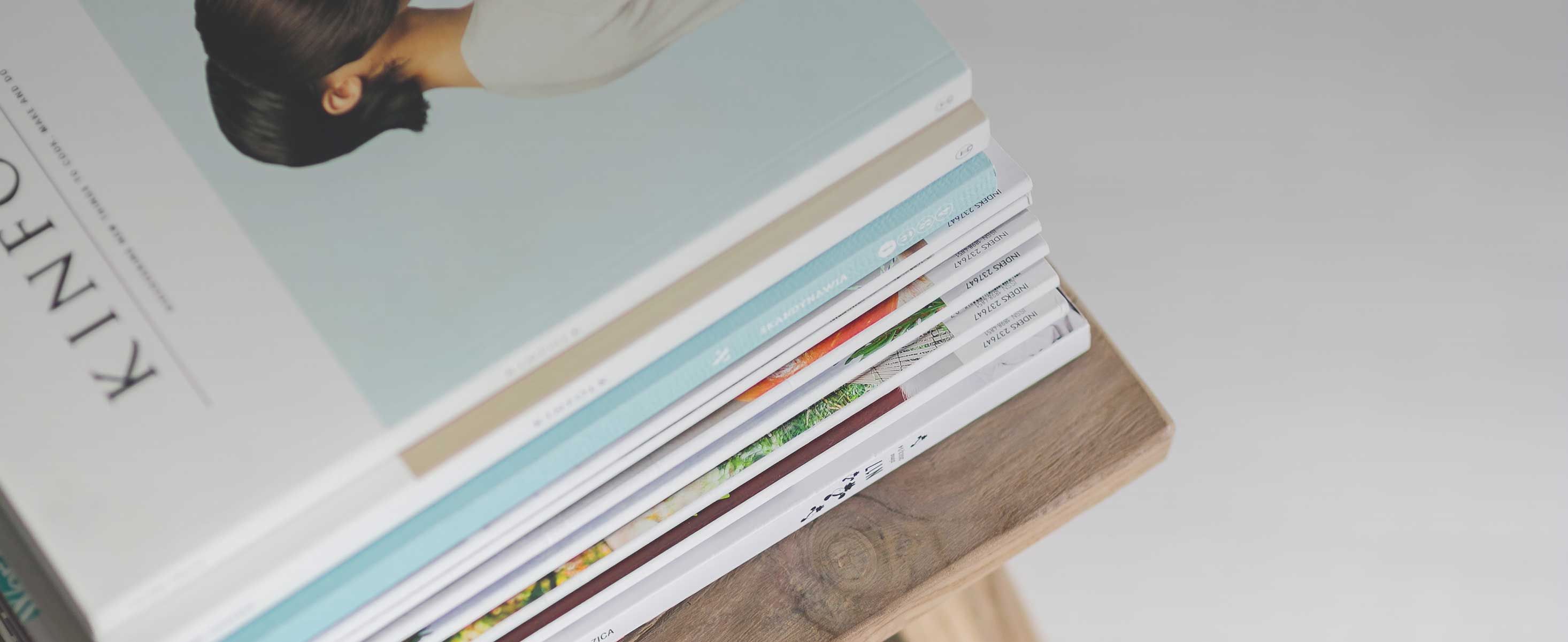
2 minute read
A safety issue that people tend to forget is ergonomics.
“Then we have training that not only goes to our team but also goes to the market,” Brink said. “That’s things like aerial lift operator training, forklift operator training and hoist and crane operator training that we make sure our team is properly certified, but we also offer that training to the public and to our customers.”
QLI, which specializes in post-acute rehabilitation and care for individuals with neurological injury diagnoses, has over 400 team members providing care to about 150 residents across their rehabilitation, summit, and assisted living campuses, according to Ash Bentley, coordinator of occupational health and safety.
“Keeping our residents, families and team members safe is a high priority at QLI, so we cast a wide net when it comes to planning for possible safety and emergency issues,” he said. “Our Safety Committee and Emergency Response Team meets regularly to update plans for responding to emergencies including adverse weather, natural disasters, fire, interruption of utilities and services, threats of violence, and armed intruder/active shooter situations.”
For example, QLI has partnered with the Omaha Metropolitan Healthcare Coalition (OMHCC) to participate in a simulated response to a hypothetical dirty bomb.
“It is challenging to try to foresee the unforeseeable, but these types of exercises help us grow our overall safety awareness and readiness,” Bentley said.
Safety From the Top Down
“Safety begins at the top,” said Don Birkentall, NSCN safety consultant/instructor. “The message of employee safety needs to come from the head of the company. When safety is important to the head of the company, it will be important to all management and employees below.”
For companies successful with safety protocols, presidents and CEOs drive the safety culture and hold directors, supervisors, and managers responsible for employee safety within their areas of responsibility. Company leaders routinely walk through workplaces to search for potential hazards and provide resources to have deficiencies corrected as quickly as possible.
“Safe workplaces train their employees to recognize potential hazards and how to prevent injury,” Birkentall said. “They give workers the knowledge and equipment to perform their jobs in a safe and productive manner.”
Brink said safety is ingrained in Riekes Equipment’s culture.
“All of our top leadership is very dedicated to safety and addressing concerns,” she said. “For any business to be successful, safety must come from all levels of the organization.”
The company has an active safety committee, which includes some of its directors and about a dozen employees who serve rotating terms. They visit sites to do walk-throughs to make sure everything is safe.
“They launch initiatives and track anytime there’s a near miss so we can eliminate that as a risk for us going forward,” Brink said. “That committee is key to making sure our safety is above that industry standard.”
Team members in all areas at QLI are encouraged to take an active role in safety.
“Safety is not about just following the rules,” Bentley said. “It is about taking actions to make sure that every team member goes home each day as safe and healthy as they were when they arrived. It’s truly a team effort.”
All new QLI team members participate in over six hours of training on emergency procedures and workplace safety during their first week of employment. Ongoing annual training for