OASIS
Dubai Silicon Oasis Authority (DSOA), the regulatory body of Dubai Silicon Oasis (DSO), an integrated free zone technology park, announced the commencement of this year’s community farm. The farm, providing DSO residents with a total area of 8,000 square meters, aims to instill sustainability values and encourage environmentally friendly practices.
The community farm introduces families living in DSO to the standards of organic farming and drip irrigation, enhances biodiversity, raises awareness on food security through providing residents with 400 plots in a bid to test the sustainable organic community farming model, in a useful and enjoyable experience.
DSOA provides fertilized soil and smart irrigation for the project at regular intervals twice per day, as well as supports the farmers in combating common agricultural pests in environmentally friendly ways by adopting world-class technologies. Children will have the chance to spend enjoyable hours learning the values of manual labor, environmental protection and explore new applications and technologies that support sustainability.
Engineer Khalil Odeh Shalan, Senior Vice President of Operations and Facilities at DSOA, said: “In line with the DSOA Strategy, the community farm initiative at DSO strengthens bonds among community members, and instills the values of sustainability in the younger generation. The farm also helps the youth in learning about the values of cooperation, as well as preservation of the environment and natural resources.”
Shalan emphasized DSOA’s commitment in following strict precautionary measures to protect the community from the spread of the coronavirus.
Shalan commended the massive turnout by DSO residents to participate this year, as the farm welcomed more than 1000 participants from different nationalities. The community farm this year will include a friendly competition between participants to win the titles of Best Plot and Best Organic Products.
The community farm aids the community in leading a selfsufficient lifestyle, as they can grow multiple types of vegetables and plants that are consumed almost daily during the agricultural season.
Green spaces in DSO, including the Community Farm, public parks, green roofs, and interior vertical gardens, cover 1.2 million square meters, in addition to the jogging and cycling paths, urban beautification and open public spaces, that welcomes residents, visitors and employees alike.
DSOA’s has obtained a series of certifications, 4 LEED Platinum and 1 LEED Earth, for sustainable green buildings that span over 4,000 square meters, 3,000 square meters of green roofs, and 100 square meters of green walls.
The centralized smart irrigation system, controlled through the wireless networks across DSO, saves more than half a million dirhams in yearly operational costs. The hybrid solar irrigation system analyzes the weather to calculate how much water needs to be dripped across its 100,000-squaremeter subsurface irrigation network. This effectively reduces the amount of water that is evaporated by the sun’s heat, saving up to 55 percent of irrigation water.

As soon as growers connect their greenhouses to the platform, they can start using online applications and services and manage their crops from anywhere, at any time. Anomalies are detected automatically and comparing crops by variety, greenhouse and geographic locations is becoming reality. The open platform enables growers to have crystal clear insight in their key processes and steers them timely and precisely.
The Priva Open Platform is not just a new product. It is the foundation of a new way of working. And the best thing is, growers don’t need to make investments to get started. All they need is a subscription. Priva process computers are already prepared to connect with the platform.
The internet of things, cloud services, data science, artificial intelligence and robotics. In the past five years Priva has invested heavily in these technologies and built a future proof platform based on Microsoft Azure cloud technology. To help growers worldwide with any challenge they may have, Priva connects products and services of partners to the open platform. The first online applications and services are available, and this is just the beginning.
Plantonomy is Priva’s unique technology for autonomous growing. It can steer crops according to the natural biorhythm of the plant. Meiny Prins (CEO of Priva): “Plantonomy is not a trial or a challenge. The application is already cultivating many hectares autonomously within large production greenhouses in Mexico, the UK, The Netherlands, the US and Australia.” Plantonomy is
FARNEK TO CREATE EXTENSIVE ROOFTOP VERTICAL GARDEN AT NEW DUBAI STAFF ACCOMMODATION CENTRE
Leading UAE-based smart and green facilities management (FM) company Farnek, has signed a contract with Dutch green-tech projects specialist developer Urban Ponics, to design and help create a 240sqm rooftop vertical garden at Farnek’s brand new staff accommodation centre in Dubai South – Farnek Village.
Dominating the rooftop garden will be a 200sqm ‘shade house’, a structure which provides a mix of shade and light to create suitable conditions for shadeloving plants. Urban Ponics will transport this in parts from Holland to Dubai and together with Farnek’s in-house engineering team, assemble the metal tube framework for the 3m high structure onsite. It will come complete with shade netting, grow pods, lava buckets, misters, pumps, water tanks, irrigation and drainage pipes.
Farnek decided to embrace this novel concept, not only to repurpose the bare concreted space on the Village roof, but to grow fresh vegetables and other produce for its 5,000 staff, living at the AED 200 million complex.
“Farnek is an innovative sustainable company and we are always trying to identify new ways of managing our business in a cost and energy-efficient manner. Farnek Village will soon be home to thousands of our employees and we wanted to create a project that would be symbolic of our purpose and our values.
“Due to its sustainable design, space is at a premium in the Village and this initiative makes perfect use of an aspect that is generally under utilised at best and completely ignored at worst,” said Markus Oberlin, CEO, Farnek.
The garden, which will be complete in midJanuary 2021, will be used to produce over 3,000 leafy greens such as lettuce, kale, and spinach, as well as tomatoes, cucumbers, eggplants, capsicums and chillis. The first harvest should be ready in around six weeks from seeding and will be used in Farnek’s own kitchens and promises to be cleaner, tastier and more nutritious, than ordinary salad plants.


designed to simplify consistent crop development and allows individual growers to easily and automatically steer the growth of an entire crop – not just a compartment.