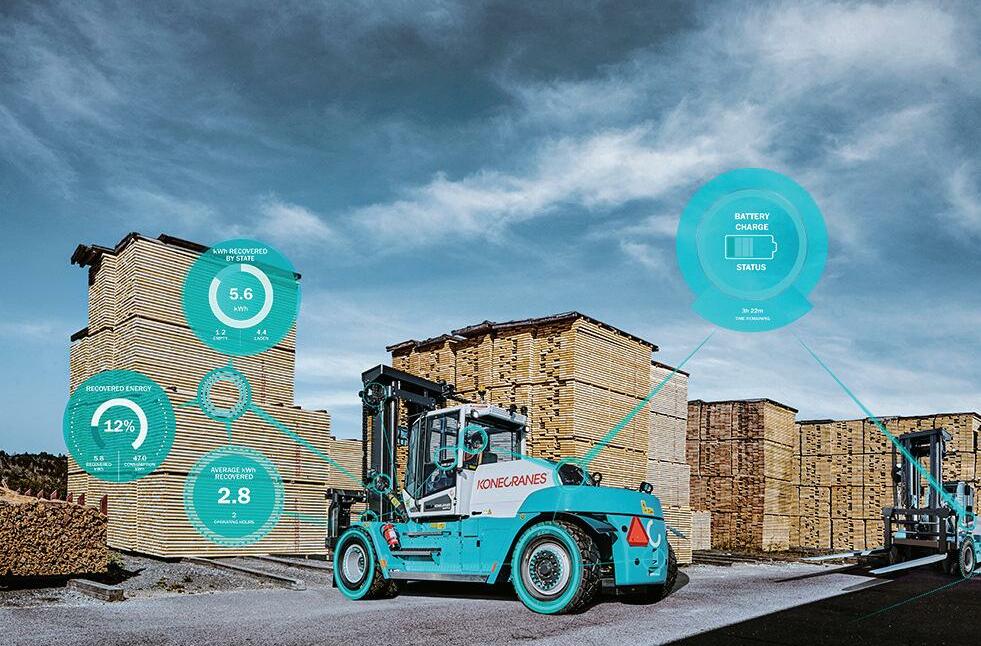
9 minute read
Electrification trend continues to be strong
ElectrificationElectrification trendtrend continucontinueses toto bebe strongstrong
W
hen it comes down to electrifying forklift trucks it seems there are only a handful of players in the market. In this article we look at two Finland-based manufactureres of forklift trucks Konecranes and Kalmar who are both world leaders in this field. Over the years, Konecranes have left their (future) customers somewhat in the dark about what they were doing when it comes down to battery technology for forklift trucks.They have been very succesfull applying battery technology to their automated guided vehicles (AGVs) for years so it was somewhat confusing why they didn ’t make the step to electric (heavy-duty) forklift trucks sooner.
Instead,they focused on their Ecolifting initiative intended to reduce the energy consumption and overall carbon footprint of their forklift trucks. “Ecolifting is the commitment of Konecranes Lift Trucks to support the market and customer through future decades of transition with environmental footprint reduction, sustainability, technology and operational change, ” said Jeffrey Stokes, Director Product Management, Konecranes Lift Trucks. “It’ s clear that the next decade will see a significant shift in many aspects of our business and market, to which new innovative ideas combined with new technologies will be a key enabler. ”
But it became obvious that Ecolifting, although sucessfull, was not enough and that customers demanded a much further reduction in the environmental impact of each lift truck they delivered. So in order to decrease the carbon emissions when using the trucks, the company started applying lithium-ion batteries on lift trucks. This started with the lower end - up to 5 tonnes - and it took a while before making the next step to the heavy-duty forklift trucks.
“For businesses that operate forklift trucks from 10 tonnes capacity and up, electrification is becoming more and more of an attractive option, ” said Stokes. “The potential for electrifying industrial lifting has come so far that it’ s becoming hard not to justify transitioning towards it, especially if the goal is reducing carbon footprint and noise emissions while lowering operating costs and improving the drivers ’ work environment. ” At competitor, Kalmar (part of Cargotec) there has been great progress since 2021 according to David Pilten, Business Development Director, Kalmar Forklift Trucks, who told WPD that “ since the end of last year, every piece of equipment in the Kalmar forklift range has been available in an electrically powered version, including an electric heavy forklift suitable for use in a range of environments from ports to factories. ”
Kalmar prides itself on the fact that more than one-third of their forklifts in Europe are now electrically powered, and that there are in excess of 5500 electric forklifts operating in 75 countries across the world – however there is an issue.These primarily light vehicles with lifting capacity ranging from 5-9 tonnes are often powered by lead-acid batteries, although newer models are equipped with lithium-ion batteries.These lead-acid batteries used on the forklift trucks might cause an issue with‘ environmentally- friendly ’ operators, not only on the issue of disposal, but also the life span which is not as long as lithium-ion batteries, Furthermore, charging of lead-acid batteries takes much longer (which results in less productivity).
It is therefore no surprise that Pilten points out that the company has seen an increase in interest in lithium-ion powered electric heavy forklifts trucks, and in particular, with lifting capacity of up to 33 tonnes. Needless to say that Kalmar ' s new series of electric forklift trucks of 9-18 tonnes are all equipped with lithium-ion batteries offering eight hours of operating time and charging from empty to full in less than two hours (offering improved productivity compared to lead-acid batteries).
Reading between the lines, there is a huge market for forklift trucks in the 3-18 tonnes range and it is no surprise that Konecranes has focused on businesses that operate forklift trucks from 10 tonnes capacity and up, as electrification is becoming more and more of an attractive option for them.
The Konecranes electric forklift truck E-VER combines durable, heavy-duty lifting machinery with an all-electric drivetrain and the latest eco-efficient features to help improve productivity while reducing the energy consumption, emissions and costs. The E-VER achieves this by using a lithium-ion battery that powers a 110kW electric drive motor and an 80kW motor for hydraulics and lifting.
Return on investment
While customers appreciate the importance of working towards a zero-emission future, they also need to understand what the switch to electric vehicles means in terms of infrastructure requirements including charging facilities, shift patterns and total cost of ownership.
But when considering operating costs, it is important to note that the electric machines do not have many of the components of a diesel powered vehicle that need to be serviced/replaced regularly.
“For instance, they don ’t require oil filter changes, catalysers or diesel particle filters, ” explains Mikael Andersson, Product Manager for Kalmar forklift trucks. “In terms of emissions, the diesel combustion process emits 2.64kg of CO2 for every litre of fuel consumed, which equates to approximately 40 tonnes of CO2 emissions per year for the average forklift truck.To produce the same output as a litre of diesel, an electric machine requires approximately 3kWh of electricity. So over the course of a year our average machine will consume approximately 45,000kWh of electricity, but will produce zero emissions. ”
Therefore it is expected that taking in to account the reduced costs for fuel, m aintenance and spare parts, and the higher price for an electric forklift versus a diesel forklift, the return on investment will be within two to three years.
“Today the focus is primarily on Tank-toWheel (TTW) rather than Well-to-Wheel (WTW) when discussing emissions from battery electric vehicles.We believe the focus should of course consider the complete Well-to-Wheel chain. One thing also seldom considered is the carbon footprint from producing batteries, ” says Anders Nilsson, Director R&D Technology, Konecranes Lift Trucks. “Our award winning fully electric forklifts are equipped with battery cells with an 80% lower carbon footprint in benchmark comparison ” .
Patrik Lundback,Vice President, Sales and Distribution, Konecranes Lift Trucks told WPD: “On the sales side we understood there will be a great interest in our E-VER forklift truck, but I must admit that the interest is greater than we expected and the reception from our customers has been nothing but great. In addition, in December 2021, Konecranes launched Battery as a Service (BaaS), a breakthrough technology and business model. We now provide upgradable and remotely monitorable Li-ion batteries to our BaaS users. ”
When it comes down to sales a similar response comes from Kalmar. “We had a strong order intake during the first half of 2022 with good activities from most markets. The electric trend continues to be strong, especially in the northern EU, ” said Pilten. “Markets outside the EU are now also investing into sustainable solutions. ”
It is obvious that manufacturers are positioning themselves in this market segment of the port industry as it is a clear win-win situation, driven by increasingly strict legislation, investor demands, and local requirements, driving the transition to more eco-efficient cargo handling for now and in the future.
Konecranes FLT E-VER
Kalmar electric heavy forklift

Customisation,Customisation, thethe (new)(new) standardstandard inin thethe fenderfender industryindustry
F
ender systems are the interface between ship and berth.A safety measure to protect vessels, infrastructures and people, that needs to perform for its entire service life, even in the most remote locations and under harshest conditions.
Designing good fender systems encompasses many skills and disciplines, and standards are needed to design and manufacture them. Nevertheless, even two berths for the same application might require different fender systems and a design concept that is rarely simple and never an off-the-shelf solution. Putting an extensive focus just on the rubber unit and more or less ignore the requirements of the overall project, is a dangerous one-sided approach to fender design, which unfortunately seems to become common practice in the industry by some. No two projects are alike, no two solutions are alike and customisation is the new standard when dealing with a marine infrastructure project.
Figuring out customisation
First things first. Customisation refers to the act of adapting a product or service to suit certain requirements and preferences, and also applies when modifying something to solve a specific task.Translated into business language this means, customisation is the result of putting the spotlight on the project and the customer.
We are used to seeing customisation in the retail industry, e.g. soft drink cans are customised with the buyer ’ s name, or in the automotive industry. Now, what is the path to fender system customisation? A focus on the uniqueness of each project and of each client.This uniqueness might come in the shape of the product, the installation, sustainability, delivery and other special project and client requirements.
A customised fender system can only perform as expected if several aspects are considered, such as the project conditions, all the system components and their manufacturing. Considering them all and treating a fender system as one unit is the way to meet the project and client expectations.
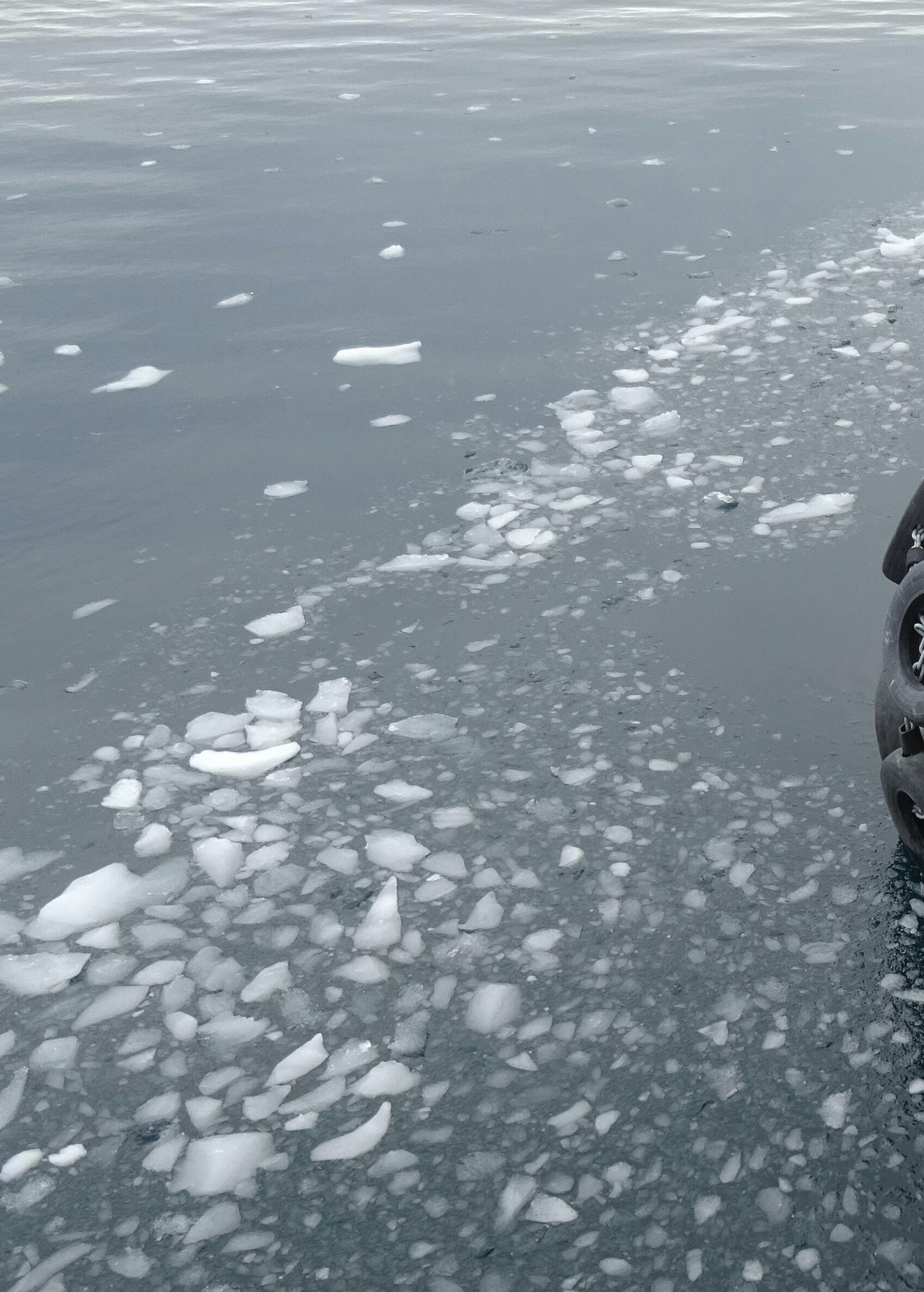
Project conditions
Firstly, deeming and delivering each project as unique means taking into account the constraints of the project.These are very individual and comprise, amongst others, the local climate, vessel types and berthing energy, location, berthing approach or berthing structure. Furthermore, the review of different characteristics of the various fender types should also be incorporated in the design process.
Components
Part of the customised approach is to ensure the fender system is up to its task, the designer must keep an eye on the big picture, while paying attention to every little detail.The rubber unit is a crucial component of the system, but it is only as good as the system ’ s overall design.A fender system is made of different components: rubber unit, steel panel, chains, anchors, fixings and PE plates.All of them and their interaction should be seen together to make sure they are all designed in the correct balance and work together properly.
Manufacturing
From a technical point of view, the road to a good rubber fender is completed with the combination of high-quality source materials and a fender manufacturer expertly skilled to guarantee the performance of the final product to the individual project requirements, and also international standards.The same applies for steel parts and PE as well.
When speaking about customisation, the focus is often on the product itself as an individual solution for the client, based on project requirements. However, customisation goes far beyond that and is valid for the entire steps of a project, from consulting to design, to manufacturing and delivery.
Such level of attention to the uniqueness of each project and of each client is only possible when relying on a company that has the resources and experience to design, engineer, manufacture and follow up the whole process until its completion.
In environments such as the Antarctic, the short installation window required a customised service and a very close and individual coordination between the client, the contractor and the manufacturer.
