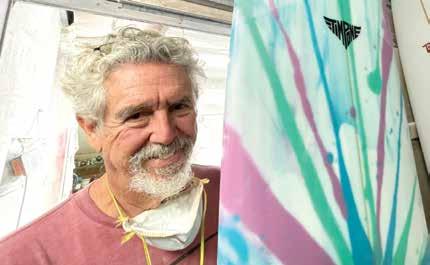
6 minute read
[New] Building a Better Board
Timpone Leaf Lite EcoBoards sport novel, natural materials
By Dan Collins
Advertisement
Sometimes it takes a new generation to push things to the next level.
Jeff Timpone had spent years perfecting the craft of surfboard building since the 1970s, but it’s his ecology-minded son Nick who has dramatically transformed the family business model over the last decade, incorporating new materials that improve performance and reduce the environmental cost of making surfboards.
The elder Timpone shaped his first board in a Laguna Beach garage in 1968. Later that same year, he moved to O‘ahu, where he worked as a boat builder while continuing to surf and build his own boards. After three years in the islands, he returned to Southern California where he honed his craft, working as a shaper for Russell Surfboards’ Brotherhood Glass in Newport Beach before opening his own shop in Huntington Beach in 1980.
After a decade in business, and confident in his growing skill set, Jeff returned to Hawai‘i, settling on Maui in 1989—this time with a wife and two kids in tow.
Again, he went to work at local shops, three in all, building sailboards and learning how to work with epoxy, which was popular with sailboarders due to its lightweight, superior strength, and rigidity, as opposed to the polyester resin typically used to coat surfboards.
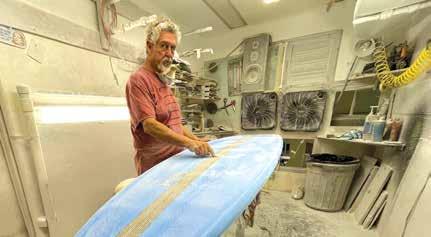
Having mastered the epoxy construction process while evolving the rail shape and rocker contours best suited to the waves at Kanaha and Ho‘okipa, he became adept at building all manner of surf- and sailboards, eventually leading him to rent space in Ha‘ikū’s Pauwela Cannery building—where most of the island’s shapers are headquartered— and return to working for himself.
By the time tow-in surfing began to emerge as a new twist on the sport in the 1990s, Jeff had established himself as one of the island’s master shapers, designing custom boards for the likes of Rush Randle and Laird Hamilton. Today, he’s busier than ever, often telling customers that it may take months to deliver the board they’ve ordered. But he likes keep- ing the business small and the boards custom.
As the business grew, son Nick began to learn the trade and help his father with the construction, glassing, and sanding of the boards. “I was just sort of a shop rat, kicking around the shop while my dad was running the show and shaping,” Nick recalled. He grew up surfing with future pros like Dusty Payne and Clay Marzo.
Modern surfboard design involves carving the desired shape out of a foam blank, which typically incorporates one or more narrow, wooden “stringers” running the length of the board to lend the foam strength and rigidity. Fin boxes and leash anchors are inserted and the finished shape is then wrapped in fabric— typically fiberglass but sometimes carbon fiber or other woven material. The cloth is saturated with polyester resin or epoxy to form a thin, hard shell over the foam. The board is then sanded and painted. None of this process is environmentally friendly, and some aspects are downright toxic. Shapers need to protect their lungs from the fumes and the fine fiberglass dust.
Typically after five or six years, the boards begin to crack and take on water, making them heavy, or they just plain snap in two. Either way, they end up in the landfill. This got Nick thinking about how he could make boards that were more friendly to the environment.
Nick had grown up a nature boy and developed a strong passion for conservation.
Ten years earlier, Clark Foam, the monolithic manufacturer of polyurethane surfboard blanks which had set the industry standard since 1961, abruptly shuttered their factory, citing regulatory issues with the Environmental Protection Agency (EPA) over the materials they used. At the time they were producing about 60 percent of the blanks sold globally, and supplying 90 percent of the U.S. market.
Timpone responded by adapting to expanded polystyrene (EPS) blanks, made from the same styrofoam that’s used for packing material and cheap ice chests. While neither material is easily recycled, at least the EPS is recyclable.
“The potential to recycle styrofoam is there, but the infrastructure is not,” due to lack of scale and low demand, Nick explained. “But because of that potential, I see that as the most viable option, environmentally.” He admits that the boards he’s building today may not get recycled, but as demand for green solutions increases, hopefully it will become practical someday in the future.
“We’re limited by the available materials and the available infrastructure,” Nick explained. “There is no styrofoam recycling in Hawai‘i—full stop—and there’s barely any on the continental U.S."
It’s not easy to build a “green” surfboard, in part because the process has historically been steeped in chemistry. “A lot of the resin and foam kind of popped up in the ‘50s,” Nick explained. “The petrochemical industry kind of bloomed then and we haven’t really tried to revamp it since."
"My dad’s old school,” said the younger Timpone. “Board builders who got their start in the ‘70s are really conservative as far as, like, ‘stick to what you know and don’t deviate.’ But I’ve got to hand it to him. He’s a great example of an old dog that learned new tricks."
The two had to forge their own way, because there hadn’t been much investment into experimentation with new materials that are less impactful. “The challenge I realized I was up against is what’s available to us,” he said. “Luckily, there are a couple of companies that are nibbling at the edges of creating something new.”
For example, before they settled on EPS blanks, Timpone was buying polystyrene blanks containing 50 to 70 percent recycled content from Marko Foam. Recycled material was mixed with new polyurethane, heated and re-blown into foam. But the company struggled to produce quality that matched virgin blanks. They eventually settled on 25 percent recycled content. “They came out bright white, clean, and not crumbly,” Nick said. But the demand just wasn’t sufficient to make the product line viable.
“I’m pulling my hair out going ‘how is there not a demand? Everybody in the surfboard industry should be jumping on this!” he went on. “But they’re more into economics than they are into the ethos of it all, which I understand from a business standpoint.” in announcing the installation of the 680-panel solar array.
Jeff laments losing their sole source of recycled blanks. “They told us they’re just not getting enough raw material to recycle,” he said.
Having experimented with a variety of reinforcement fabrics, Nick settled on hemp linen and woven flax fiber cloth, layered with fiberglass. “Hemp has been used as a reinforcement for centuries,” Nick said. “It’s
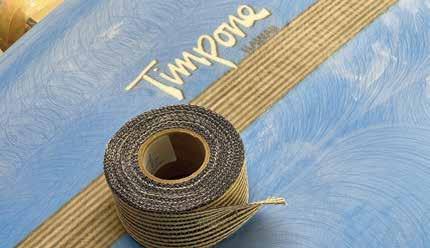
My dad’s old school. But I’ve got to hand it to him. He’s a great example of an old dog that learned new tricks. I brought all this information and materials to him and he embraced it.
Now the Timpones exclusively use Solar Made EPS blanks from US Blanks, started by former Clark Foam employees after the shutdown and now the dominant manufacturer. Since 2016 the company’s Los Angeles factory has been 100 percent solar powered. “Carbon footprint reduction has influenced every decision made at US Blanks,” said co-founder and VP Jeff Holtby got a very low ecological footprint, even from the growing process – because it doesn’t require herbicides or pesticides. It’s naturally resistant.”
“I like the raw look of some of the alternative fabrics,” he said. “They’re brown, not bleached, and it gives you this earth tone that visually tells you this is different. I personally think they look really cool. I especially like the flax because it’s a nice medium brown, but it’s very fibrous, you can see the weave.”
Instead of chemical resins Timpone uses a plant-based epoxy derived from the waste from pulp mills he calls “super sap,” sold by Entropy Resins. They initially tried a higher biocontent version of the resin, but it had discoloration issues. “Unfortunately, because it’s so natural, it renders the board in a sort of amber color,” Nick explained, “which is a real bummer, because a lot of people see that and they’re like, ‘that’s a sunburnt board,’” even though it’s brand new. Most surfers prefer a clean, white board— especially when they’re paying for a custom shape.
“What me and my dad do are custom one-offs. So, we’re not trying to produce ten boards a day. We’re really able to focus in on each individual board which allows us to use these different materials when the customer is willing to. For us, we were more than willing to pay a little extra because we were going to be able to make a unique product.”
One material that the Timpones are especially happy with is a hemp and basalt fiber tape that they custom ordered from an Australian company to replace the lengthwise strip of carbon fiber that lends most epoxy boards their strength, end to end. The boards they produce using these alternative materials get the special label, Maui Leaf Lite surfboards, and cost a bit more than his traditional designs. They now account for almost half of Timpone’s business.
“The boards come out bitchin,” said Nick. “They’re strong, they’re light. I believe they’re more durable.”
“On our website, and our social media I try to steer away from getting too deep into the environmental impact part, because people don’t really want to hear that,” Nick asserts. “What they want to hear is that your shit is quality.”
Nick acknowledges that their effort is largely symbolic. “Building these surfboards isn’t going to save the world. It’s the ideal that the board represents. It’s the movement, and I feel we can all be moving in the same direction.”
FOR MORE:
Facebook.com/timponehawaii @timponehawaii
Ecoboard.sustainablesurf.org
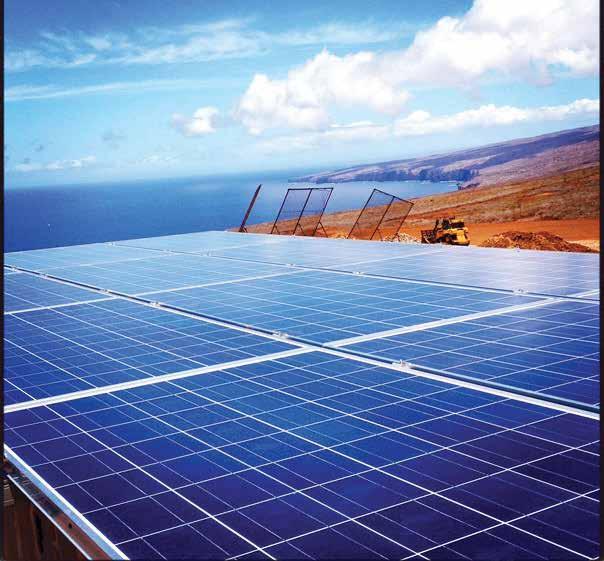
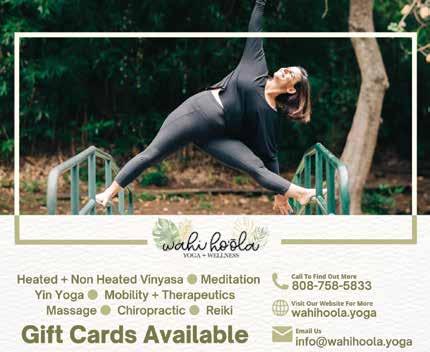
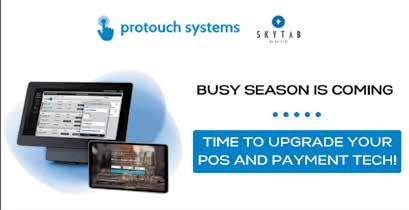