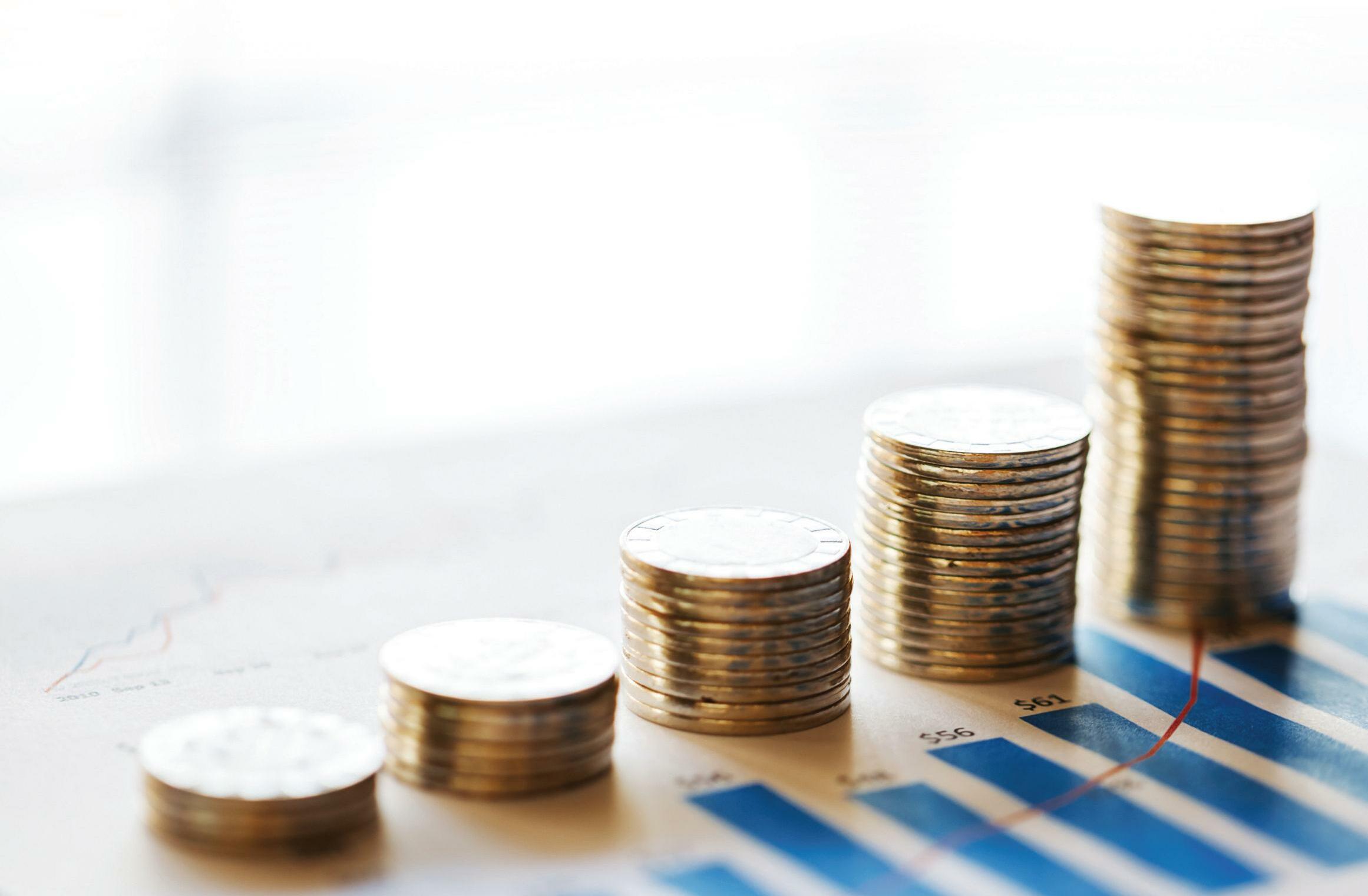
23 minute read
Port study reveals Canadian investments more than double of US West Coast ports funding
Port study reveals Canadian investments more than double US West Coast ports funding
ArecentstudyexecutedbyDavies TransportationConsulting,incollaboration withHatchConsultantsAssociates,has revealedthatCanadianportshavereceived morethandoublethefederalfunding levelscomparedtoUSWestCoastports...
The study, commissioned by ports in Washington and California, highlights the need to increase US port infrastructure funding in order to strengthen US ports ’ competitiveness along the West Coast. Current federal levels of investment in infrastructure are insufficient to build the freight system the US needs today and in the coming decades. Improving the efficiency of existing infrastructure requires strategic investments that enable ports to handle current volumes and grow capacity to remain competitive with ports in British Columbia (BC). From 2016-2020, BC ports received USD372 million in Direct Port project funding compared with USD45 million forWashington State ports and USD179 million for California ports.This funding differential leads to a competitive disadvantage for US west coast ports.
Beyond port-specific projects, the road and rail infrastructure that supports the efficient movement of goods throughout the supply chain are also receiving significantly fewer federal dollars than BC investments.The study reports that from 2005-2020 federal contributions to port-related projects total USD1.332 billion in BC compared to US USD457 million for Washington projects. These dollars support critical infrastructure such as road, rail, highway and bridge upgrades.
“The Northwest Seaport Alliance has worked diligently to remain competitive despite inequitable distributions of the Harbour Maintenance Tax and growing competition with BC ports.The Canadian government has made their British Columbia ports a national priority and unfortunately US west coast ports have seen market share slowly shift north to Canada, ” stated NWSA Co-Chair and Port of Tacoma Commissioner President Dick Marzano. “More infrastructure funding from the US federal government means that we can move more cargo and support more family-wage jobs across our region. ” US west coast ports compete directly with ports in Canada such as Prince Rupert and theVancouver-Fraser Port Authority for cargo volumes in theTranspacific trade.As the Northwest Seaport Alliance, Port of Long Beach,and other ports in California aim to maximise US trade opportunities,accessing federal and non-federal funds for port-related investments is a fundamental challenge.
Key takeaways from the study include: * Ports in British Columbia have successfully competed against Washington and California ports for container traffic. * Canada has treated West Coast Ports as a national priority. * Canadian federal contributions to BC port projects have substantially exceeded US grants to Washington and California ports over the past five years.
“The important role seaports play in the nation ’ s economy has never been more visible than it is today, during the global pandemic, ” said Port of Long Beach Executive Director Mario Cordero. “The ports of Long Beach and Los Angeles, known as the San Pedro Bay port complex, handle 40% of the nation ’ s container cargo imports.TheWest Coast is the gateway to Asia and the country ’ s most prominent trade partners.A more equitable distribution of federal funding would make all our operations faster and more efficient, with tremendous benefits up and down the supply chain. ”
Beyond funding, the study identifies ways to increase USWest Coast port competitiveness including prioritising investments to accommodate larger vessels, upgrading landside infrastructure, and improving the environmental sustainability of port operations. “The Northwest Seaport Alliance is making strategic investments in infrastructure to increase the efficiency of Seattle and Tacoma ports and remain competitive, but we can ’t do it alone, ” stated NWSA Co-Chair and Port of Seattle Commissioner President Fred Felleman. “Investments in port infrastructure not only benefit our economy but also reduce impacts on our neighbouring port communities and the environment.The Infrastructure Investment and Jobs Act and the Build Back Better Act fully recognise these benefits. ”
Ports play an integral role in the health of the US economy. By facilitating import goods for businesses and providing a key gateway to international markets for exports, ports support the country ’ s GDP and create millions of family-wage jobs across the country.
The Northwest Seaport Alliance has stated it is committed to maintaining a thriving gateway for US trade in the Pacific Northwest and is making substantial investments to modernise its marine terminals and improve freight mobility through the port.
The NWSA is already implementing many of the study ’ s recommendations including modernising Terminal 5 to handle larger container ships, partnering with local governments to advocate for improved landside infrastructure, and investing in zero-emission cargo handling equipment in the gateway.
Nordic ports ready for expansion in years to come
DespitetheCOVIDpandemicandits negativeconsequencesforinternational economiesandtrade,majorNordicports arecontinuingtheirexpansionplansthis yearasEugeneGerdenreports…
hese expansion plans are primarily in the form of the construction of new infrastructure and modernisation of existing ones. For example, in Sweden, the largest country in the region,local government together with private investors and stevedores, plan to speed up the implementation of at least two large-scale projects in the port sector. One of them will be implemented in the Port of Gothenburg,Scandinavia ’ s largest port,that will be turned into a major hydrogen hub in the region. As part of this project, a new hydrogen production facility with the capacity to produce up to two tonnes of hydrogen per day will be built within the port area.This implementation is part of Sweden ’ s goal to reduce emissions from domestic transport by 70% by 2030. In the meantime, the Gothenburg project (scheduled for implementation in the near future) is not the only major investment in the Swedish port sector.
Another major Swedish seaport, Helsingborg, is also expanding with the building of a large-scale container terminal within its port area. Under the terms of this project, a 750m-long berth will be built to accommodate three deepsea 225m vessels. In addition, there are also plans to build an intermodal terminal that will connect southern Sweden ’ s logistics clusters.The project is expected to be completed by 2028. At present, ports play an important role in the development of the Swedish economy, with almost 90% of the country ' s international trade being moved by maritime transportation. Most local analysts expect the same situation will continue within the next several decades.
In the meantime, the development of the port sector is also ongoing in neighbouring Norway - another major country in the Nordic region.According to some Norwegian media reports, probably one of most important projects in the port sector for several years will be implemented in the port of Bergen. Plans include the building of a new cargo terminal within the port area that will function as a hub for zero-emission distribution of goods and services.It is planned that the EUR25 million

needed for the project could be funded by the EU in the form of a grant - as part of the EU Green Deal political project where the goal is to reduce emissions from the transport sector. In the meantime, the Norwegian Foreign Minister Ine Marie Erikson Sereide, has confimed that Norway has no plans to invest in the development of its ports located along the Northern Sea Route, and in particular the port of Svalbard.This is in stark contrast to neighbouring Russia, which considers the Northern Sea Route as a full-scale alternative to the Suez Canal and make numerous investments in the development of its port infrastructure.
In Denmark, Copenhagen Malmö Port AB (CMP) - the company operating both the ports in Denmark’ s capital Copenhagen and in Sweden ’ s third largest city, Malmö - has recently confirmed its plans to build a new container terminal in Copenhagen ’ sYdre Nordhavn seaport. The planned terminal will be completed by 2023 and has an estimated budget of USD130 million. It will have a 165,000 square meter large port area, a quay length of 550m and two new ship-to-shore container cranes.The new facility will be part of a 1 square km land refill which will also accommodate a nature park.The project also aligns with the aim of the European Union to cut down emissions rates from such industrial activities.According to some local analysts, the new container terminal plan promises potential growth in business and sustainable development to the Nordhavn region of Copenhagen.
Whilst building the new terminal, CMP will continue to operate the container terminal in Levantkaj, Copenhagen, in order to welcome any additional container traffic to the port.The port of Copenhagen, one of Denmark’ s largest seaports, saw container volumes significantly drop in 2020 and 2021 as a result of the global pandemic. Finally, in Iceland, the country ’ s government, together with private investors, are considering to resume the Finnafjord Port project, a proposed deepwater port and industrial site. The pandemic led to its suspension, however the planned construction will now start between 2022 and will continue until 2040. The deepwater port of Finnafjord will mainly serve as a transit hub for traffic entering and exiting Russia ’ s Northern Sea Route.In addition, the port may also serve as a search and rescue base as traffic volume throughout the region increases.
The joint-venture project will be implemented by Bremenports, which owns 66% of the port, EFLA owns 26%, and the nearby municipalities ofVopnafjaroarhreppur and Langanesbyggo own 8%. Once completed the new port could also become a distribution hub for offshore arctic oil and mineral resources for Greenland and Iceland.
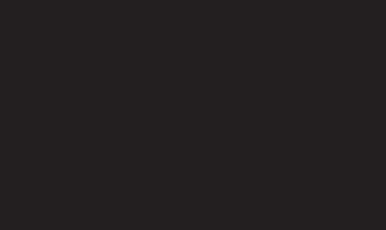
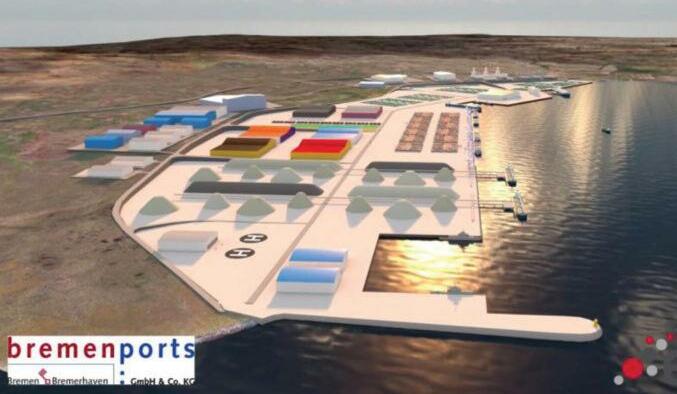
Above: Finnafjord project in Iceland. Main photo: Port of Helsingborg.
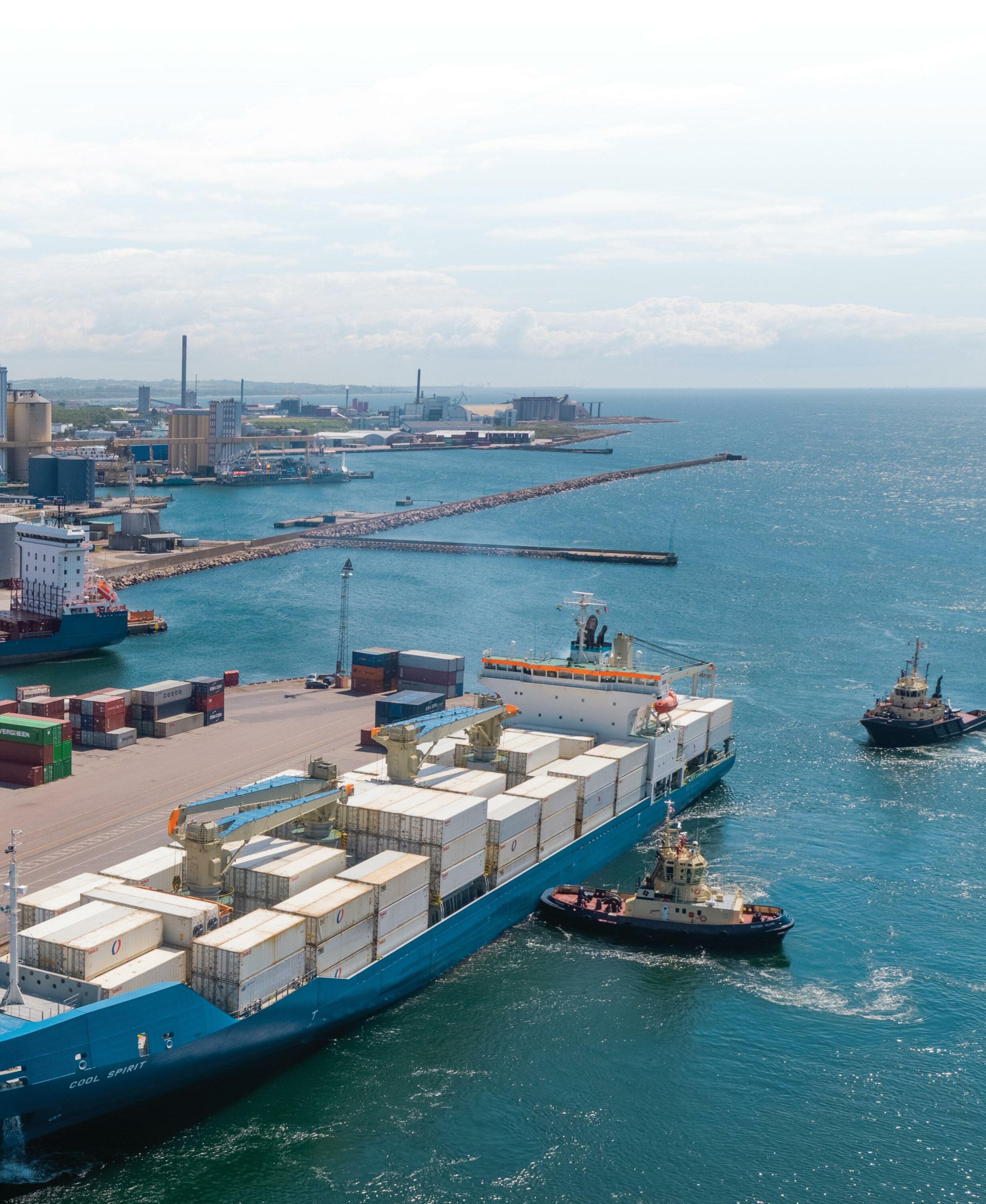
Hammar has introduced an electric power pack for their sideloader.
Sideloader makers weather the global pandemic
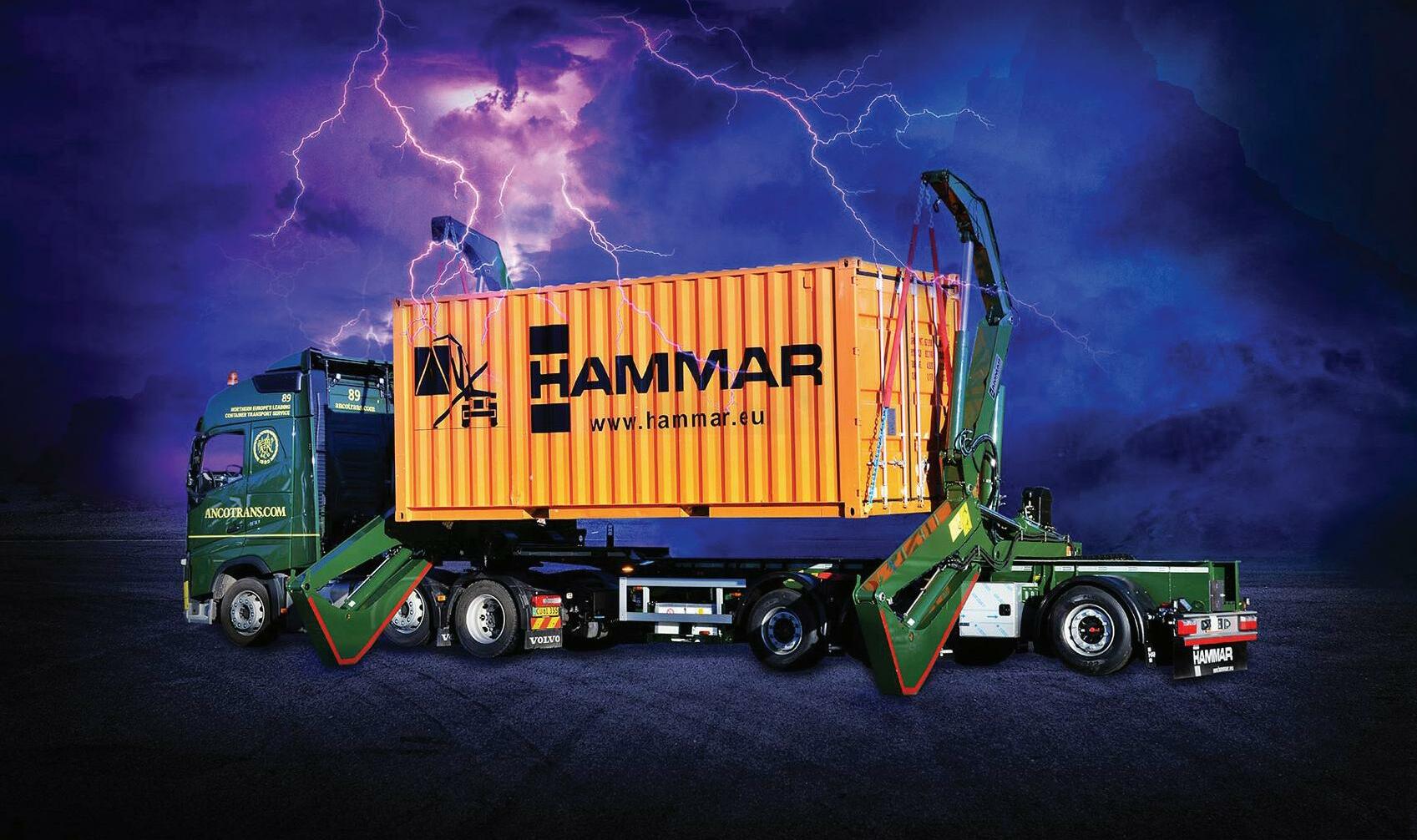
DespitetheglobalCOVID-19pandemic manufacturersofsideloadersarereporting someinterestingdevelopments. World PortDevelopmentreports…
For those that have not seen a sideloader (also known as sidel or self-loading trailer) in action ifter perhaps a simple explanation how such a system works is appropriate.A hydraulic system is mounted on a truck or trailer to safely handle shipping containers and other cargo from/to other trailers, trucks or trains, or directly on ground level, where the container/cargo can safely and efficiently be packed or unpacked.A major benefit of a sideloader is that it can operate with minimal manpower and without any additional equipment, minimising waiting time, planning as well as making it possible to deliver a seamless, competitive service. It also offers a versatile cost-effective way of loading,transporting and unloading containers and other cargo. The sideloader is often used where other container handling equipment is not available, or non-existent.Just like any other cargo handling equipment to fullfil customer expectations and requirements,manufacturers constantly improve their equipment in order to increase their handling capacity, efficiency and performance.
Steelbro
The engineers and design team at New Zealand-based Steelbro recently launched their SB303 30 tonnes lifting capacity sideloader. The SB303 provides the user with fast movement of containers from trailer-to-ground and ground-to-trailer with its ability to quickly deploy and stow stabilisers.The key to increased speed is a new HYDRAlift hydraulic system technology.The new inline crane design is also light with tare weights starting from just 7 tonnes. “Our research and insight programme identified a need for a fast, light sidelifter for use within an urban environment to deliver and pick up 20’ and 40’ containers. To deliver this to the market,the team designed the SB303, ” explains Richard Brown, Research and Development Manager at Steelbro.
According to Brown, the HYDRAlift is a fundamental rethink of the sideloader control combined with the latest in hydraulic piston pump technology and a new advanced proportional control valve.The single central control valve halves the number of proportional valve sections per sideloader, minimising servicing costs. In addition, intelligent use of available oil flow allows for better engine and pump utilisation.
Brown toldWPD that the SB303 is also cost effective to run, as horsepower utilisation has been optimised by enabling the efficient use of engine power.In addition,machine controllability has been optimised via proportional joystick control with multi-function operations and improved flow sharing technology which enables precision control throughout the lift. This functionality also ensures containers can be delivered safely at speed.The new model is also equipped with an enhanced SMARTlift II next generation load monitoring system. This is the latest evolution of Steelbro ’ s load monitoring system that has been continuously improved since its release in 2005. SMARTlift II provides users with the additional benefits of a colour display with high resolution screen, clearer messaging, simpler diagnostics and maintenance as well as environmental protection. The SB303 has a large outreach of 3.64m from the trailer lifting side and is optimised to perform pick up and delivery of containers from ground-to-trailer and trailer-to-ground only. It can lift both single 20’ , 40’ containers and 2x 20ft containers.
Hammar
At Sweden-based Hammar, customer requirements forced them to look at different options for increasing handling capacity, including the possibility of placing the container in a second row.Technically, many factors decide how much you can lift with a sideloader. This includes for example, the reach of the support legs, the weight of the sideloader, the strength of the extension construction, hydraulic pressure and cylinder sizes.As a result, the Hammar designers came up with two new options for their Hammar 110 model - a 40 tonnes Safe Working Load (SWL) for extra heavy duty, and a new support leg option “WideLeg ” .
The new 40 tonnes SWL option is available with both the new WideLeg option and the standard support legs on the Hammar 110. Reinforcements at vital points have been made on the crane module, with the goal to minimise extra weight and maintain maximum safety.With 40 tonnes SWL the Hammar 110 is tested with 50 tonnes before delivery.
The new WideLeg option is a new support leg design available to the Hammar 110 model.Very similar in function, the WideLeg option differs by giving an additional 500mm reach, meaning it will reach approximately 3.65m measured from the trailer lifting side. This will give even more stability, make transfer operations easier while also allowing the transfer from rare special wide vehicles. Another solution on offer is the ‘MegaReach’ crane extension allowing sideloaders to stack two containers high in second row.The new MegaReach extension will be a new milestone for sideloaders allowing a longer reach and an increased SWL of 15 tonnes at maximum reach. It can stack containers in second row weighing up to 17 tonnes.
“This is the first crane extension for sideloaders in the world to reach anywhere near these capabilities. Sideloader operators often face less than ideal situations, and the added versatility of these extensions will make many jobs much easier. Stacking containers will be more viable, and we believe it could open up completely new markets for Sideloaders, ” says Bengt-Olof Hammar, CEO and owner of Hammar Group.
In terms of safety, Hammar tells us that operators don ’t have to worry about their operations as they are monitored by their Safety+ system (although this depends on what model you choose). Forced by customers to go ‘ green ’ Hammar has also introduced an electric power pack for their sideloaders. The electric power pack (ePP) lasts around 20 consecutive lifts with a 35 tonnes weight. It can be charged by the truck while driving or by plugging it in the mains. Compared to the traditional diesel power pack the ePP has many advantages, including less environmental impact, a healthier working environment, lower operating costs, a lower weight and significantly lower noise levels. Zero emission and lower noise levels are particularly useful in the increasingly dense urban areas, where this otherwise can be a problem.Ancotrans, one of the largest sideloader operators in Denmark, was the first company outside Australia to receive the electric sideloader.With a long-term focus on greener container transports the electric power pack was an obvious choice.
Bengt-Olof Hammar told WPD that such technology is in constant motion and Hammar is already developing the next generation of electric power packs for sideloaders. “We will continue to look at and develop greener alternatives and be at the frontline of electric sideloaders, ” he said.

Fallout of COVID
The pandemic saw an increase in spare parts sales as customers sought to optimise their current fleet of sideloaders.In order to simplify this process for all global customers, Steelbro launched an online parts shop this year. It is accessed via their website and customers can use the shop to identify parts and receive a quote in a currency of their choice.
“Steelbro had experienced growth over the last 2 years, although at times customers have been cautious about committing to capital expenditure in the uncertain economic environment. Interest in sidelifters is still strong and the benefits the product brings have been vital during the pandemic and we expect this to continue into the future, ” said Peter Dobbs, General Manager at Steelbro. “Steelbro is already seeing a rebound in demand in key markets such as New Zealand,Australia and Malaysia. ”
In 2019, Steelbro expanded their footprint in New Zealand to incorporate a workshop facility that was primarily focussed on new product design and development.Their strategy is to support customers by working directly with them and the purchase of a larger workshop in Christchurch in 2020 demonstrated the company ’ s commitment to this strategy. According to Dobbs, the new premises enabled Steelbro to create a specialised sideloader site.All functions are located at one site: service and repairs, research and development, sales, assembly and fabrication, technical support, spare parts and administration.This new premise means Steelbro can offer a wider range of services to customers.
Earlier this year, Steelbro also expanded its footprint in Australia with the opening of a new sales and workshop facility in Brisbane. This facility supports customers across the east coast of Australia for both Steelbro Sidelifter sales and parent company Howard Porter trailer sales.
Courtesy of Steelbro

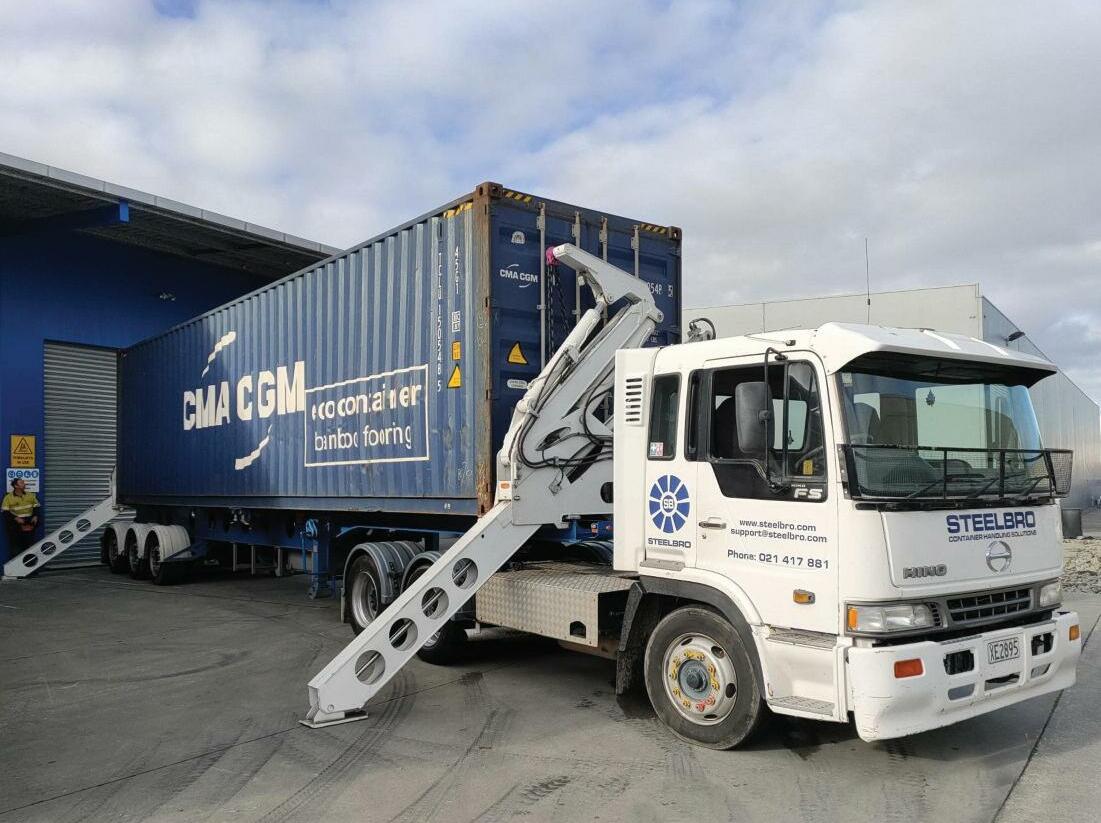
Evolution of scientific methods for structural life assessment and its application on lightweight spreader design
Bromma has been engagedin many industry-supportedacademicresearch projects,oneofwhichhasfocusedon lightweightweldedsteelstructuresincluding thedesign,manufacturingandlifelength assessmentmethodsused.
arlier this year, Sweden-based spreader manufacturer Bromma released a white paper on how the life length assessment of complex steel structures used in crane spreaders are applied and how the application relates in the real world. Although Bromma wants to make it clear that there are no reasons to suspect that manufacturers of steel structures are not conforming to the standards specified, the key question of the white paper is whether the standards are up-to-date with reality. According to Bromma, the studies performed have already influenced the design of steel structures and are expected to play an even more important role in the future, as the industry realises the discrepancy between reality and the standards applied. The white paper, written by Dr Mansoor Khurshid, Head of Structural Science and Lars Meurling,VP EMEA & Marketing, reveals that different kinds of fatigue strength assessment methods show very different results. More advanced methods reveal sensitive stress zones in the steel structures more precisely. The results from assessments using ’ simpler ’ methods indicate a longer life length compared to the more advanced methods. The ‘ simpler ’ methods as specified in existing standards, show in addition a significant deviation to experimental tests performed depending on the location in the spreader under investigation. The outcome of calculation methods called for in current industry standards will likely lead to results deviating from reality. Bromma conforms to current industry standards but are, in addition, using significantly more advanced methods for fatigue life length assessment.The result is optimised steel structures with improved durability.
Lightweight spreaders
Structural integrity is an important aspect in spreaders where steel is the primary material and welding is a primary technique used for joining them together.Welded joints are usually critical sections prone to mechanical failures, which involve extremely complex E interaction of load, time, material, manufacturing processes, and environment. Environment includes operation temperatures, and corrosive environment such as experienced in ports. Loads may be monotonic e.g. maximum safe working load limits, steady or variable e.g. lifting constant container weights all the time or lifting up variable container weights (Q class classification in EN13001).The duration of these loads can vary from a few seconds to minutes e.g. overloads can occur for a shorter interval of time or a load due to normal container weight can occur on the structure for the whole working cycle. One of the goals of Bromma is to develop spreaders with low weight. Lighter spreaders reduces crane power consumption and CO2 emissions. Bromma utilises high strength steel in spreaders to achieve these goals. To successfully implement such steel qualities in spreaders it is important to understand the material characteristics as well as how to join parts of the material together and where to place the welds.
Spreader structural strength
There are thirteen common failure modes identified in metals.Two of the common failure modes are ductile failure and fatigue failure.
A particular welded structure such as a spreader is usually designed primarily against these failures to ensure sufficient structural strength.Around 50 to 90 percent of all mechanical failures (not limited to spreaders) are related to fatigue. Fatigue is a wide area which is influenced by various factors such as selection of fatigue strength design methodology, type of residual stresses, type of loading, welding processes, and post weld improvement methods (see Figure 1). The life span of a spreader is defined by the fatigue calculation methodologies and the materials used in the design process. It is important to define correct capacity of the welds in spreaders and know the load spectrum of the customer, i.e. Q class and average container weight handled. Design curves in the standards such as EN13001 available today have been developed for simple uniaxial stress states and the use of global fatigue strength assessment methodologies is recommended.
However, the welds in spreaders might be subjected to complex stress states and simple fatigue strength assessment methods may not be applicable.To design welds against these complex stress states, the choice of the appropriate analysis method and definition of the loading plays a vital role. It is important to understand the interaction of stresses resulting from hoisting, slewing, trolley, gantry and landing operations etc and their effect on the spreader structure.
Better understanding of the safe working load limits, working cycles, average container weights and fatigue strength will make it possible to manufacture spreaders with an even higher grade of high strength steels such as those with a yield strength greater than 1000MPa.
Box welded structure assessment
Several years ago, Bromma established an R&D collaboration with KTH - Royal Institute of Technology Stockholm, Sweden, through a joint appointment and ventures, with focus on further development of novel and advanced design methods for accurate strength and life estimation of Bromma ’ s products.
One such project within the collaboration is project Varilight (Reduced VARIation in the manufacturing processes enabling LIGHTweight welded structures).This project was a joint effort between industrial (HIAB, Swedish Steel AB, Swedish Welding Commission, Cargotec Sweden AB, Bromma Conquip and Volvo Construction Equipment) and academic partners (Chalmer Tekniska Högskolan, and KTH-Royal Institute of Technology).
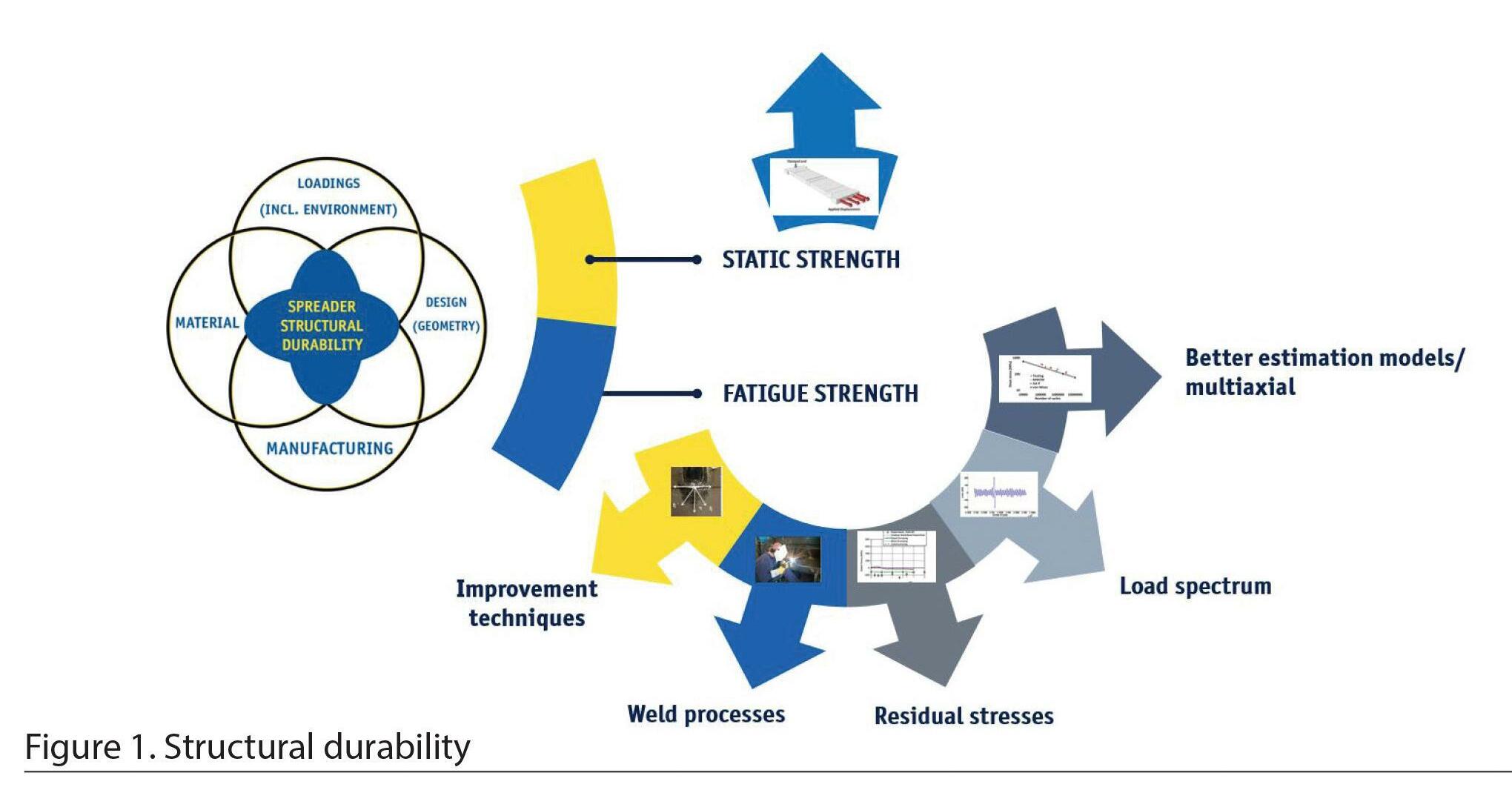
Among other things, a box-welded structure has been investigated within the project. The life span of box-welded structure is influenced by the definition of working cycle, choice of fatigue strength assessment methodology, load spectrum and welding residual stresses.The most common design specification for crane spreaders today is 2 million working cycles but a specification for 4 million working cycles is starting to appear. Information about the definition of working cycle, choice of fatigue strength assessment methodology, understanding of load spectrum and behaviour of spreader components subjected to fatigue loading sets the basis.
Working cycle
A typical spreader move or working cycle comprises of various movements.According to Bromma a working cycle is defined as a spreader landing on the load, hoisting the load, trolley movement, spreader landing and leaving the load, and the empty spreader travelling back to lift another container.
This definition is in line with the working cycle definition in EN13001 and BS2573. During a typical working cycle there are stresses generated at various sections of the spreader.A typical working cycle for a spreader can result in three stress blocks as seen in Figure 2. Some of the stress blocks can be more damaging to the life of a spreader than others.
Fatigue strength assessment methodologies
Design methodologies play a vital role in the construction of lightweight structures especially when deciding their life span or fatigue strength. For welded structures, stress based methods such as nominal stress, hotspot stress, and effective notch stress exists to design for high cycle fatigue such as 2 million or 4 million working cycles. Other methods e.g. strain life approaches and linear elastic fracture mechanics are also used. In the design of Bromma spreaders, a combination of these methods following guidelines in EN13001 and other scientific literature is used.

Figure 3 provides an overview about the accuracy and required effort to use these methods. It can be observed that as we move from designing simple welded joints to complex welded structures, the accuracy of most of these methods decre¬ases. Furthermore, if we move from using global methods (nominal stress method) and start using local methods (effective notch stress method) the accuracy of estimating fatigue strength increases.
In EN13001, nominal stress method is included. The designers are free to use more advanced methods. So which methods are applicable for the assessment of complex structures like spreaders? Can all the critical areas such as box welded structure be analysed with the methods recommended in the standards or should we use more complex fatigue strength assessment methods?
Fatigue strength of box welded structure - testing and results
In projectVarilight, box welded structure was analysed using various fatigue strength assessment methodologies. (Figure 4).
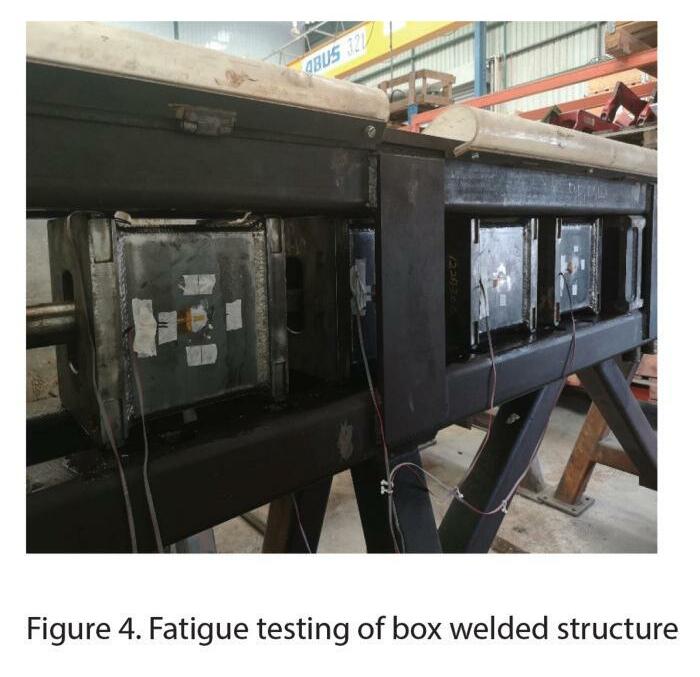
A round robin study for evaluating various fatigue strength assessment methodologies and studying scatter in the results was conducted in Sweden within the project.
In this study, the same problem was sent to various engineers (from different organisations) for calculations and they were asked to use nominal stress method for calculations and one other method of their choice. It was observed that even though the same problem was assessed by various engineers, there was a clear scatter between the life estimates by the engineers for the box structure. In Figure 5, it can be observed that simple calculation methods, which are recommended by the standards, were over-estimating the fatigue strength for this particular component whereas advanced complex fatigue strength assessment methodologies such as effective notch stress and linear elastic fracture mechanics (LEFM) are conservative to estimate the life span. In the above assessment, the effect of residual stresses was also considered. Residual stresses at the weld toe and weld root were studied experimentally and by using computational weld mechanics techniques. Based on the observations in Figure 5, more advanced methods are conservative and safe to use while care has to be taken when using nominal stress method.

Conclusions
Based on the analysis the following conclusion can be drawn: - There is a significant difference in the precision of different fatigue strength evaluation methodologies, when applied on complex welded joints in crane spreaders. -The methodologies specified in the applicable design standards are relatively ‘ simple ’ methods, which in cases of complex weld details overestimates the life length of a steel structure. - When more advanced calculation methods are used, the outcome is more in line with reality. - By applying the more advanced methods in the design process - even though the standards are less stringent - manufacturers of lifting equipment can lead the development towards more durable and also potentially safer steel structures and products.
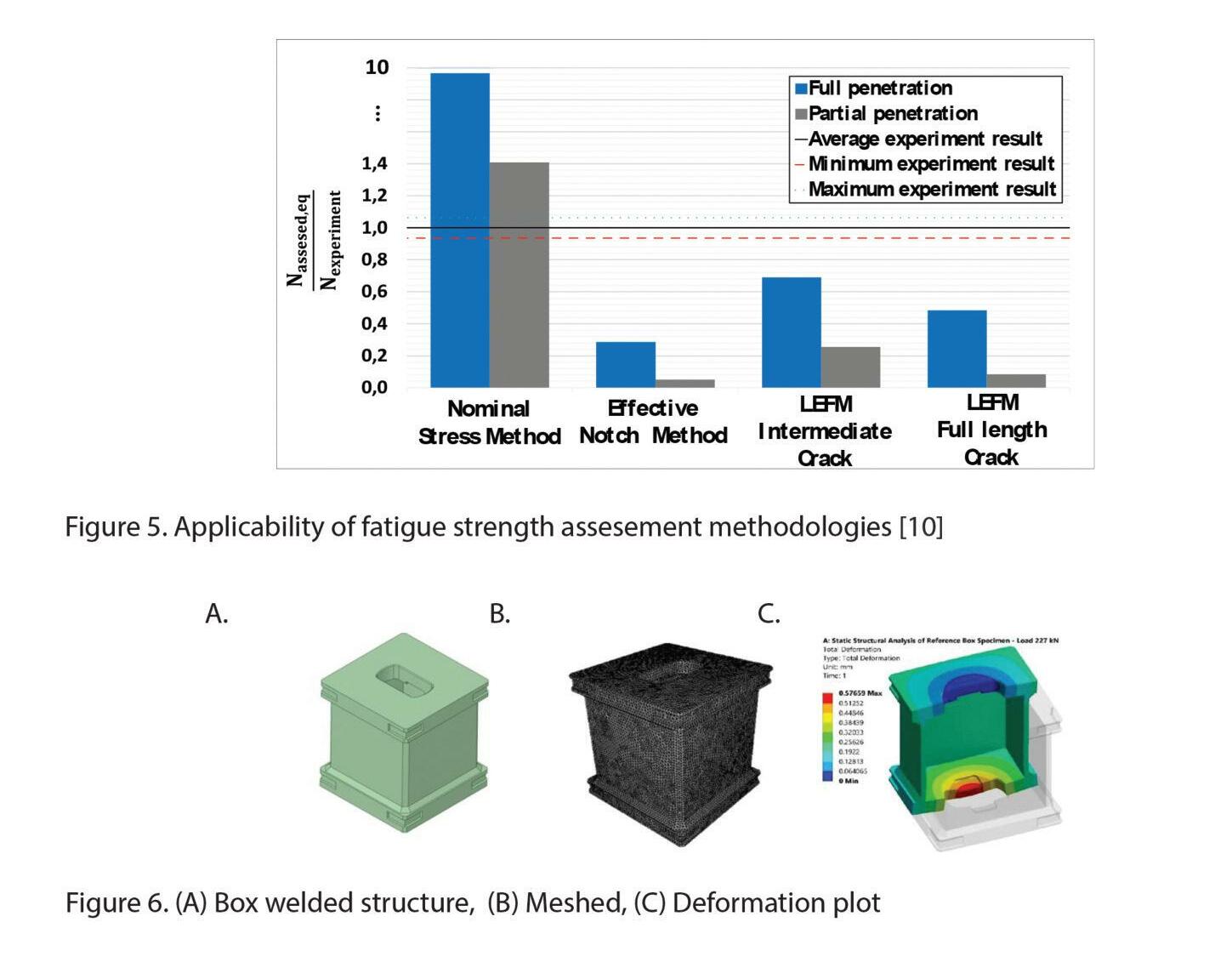